Rocket Program TEXUS
Airbus Defence and Space
Airbus Defence and Space is part of the Airbus Group. The division specializes in military and civil space systems. Airbus Defence and Space also carries out research and development work for the production of defense and space-oriented equipment, including military aircraft, launch vehicles and spacecraft. In addition, the company offers related services such as cyber security and military intelligence.
Founded in January 2014, the business segment is based on three main pillars: Military Aircraft (MiAS), Space Systems and Connected Intelligence (CI). As of 2023, Airbus Defense and Space is represented in 35 countries and employs around 34,000 people from over 86 nations. The business segment's main sites are located in France, Germany, Spain, the UK, Italy, the Netherlands and South Africa.
Technological Experiments in Zero Gravity
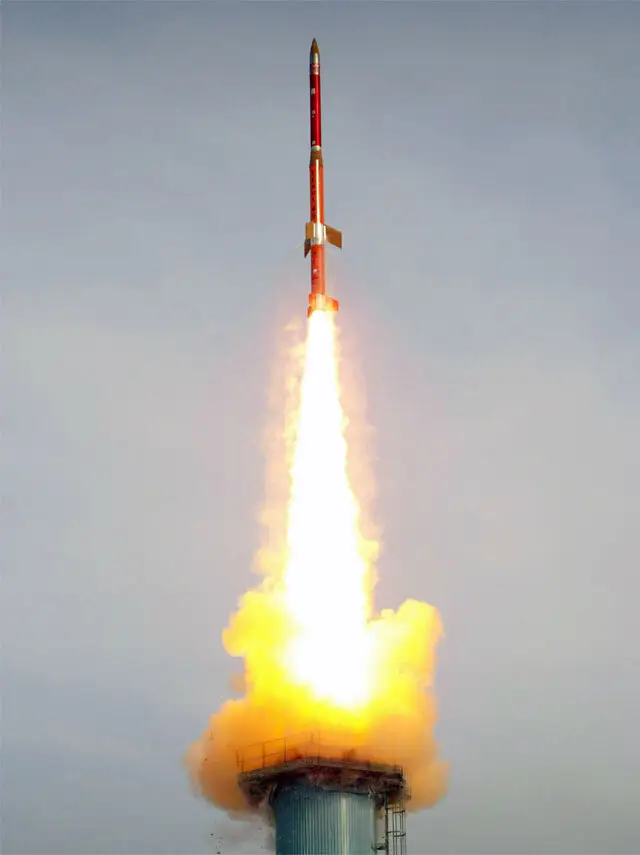
The first research rocket, TEXUS 1, was launched on December 13th 1977, and a further 59 unmanned research rockets have been successfully launched and landed. Since December 2005, the two-stage VSB-30 launcher from Brazil, which was specially developed for TEXUS, has been in use.
The abbreviation TEXUS stands for ‘Technological Experiments in Zero Gravity’. In 1976, the groundwork was laid for the TEXUS research program, which was initially a national program.
To date, 60 research missions have been successfully carried out as a European-German sounding rocket program. The project was commissioned by the German Aerospace Center (DLR) and the European Space Agency (ESA).
TEXUS has been funded by the Federal Ministry of Economics and Climate Action (BMWK) since the very beginning. In addition, numerous research institutes and universities worldwide are actively contributing to the further development of this project. They carry out biological, material science, and physical experiments on board the unmanned research rocket.
The space conditions of zero gravity are crucial here. Today, TEXUS is the longest-running rocket program for scientific experiments and technology testing in zero gravity.
The abbreviation TEXUS stands for ‘Technological Experiments in Zero Gravity’. In 1976, the groundwork was laid for the TEXUS research program, which was initially a national program.
To date, 60 research missions have been successfully carried out as a European-German sounding rocket program. The project was commissioned by the German Aerospace Center (DLR) and the European Space Agency (ESA).
TEXUS has been funded by the Federal Ministry of Economics and Climate Action (BMWK) since the very beginning. In addition, numerous research institutes and universities worldwide are actively contributing to the further development of this project. They carry out biological, material science, and physical experiments on board the unmanned research rocket.
The space conditions of zero gravity are crucial here. Today, TEXUS is the longest-running rocket program for scientific experiments and technology testing in zero gravity.
