What is OPC UA?
OPC UA is the abbreviation for Open Platform Communications Unified Architecture. It is the standard for secure and reliable data exchange, especially for industrial automation in various industries. The specification is platform-independent and ensures a continuous flow of information between products, plants, devices, machines, systems, and entire factories. It is 100 percent interoperable.
In short: OPC UA is one of the world's most important communication standards for networked, lean, and therefore fast data exchange in the industrial environment. OPC UA thus enables the Industrial Internet of Things (IIoT), Manufacturing X, and Industry 4.0.
History: OPC Classic for Windows Operating Systems
1990s: The simplification of various proprietary communication protocols was the original goal of Open Platform Communications (OPC). The developers of OPC wanted to standardize the data flow and offer an open standard. This was particularly important for industrial production. The developers' aim was to simplify the integration of different systems, and thus, optimize industrial automation as a whole – in short, to harmonize the flow of data and the networking of devices. The result was a communication protocol for data in industry. In fact, it was the collaboration between industrial suppliers, manufacturing companies, and software developers that made the development of OPC so successful. This is still the case today, and is rooted in the philosophy of the OPC Foundation.
When the standard was first published in 1996, the goal was to abstract PLC-specific protocols – such as Modbus or Profibus – into a standardized OPC interface that would allow HMI/SCADA systems to work with an "intermediary" that converts generic PLC read/write requests into device-specific requests and vice versa. As a result, numerous OPC-enabled products have been launched on the market.
OPC Classic: Originally, the OPC standard was limited to the Windows operating system. The term OPC was therefore derived from Object Linking and Embedding (OLE) for Process Control. These specifications, now known as OPC Classic, have been adopted in a wide range of industries, including manufacturing, building automation, oil and gas, renewable energy, and utilities. For more than 30 years, the OPC standard has formed the foundation for seamless communication between different automation systems and devices from different manufacturers. It stands for the connection between OT and IT.
What Does the OPC Unified Architecture (UA) Mean Today?
In the 2000s, industrial production changed as service-oriented architectures were increasingly developed for manufacturing systems. This resulted in new requirements for OPC in terms of security and data modeling. For this reason, the OPC UA specifications were developed by the OPC Foundation in collaboration with the member companies. The new specifications offer an open, future-proof, scalable, and expandable architecture with numerous additional functions. The abbreviation UA stands for Unified Architecture.
The current OPC UA specification was first published in 2008. It is an open, platform-independent communication standard for the exchange of data and information between different systems and servers in the field of automation. OPC UA is the latest specification generation of the OPC Foundation. OPC UA is a standard of the International Electrotechnical Commission (IEC). It is described in IEC 62541.
Essentially, OPC UA was developed to overcome the shortcomings of previous OPC standards and enable reliable, secure, and interoperable communication. This also includes tunneling, as OPC UA eliminates the need for tunneling. By using an OPC wrapper, the OPC Classic Server is still able to communicate across the network and make the data available to other servers and systems.
OPC UA in 2024 stands for the interface between clients and servers, as well as servers and servers, including access to real-time data, the monitoring of alarms and events, access to historical data, and other applications. It is the foundation for artificial intelligence (AI) in companies, simulation, and digital twins. In short, OPC UA is the evolution of the specification from the 1990s.
OPC UA Foundation and OPC UA Field Level Communications (FLC)
Since its publication in 1996, the industry standard has been driven forward by the OPC Foundation. Companies like Microsoft, Rockwell Automation, Siemens, ABB, Honeywell, Mitsubishi Electric, and Schneider Electric were among the founders of the initiative.
From the beginning, the Foundation was a non-profit organization that focused on developing standards for interoperability in industrial automation, together with partners. Companies worldwide are actively working on specifications. Work on the Companion Specifications mainly takes place in the expert circles of the working groups. To summarize, software and hardware specialists around the globe are driving the IoT forward by working on standards and then sharing them with others.
