The Warehouse in Modern Logistics
The modern supply chain is increasingly developing into “just-in-time” logistics (JIT). With this method, the required materials and products are delivered exactly when they are needed. This minimizes storage costs and times. A more advanced form of this is “Just-in-Sequence” (JIS), in which parts are not only delivered just-in-time, but also in the correct sequence in order to further increase production efficiency. Both developments aim to eliminate the storage of goods as far as possible. However, this is not yet the case in all supply chains.
The classic warehouse with a focus on “storage” can still be found in simple supply chains. However, in times of crisis, traditional warehouses regain importance for companies, as supply chains are interrupted. In this case, having a dedicated warehouse makes sense.
What is a Traditional Warehouse?
In a classic and traditional warehouse, goods are stored for later use. Warehouses are usually used by companies, including manufacturers, importers, exporters, customs, wholesalers as storage centers for temporary storage. The main processes that take place in these warehouses are in fact, the storage of goods.
At warehouses, forklifts and cranes are typically used for the loading and unloading of goods from various modes of transport such as trucks, planes, ships, or trains. For this reason, warehouses are commonly located near major transportation lines to ensure easy accessibility and quick transport. They are found near docks, highways, railways, or airports, for example.
Warehouse management is used to run and manage the daily operations in a warehouse. Good warehouse management strategies involve high-quality service at low costs. This optimizes the flow of goods throughout the supply chain and strengthens business relationships between stakeholders of the supply chain, and with end customers.
Traditional warehousing management or warehouse management is the manual and human operation of tasks in the warehouse. This includes manual inventory management, picking, and order fulfillment. Modern warehouse management involves the use of warehouse management software and modern technologies that automate warehouse operations. This will be further explained in the sections below.
What Kind of Warehouses Exist?
There are many different types of warehouses. Each serves a specific purpose within the supply chain and ensure that goods are stored, managed, and distributed efficiently based on the needs of the business and the nature of the products. The largest warehouses are designed for high-volume storage and distribution. These include distribution centers (DC), fulfillment centers, cold storage warehouses, automated warehouses, and bonded warehouses, for example. Here is a list of the different types of warehouses:
- Public Warehouses: Storage facilities available for lease to any company or individual needing storage space. Public warehouses have flexible leasing terms, and are often used by smaller businesses or for seasonal storage needs. They are operated by third party logistics (3PL) providers.
- Private Warehouses: Owned and operated by an individual company for their exclusive use. Private warehouses are custom-designed to meet specific needs, typically have higher control over operations, and are typically used by large businesses.
- Bonded Warehouses: Storage facilities where goods can be stored without paying import taxes until they are moved to market. It provides secure storage under customs control, and is commonly used for imported goods awaiting clearance.
- Cold Storage Warehouses: Specialized facilities for storing perishable items at very low temperatures. These warehouses are essential for frozen foods, pharmaceuticals, and other products requiring refrigeration or freezing. Advanced temperature control systems and refrigeration are used in various chambers to accommodate different temperature requirements (temperature monitoring).
- Automated Warehouses: Warehouses using automated systems for handling, storing, and retrieving goods. These warehouses use robotics, automated storage and retrieval systems (AS/RS), and have minimal human intervention.
- Fulfillment Centers: Specialized facilities for processing and shipping e-commerce orders directly to consumers. Fulfillment centers have efficient order picking, packing, and shipping processes, and handle a high volume of small orders. They are typically operated by 3PL poviders and have a greater focus on B2C operations.
- Consolidation Warehouses: Facilities where shipments from various suppliers are consolidated into larger, more economical loads. Costs are saved through bulk shipping and improved logistics efficiency.
- Cross-Docking Warehouses: Warehouses where incoming goods are directly transferred to outbound transportation with minimal storage time. This reduces inventory holding, speeds up delivery times, and improves supply chain efficiency.
