The Automation of Production
In simple terms, the industrial sector is described as the 'industrial production of tangible goods in a factory system'. Production can relate to all conceivable goods.
Due to the processing of raw materials, the industrial sector belongs to the secondary sector of the economy. It is characterized by the further processing of goods from the primary sector. Industry is therefore material-intensive. It is also capital-intensive due to the production process and the use of capital goods.
Outstanding features of industry are systematic mass production, the use of standardized processes, and a regulated and structured form of production. Larger production companies are also characterized by a high degree of automation, mechanization, and process control. In most cases, the IT-supported production processes are designed to be scalable.
Which Manufacturing Industries Are Included?
The manufacturing industry includes all sectors that convert raw materials into finished products. It plays a central role in the global economy and can be divided into different categories. This list shows only a part of the different industries in the world. Each of these industries contributes to the global economy in its own way by providing specialized products and services that are needed in daily life, as well as in other sectors of the economy. Some of the following industries belong to both the primary and secondary sectors.
- The automotive industry produces cars, trucks, motorcycles, and vehicle parts.
- The tire industry includes the production of tires for all types of vehicles.
- Mechanical engineering produces industrial machinery, large-scale plants, conveyor systems, agricultural machinery, construction machinery, and machine tools. It also includes small parts and components such as grippers or frames.
- The chemical industry specializes in the production of chemicals, fertilizers, paints, plastics, and synthetic fibers.
- The food and beverage industry produces food, beverages, and processed foods.
- The textile and clothing industry produces fabrics, textiles, and clothing.
- The pharmaceutical industry produces medicine, medical devices, and biotechnological products.
- The electronics and electrical appliances industry manufactures computers, consumer electronics, household appliances, and industrial electronic components. It also includes the manufacture of robots.
- The wood and paper industry processes wood into furniture, paper, pulp, and other products.
- The aerospace industry manufactures airplanes, spacecraft, and related equipment.
- The energy and raw materials industry specializes in the manufacture of equipment for energy production as well as the extraction and processing of oil, gas, coal, and other raw materials. It can therefore be classified as either a primary or secondary sector.
- The medical and laboratory technology industry focuses on the production of medical instruments, diagnostic devices, and laboratory equipment.
Wireless IoT Technologies in Industry
Products Designed for the Manufacturing Sector
In principle, all wireless technologies and the corresponding products are used in industry. However, the level of integration and functionality in the industrial process varies. UHF RFID systems play a very important role alongside OPC UA, RTLS, and 5G. Overall, however, it can be said that the interplay of technologies is becoming increasingly sophisticated and complex. The interoperability of products is therefore an advantage.
The area of sensor technology now occupies a key position, as it is no longer just pure labelling and identification that optimizes the process, but primarily the processing of sensor data. Alongside the automotive industry, the industrial sector is the most digitized and automated economic sector. Accordingly, the penetration of wireless IoT products, technologies, and solutions is highest in this sector.
The Status Quo of Wireless IoT Solutions in Industry
All of the examples in the following list are aimed at the digitalization and automation of production processes and logistics movements. They generate data streams and thus, the basis for AI-based solutions and sustainability in companies.
This makes them part of an Industry 4.0 strategy. Especially when sensor data is generated that allows conclusions to be drawn about the location or condition of the object. Conclusion: A reduction of CO2 emissions, increased connectivity, and energy savings.