Numerous end users are now also members. Examples include L'Oréal, Airbus, Procter & Gamble, and the Renault Group. The end users benefit from the fact that major providers of IoT cloud solutions such as Google and Microsoft integrate OPC UA into their solutions.
Test Tools for OPC UA
To take the first steps towards OPC UA, many companies offer OPC UA test tools. These allow manufacturing companies to operate OPC UA test servers and OPC UA test clients in order to simulate the production environment.
In 2018, the OPC Foundation launched the OPC UA Field Level Communications (FLC) initiative. The initiative works on communication interfaces for field devices such as sensors, actuators, and controllers, so that these devices can be seamlessly integrated into OPC UA networks. The OPC UA FX (Field eXchange) specification was finalized for this.
In addition, a multi-vendor demo with controllers and network infrastructure components was implemented to demonstrate the cross-vendor interoperability of automation components for a wide range of applications in factory and process automation.
OPC UA-Enabled Products
A Standardized and Secure Exchange of Information
The Advantages of OPC UA
- Simple interfaces
- Standardized message format
- Security and encryption
- Real-time capability
- Interoperability and connectivity
The advantages have already been touched on in the first sections. To summarize the benefits: OPC UA is a standardized and secure data communication in the industrial environment that works seamlessly from the field level to the cloud and back, and is scalable as required. The architecture is flexible, transparent, and platform-independent.
Standardized interfaces enable access to a wide range of applications. Overall, OPC UA can be flexibly expanded and is therefore scalable and future-proof in an increasingly complex industrial environment. This applies to Manufacturing X, machine-to-machine communication (M2M), digital twin solutions, AI, and simulation.
The advantages have already been touched on in the first sections. To summarize the benefits: OPC UA is a standardized and secure data communication in the industrial environment that works seamlessly from the field level to the cloud and back, and is scalable as required. The architecture is flexible, transparent, and platform-independent.
Standardized interfaces enable access to a wide range of applications. Overall, OPC UA can be flexibly expanded and is therefore scalable and future-proof in an increasingly complex industrial environment. This applies to Manufacturing X, machine-to-machine communication (M2M), digital twin solutions, AI, and simulation.
The Advantages of OPC UA
- Simple interfaces
- Standardized message format
- Security and encryption
- Real-time capability
- Interoperability and connectivity
Facts & Figures
According to a report by the market research consultant „Fortune Business Insights“, the global market for OPC server software is divided into five regions. These include Europe, North America, South America, the Middle East and Africa, as well as the Asia Pacific region. As a result of an early adoption of advanced machine-to-machine technologies and solutions, In 2022, North America had the largest share in this market, at 32 percent, followed by the Asia Pacific region at 25 percent, and Europe at 24 percent.
What Does 'Platform-Independent and Interoperable' Mean?
TCP/IP and web protocols ensure that data communication via OPC UA is 100 percent platform-independent. What's new since 2008? Regardless of whether the server's operating system is Windows, Linux, UNIX, or MacOS, the OPC server can be accessed via all protocols. This also applies to proprietary systems with a TCP/IP stack. Data communication therefore works regardless of the manufacturer or type of operating system or hardware platform. In practice, this means that embedded systems, devices, and controllers can act as servers regardless of the operating system. No special adaptations or configurations are required.
Full interoperability is achieved by using a standardized data model and communication protocol that is understood by all systems that support OPC UA. This creates the basis for connecting Operational Technology (OT) and Information Technology (IT).
Connecting OT and IT
The connection between OT and IT in OPC UA refers to the integration of data. OT includes control and automation systems, field sensors, actuators, and other devices used in industrial environments to monitor and control processes. IT, on the other hand, includes networks, servers, databases, ERP systems, software applications, and other technologies used in corporate networks to store, analyze, and manage data.