- Hazardous Materials Warehouses (Hazmat Warehouse): Specialized facilities for storing hazardous materials and chemicals. In these warehouses, compliance with safety regulations, proper ventilation, and safety systems are crucial.
- Raw Materials Warehouses: Facilities for storing raw materials used in manufacturing processes. These warehouses are usually found in close proximity to production facilities, and have organized storage for easy access.
- Finished Goods Warehouses: Warehouses for storing finished products ready for distribution. These warehouses typically employ efficient inventory management, so that goods are ready for shipping to retailers or customers.
- Showroom Warehouses: Combines storage with a showroom for displaying products. These warehouses are often used in wholesale and retail sectors, allowing customers to view products before purchasing.
- Value-Added Service Warehouses: Warehouses that provide additional services such as packaging, labeling, assembly, or customization. This enhances product value, reduces lead times, and meets specific customer requirements.
- Smart Warehouses: Warehouses that are technologically advanced and automated. RFID tags, BLE beacons, and IoT sensors are typically used for real-time data collection for inventory.
- Buffer Warehouses: An intralogistics warehouse that is used by manufacturing companies to store material reserves that may be required for production. Intermediate products are stored in these warehouses.
- Transit Warehouses: An intermediate warehouse where goods are stored for a short period of time before shipment. Also known as a “transshipment warehouse”.
- Distribution Centers (DC): A B2B storage facility that is used to receive, temporarily store, and redistribute goods quickly. The main task is to speed up the flow of goods and deliver products quickly to retailers, customers or other end users. They are often used by e-commerce companies or online retailers and are either managed by the companies themselves or by external logistics providers (3PL). Various processes and tasks are carried out in a distribution center. These include: the receipt of goods, the inspection of goods, the transportation of goods within the warehouse, the storage of goods, the preparation of orders and the dispatch of goods. Distribution centers are categorized as either conventional, mechanized, or automated.
The movement of goods in a conventional DC is handled by people and mobile equipment. In a mechanized DC, this is assisted by conveyance and sorting systems that are mechanized. In an automated DC, the movement of goods is handled either partially or completely by robotics (autonomous mobile robots (AMR)) or machines.
Enterprise resource planning (ERP) solutions, AI and machine learning algorithms are also used in an automated DC to ensure smoother and more efficient processes. At Walmart's Casa Grande distribution center in Arizona, USA, for example, augmented reality (AR), virtual reality (VR) and drones are used to scan inventory.
What is Warehouse Management?
Warehouse management refers to the organization, management, and control of warehouses and the goods in them. This includes all activities that are necessary for the efficient use of storage space and the optimization of warehouse inventory. The main task of warehouse management is to secure the company's supply chains. Warehouse processes should run smoothly and cost-effectively, while storage capacities are optimally utilized.
Warehouse management comprises various sub-areas that enable material flow.
- Goods Receipt: Includes the acceptance, inspection, and registration of incoming goods. Ordered and returned goods are received and prepared for storage. All goods are identified and captured. Mobile data capture with wireless scanners optimizes this process. A quality check is carried out when goods are received. Labels for identification and traceability are often attached. Delivery bills and invoices are created. The warehouse process begins with the storage of goods in assigned storage locations. During cross-docking, the goods are taken directly to the goods receiving area.
- Picking: The assembly of goods for shipping or production through the use of systems to increase efficiency. Order picking is divided into large and small order picking. In small order picking, orders are fulfilled by assembling goods and materials from the warehouse inventory. The picker collects the goods using a list and takes them to the goods receiving area. Mobile data collection (MDC) supports this process. In large order picking, entire load carriers, or parts thereof, are transported directly from the storage location to the goods receiving area, including packing processes for larger partial quantities.
- Outgoing Goods: Goods are prepared for dispatch and shipping documents are created. The goods are repacked and checked here. Mobile devices are used here to create delivery bills, SSCC labels with the shipping unit number, and other accompanying documents. Finally, the goods and all documents are handed over to the carrier.