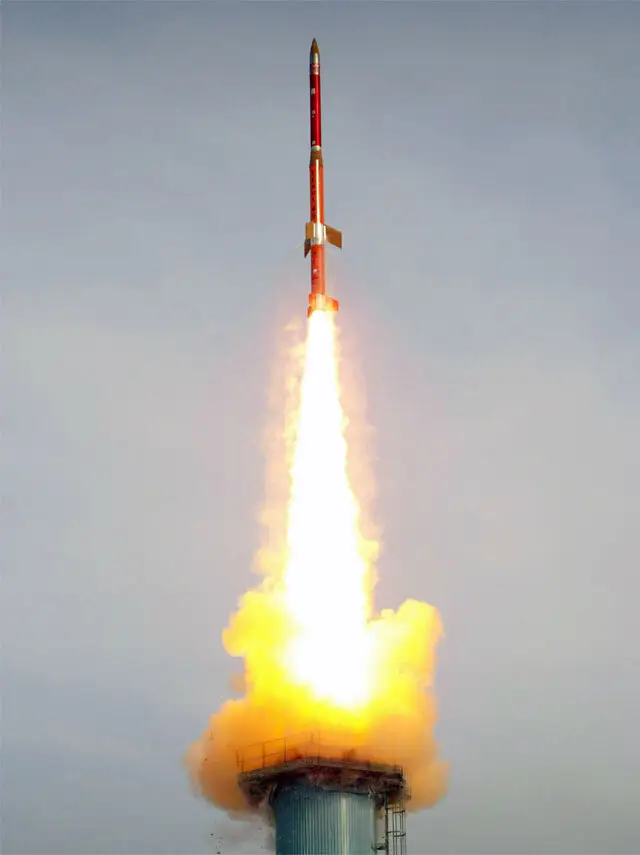
The first research rocket, TEXUS 1, was launched on December 13th 1977, and a further 59 unmanned research rockets have been successfully launched and landed. Since December 2005, the two-stage VSB-30 launcher from Brazil, which was specially developed for TEXUS, has been in use.
Airbus is Europe's largest aerospace company and one of the leading companies in the aviation industry worldwide. Airbus is headquartered in Leiden (The Netherlands). With 147,893 employees from 147 countries, Airbus operates in more than 180 locations worldwide and works with around 18,000 direct suppliers on a global scale.
Mobile Rocket Base
Sounding Rockets
Sounding rockets carry scientific and technological experiments to the edge of space before returning to Earth as a 5-meter-long payload from an altitude of 250 kilometers. TEXUS enables biological, material science and physical experiments to be carried out in microgravity. Typically, there are three to four experiment modules on board, each of which fulfills specific study purposes.
The flight of an unmanned research rocket lasts up to 15 minutes. The actual period of zero gravity only lasts 6 minutes. The rocket itself is 13meters long, has a diameter of 45cm and a total mass of 2,680kg. With a payload capacity of 400kg, TEXUS can accommodate experiments with a mass of up to 280kg. The length of the payload module is 5.3 meters. The diameter is 438mm.
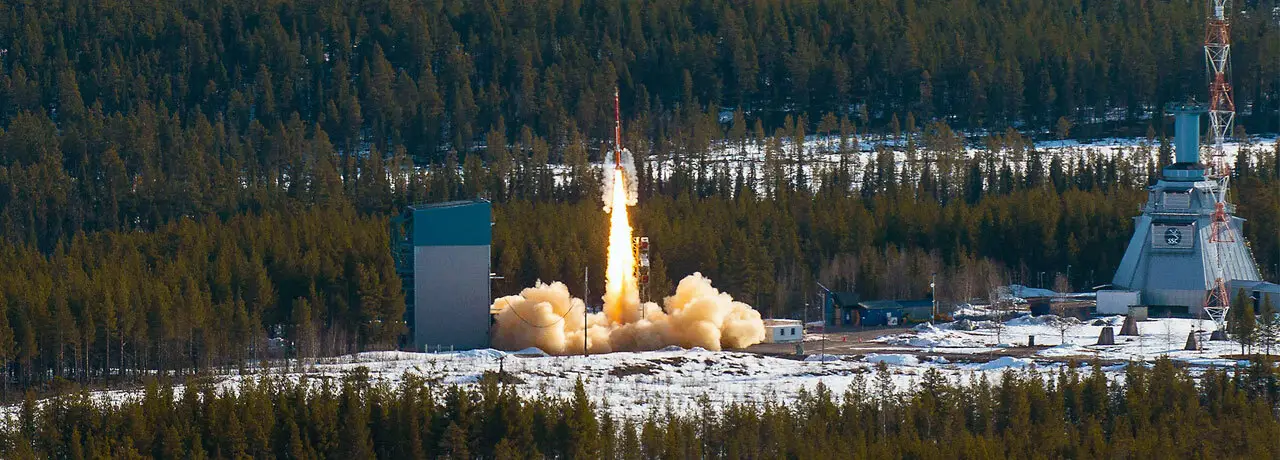
The 60th rocket, the TEXUS 60, was successfully launched on March 24th 2024 from Esrange Space center in Kiruna, Sweden. The rocket reached an altitude of 251 km and spent 362 seconds in zero gravity. The payloads included two experiments from the German Aerospace Center (DLR) called Simona and GECO, as well as a joint project between DLR and the Japanese space agency JAXA called Phoenix 2.
