What is Condition-Based Monitoring?
Condition-based monitoring, or condition monitoring (CM), refers to the process where the condition of a machine, building, asset, or system is monitored according to specified parameters. The primary purpose of condition monitoring is to detect early signs of equipment failure in order to prevent unexpected breakdowns. It is a maintenance strategy and serves as the basis for predictive maintenance (PdM Maintenance) and maintenance 4.0.
There are nine main types of condition-based monitoring:
1. Vibration Analysis
Traditional condition monitoring is typically based on vibration analysis. Vibration analysis involves monitoring the vibration levels of machinery and equipment to detect imbalances, misalignment, or other mechanical issues. Changes in vibration patterns can indicate wear and tear, allowing for early detection of rotational and structural issues. Techniques includes broadband vibration analysis and shock pulse analysis.
2. Oil Analysis
Oil analysis tests the quality and composition of lubricants and other fluids used in machinery. It can identify contaminants, degradation, and the presence of wear particles, which indicate internal wear. Oil analysis is commonly used in the transportation industry, and as part of condition monitoring for gearboxes and compressors.
3. Temperature Measurements
Temperature measurements involve the (remote) temperature monitoring of equipment and components to detect overheating or unusual thermal patterns. Abnormal temperature rises can indicate issues like bearing failures, electrical problems, or lubrication deficiencies. Passive and active thermography are advanced techniques that involve the use of cameras to capture the heat emitted from equipment.
4. Acoustic Analysis
Acoustic analysis is divided into two categories: Sonic and ultrasonic. In sonic analysis, microphones measure sound within the human hearing range. It is used for lubrication analysis, in order to determine if the equipment or parts of it are properly lubricated. Ultrasonic analysis goes a step further and is used to detect sounds that may indicate potential fault or failure in equipment. These sounds may not be audible to the human ear. Ultrasonic analysis is commonly used to detect cavitation, leaks, and parts that are not properly seated.
5. Motor Circuit Analysis
Motor circuit analysis evaluates the health of motors. Motor circuit analysis is used to detect insulation breakdowns, and electrical imbalances. This type of condition monitoring can be performed as the motor runs (online), or when it is de-energized (offline).
6. Electrical Monitoring
Electrical monitoring involves tracking electrical parameters. Characteristics such as capacitance, resistance, as well as pulse and frequency response can be tested this way. This type of condition monitoring measures the degradation of electrical systems to enable preventative maintenance before asset failure occurs.
7. Electromagnetic Measurement
Electromagnetic measurement monitors the electromagnetic fields generated by equipment. Changes in the current and distortions in the electromagnetic field indicate potential issues caused by defects.
8. Radiation Analysis
Radiation analysis refers to the internal analysis of assets and components via radiation imaging. It is a non-destructive testing method that measures the absorption rates of radiation in the tested material. Internal flaws absorb varying amounts of radiation.
9. Laser Interferometry
Laser interferometry refers to the use of laser interferometers to measure tiny displacements, vibrations, or deformations in machinery with high precision. The wave displacement of two laser beams are measured in order to identify defects on the surface or subsurface of materials.
How Has IIoT Changed Condition-Based Monitoring?
The Industrial Internet of Things (IIoT) has significantly transformed condition monitoring through the introduction of advanced technologies.
Companies are moving away from manual testing and inspections to automated processes for condition monitoring and remote maintenance. Condition-based monitoring in Industry 4.0 and maintenance involves the shift to real-time data collection and analysis. IIoT enables continuous, real-time monitoring of equipment conditions through interconnected condition monitoring sensors and devices. This allows for the immediate detection of anomalies and potential issues, leading to quicker responses and more proactive maintenance.
The vast amount of data collected by IIoT devices such as RFID tags with integrated sensors, and LoRaWAN and UWB sensors, is analyzed using advanced analytics and machine learning algorithms, which helps in identifying patterns, predicting failures, and providing actionable insights for maintenance decisions. By enabling real-time monitoring and predictive maintenance, condition monitoring helps achieve the goals of Industry 4.0, leading to more efficient, reliable, and intelligent industrial operations.
How Does Condition Monitoring Work?