- Inventory: Physical stock is compared with system data through annual or permanent inventories. Stocktaking helps companies optimize processes by reducing inventory shortages. Traditionally, stocktaking is carried out manually by employees. The goods are counted, measured, and weighed. Wireless technologies such as RFID and barcodes are increasingly being used to record goods in warehouses. There are different types of inventories. These include the key date-based inventory, zero-crossing inventory, count level inventory, and permanent inventory.
- Returns Management: Returns are processed and decisions made on restocking or disposal.
- Warehouse Logistics and Control: The planning and control of warehouse processes via Warehouse Management Systems (WMS).
Wireless IoT Technologies and Warehouse Management
Products for a Digital Warehouse
A suitable IT infrastructure is crucial for a digital warehouse. Warehouse management with warehouse inventory scanners and barcode technologies is the most common. Barcode scanners and printers are most commonly used in warehouses. Other hardware products used in a digital warehouse include access control systems, networks and cabling, CCTV surveillance and wireless mobile terminals.
Warehouse management with RFID involves the use of RFID systems, including RFID tags and transponders, RFID readers and specialized software.
RFID scanners and antennas, warehouse barcode systems and access control devices are often used to improve the track and traceability, as well as the visibility of goods. Warehouse tasks such as picking, packing and shipping are automated with 1D and 2D barcode scanners and access control systems.
Printers are also used in the warehouse to print barcode or RFID labels and required documents. There are three main types of printers: industrial printers, desktop printers and mobile or handheld printers. RFID and barcode labels are attached to load carriers, packaging or directly to the products. These labels are read by suitable readers.
Mobile data entry devices (MDEs) are data collection devices that are connected to a central data processing system. The connection can be made either via infrared, radio, an acoustic coupler, WLAN or a mobile data network. These devices are used to record and evaluate the data in the warehouse. MDEs with an integrated scanner can also be used for order picking.
Forklift terminals are mounted on forklift trucks and mobile vehicles in the warehouse. They ensure fast data transfer and provide employees with an overview of all logistics processes.
Devices used in warehouses include GPS and BLE trackers, data glasses, mobile devices, voice-activated picking technology and robotics. Human-robot collaboration (HRC) is increasingly being used in warehouses. Collaborative mobile robots (cobots) are often used for picking and transporting goods.
Warehouse Software
The use of warehouse software is crucial to ensure that order fulfillment operations run smoothly and efficiently. There are four main types of software that is used in warehouses.
1. Enterprise Resource Planning (ERP)
Enterprise Resource Planning (ERP) is an integrated software platform that consolidates and manages core business processes, such as finance, human resources, manufacturing, supply chain, inventory management, and customer relationship management, into a unified system. By centralizing data and providing real-time insights, ERP systems enhance decision-making, improve efficiency, and streamline operations across an organization.
2. Warehouse Management Systems (WMS)
Warehouse Management Systems (WMS) are software tools that are often used to control, coordinate, and optimize warehouse processes, movements, and procedures. This includes inventory tracking, order fulfillment, receiving, and shipping. As a warehouse tracking system, WMS provides real-time visibility into inventory levels, improves accuracy, enhances productivity, and ensures efficient use of warehouse space, ultimately leading to better overall supply chain management. WMS is used by many companies, including warehouse operators and industrial companies, wholesalers and retailers, warehouse service providers, and trading companies. These systems are often used in combination with other tools in the warehouse – from barcode scanning to RFID tags, augmented reality wearables and warehouse robots.
WMS can also be integrated with transportation management systems (TMS), ERP and logistics software. There are four main types of WMS: standalone WMS, cloud WMS, SAP Extended Warehouse Management (SAP EWM), and integrated ERP and SCM-based WMS.
WMS are also often used with a Yard Management System (YMS) to ensure the seamless flow of goods from the yard into the warehouse and vice versa. YMS manages the trailers and containers in the yard, while WMS handles the storage and movement of goods inside the warehouse.