Research Experiments on Board the TEXUS
- SIMONA The Space Investigation of MONotectic Alloys experiment aims to analyze phase separation processes in a monotectic alloy in order to improve the models for the material behavior during segregation or mixing in melts.
- GECO In the Gravity Elicited Calcium Oscillations experiment, scientists use a fluorescence microscope with a 3D scanning laser to observe living cells under microgravity conditions. In doing so, they capture 3D images to investigate changes in the calcium concentration.
- PHOENIX II The aim is to investigate combustion processes in zero gravity and the spontaneous ignition of fuel droplets in order to increase combustion efficiency, particularly for more environmentally friendly engines and fuels. A better understanding of these processes could significantly increase their efficiency.
- SaFari Researching the crystallization of liquid silicon under microgravity to develop more accurate predictions and models of its crystallization behavior. Silicon is crucial for solar cells; therefore, it is important to improve production to drive the green transformation.
- TOPOFLAME This experiment investigates the behavior of a flame in microgravity by burning a fuel under constant gas pressure, similar to the conditions in spacecraft. The main aim is to improve safety on board spacecraft by investigating how fire spreads in microgravity.
- T-REX Conducting biological studies on human cells, the so-called T lymphocytes. Research into the mechanisms of microgravity perception in mammalian cells.
Research Rocket Flight
During its ballistic trajectory, a research rocket reaches a zenith maximum altitude of around 260 kilometers, completing its journey from take-off to landing in around 15 minutes. During this short period of time, the experiments on board are exposed to zero gravity for around six minutes. This is a rare opportunity to gain insights into various phenomena of zero gravity.
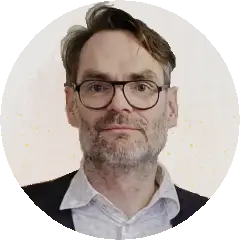
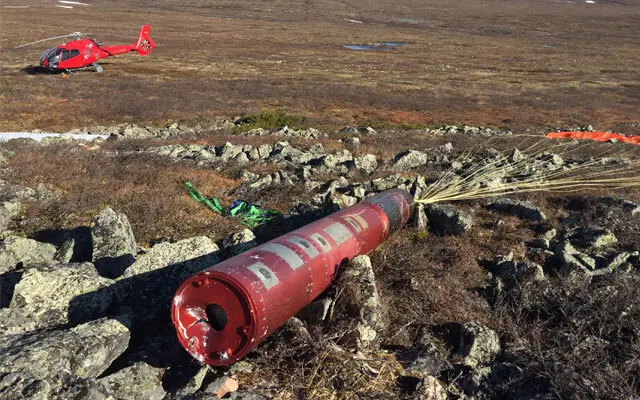
The safe recovery of the payload is facilitated by parachutes and a subsequent recovery by helicopter, organized by Airbus and the Swedish Space Corporation, the operators of Esrange.
OPC UA Integration
First Contact with OPC UA
Airbus Defense and Space was first introduced to OPC UA by its partner company AMS Soft. The partner was already working with OPC UA in the automotive sector and also recommended the solution for flight software. In 2016, an OPC UA project team at Airbus Defence and Space began examining OPC UA as a potential solution for data communication. The first step was to review the options and hurdles for implementing a new system for the TEXUS missile program.
The decision to seriously consider OPC UA as a potential solution resulted from a comprehensive review of the specifications rather than extensive testing. After a thorough review of the standard, Airbus Defence and Space quickly recognized the compatibility of OPC UA with the project requirements. As a result, the integration of OPC UA into the operational processes was carried out immediately.
Step-by-Step to OPC UA
The operational test phase for the integration of OPC UA in TEXUS also began in 2016. Initial preparations were made and definitions drawn up at the start. The first phase was carried out quickly, so that the implementation was completed within a year. The speed of all processes in the first phase was facilitated by the gradual introduction of individual system components instead of a complete OPC UA integration.
In this way, the first components could be quickly integrated into the system. "Although the introduction only covered part of the system in 2017 for organizational reasons, there were no reservations about OPC UA," explains Enrico Noack. At the time, the existing experimental modules were working independently of OPC UA. A gradual introduction of new elements, while retaining the existing systems, was, therefore, necessary.
The solution envisaged that new experiment modules would be fully integrated into OPC UA when they were introduced. Existing modules receive ground adapters in order to operate in parallel with the old Pulse Code Modulation (PCM). This means that the system will still be able to accommodate old modules.