There are five main steps to condition monitoring.
The first step involves the installation of sensors on the equipment or asset to be monitored. Sensors are selected according to the parameters that need to be measured and captured.
Data from these sensors is then collected from equipment and transmitted to a central system or cloud for processing. Depending on the monitoring system used, data collection can occur either in real-time, or at regular intervals.
Specialized software, advanced analytics, and machine learning algorithms analyze the data to identify anomalies, trends, and patterns. These are compared with historical data in order to determine potential issues.
When certain thresholds are crossed or potential failures are detected, the system generates alerts or notifications. Maintenance personnel are informed via SMS, e-mail, or through a device with a dedicated monitoring software.
Maintenance teams then review these alerts to determine the appropriate actions, and proactively schedule maintenance activities based on the condition of the equipment. This way, equipment failures are prevented before they happen. Integration with Computerized Maintenance Management Systems (CMMS) allows for automated maintenance scheduling.
Wireless IoT Technologies and Condition-Based Monitoring
Products for IoT Condition-Based Monitoring
The main condition monitoring hardware component are the IoT sensors. Different sensors measure different parameters, such as temperature, pressure, vibration, sound, oil levels, and humidity.
Interface gateways such as IO-Link, programmable logic computers (PLCs), and LoRaWAN are used to enable the collection, transmission, and integration of data from the sensors.
Data acquisition hardware plays an important role in gathering and processing sensor data. Data acquisition (DAQ) systems serve as the interface between physical sensors and the monitoring system. Some DAQ systems are equipped with onboard processing capabilities that allow for real-time analysis of the incoming data. In condition monitoring, DAQ systems aggregate data from various sensors and prepare it for further analysis. DAQ systems then transmit data to edge devices, centralized monitoring systems, cloud-based platforms, or enterprise systems like Enterprise Resource Planning (ERP) and Computerized Maintenance Management Systems (CMMS).
The most important software and tools for a condition monitoring system are data acquisition software, data processing software, data visualization software, alerting software, and maintenance planing software.
Facts & Figures
Condition monitoring is being increasingly being used in various industries. According to a report by “Market and Markets”, the global market for machine condition monitoring is estimated to grow by 8.3 percent between 2024 and 2029. Cloud-based condition monitoring systems are also on the rise. According to a report from the market research platform “Gitnux”, the market share of cloud-based vibration monitoring systems is predicted to exceed 25 percent of the global market for vibration monitoring systems by 2027. Companies using vibration monitoring can reduce the failures of machines by up to 30 percent.
Successful Examples of IoT Condition-Based Monitoring
Condition monitoring is widely adopted across various industries. It contributes to digitalization in industry by enabling the monitoring of machinery and equipment for early signs of wear and tear. The oil and gas industry applies condition monitoring to drilling rigs, pipelines, and processing equipment. Under the umbrella of digitalization in transportation, including automotive, aviation, and railways, condition monitoring is used to ensure vehicle and system reliability. As part of digitalization in healthcare, the condition of medical equipment is monitored. Mining operations uses condition monitoring to oversee heavy machinery. The aerospace industry monitors aircraft engines and systems. Condition monitoring is also used for generators, wind turbines, and solar panels as part of digitalization in the energy industry, for example.
The real-world examples below show how IoT technologies are used in condition monitoring in the energy industry, in production, and in agriculture.