3. Warehouse Controls Systems (WCS)
Warehouse Control Systems (WCS) are software solutions that oversee the operation of automated material handling equipment within a warehouse, such as conveyors, sorters, autonomous mobile robots (AMRs), and automated storage and retrieval systems (AS/RS). WCS provides real-time control and coordination of these systems, ensuring smooth and efficient material flow, reducing errors, and maximizing the performance of automated warehouse operations.
4. Warehouse Execution Systems (WES)
Warehouse Execution Systems (WES) are advanced software platforms that manage and coordinate real-time activities and workflows within a warehouse, bridging the gap between Warehouse Management Systems (WMS) and Warehouse Control Systems (WCS). WES optimizes order fulfillment processes, balances workloads, and dynamically adjusts operations to improve efficiency, reduce bottlenecks, and ensure timely delivery of goods. It is essentially the evolution of WCS. All of the automation controls that is handled by a WCS can also be handled by a WES. A WES, however, also includes additional functions including bin level inventory, wave and order management, and picking management, for example.
The minimum requirement for most warehouses are the use of ERP and WMS. WES and WCS feeds into the WMS, which then feeds into the ERP.
Facts & Figures
The majority of warehouses are not yet automated. According to a report by “World Metrics”, around 80 percent of warehouses worldwide are still operated manually and without automation. However, figures show that the use of automated warehouses is on the rise. According to a report by the market research platform “Interact Analysis”, 26 percent of warehouses will be automated by 2027.
Successful Examples of IoT in Warehouse Management
The size of a warehouse can range from 5,000 to over 100,000 square meters. The Boeing Everett Factory in Washington, USA, is known as the largest warehouse in the world at 400,000 square meters. The size of warehouses and distribution centers, and the volume of goods are clear indicators that processes must be automated and all goods must be traceable. The following solutions are based on success stories that show how goods can be efficiently managed and tracked in the warehouse.
Warehouse Logistics at Symington Family Estates
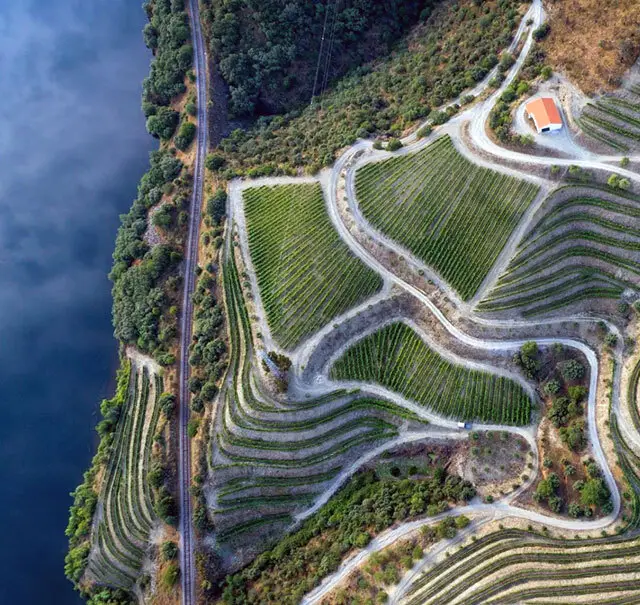
The Portuguese wine producer Symington Family Estates has been optimizing its warehouse logistics with RFID since 2015. Metal load carriers, each containing around 600 bottles of wine, are fitted with hybrid barcode and RFID labels. These load carriers are guided past the RFID readers at the warehouse entrance gate. Information from the RFID transponder, such as location, handling unit ID, Serial Shipping Container Code (SSCC), and time zone, is transmitted to the ERP system. The result: Real-time tracking of load carriers in the warehouse.