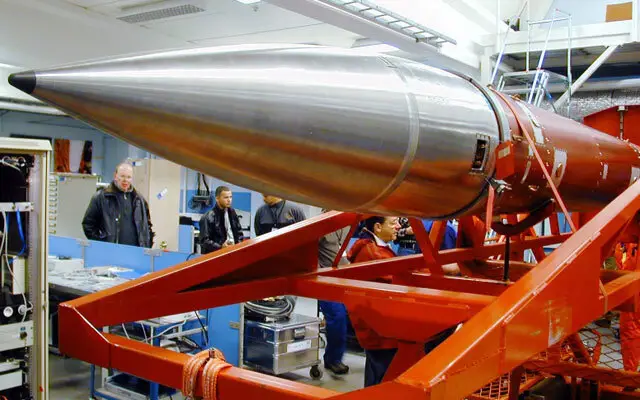
After a thorough examination of the standard, the TEXUS team at Airbus Defence and Space quickly recognized the compatibility of OPC UA with the project requirements.
The adoption of OPC UA has been driven by two key factors: the Ethernet capability and the integrated data model within the server. Ethernet capability enables remote testing and operation, eliminating the need for physical presence. In addition, the embedded data model simplifies the completion of test modules by facilitating easy access and compilation of the required information.
All Modules OPC UA-Compliant by 2025
In the coming months, until the end of 2025, all rocket and ground systems are to be integrated into OPC UA. The TEXUS 60 rocket (launched in March 2024) is the last research rocket and the last launch for which adapters were used. Two experiment modules on board TEXUS 60 were already working with OPC UA. A third was not yet OPC UA compliant. This third module is now to be integrated into OPC UA. When TEXUS 61 is launched, all experiment modules will be integrated into OPC UA. The launch preparation of TEXUS 61, equipped with fully integrated OPC UA modules, is scheduled to begin at the end of 2025.
Data Management With OPC UA
Integration of Devices, Machines, and Sensors with OPC UA
Performance of OPC UA at TEXUS
- With OPC UA, the number of data points per experiment increases from 64 to 4,000.
- OPC UA enables a better insight into the system, as comprehensive communication data can be transmitted in real time.
- System integration is simplified.
- Efficient troubleshooting is made possible, which was previously time-consuming and labor-intensive.
- If data communication fails, data is temporarily stored in the experiment module.
The main elements that are integrated into the system with OPC UA are sensors, actuators, and controllers. The UEIPAC from United Electronic Industries (UEI) is a main component which, as an embedded controller, provides the interface to a range of sensors and actuators. IBV Systems has developed software for this platform, which captures data on the real-time Linux and controls actuators.
Another important device is the Tinker Board from ASUS, which is mainly used on the ground. These embedded systems simplify the use of sensors. Controllers from the Swiss company Meerstetter Engineering are currently used for TEXUS. They are integrated into the system via the UEIPAC which enables communication via OPC UA.
This integration increases operational efficiency by enabling seamless communication via the RS422 module and the execution of commands via OPC UA protocols. The UEIPAC and software convert all received data and commands into OPC UA format, streamlining communication and improving interoperability within the system.
The main elements that are integrated into the system with OPC UA are sensors, actuators, and controllers. The UEIPAC from United Electronic Industries (UEI) is a main component which, as an embedded controller, provides the interface to a range of sensors and actuators. IBV Systems has developed software for this platform, which captures data on the real-time Linux and controls actuators.
Another important device is the Tinker Board from ASUS, which is mainly used on the ground. These embedded systems simplify the use of sensors. Controllers from the Swiss company Meerstetter Engineering are currently used for TEXUS. They are integrated into the system via the UEIPAC which enables communication via OPC UA.
This integration increases operational efficiency by enabling seamless communication via the RS422 module and the execution of commands via OPC UA protocols. The UEIPAC and software convert all received data and commands into OPC UA format, streamlining communication and improving interoperability within the system.
Performance of OPC UA at TEXUS
- With OPC UA, the number of data points per experiment increases from 64 to 4,000.
- OPC UA enables a better insight into the system, as comprehensive communication data can be transmitted in real time.
- System integration is simplified.
- Efficient troubleshooting is made possible, which was previously time-consuming and labor-intensive.
- If data communication fails, data is temporarily stored in the experiment module.
OPC UA Support Specification
Other benefits of OPC UA at TEXUS
- Modules are autonomous and can control experiments independently.
- Basic experiments can also be carried out during communication interruptions.
- After module recovery, scientists have access to all experiment data.
- The integrity of the research results remains guaranteed.
- The housekeeping data collected on board is transmitted in real time to ground systems and devices.
The TEXUS OPC UA support specification includes data types, image types, methods and namespace configurations, and optimizes data management and storage. This ensures standardization and interoperability.
OPC UA has also significantly increased the number of data points per experiment from 64 to 4,000. The efficiency of each research flight and each individual experiment has, thus, been significantly increased, as considerably more scientific data is generated.
In addition, OPC UA provides better insight into the system, as comprehensive communication data can be transferred alongside the measurement data. This simplifies system integration and, if necessary, enables efficient troubleshooting. The search for errors was previously time-consuming and labor-intensive.
The TEXUS OPC UA support specification includes data types, image types, methods and namespace configurations, and optimizes data management and storage. This ensures standardization and interoperability.