By using OPC UA, data from the OT can be securely, quickly, and seamlessly integrated into the IT environment. All processes and the connectivity of process data in production are improved by this networking. More informed decisions can be made on the basis of real-time data and data analyses. The platform independence and interoperability of OPC UA guarantees an increase in operational efficiency. As the data is not isolated, companies can control it from the edge to the cloud.
OPC UA for Collaborative Industrial Robots
OPC UA from the OPC Foundation can be used in combination with a 5G network in order to facilitate communication and collaboration between stationary and mobile industrial robots. Stationary robots are used to load and unload boxes in warehouses. These robots work together with mobile robots, also known as automated guided vehicles (AGVs), which transport crates in the warehouse. Both wired and wireless connections are used. The stationary robots are connected via a wired infrastructure. The mobile robots are connected via a private 5G network. The transport agnostic OPC UA Safety Architecture is also used here to enable fail-safe, safety-critical operation in the warehouse. The OPC UA safety layer ensures that transmission errors such as lost, damaged, or delayed messages are detected. Programmable logic controllers (PLCs) control the various robots in the warehouse via a controller-to-controller connection. The PLCs are connected to each other and also exchange process data with each other.
Wired Ethernet is used in the warehouse's network infrastructure. This is part of the mobile robots, which contain devices such as the PLC and sensors. The stationary robots are also connected to the factory network and the local industrial network via the wired infrastructure. The industrial 5G network is used to connect the stationary and mobile robots. A supporting Layer3 PDU session enables IP-based interconnectivity between the PLC of the stationary robot and the PLC of the mobile robot. This typically happens with cycle times of a few milliseconds. OPC UA Safety also exchanges time-critical safety messages via this network to ensure deterministic end-to-end transmission.
"To connect these robots, we use the industrial 5G network. In this case, the support of Layer3 PDU sessions enables IP-based interconnectivity between two controllers. Cycle times of a few milliseconds are typically achieved."
OPC UA in Use at Airbus Defence and Space
Airbus Defense and Space, a division of the European Airbus Group, has been using OPC UA from the OPC Foundation since 2017 to optimize data management and communication in its "Technological Experiments in Zero Gravity" (TEXUS) project. Two of the experiment modules on the TEXUS 60 rocket are already equipped with OPC UA. The devices on board the TEXUS rocket and on the ground communicate via OPC UA. The flight software within the on-board system uses OPC UA for data acquisition and experiment control. By using OPC UA, the number of data points per experiment was significantly increased from 64 to 4,000. OPC UA also makes it easier for development engineers to access data via displays, archives, and systems on the ground. Sensors, actuators, and controllers are controlled via the TEXUS OPC UA specification. OPC UA enables centralized control and data conversion via adapters for database integration. Communication data is transmitted in real time. This leads to improved efficiency of data management across different platforms.
TEXUS research rockets are unmanned. The rocket is 13 meters long and weighs just under 2,700 kilograms. The payload measures 5.3 meters and contains three to four autonomous research modules, each containing experiments. The rocket takes these experiments to an altitude of up to 260 kilometers within 15 minutes. In the last 6 minutes, the experiments are carried out in zero gravity before the payload falls back to earth and is recovered.
"The adoption of OPC UA has been driven by two key factors: The Ethernet capability and the embedded data model within the server. The Ethernet capability enables remote testing and operation without the need for a physical presence. In addition, the embedded data model simplifies the completion of test modules by allowing easy access and compilation of the required information."