The Portuguese wine producer Symington Family Estates has been optimizing its warehouse logistics with RFID since 2015. Metal load carriers, each containing around 600 bottles of wine, are fitted with hybrid barcode and RFID labels. These load carriers are guided past the RFID readers at the warehouse entrance gate. Information from the RFID transponder, such as location, handling unit ID, Serial Shipping Container Code (SSCC), and time zone, is transmitted to the ERP system. The result: Real-time tracking of load carriers in the warehouse.
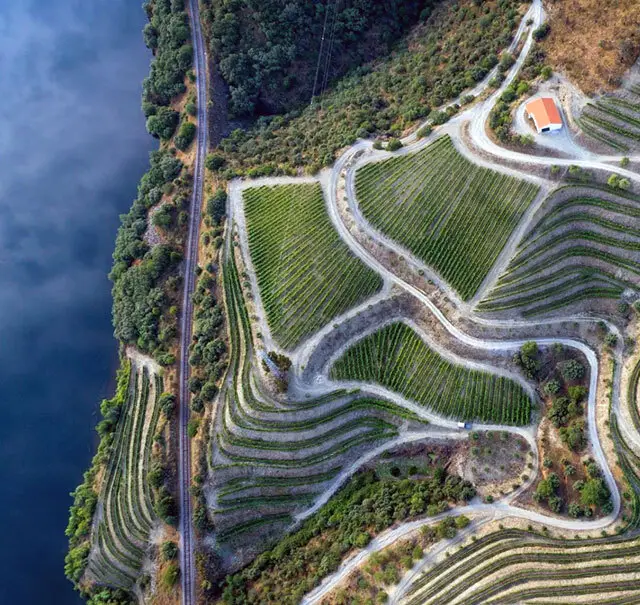
“For cost reasons, we did not include the finished wine products in the first RFID integration phase. In the future, however, we want to integrate all products into the RFID solution. We are currently planning to expand the RFID integration to all production and logistics processes. This includes not only the production lines, but also the warehouses for semi-finished products, finished products and the warehouse for raw materials.“
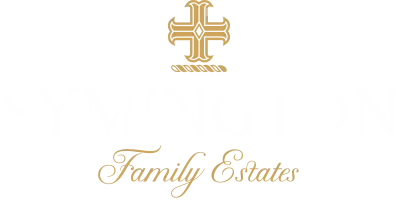
Isabel Freitas
Analyst Developer
Warehouse Transparency at Granterre
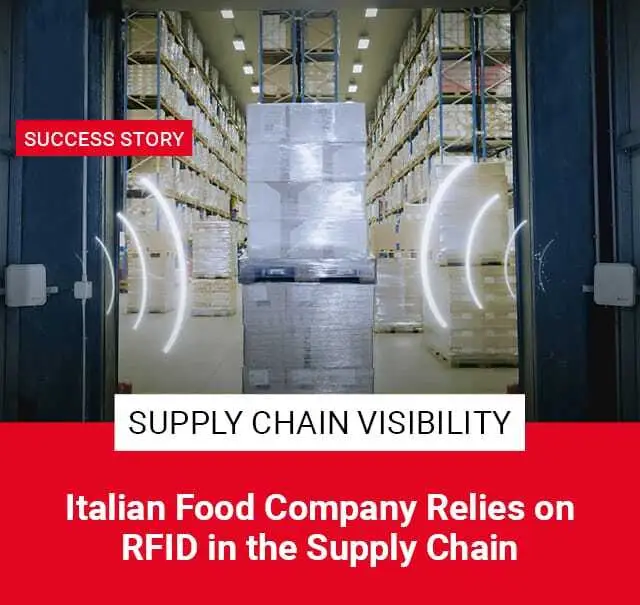
An RFID tracking solution is being used at Italian food manufacturer Granterre's distribution center in Bologna Interporto to increase supply chain transparency. In the 30,000 square meter distribution center, transport units with RFID tags are automatically captured by RFID gates at the entrances and exits. The RFID system is controlled by Murata's id-Bridge 4.0 middleware. The result: The time for loading and unloading goods is reduced by 50 percent and shipping accuracy is 99.95 percent.