OPC UA has also significantly increased the number of data points per experiment from 64 to 4,000. The efficiency of each research flight and each individual experiment has, thus, been significantly increased, as considerably more scientific data is generated.
In addition, OPC UA provides better insight into the system, as comprehensive communication data can be transferred alongside the measurement data. This simplifies system integration and, if necessary, enables efficient troubleshooting. The search for errors was previously time-consuming and labor-intensive.
Other benefits of OPC UA at TEXUS
- Modules are autonomous and can control experiments independently.
- Basic experiments can also be carried out during communication interruptions.
- After module recovery, scientists have access to all experiment data.
- The integrity of the research results remains guaranteed.
- The housekeeping data collected on board is transmitted in real time to ground systems and devices.
Optimized Data Management
OPC UA is used in both the on-board and ground systems. In the on-board system, it is used in the flight software for data capture and experiment control. On the ground, OPC UA is used in displays, archives, and ground systems to enable data access for development engineers. All ground systems and devices are, therefore, OPC UA-compliant and enable centralized control and data conversion via adapters for integration into databases.
The result: Highly efficient data management across different platforms.
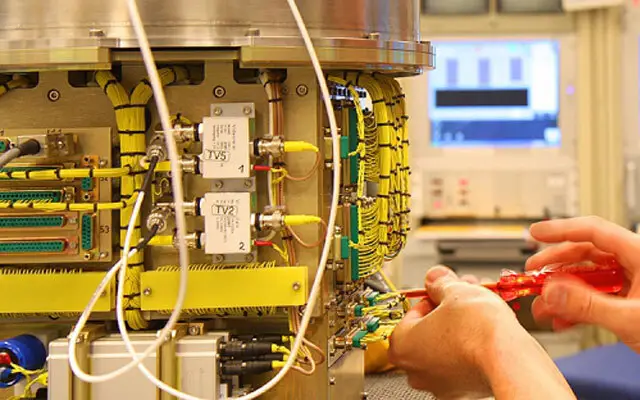
OPC UA transfers changed data efficiently and avoids unnecessary re-transmissions, which is ideal for handling large amounts of data such as the 4,000 measuring points in the TEXUS project.
OPC UA Data Throughput
The maximum data throughput for the Space-to-Ground connection is approximately 5 Mbit/s for all experiments combined. The OPC UA protocol is so lean that an average of 32 Kbit/s per experiment is sufficient. OPC UA transfers changed data efficiently and avoids unnecessary re-transmissions, which is ideal for handling large amounts of data such as the 4,000 measuring points in the TEXUS project.
In addition, only the data required for the scenario in question is transferred. OPC UA significantly increases the performance and efficiency of data transmission.
Challenges and Benefits
The Challenges of OPC UA Integration
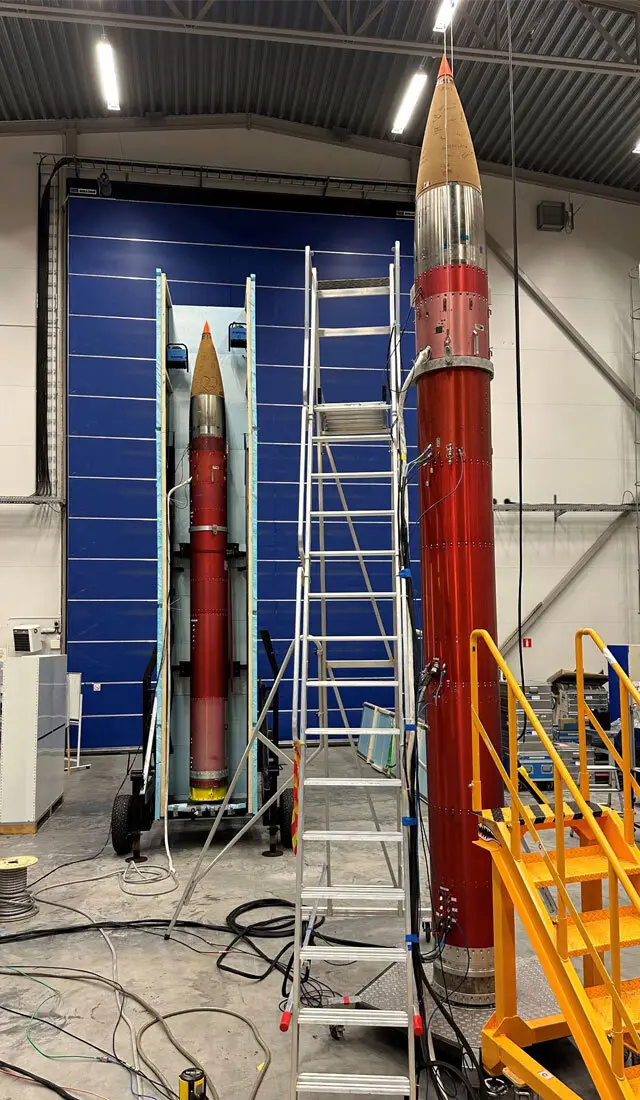
Two modules on board TEXUS 60 already support OPC UA, and a third module will soon be OPC UA-compliant.