- Authentication Solutions on Machines: Deny unauthorized access | grant qualified access | reduce accidents at work | protects against sabotage | process control and documentation of all actions and decisions | error traceability
- Asset Tracking and IoT Asset Management: Precise inventory monitoring | reduction of acquisition costs and storage space | ensuring availability | anti-theft protection | real-time localization | increased efficiency | demand-oriented maintenance and servicing | traceability | optimized logistics planning | data as the basis for AI in companies
- Positioning and Real-Time Localization: Precise monitoring of systems, machines, devices, tools, and products | reduction of search times | optimized maintenance processes | movement patterns and AI | improved productivity | work safety | anti-theft protection | digitalization of the supply chain
- Digitalization of the Supply Chain: Increased transparency | real-time monitoring of the supply chain | inventory accuracy | automated ordering systems and AI-supported forecasting models | optimized transport routes and production processes | resource efficiency | cost reduction | more precise delivery times | reliable supply chain | customer satisfaction | demand-oriented planning | optimized risk assessment
- Maintenance and Predictive Maintenance: Prevention of failures | machine status data in real time | increased process reliability | reduced maintenance requirements | reduced maintenance costs | increased safety | extended service life | need-based maintenance | optimization of spare parts logistics | work safety
- Condition Monitoring: Early detection of problems | monitoring of operating states | avoidance of machine failures | reduction of wear and tear | reduction of downtimes | production safety | extension of system service life | optimization of maintenance schedules | cost reduction | monitoring of critical machine components | data analysis
- Container Management: Optimized transport and storage processes | demand-oriented use, circulation and quantity | reduction of empty runs and waiting times | cost reduction | minimization of container damage | optimal capacity utilization | traceability and transparency | more reliable supply chain | optimized cleaning cycles
- Temperature Monitoring: Quality assurance | precise control of process temperatures | reduced safety risks | process efficiency | occupational safety | longer equipment service life | compliance with legal regulations | energy savings | cooling system management | longer product shelf life
- Permanent Inventory: Up-to-date inventory data | precise production control | continuous inventory monitoring | reduction of downtimes | lower warehousing costs | quick response to market changes | reduction of inventory differences | less effort required for annual stocktaking
- Industrial Identification: Traceability | facilitated warehousing | correct components and production processes | faster throughput times in production | provision of handling instructions or expiry dates | localization | authenticity | link to safety-relevant information such as hazard classes or handling | automation of production processes | brand image and support for marketing strategies
- Traceability: Traceability of origin and materials | reduction of quality problems | compliance with quality standards | improved risk management | increased supply chain efficiency | transparency | rapid response to market changes | compliance with legal regulations | counterfeit protection | targeted recall management
- Data Management: Better decision-making | data analysis | process optimization | continuous process monitoring | identification of inefficiencies and bottlenecks | reduction of energy consumption | identification of material waste | early detection of quality deviations | risk management | AI solutions | new business models | transparency
More than 50 Percent of All OEM Devices to be IoT-Enabled by 2026
Strong growth is expected for the global market for the Industrial Internet of Things (IIoT). The projected growth rate is 23.2 percent bewteen 2024 to 2030. This upward trend is primarily driven by the increasing Industry 4.0 initiatives, the ongoing implementation of advanced automation systems, the introduction of new technologies, the trend towards smart factories, and government incentives to support the adoption of industrial IoT.
According to a report by ‘IoT Analytics’, original equipment manufacturers (OEMs) have made significant progress in their IoT strategies. This has been achieved through the integration of innovative software, enhanced services, and redesigned business models. It is expected that more than 50 percent of OEM products will be IoT-enabled by 2026. In 2023, there were more than 16 billion active IoT devices worldwide. On average, 40 percent of products sold in 2023 were connected, and this figure is expected to rise to 54 percent by 2026.
A concrete example of the application of IoT solutions in industry is the OEM Schindler, which installed more than 500,000 IoT-networked elevators worldwide. In the automotive industry in particular, the proportion of connected products is expected to increase significantly from 34 percent to 54 percent by 2026. This trend reflects the rapid development of IoT integration in the modern production landscape.