An RFID tracking solution is being used at Italian food manufacturer Granterre's distribution center in Bologna Interporto to increase supply chain transparency. In the 30,000 square meter distribution center, transport units with RFID tags are automatically captured by RFID gates at the entrances and exits. The RFID system is controlled by Murata's id-Bridge 4.0 middleware. The result: The time for loading and unloading goods is reduced by 50 percent and shipping accuracy is 99.95 percent.
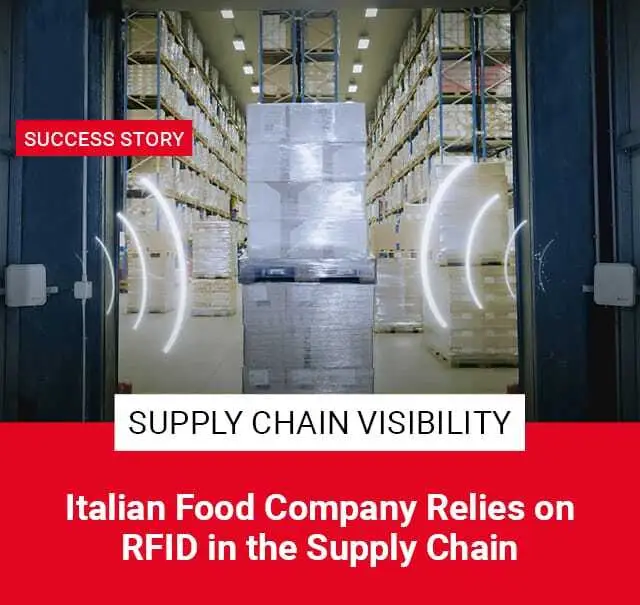
Pallet Management at KEB Automation
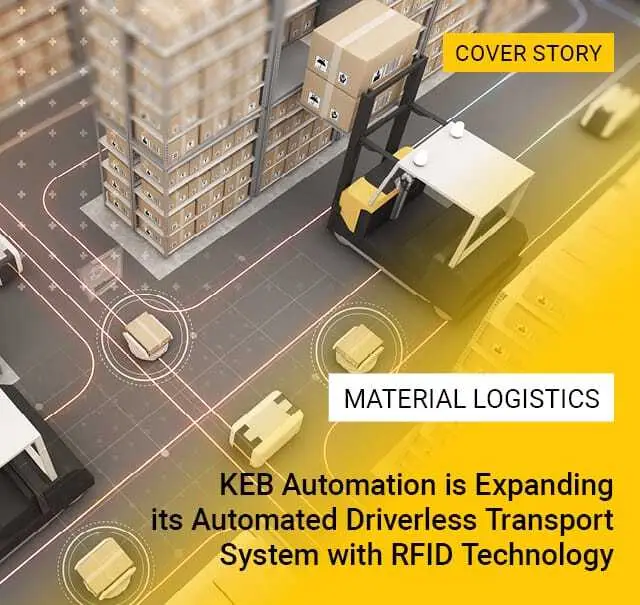
KEB Automation uses an RFID-based pallet tracking solution in its warehouse. The load carriers are fitted with RFID labels that contain a unique HU number for identification. All HU numbers are registered in the SAP Extended Warehouse Management (EWM) system. After picking, the pallets are prepared for the driverless transport systems (DTS). 20 of Turck's Q5X sensors detect the pallets on their way to the production halls. After recognition, the pallets are picked up by the DTS and transported through an RFID gate.
KEB Automation uses an RFID-based pallet tracking solution in its warehouse. The load carriers are fitted with RFID labels that contain a unique HU number for identification. All HU numbers are registered in the SAP Extended Warehouse Management (EWM) system. After picking, the pallets are prepared for the driverless transport systems (DTS). 20 of Turck's Q5X sensors detect the pallets on their way to the production halls. After recognition, the pallets are picked up by the DTS and transported through an RFID gate.