The biggest challenge TEXUS faced was the transition of the space-to-ground communication system to Ethernet, replacing the previous communication standard.
While the old standard offered the benefits of a fixed data frame, its inherent inflexibility required adherence to specific protocols, which limited the operation of the system.
Since OPC UA is based on Ethernet, the entire transmission path had to be converted, which required compliance with two standards at the same time.
Initially, bandwidth limitations were a major obstacle, as only 32 kbits/s per experiment were initially available for OPC UA data transmission. Overcoming these challenges required extensive adjustments and persuasion, especially when converting the service system, which is provided by OHB, from the old PCM format to the new standard.
Thanks to early communication initiatives and step-by-step implementation strategies, full Ethernet-based transmission capability was finally achieved.
The biggest challenge TEXUS faced was the transition of the space-to-ground communication system to Ethernet, replacing the previous communication standard.
While the old standard offered the benefits of a fixed data frame, its inherent inflexibility required adherence to specific protocols, which limited the operation of the system.
Since OPC UA is based on Ethernet, the entire transmission path had to be converted, which required compliance with two standards at the same time.
Initially, bandwidth limitations were a major obstacle, as only 32 kbits/s per experiment were initially available for OPC UA data transmission. Overcoming these challenges required extensive adjustments and persuasion, especially when converting the service system, which is provided by OHB, from the old PCM format to the new standard.
Thanks to early communication initiatives and step-by-step implementation strategies, full Ethernet-based transmission capability was finally achieved.
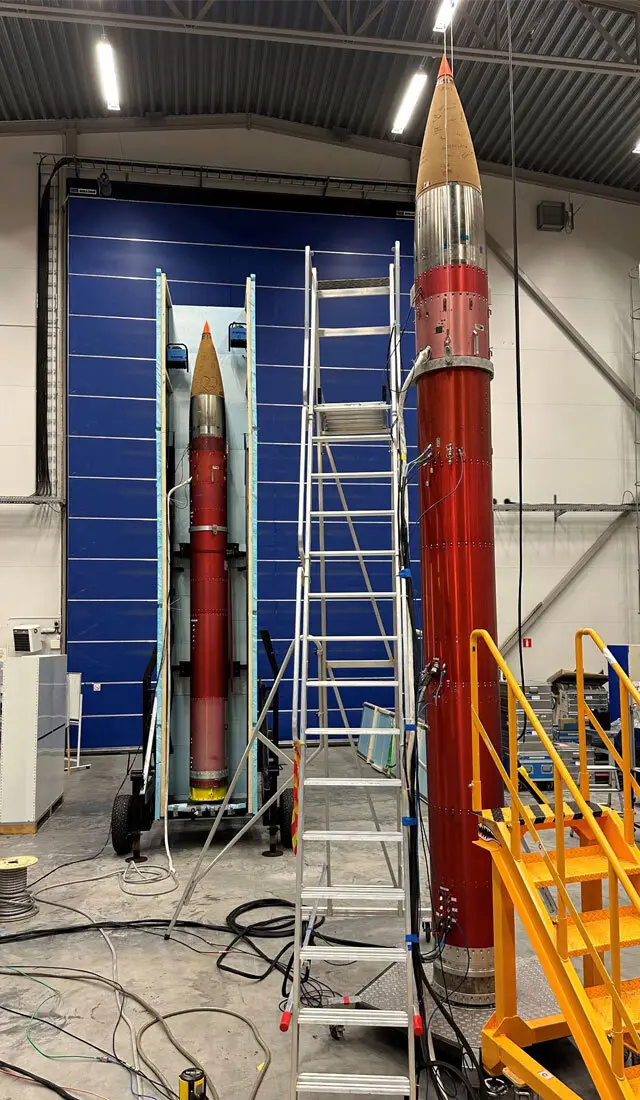
Two modules on board TEXUS 60 already support OPC UA, and a third module will soon be OPC UA-compliant.
OPC UA serves as a data highway known for fast, rich, controlled, and secure data transfer. The OPC Foundation always anticipates our needs, proving their proactive approach, such as with PubSub. In the three years leading up to the implementation, the collaboration with OPC Labs and Unified Automation has been instrumental in our progress and we are very pleased with the achievement of our efforts.
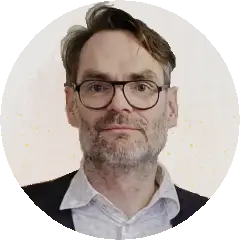
Advantages of OPC UA-based Communication
The biggest advantage lies in the standardization enabled by the use of Ethernet. This ubiquitous interface facilitates the versatile use of experiment modules outside of rocket environments, including use in the ZARM drop tower in Bremen and during parabolic flights.