OPC UA in Use at Scatec
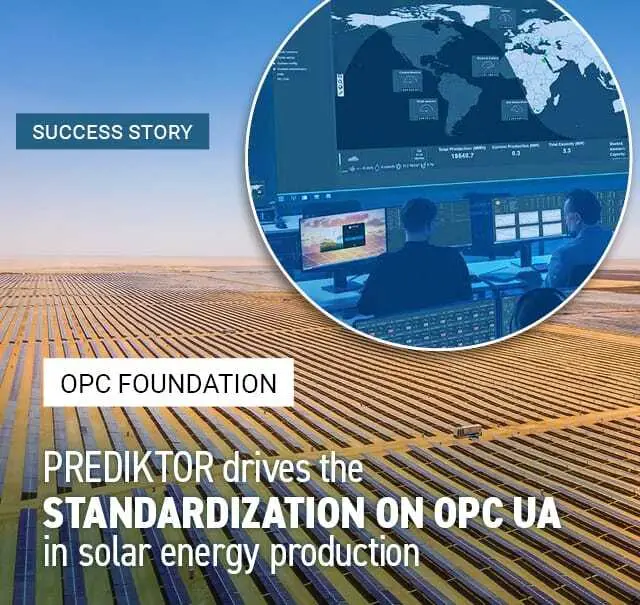
A MAP gateway system from system integrator Scatec, a provider of renewable energy solutions, is used to consolidate all solar plant data operated by Scatec worldwide. More than 100,000 data points are received every second. The data is standardized and semantically interpreted with the help of AI algorithms. The various data signals from the solar installation are mapped via the MAP gateway and then read into Prediktor's Supervisory Control and Data Acquisition System (SCADA). Depending on the size of the system, this takes between three and six months.
The SCADA installed in the solar fields provides the operators with interfaces for system operation. This establishes interoperability between the various devices and system types. From here, the sensor data from all systems is fed into the central asset management system PowerView. This system uses OPC UA from the OPC Foundation to semantically standardize the data and combine it into a single "asset" structure. This enables a "group view" of global operations and performance. This way, operators are able to view standardized data representations across the entire asset fleet.
A MAP gateway system from system integrator Scatec, a provider of renewable energy solutions, is used to consolidate all solar plant data operated by Scatec worldwide. More than 100,000 data points are received every second. The data is standardized and semantically interpreted with the help of AI algorithms. The various data signals from the solar installation are mapped via the MAP gateway and then read into Prediktor's Supervisory Control and Data Acquisition System (SCADA). Depending on the size of the system, this takes between three and six months.
The SCADA installed in the solar fields provides the operators with interfaces for system operation. This establishes interoperability between the various devices and system types. From here, the sensor data from all systems is fed into the central asset management system PowerView. This system uses OPC UA from the OPC Foundation to semantically standardize the data and combine it into a single "asset" structure. This enables a "group view" of global operations and performance. This way, operators are able to view standardized data representations across the entire asset fleet.
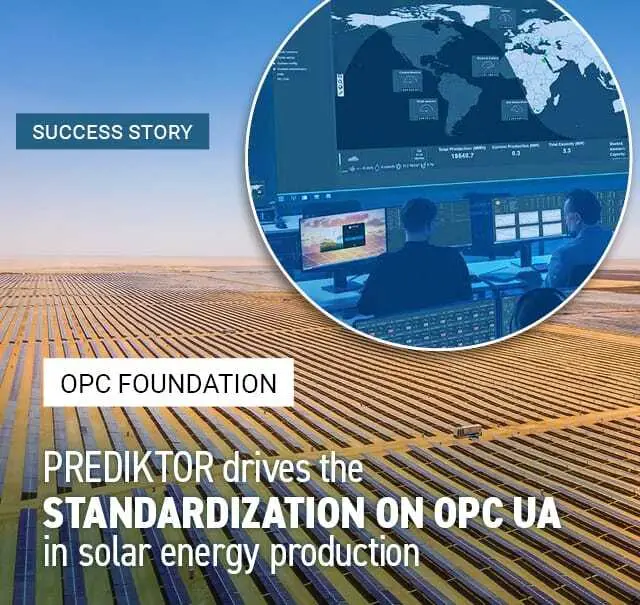
"The beauty of solar energy is that the resource is already available. You just have to record it. However, it's more complicated to capture all the system data and analyze it for system control and maintenance."