Warehouse Control and Pallet Tracking at KEB Automation
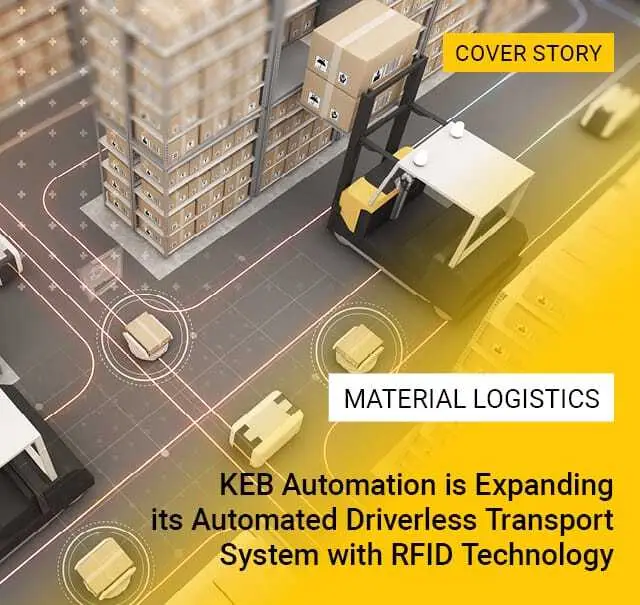
KEB Automation, a specialist in drive and control technology, uses RFID technology for warehouse control and pallet tracking. The RFID tags contain a unique handling unit (HU) number. This is used to identify the load carriers in SAP Extended Warehouse Management (EWM).
The picked pallets are provided for the automated guided vehicle system (AGV) in the automated warehouse via a conveyor system. From there, the pallets are transported to the production halls. At the transfer points between the forklift and the AGV, 20 Q5X sensors from Turck are installed at a height of three meters. These sensors detect the presence of the pallets for transportation. As soon as the sensor detects a pallet, a transport order is generated for the DTS. The pallet is then picked up by the DTS and guided through an RFID gate. In this way, the HU information is received by SAP EWM.
External antennas are used to capture the RFID tags on each pallet. A read rate of almost 100 percent is achieved. These antennas are mounted on both sides of the hall door and connected to a Q300 UHF RFID reader. This enables the load to be identified regardless of the position of the pallet. When passing the RFID gate, the DTS sends a request to a middleware. This middleware collects the pallet information from the antenna and then queries the SAP system for the pallet's destination. The collected data is then transmitted to the DTS.
KEB Automation, a specialist in drive and control technology, uses RFID technology for warehouse control and pallet tracking. The RFID tags contain a unique handling unit (HU) number. This is used to identify the load carriers in SAP Extended Warehouse Management (EWM).
The picked pallets are provided for the automated guided vehicle system (AGV) in the automated warehouse via a conveyor system. From there, the pallets are transported to the production halls. At the transfer points between the forklift and the AGV, 20 Q5X sensors from Turck are installed at a height of three meters. These sensors detect the presence of the pallets for transportation. As soon as the sensor detects a pallet, a transport order is generated for the DTS. The pallet is then picked up by the DTS and guided through an RFID gate. In this way, the HU information is received by SAP EWM.
External antennas are used to capture the RFID tags on each pallet. A read rate of almost 100 percent is achieved. These antennas are mounted on both sides of the hall door and connected to a Q300 UHF RFID reader. This enables the load to be identified regardless of the position of the pallet. When passing the RFID gate, the DTS sends a request to a middleware. This middleware collects the pallet information from the antenna and then queries the SAP system for the pallet's destination. The collected data is then transmitted to the DTS.
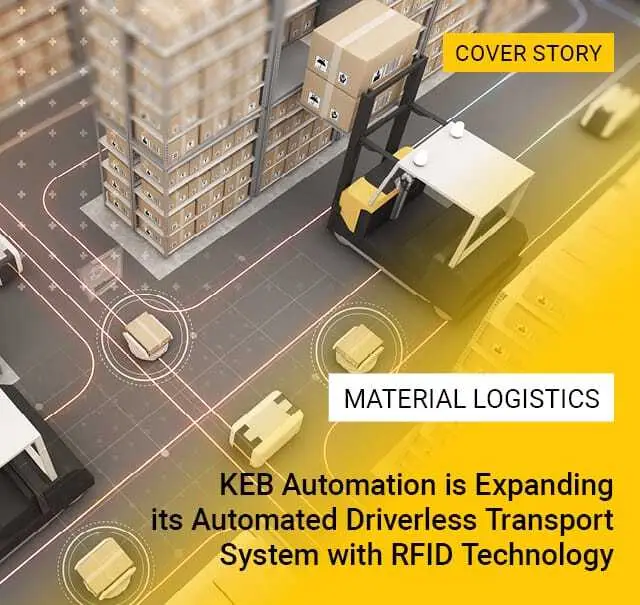
"Turck's solution provides us with the desired transparency without time-consuming manual effort. The RFID tags are captured entirely automatically so that warehouse tasks from the SAP Extended Warehouse Management System can be carried out or processed at the same time."