Condition Monitoring at Climeworks
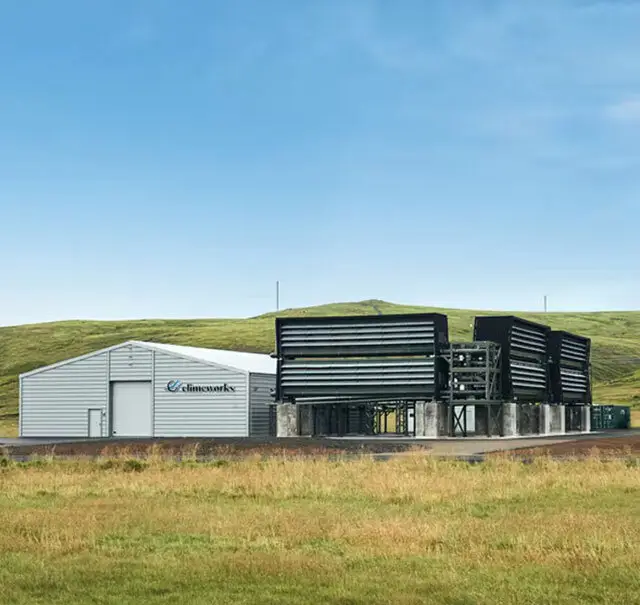
At its direct air capture and storage (DAC+S) plant Orca, Climeworks has deployed sensor technology for the condition monitoring of plant components. Sensors measure temperature, pressure, valve data, weather data, quality of treated CO2, energy consumption, and functionality of the sorbent. Predictive maintenance is made possible. In order to fully enable remote process control, the OPC Foundation’s OPC UA data communication standards are being tested for implementation in the next plant.
At its direct air capture and storage (DAC+S) plant Orca, Climeworks has deployed sensor technology for the condition monitoring of plant components. Sensors measure temperature, pressure, valve data, weather data, quality of treated CO2, energy consumption, and functionality of the sorbent. Predictive maintenance is made possible. In order to fully enable remote process control, the OPC Foundation’s OPC UA data communication standards are being tested for implementation in the next plant.
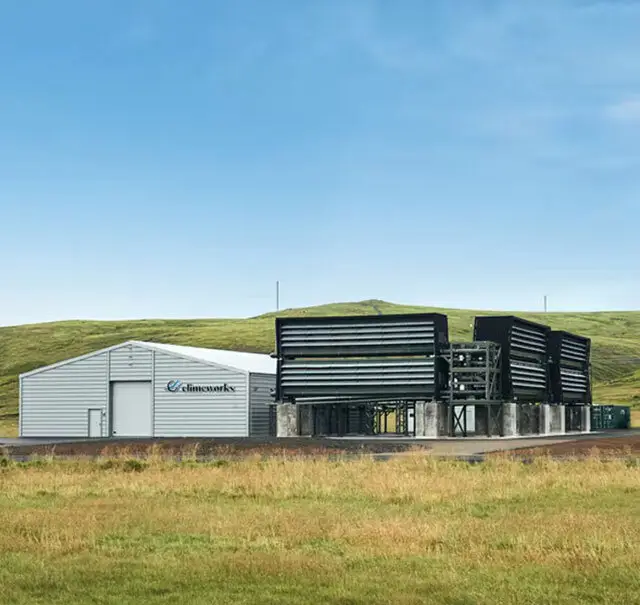
"The Orca plant is the first of its kind, which is why there are still employees stationed on-site to observe. However, the control is done from Switzerland. The goal is to operate the plants as black factories. This means that there will be no staff on-site and control will be completely remote. For this reason, the OPC UA data communication standard is being tested in laboratory environments. This is to be used for control in the next plant."

Nathalie Casas
Head of Technology
Livestock Condition Monitoring by the LfL
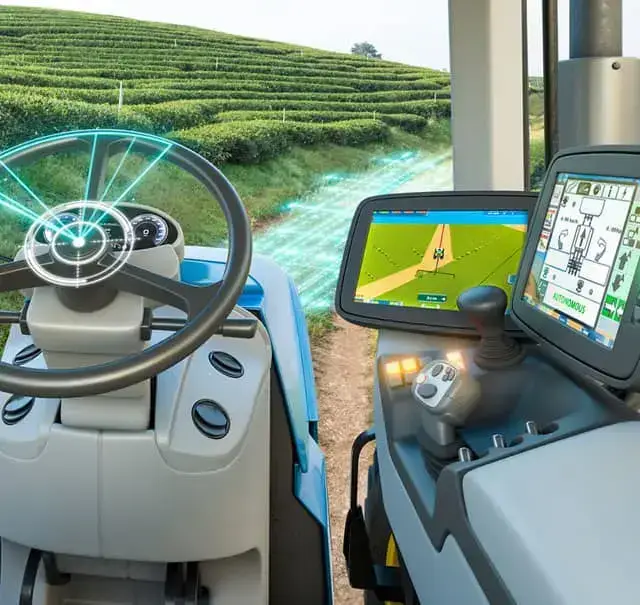
As part of the “DigiMilch” project of the Bavarian State Research Center for Agriculture (LfL), sensors and AI are used to monitor the condition of livestock. Each animal is fitted with sensors, attached to the ear, neck or foot. These sensors measure parameters including drinking cycles, chewing time, resting time, feeding time, body temperature, and standing time. Data is transmitted to the smartphone or computer of the farmer and analyzed via AI systems. The farmers are notified via an alarm if abnormalities are detected.