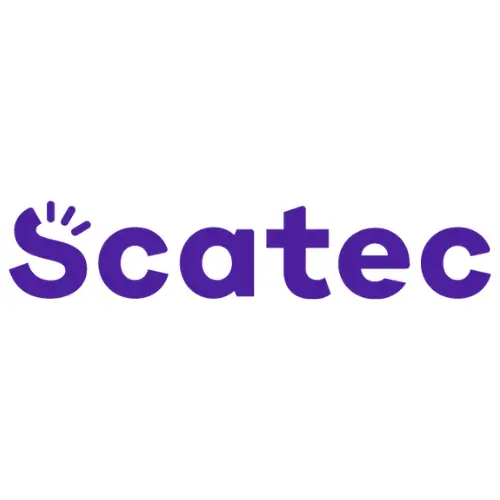
Senior Vice President Engineering and Technology
More Articles on OPC UA
Information Exchange in Edge-to-Cloud Applications Based on OPC UA!
To support communication from the field level to the cloud, the OPC Foundation has developed information models for semantic information exchange (IMS). These include specific structures and concepts such as modeling data and defining types. These models serve as the basis for the semantic exchange of information between different components in an OPC UA network.
OPC UA offers two communication models:
- Client/Server (e.g. via TCP or WebSockets)
- Publish/Subscribe (e.g. via UDP or MQTT)
As OPC UA works independently of a specific transport protocol (OPC UA is an IEC standard), the standard defines the specification of data structures, protocols, and communication mechanisms. However, the transport protocol is not defined. This means that OPC UA defines the semantics and the behavior of the data to be transferred, and at the same time, supports various transport protocols. This makes OPC UA the first manufacturer-independent multi-cloud standard.
IT companies have developed OPC UA Cloud Libraries based on this IMS. Their aim is to simplify the integration of OPC UA in cloud computing environments. They enable developers to create cloud-native applications that can communicate seamlessly with OPC UA-enabled devices and systems. This means that semantic information and live data from the periphery can be used directly in cloud environments.
These OPC UA Cloud Libraries are essentially software development kits (SDKs) designed specifically for the integration of OPC UA into cloud-based applications. They offer functions for establishing connections to OPC UA servers and exchanging data via the OPC UA protocol, such as authentication methods, data models, scalability methods, the provision of application programming interfaces (APIs), and integrations with cloud services such as databases, storage solutions, or analysis platforms.
OPC UA over TSN
The Advantages of OPC UA over TSN
- Real-time communication
- Deterministic
- Minimal latency times
- Robot control
- Artificial intelligence
The integration of OPC UA with Time-Sensitive Networking (TSN) was published by the OPC Foundation in 2018. Benefit: Real-time communication via standardized Ethernet networks becomes possible. By integrating OPC UA over TSN, different devices and systems in factory automation can communicate seamlessly with each other. This increases the efficiency and flexibility of production processes.
For digitalization in industry, this means that machine networks that want to use real-time control must include predictable sources of error in decisions, want to predict production performance more accurately, and thus, increase overall efficiency, require deterministic response times and minimal latency. OPC UA over TSN works like a real-time operating system. By combining OPC UA and TSN, industrial automation systems can exchange data in real time, which is critical for applications such as production equipment control, robotics and industrial IoT.
The integration of OPC UA with Time-Sensitive Networking (TSN) was published by the OPC Foundation in 2018. Benefit: Real-time communication via standardized Ethernet networks becomes possible. By integrating OPC UA over TSN, different devices and systems in factory automation can communicate seamlessly with each other. This increases the efficiency and flexibility of production processes.
For digitalization in industry, this means that machine networks that want to use real-time control must include predictable sources of error in decisions, want to predict production performance more accurately, and thus, increase overall efficiency, require deterministic response times and minimal latency. OPC UA over TSN works like a real-time operating system. By combining OPC UA and TSN, industrial automation systems can exchange data in real time, which is critical for applications such as production equipment control, robotics and industrial IoT.