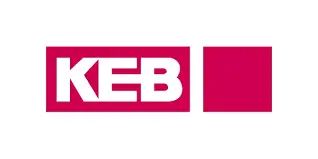
Viktor Derksen
Head of Industrial Engineering
Optimized Washing Machine Production with OPC UA
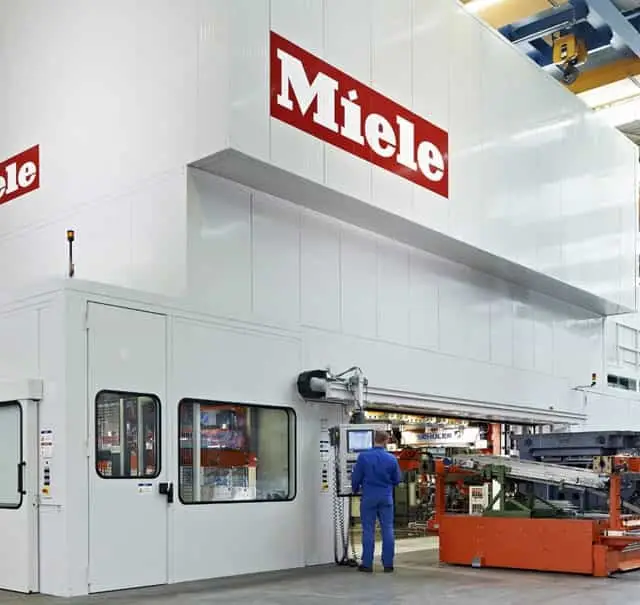
Miele, a supplier of premium domestic appliances, has been using OPC UA from the OPC Foundation since 2018 to modernize and simplify data communication in the press and body shop of washing machine production. Within three weeks, the old system was replaced and new communication levels, including the OPC UA interfaces, were integrated in the press shop in Gütersloh.
In washing machine production, a material flow simulator uses the data transmitted via OPC UA to test various production scenarios. This data forms the basis for optimizing production. Initially, the production planning data from SAP with set-up times, costs, capacities, work shifts, and material numbers was linked to the real plant data. Interfaces were integrated and data format standards defined so that the data could be retrieved via OPC UA.
What is OPC UA good for? OPC UA not only enables the generation, processing, and evaluation of data, but also the seamless transfer of data to other systems. Live data is retrieved from data sources by the material flow simulator via the OPC UA interfaces. This enables production signals, for example from the press shop, to be transferred to the simulator in a matter of seconds. Plant status data is recorded and visualized in the simulator. The systems are already depicted as virtual 3D models in the simulator. Simulation models and 'digital twin' concepts can be implemented by enriching them with real data.
Miele, a supplier of premium domestic appliances, has been using OPC UA from the OPC Foundation since 2018 to modernize and simplify data communication in the press and body shop of washing machine production. Within three weeks, the old system was replaced and new communication levels, including the OPC UA interfaces, were integrated in the press shop in Gütersloh.
In washing machine production, a material flow simulator uses the data transmitted via OPC UA to test various production scenarios. This data forms the basis for optimizing production. Initially, the production planning data from SAP with set-up times, costs, capacities, work shifts, and material numbers was linked to the real plant data. Interfaces were integrated and data format standards defined so that the data could be retrieved via OPC UA.
What is OPC UA good for? OPC UA not only enables the generation, processing, and evaluation of data, but also the seamless transfer of data to other systems. Live data is retrieved from data sources by the material flow simulator via the OPC UA interfaces. This enables production signals, for example from the press shop, to be transferred to the simulator in a matter of seconds. Plant status data is recorded and visualized in the simulator. The systems are already depicted as virtual 3D models in the simulator. Simulation models and 'digital twin' concepts can be implemented by enriching them with real data.