As part of the “DigiMilch” project of the Bavarian State Research Center for Agriculture (LfL), sensors and AI are used to monitor the condition of livestock. Each animal is fitted with sensors, attached to the ear, neck or foot. These sensors measure parameters including drinking cycles, chewing time, resting time, feeding time, body temperature, and standing time. Data is transmitted to the smartphone or computer of the farmer and analyzed via AI systems. The farmers are notified via an alarm if abnormalities are detected.
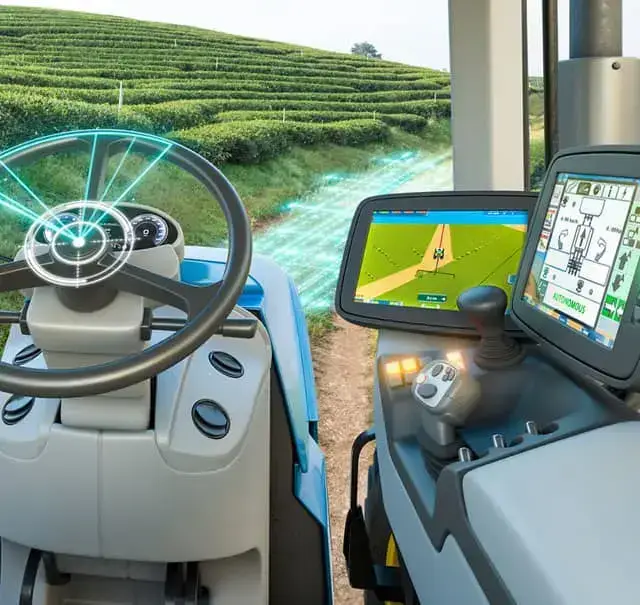
Machine Condition Monitoring by Enerthing
The company Enerthing has developed batteryless sensors that is used for condition monitoring in industrial settings. Machines are equipped with light-powered sensors. A Bluetooth mesh system is used to retrieve live data from the shop floor. The data is transported through different sensor nodes to a gateway, to the cloud, and then to the customer software, or to a dashboard. Anomalies are detected by measuring parameters like vibration over time. An alerting system notifies staff in order to trigger maintenance activities.
“Condition monitoring will ideally lead to predictive maintenance. By measuring the vibrations, we can detect over time, if there are anomalies. Whether the vibrations increase over time, or if its the temperature that increases over time, for example. This way, its very simple to check imbalances of ventilator blades, or misalignment of motors with respect to the machine, because the vibration amplitude increases over time.”
More Stories on Condition Monitoring
Condition Monitoring in Agriculture
Sigfox IoT-enabled sensors are used for condition monitoring in agriculture. These sensors collect data such as temperature and rainfall over time, in order to optimize farming operations. The sensors monitor the humidity, moisture, and temperature levels of soil, as well as the temperature of the air. This data is transmitted directly to the Internet. Wi-Fi, GSM, or regular Internet connection is not necessary. This way, farmers receive live data from the field that allows them to make better decisions in terms of pest control, planting, and irrigation, for example. Farmers can also use RFID sensor solutions in combination with AI to monitor the condition of livestock.
The Future of Condition-Based Monitoring
In modern Industry 4.0 environments, it is no longer the question of whether or not condition monitoring should be implemented, but rather to determine the extent and scope of condition monitoring data. In many modern industrial plants, personnel and service companies are often situated away from the actual sites of operations. Currently, most of these workers function as isolated islands of information, primarily due to the absence of effective software tools that facilitate communication and integration.