The Advantages of OPC UA over TSN
- Real-time communication
- Deterministic
- Minimal latency times
- Robot control
- Artificial intelligence
OPC UA Pub/Sub
The OPC UA Publisher/Subscriber (Pub/Sub) was published for the first time in 2017. This was part of the OPC UA specification version 1.04, which contains a new method for data transmission. In addition to client/server communication, publisher/subscriber communication is now also possible.
The publisher/subscriber method allows the asynchronous distribution of data and events over the network. This way, scalable communication can be realized in distributed systems. This method is advantageous for certain requirements. Devices and software can also communicate with each other without client/server communication. Communication now takes place directly between publisher and subscriber. This speeds up communication.
This development step became necessary as more and more requirements for high-performance and real-time capable applications were placed on OPC UA. This is primarily due to the progress made in industrial communication. OPC UA Pub/Sub supports modern network technologies such as Time-Sensitive Networking (TSN), for example. Networked IIoT environments require digressions: The Publisher/Subscriber (Pub/Sub) methodology is also offered by the MQTT message protocol. However, this communication path is more challenging because OPC UA Pub/Sub already knows the OPC UA data structures, which is not the case with MQTT.
OPC UA Offers Various Security Mechanisms
- Encryption of the data transmission between client and server ensures the confidentiality of the transmitted information. Asymmetric encryption algorithms such as RSA (1977) and symmetric encryption algorithms such as the Advanced Encryption Standard (AES, 2002) are used for this purpose. 128- or 256-bit encryption, message signing, packet sequencing, and user authentication are used to secure the data during transmission.
- OPC UA enables authentication solutions for users and systems to ensure that only authorized entities can access resources. This is typically done via certificates.
- In addition to authentication, OPC UA also supports the authorization (via roles and permissions) of users and systems to determine which actions and resources may be used by a particular entity.
- Data signatures ensure the integrity of the transmitted information in order to detect tampering during transmission.
- OPC UA supports the logging of events and activities to ensure the complete traceability of actions and operations. This facilitates the evaluation of security incidents and adherence to compliance requirements.
Partners Spezialized in OPC UA-Enabled Solutions
OPC UA Interoperability Standards and Specifications
The OPC Foundation has developed and adopted several standards and specifications that help to promote interoperability and integration in industrial automation.
1. OPC Classic (1996)
These are older versions of the OPC standard based on the Distributed Component Object Model (DCOM). OPC Classic comprises various parts, including Data Access, Alarm & Events, and Historical Data Access, each covering specific aspects of data communication and data management in industrial automation.
2. OPC UA (2008)
OPC UA is an open, platform-independent communication standard for industrial automation. It offers secure, reliable, and interoperable communication between different systems and devices, regardless of manufacturer or type.
3. OPC UA Information Models and Companion Specifications (OPC UA for Machinery 2012)
These documents define the semantic structure of data and information used in OPC UA systems, as well as specific models and standards for different applications and industries.
Since 2012, the OPC Foundation has published a series of Companion Specifications that focus on different industries and application areas, including digitization in the automotive industry, digitization in the energy industry, robotics, building automation, digitization in healthcare, and many others. Each Companion Specification defines specific models, data types, and functions that are relevant for the respective industry or application.
4. OPC UA Pub/Sub (2017)
This extension of the OPC UA standard enables the asynchronous distribution of data and events over a network. OPC UA Pub/Sub was developed to meet the requirements for high-performance and real-time capable applications, and to improve the scalability and efficiency of OPC UA systems.
5. OPC UA for Devices (2015)
This is a special variant of OPC UA that was developed for the integration of devices and embedded systems OPC UA for Devices provides a simple implementation of OPC UA and enables the seamless integration of devices into OPC UA networks.
6. OPC UA via TSN (2018)
OPC UA TSN is not a standard, but the integration of OPC UA via the Time-Sensitive Networking (TSN) protocol. TSN itself stands for a series of standards defined by the IEEE (Institute of Electrical and Electronics Engineers) for the optimization of Ethernet networks for real-time communication.