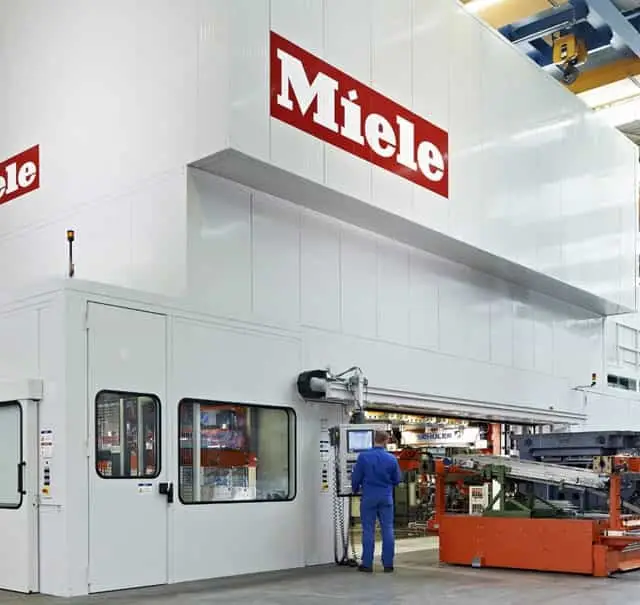
"The high security level of OPC UA is a significant factor for Miele. Communication with OPC UA works according to the 'secure by default' principle. All data is encrypted and transmitted securely. These security standards are used to transfer the laundry's systems and production data to Microsoft's Azure Cloud."
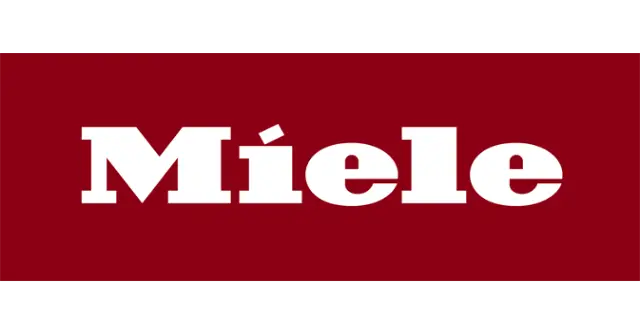
Christian Stickling
Information Technology in Appliance
Minimizing Errors in Pharmaceutical Production with RFID
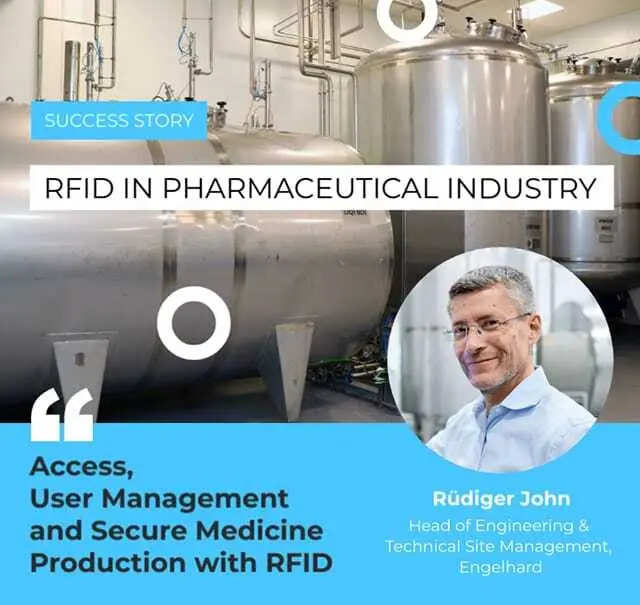
The pharmaceutical manufacturer Engelhard Arzneimittel minimizes production errors through RFID and automation. In the production of medicine, hose connections must be correctly selected and sealed. Engelhard has fitted the ends of these hoses with passive RFID tags to ensure that the hoses are connected correctly, and to eliminate possible errors in the hose connections. The hose socket is equipped with two guiding rings.