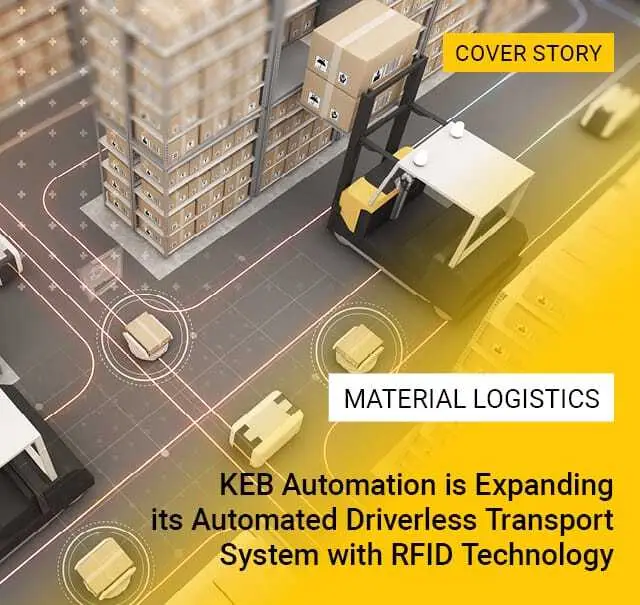
“The capture of the RFID tags is fully automated, allowing warehouse tasks from the SAP Extended Warehouse Management system to be completed or processed at the same time.”
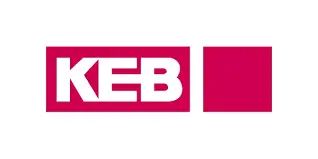
Viktor Derksen
Head of Industrial Engineering
More Stories on Warehouse Management
The Future of the Warehouse is Digital
As digitalization plays an increasingly important role in the modern world, companies must redesign their supply chain and warehouse processes accordingly. The digital warehouse is an important part of the modern supply chain. It is the basis for the efficient distribution of products.
The rapid growth of the e-commerce market, driven by the COVID-19 pandemic, has led to the need for more or larger warehouses. To cope with the increasing demand in e-commerce, online retailers need to digitize and automate warehouse management to remain competitive in the market.
Although interest in warehouse automation and digitalization seems to have increased in recent years, the majority of warehouses have not yet implemented automation solutions. The reasons for this include: High costs, complex processes, existing infrastructure, lack of skilled workers and security concerns.
The best solution to accelerate digitalization in the warehouse lies in the implementation of modern warehouse software solutions, the use of IoT and sensors, the introduction of automation and robotics, the use of data analysis and AI in companies, and the use of cloud-based solutions. A gradual introduction of these technologies, supported by the training and development of specialists, can effectively advance the digitalization process.
Advantages of a Digital Warehouse
Advantages of Wireless IoT
- Accurate and faster stocktaking
- Real-time localization of goods
- Complete visibility of goods
- Reduction of the error rate
- Reduction of costs
As part of digitization of the supply chain, digital warehouses bring numerous benefits, such as increased accuracy and speed of warehouse operations and processes, improved visibility of goods, optimized customer service and lower operating costs.
The elimination of paper-based processes, including inventory logs, shipping documents, and picking lists, leads to a reduction in errors and the elimination of misplaced documents. All relevant and important documents are made available on a digital dashboard. By automating manual processes, employees can be deployed for other tasks.
Industrial identification technologies provide complete visibility of all goods entering and leaving the warehouse. Handheld readers such as barcode scanners and RFID readers, together with document management software, automate data capture. This eliminates errors that can occur during manual data entry, increases inventory accuracy and reduces the time spent on stocktaking. Real-time monitoring of inventory in the warehouse also prevents oversales. Digital warehouse systems are also often user-friendly. Employees can quickly adapt and perform their tasks more efficiently.