The implementation of cloud-based condition monitoring platforms can bridge this gap by connecting isolated workers with data sets. This technology eliminates barriers to information visibility and collaboration. Consequently, this enhanced collaboration will lead factories of the future to improved maintenance performance and ultimately maximize business value.
An increasing number of companies are moving from reactive, scheduled maintenance schedules to a more condition-based and predictive approach. Integrating AI is the next step in the prediction of potential problems. With the move towards Industry 5.0, AI and the IIoT in condition monitoring are becoming increasingly important. This upcoming industrial era will emphasize human-robot collaboration (HRC), customization, and sustainability. By working together, humans and AI will ensure that maintenance teams achieve their goals in terms of operational efficiency. Advanced condition monitoring systems will be used to generate the data and insights required for this.
The future of condition monitoring also involves digital twins and augmented reality (AR). The integration of digital twins with condition monitoring systems (CMS) are emerging as game-changers in industrial digitalization for companies. Integrating condition monitoring systems with digital twins provides manufacturers with a comprehensive, real-time view of equipment performance and health (machine health monitoring). Digital twins can simulate asset or equipment behavior using live data from condition monitoring systems. This way, operators can monitor important parameters and quickly detect abnormalities or deviations. Digital twins also enable predictive maintenance.
AR is increasingly being utilized in condition monitoring to enhance the efficiency and effectiveness of maintenance and operational tasks. AR can overlay real-time data from sensors and condition monitoring systems directly onto the physical equipment. Technicians can see metrics like temperature, vibration, and pressure superimposed on the machinery through AR glasses or mobile devices. Additionally, AR enables the creation of interactive dashboards that can be accessed through smart glasses or tablets, allowing maintenance personnel to visualize historical data, trends, and predictive analytics on-site. Remote assistance is another significant benefit, as experts can provide support by seeing what the on-site technician sees through AR, guiding them in real-time and highlighting specific components that need attention.
Advantages of Condition-Based Monitoring with IoT
Advantages of Wireless IoT
- Increased equipment or machine up-time
- Increased productivity
- Prevention or reduction in downtime or equipment failures
- Real-time insights into asset health and performance
- Cost reduction for repairs and maintenance
One of the primary benefits of integrating IoT in condition monitoring is the ability to collect real-time data from a vast network of connected sensors embedded in machinery and equipment. This continuous data stream provides a detailed and up-to-the-minute view of equipment performance, enabling immediate detection of anomalies and potential issues. By monitoring parameters such as temperature, vibration, and pressure in real-time, IoT helps prevent unexpected breakdowns and reduces the risk of costly downtime. Worker safety is also increased, as the risk of machines malfunctioning or breaking down has decreased.
Another advantage of IoT in condition monitoring is that it enables predictive maintenance. IoT devices collect extensive historical and real-time data that, when analyzed using advanced analytics and machine learning algorithms, can predict when equipment is likely to fail or require maintenance. This predictive capability allows maintenance to be scheduled at the most opportune times, avoiding unplanned downtime and extending the lifespan of equipment. By shifting from a reactive to a predictive maintenance strategy, businesses can achieve greater operational efficiency and cost savings.
Traditional monitoring setups can be limited by the need for extensive wiring and infrastructure. In contrast, IoT-enabled systems can be easily expanded by adding more wireless sensors as needed. This scalability allows businesses to start with a small, manageable system and gradually increase their monitoring capabilities as required. Additionally, IoT devices can often be integrated with existing systems.
The use of IoT in condition monitoring also improves data accessibility and visibility. Cloud-based IoT platforms aggregate data from multiple sources, making it accessible from anywhere via the Internet. This centralized data repository allows stakeholders at different locations to access and analyze the same set of data, which leads to improved collaboration and decision-making. Real-time alerts and notifications can be sent to relevant personnel, ensuring that potential issues are addressed promptly regardless of their physical location.
Furthermore, IoT can be used to conduct remote monitoring (remote condition monitoring) and diagnostics. Technicians and engineers can monitor equipment performance and diagnose issues without being physically present on-site. This capability is particularly valuable for facilities located in remote or hazardous environments, reducing the need for frequent on-site visits and improving overall safety.