The loose inner ring is weighted and can be rotated freely. The RFID chip moves with the loose ring. This ensures that it is always in the correct position for reading, regardless of the direction in which the employee turns the hose. Only one read head is required to read the tag. This is attached to the hose connection. As soon as the operator connects the hose, he immediately confirms this process in the control system. The system then reads the tag. The next process step is only initiated once the control software has recognized the correct hose connection.
The pharmaceutical manufacturer Engelhard Arzneimittel minimizes production errors through RFID and automation. In the production of medicine, hose connections must be correctly selected and sealed. Engelhard has fitted the ends of these hoses with passive RFID tags to ensure that the hoses are connected correctly, and to eliminate possible errors in the hose connections. The hose socket is equipped with two guiding rings.
The loose inner ring is weighted and can be rotated freely. The RFID chip moves with the loose ring. This ensures that it is always in the correct position for reading, regardless of the direction in which the employee turns the hose. Only one read head is required to read the tag. This is attached to the hose connection. As soon as the operator connects the hose, he immediately confirms this process in the control system. The system then reads the tag. The next process step is only initiated once the control software has recognized the correct hose connection.
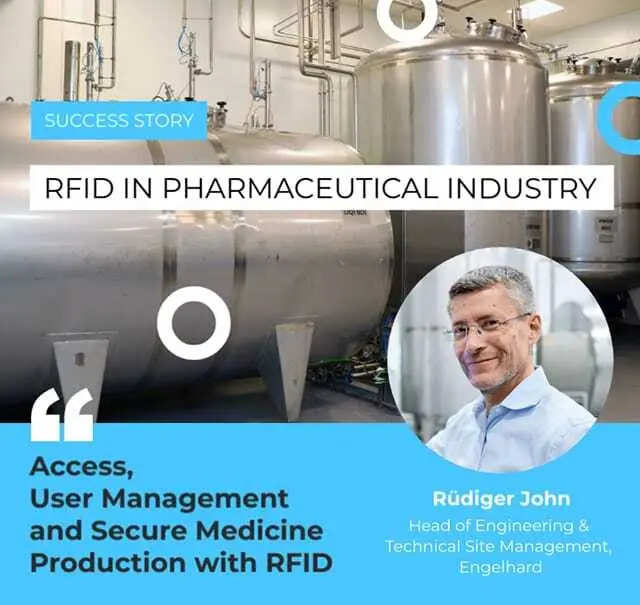
"With the concrete project planning from 2019, it was clear that RFID should be used for user identification at the control panels and for the hose connection. Basically, the hose connection had to be available for production, but at the end of 2019 a new requirement was added: How do we ensure that the hoses can no longer be mixed up? This now works with RFID."
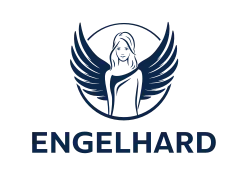
Rüdiger John
Head of Engineering & Technical Site Management
More Articles on IoT in Industrial Manufacturing
Digitalization of the Manufacturing Industry
The ongoing digitalization of companies in the manufacturing industry and the concept of Industry IoT (IIoT) require seamless and efficient data communication. In the process industry, this is particularly crucial in order to increase productivity, efficiency, and adaptability. A key aspect here is the use of OPC UA (Open Platform Communications Unified Architecture) as the communication standard. OPC UA enables the secure connection and networking of IoT devices with the cloud in industry. This creates a robust basis for Industry 4.0 applications.
In addition to OPC UA, newer concepts such as Manufacturing X and Gaia X also play an important role. These platforms aim to strengthen the data infrastructure and sovereignty of European companies and facilitate collaboration within the industry. By using these frameworks, companies can better manage and optimize their digital assets, which ultimately contributes to the realization of Industry 4.0.
Another important aspect of digitalization in manufacturing are collaborative robots (cobots in production), data glasses, and IoT wearables. These technologies improve the interaction between man and machine (human-robot collaboration (HRC)), and increase the flexibility of production processes. Cobots, for example, can work side by side with humans without the need for extensive safety precautions. Data glasses and wearables, on the other hand, allow workers to receive information in real time and thus, carry out their tasks more efficiently and precisely.