In addition, the modular instrumentation can now operate independently, as OPC UA stores the data model within the server, enabling seamless operation with a single laptop, without the need for a centralized data management system.
"This increases efficiency, especially when we have to develop up to four experimental modules a year," says Enrico Noack. This streamlined process also allows engineers to customize displays and configure the flight software independently to respond to scientific requirements.
Integration and Modularity
OPC UA's ability for system integration and modularity enables the combination of different systems and functionalities through microservices. The ability to integrate different systems, functions, and even different operating systems, such as Windows and Linux, increases flexibility and interoperability. OPC UA's modular design principle promotes adaptability and collaboration, enabling the seamless integration of partners and their unique capabilities.
The integration of various services, results in a wide software landscape. This landscape needs to be consistently maintained. Together with the University of Applied Science Bremen (HSB) a concept was developed and implemented. The emphasis is on the modularity that underlines the versatility and potential for success of OPC UA in research projects such as TEXUS.
Security and Real-Time Data
Security Measures in OPC UA Deployment
Security considerations are very important in OPC UA deployment scenarios. Various measures are taken to ensure data integrity and protection against cyber threats. These activities have been guided by the Vectano company.
A key approach at TEXUS is the use of separate, secured networks that ensure isolation and protection of sensitive data. For example, the in-flight networks are dedicated exclusively to the experiment, and internal VLANs, within the operating environment, further compartmentalize the experiments to increase security.
External access to the network, for example for monitoring the experiments by the scientists, is restricted, with the data being forwarded to cloud platforms via PubSub. This strategy prevents unauthorized access to the network and, thus, strengthens security measures.
Data Transmission in Real Time
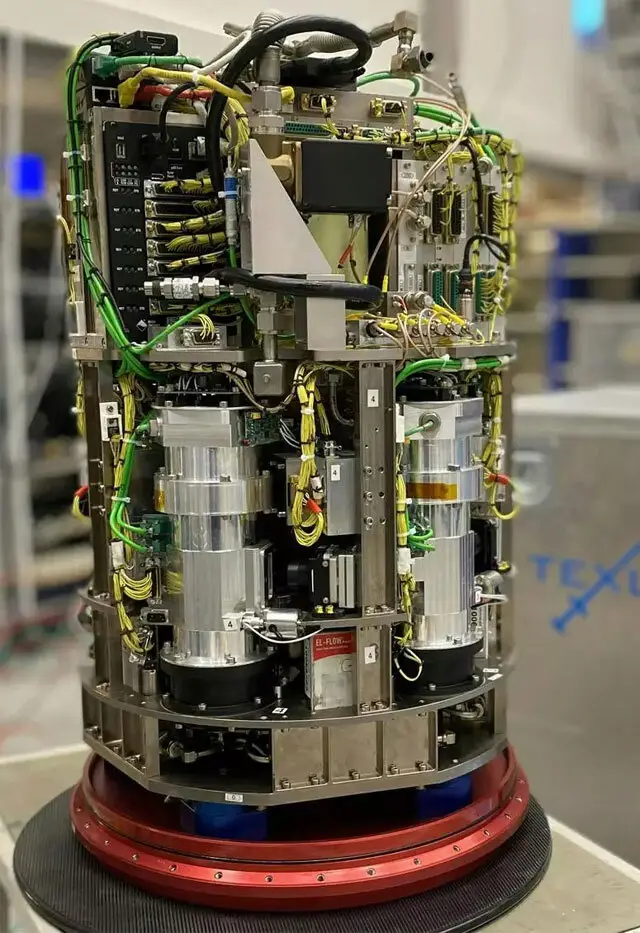
Example of a research module located in the payload.
Real-time data transmission to the various sites involved in TEXUS is ensured by using existing technologies, in particular, cloud-based access for personnel during rocket launches, such as the Esrange.
With the platform developed by the company Humatects, each experiment is assigned its own instance that can be accessed via cloud platforms, allowing users to remotely access and analyze the experiment data via browser applications.
Data is transferred to the cloud via OPC UA, and data retrieval is facilitated by integrating services from external sources, such as those developed for the International Space Station (ISS), which use protocols such as AMQP for data transfer.
Unified Automation provided support in the development of transfer protocols to ensure the compatibility and efficiency of data exchange between OPC UA and the Cloud, optimizing data transfer processes across distributed locations.
Real-time data transmission to the various sites involved in TEXUS is ensured by using existing technologies, in particular, cloud-based access for personnel during rocket launches, such as the Esrange.
With the platform developed by the company Humatects, each experiment is assigned its own instance that can be accessed via cloud platforms, allowing users to remotely access and analyze the experiment data via browser applications.