One of the primary benefits of integrating IoT in condition monitoring is the ability to collect real-time data from a vast network of connected sensors embedded in machinery and equipment. This continuous data stream provides a detailed and up-to-the-minute view of equipment performance, enabling immediate detection of anomalies and potential issues. By monitoring parameters such as temperature, vibration, and pressure in real-time, IoT helps prevent unexpected breakdowns and reduces the risk of costly downtime. Worker safety is also increased, as the risk of machines malfunctioning or breaking down has decreased.
Another advantage of IoT in condition monitoring is that it enables predictive maintenance. IoT devices collect extensive historical and real-time data that, when analyzed using advanced analytics and machine learning algorithms, can predict when equipment is likely to fail or require maintenance. This predictive capability allows maintenance to be scheduled at the most opportune times, avoiding unplanned downtime and extending the lifespan of equipment. By shifting from a reactive to a predictive maintenance strategy, businesses can achieve greater operational efficiency and cost savings.
Traditional monitoring setups can be limited by the need for extensive wiring and infrastructure. In contrast, IoT-enabled systems can be easily expanded by adding more wireless sensors as needed. This scalability allows businesses to start with a small, manageable system and gradually increase their monitoring capabilities as required. Additionally, IoT devices can often be integrated with existing systems.
The use of IoT in condition monitoring also improves data accessibility and visibility. Cloud-based IoT platforms aggregate data from multiple sources, making it accessible from anywhere via the Internet. This centralized data repository allows stakeholders at different locations to access and analyze the same set of data, which leads to improved collaboration and decision-making. Real-time alerts and notifications can be sent to relevant personnel, ensuring that potential issues are addressed promptly regardless of their physical location.
Furthermore, IoT can be used to conduct remote monitoring (remote condition monitoring) and diagnostics. Technicians and engineers can monitor equipment performance and diagnose issues without being physically present on-site. This capability is particularly valuable for facilities located in remote or hazardous environments, reducing the need for frequent on-site visits and improving overall safety.
Advantages of Wireless IoT
- Increased equipment or machine up-time
- Increased productivity
- Prevention or reduction in downtime or equipment failures
- Real-time insights into asset health and performance
- Cost reduction for repairs and maintenance
Partners Spezialized in Condition Monitoring Solutions
The Challenges of Condition Monitoring
Implementing an IoT condition-based monitoring system involves integrating various hardware and software components, often with existing enterprise systems such as ERP and maintenance management systems. This integration process can be complex and time-consuming, requiring significant technical expertise and resources.
The value of monitoring systems depends on the accuracy and reliability of the data collected. Poor data quality, resulting from sensor malfunctions, calibration issues, or data transmission errors, can lead to incorrect analysis and misguided maintenance decisions.
Installation costs for condition monitoring equipment may be expensive. This includes IoT devices, infrastructure, and system integration. Battery-powered sensors are quite costly, for example. In some cases, condition monitoring systems may need to be modified and retrofitted. In terms of operational costs, companies also need to take into account the regular maintenance of IoT devices, including calibration, firmware updates, and battery replacements. Staff training is required to ensure that data analysis of condition monitoring data is performed correctly.
Another challenge with IoT condition-based monitoring is data security. As IoT devices collect and transmit vast amounts of data across networks, they become potential targets for cyberattacks. Ensuring the security of these devices and the data they handle is critical, but it can be complex. Security measures must include encryption, secure communication protocols, and regular updates to protect against vulnerabilities.
IoT condition-based monitoring systems generate an enormous volume of data in real-time, which can be overwhelming to process and analyze efficiently. High data velocity demands robust infrastructure capable of handling real-time data streams without latency. This often requires advanced data processing techniques and scalable cloud services to ensure that the data can be analyzed and acted upon promptly.
Interoperability is also a major concern in IoT condition-based monitoring. Industrial environments often use equipment from multiple manufacturers, each with its own proprietary protocols and standards. Integrating these diverse systems into a cohesive monitoring framework can be challenging. Ensuring that different IoT devices and platforms can communicate and work together seamlessly requires adherence to common standards and protocols. OPC UA plays an important role here. To learn more, find out: what is OPC UA good for?