Digital warehouse technologies enable the accurate tracking and real-time localization of inventory and individual assets. This allows companies to respond more quickly to customer orders. Deliveries are also processed faster, resulting in higher customer satisfaction.
As part of digitization of the supply chain, digital warehouses bring numerous benefits, such as increased accuracy and speed of warehouse operations and processes, improved visibility of goods, optimized customer service and lower operating costs.
The elimination of paper-based processes, including inventory logs, shipping documents, and picking lists, leads to a reduction in errors and the elimination of misplaced documents. All relevant and important documents are made available on a digital dashboard. By automating manual processes, employees can be deployed for other tasks.
Industrial identification technologies provide complete visibility of all goods entering and leaving the warehouse. Handheld readers such as barcode scanners and RFID readers, together with document management software, automate data capture. This eliminates errors that can occur during manual data entry, increases inventory accuracy and reduces the time spent on stocktaking. Real-time monitoring of inventory in the warehouse also prevents oversales. Digital warehouse systems are also often user-friendly. Employees can quickly adapt and perform their tasks more efficiently.
Digital warehouse technologies enable the accurate tracking and real-time localization of inventory and individual assets. This allows companies to respond more quickly to customer orders. Deliveries are also processed faster, resulting in higher customer satisfaction.
Advantages of Wireless IoT
- Accurate and faster stocktaking
- Real-time localization of goods
- Complete visibility of goods
- Reduction of the error rate
- Reduction of costs
The Challenges of a Digital Warehouse
There are various challenges that companies wishing to digitize their warehouse need to consider.
Connectivity must be stable throughout the warehouse for the digital solutions to work properly. It is important to select the right wireless solution according to the individual requirements of the warehouse. Standardization and configuration is required between different hardware and software solutions. Many warehouses are working with outdated infrastructure that cannot be easily digitized. Integrating new technologies into existing systems can be complex.
The introduction of new technologies and systems is also expensive. This includes the purchase of hardware, software, and staff training. Although switching to a digital warehouse can involve significant upfront investment in technology and infrastructure, it usually leads to a quick return on investment (ROI).
With the digitization of warehouses, data management and security become increasingly important. Companies are often reluctant to introduce new technologies that could pose security risks. To protect data, companies need to implement advanced security protocols and measures. These include encryption and authentication solutions.
Partners Spezialized in Warehouse Management Solutions
Outlook – Next-Level Warehouse Management
Digitalization in warehouse management has led to increased interest in wearable technologies, augmented reality solutions, artificial intelligence, predictive analytics, and robotics.
Wearable Technology and Augmented Reality (AR)
From voice headsets to smart gloves and data glasses: Wearable technologies are a growing trend in the modern warehouse. There is growing interest in augmented reality (AR) and wearable solutions that can support employees in the warehouse. Voice headsets facilitate order picking processes by voice command.
Smart gloves are often equipped with intelligent scanners to facilitate both picking and scanning processes. Smart glasses are able to scan barcodes in line of sight and use AR to display order lists or provide technical support for maintenance tasks. Wearable technologies can also be seamlessly integrated into SAP EWM systems.
Predictive Analyses and Artificial Intelligence (AI)
Predictive analysis is based on predictive modeling, big data solutions, and data mining. These statistical methods are used to analyze historical trends in the warehouse. In combination with artificial intelligence (AI), predictions can be made to optimize inventory, automate replenishment, and increase the efficiency of warehouse operations.
Robotics
Autonomous Guided Vehicles (AGVs) are increasingly being used as a replacement for forklift trucks. This automates the transportation of goods within the warehouse, saving both time and effort for employees. Picking processes are accelerated.
Drones equipped with cameras, sensors, RFID technology, or barcode scanners can also be used for stocktaking in the warehouse. This significantly reduces the time required for stocktaking.