Data is transferred to the cloud via OPC UA, and data retrieval is facilitated by integrating services from external sources, such as those developed for the International Space Station (ISS), which use protocols such as AMQP for data transfer.
Unified Automation provided support in the development of transfer protocols to ensure the compatibility and efficiency of data exchange between OPC UA and the Cloud, optimizing data transfer processes across distributed locations.
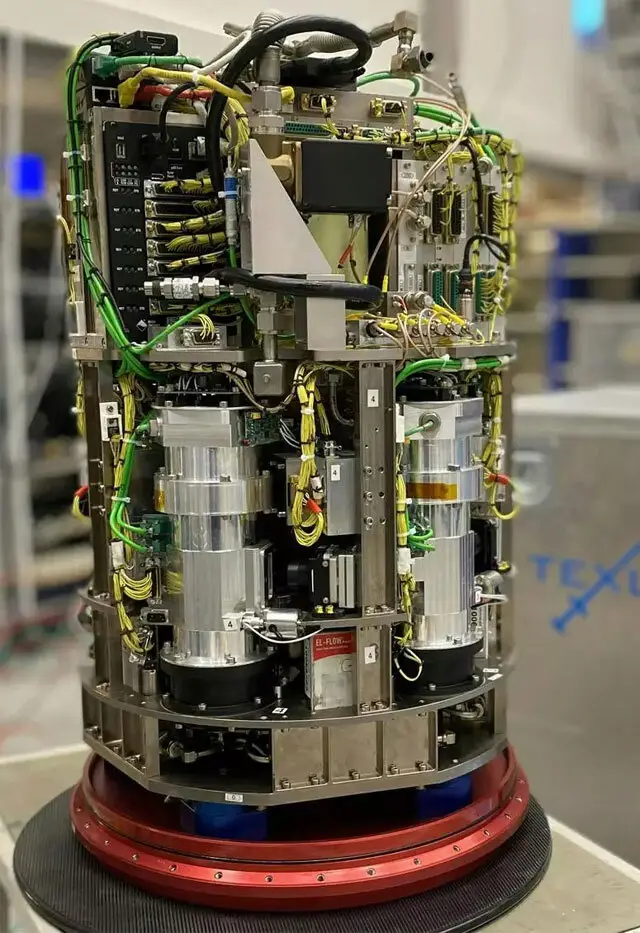
Example of a research module located in the payload.
Unified Automation
Since 2007, Unified Automation has been offering libraries for application development and software tools for the effective use of OPC UA, making it one of the most mature providers of commercial OPC UA technology. Many major automation manufacturers, solution providers and end users rely on Unified Automation's professional OPC UA products and services.
We have been advising Airbus on their OPC UA integration from the very beginning. The functionality of OPC UA and the mature implementation of our commercial toolkits enable the reliable use in a highly complex system such as the TEXUS research rocket. Modularity is achieved through standardized data models that communicate securely and in real time, whereby Airbus is requiring, and successfully using, the full range of OPC UA technologies.
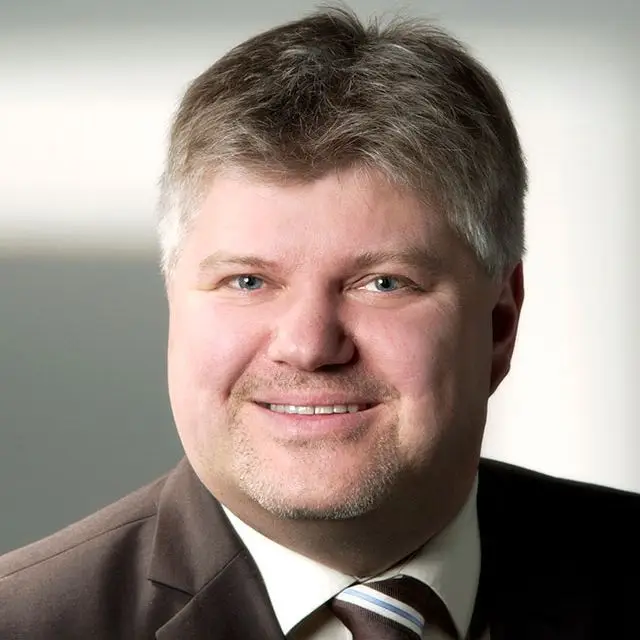
Further Advancement with OPC UA: Interface Development with AI
One of the current advancements in OPC UA is the development of an interface to artificial intelligence (AI). This initiative aims to build a bridge between OPC UA and AI technology, particularly in the creation of an operator assistance system. The integration of AI promises to provide indispensable support for the operation of complex test and experimental facilities, which generally require technical expertise.
By using such an operator assistance system, scientists gain improved access to experimental setups and can, thus, expand their use. Various Airbus departments are involved in this collaboration in order to jointly explore possibilities and optimize functionality.