Overall, the integration of advanced communication technology, innovative platforms, and interactive devices forms the basis for an intelligent and connected production environment. These elements are crucial to realizing the vision of Industry 4.0 and giving companies in the manufacturing industry a competitive edge.
Machine Vision and OPC UA
The combination of machine vision and OPC UA enables the seamless integration of visual data into the overall industrial automation system. Machine vision systems can capture images and information required for quality control, precision measurements, or robotics. OPC UA standardizes the way this information is collected, transmitted, and used, and ensures interoperability between different devices and systems. This is particularly important in complex production environments where machines and systems from different manufacturers and technologies need to work together.
In addition, OPC UA enables secure and reliable communication in real time, which is critical for machine vision applications as decisions often need to be made in milliseconds. In automated manufacturing, for example, an anomaly detected by machine vision can be processed immediately and transmitted to the control system, which can then react accordingly to avoid production errors.
Partners Specialized in Manufacturing Solutions
What Significance Does RFID Have for Industrial Production?
The importance of RFID for industry has increased considerably in recent years and has found a wide range of applications in various sectors. In manufacturing, in particular, RFID technology has revolutionized quality control. By using RFID tags and RFID readers, companies can monitor the manufacturing process in real time and ensure that all production steps are carried out precisely and in accordance with quality standards. This technology makes it possible to detect potential errors at an early stage and take immediate corrective action, improving the overall quality of the end products.
Another key advantage of RFID in industry is process optimization. RFID systems enable the seamless tracking of materials and products along the entire value chain. This leads to more efficient inventory management, better planning and control of production, and a reduction in downtime. Especially in the clothing industry, where the demand for fast and flexible production processes is high, RFID solutions offer an optimal way to keep track of stock levels and supply chains.
RFID in production makes a significant contribution to digitalization. By integrating RFID systems into industrial applications, production is becoming increasingly digitalized and automated. This transformation makes it possible to collect and analyze data in real time, allowing informed decisions to be made. This leads to greater efficiency and better utilization of production facilities.
Industrial applications of RFID are diverse and include the tracking of tools and machines, the management of maintenance processes, and the optimization of supply chains. RFID technology is also used in warehouse management to automate the storage and retrieval of goods, and to simplify inventories. RFID solutions have become an indispensable part of modern production processes throughout the industry.
In summary, RFID has become crucial for the industry. The technology supports quality control in manufacturing, optimizes production processes and contributes to the comprehensive digitalization of production. The diverse industrial applications of RFID enable companies to increase their efficiency, reduce costs and improve the quality of their products. This makes RFID a key technology for modern industry and its future development.
RFID: A Key Technology in Industry 4.0
RFID in industry stands for versatile applications and increased efficiency. In the modern industrial landscape, RFID plays a crucial role in various sectors. RFID technology offers efficient ways to identify and track products and materials without direct visual contact, leading to significant improvements in logistics and operations management. This is the reason why the focus here is once again explicitly on RFID wireless technology using the pharmaceutical, textile, and food industries as examples.
RFID in the Food Industry
RFID is used in the food industry to improve the traceability and safety of food. By attaching RFID tags to packaging or pallets, companies can quickly identify the origin of products and track them through the supply chain. This not only increases efficiency in distribution, but also enables quick responses to food safety issues.
RFID in the Pharmaceutical Industry
The pharmaceutical industry also benefits significantly from RFID technology. RFID tags help to ensure the authenticity of medicine and prevent counterfeiting. The technology also improves warehouse management and inventory management in pharmacies and hospitals by enabling precise control over medication stocks and their expiry dates.
RFID in the Textile Industry
In the textile industry, RFID is used to track items and optimize the supply chain. From production to retail, RFID tags enable a more accurate inventory management and a more efficient handling of goods. In retail stores, for example, RFID systems can help to quickly update stock levels and monitor the availability of products in real time. RFID anti-theft protection is also being introduced on a regular basis.