Produktionsautomatisierung
Der Industriesektor wird, einfach ausgedrückt, durch die Beschreibung ‚industrielle Sachgüterproduktion im Fabriksystem‘ definiert. Die Produktion kann sich auf alle denkbaren Güter beziehen.
Durch die Verarbeitung von Rohstoffen gehört der Industriesektor zum sekundären Sektor der Wirtschaft. Charakteristisch ist die Weiterverarbeitung von Gütern aus dem primären Sektor. Daher ist die Industrie materialintensiv. Durch den Produktionsprozess und den Einsatz von Investitionsgütern ist er zudem kapitalintensiv.
Herausragende Merkmale der Industrie sind die systematische Massenproduktion, die Anwendung standardisierter Verfahren und eine regulierte und strukturierte Produktionsform. Größere Produktionsunternehmen zeichnen sich außerdem durch einen hohen Grad an Automatisierung, Mechanisierung und Prozesssteuerung aus. Die IT-gestützten Produktionsprozesse sind in den meisten Fällen skalierbar ausgelegt.
Welche verarbeitenden Industrien gehören dazu?
Die verarbeitende Industrie umfasst alle Sektoren, die Rohstoffe in fertige Produkte umwandeln. Sie spielt eine zentrale Rolle in der Weltwirtschaft und kann in verschiedene Kategorien unterteilt werden. Diese Liste zeigt nur einen Teil der verschiedenen Industrien der Welt.
Jede dieser Industrien trägt auf ihre Weise zur Weltwirtschaft bei, indem sie spezialisierte Produkte und Dienstleistungen anbietet, die sowohl im täglichen Leben als auch in anderen Wirtschaftssektoren benötigt werden. Einige der folgenden Wirtschaftszweige gehören sowohl zum primären als auch zum sekundären Sektor.
- Die Metallindustrie mit den Industriezweigen Eisen, Stahl, Aluminium, Kupfer, Erden u.a. verarbeitet Rohstoffe, fördert sie aber auch. Daher ist eine Zuordnung zum primären und sekundären Sektor möglich.
- Die Automobilindustrie produziert Autos, Lastwagen, Motorräder und Fahrzeugteile.
- Zur Reifenindustrie gehört die Herstellung von Reifen für alle Arten von Fahrzeugen.
- Der Maschinenbau stellt Industriemaschinen, Großanlagen, Förderanlagen, Landmaschinen, Baumaschinen und Werkzeugmaschinen her. Auch Kleinteile und Komponenten wie Greifer oder Gestelle gehören dazu.
- Die chemische Industrie ist auf die Herstellung von Chemikalien, Düngemitteln, Farben, Kunststoffen und Kunstfasern spezialisiert.
- In der Nahrungs- und Genussmittelindustrie werden Nahrungsmittel, Getränke und verarbeitete Nahrungsmittel hergestellt.
- Das Textil- und Bekleidungsgewerbe stellt Stoffe, Textilien und Bekleidung her.
- Die pharmazeutische Industrie stellt Arzneimittel, medizinische Geräte und biotechnologische Produkte her.
- Die Elektronik- und Elektrogeräteindustrie stellt Computer, Unterhaltungselektronik, Haushaltsgeräte und industrielle Elektronikkomponenten her. Auch die Herstellung von Robotern gehört dazu.
- In der Holz- und Papierindustrie wird Holz zu Möbeln, Papier, Zellstoff und anderen Produkten verarbeitet.
- Die Luft- und Raumfahrtindustrie stellt Flugzeuge, Raumfahrzeuge und zugehörige Ausrüstungen her.
- Die Energie- und Rohstoffindustrie hat sich auf die Herstellung von Anlagen zur Energieerzeugung sowie Förderung und Verarbeitung von Öl, Gas, Kohle und anderen Rohstoffen spezialisiert. Daher ist eine Zuordnung zum primären und sekundären Sektor möglich.
- Der Industriezweig Medizin- und Labortechnik fokussiert auf die Produktion von medizinischen Instrumenten, Diagnosegeräten und Laborausrüstungen.
Wireless-IoT-Technologien in der Industrie
Produkte für die Industrie
In der Industrie werden grundsätzlich alle Funktechnologien und die entsprechenden Produkte eingesetzt. Der Stand der Integration und die Funktionalität im industriellen Prozess sind jedoch unterschiedlich. UHF-RFID-Systeme spielen neben OPC UA, RTLS und 5G eine sehr große Rolle. Insgesamt lässt sich aber sagen, dass das Zusammenspiel der Technologien immer ausgefeilter und komplexer wird. Die Interoperabilität von Produkten ist daher von Vorteil.
Der Bereich Sensorik nimmt mittlerweile eine Schlüsselposition ein, da nicht mehr nur die reine Kennzeichnung und Identifikation den Prozess optimiert, sondern vor allem die Verarbeitung von Sensordaten. Der Industriesektor ist neben der Automobilindustrie der am stärksten digitalisierte und automatisierte Wirtschaftsbereich. Dementsprechend ist die Durchdringung mit Wireless IoT-Produkten, -Technologien und -Lösungen in diesem Bereich am höchsten.
Status Quo Wireless IoT Lösungen in der Industrie
Alle Beispiele in der folgenden Liste zielen auf die Digitalisierung und Automatisierung von Produktionsprozessen und Logistikbewegungen ab. Sie generieren Datenströme und damit die Basis für KI-basierte Lösungen und Nachhaltigkeit in Unternehmen.
Damit sind sie Teil einer Industrie 4.0-Strategie. Vor allem, wenn Sensordaten erzeugt werden, die Rückschlüsse auf den Ort oder den Zustand des Objekts erlauben. Fazit: Reduzierung von CO2-Emissionen, Verstärkte Konnekivität und Energieeinsparungen.
- Authentifizierunglösungen an Maschinen: Unbefugten Zugang verwehren | Qualifizierten Zugang gewähren | Arbeitsunfälle reduzieren | Sabotageschutz | Prozesssteuerung und Dokumentation aller Aktionen und Entscheidungen | Rückverfolgbarkeit von Fehlern
- Asset Tracking und IoT Asset Management: Präzise Bestandsüberwachung | Reduzierung von Anschaffungskosten und Lagerflächen | Sicherstellung der Verfügbarkeit | Diebstahlschutz | Echtzeitlokalisierung | Effizienzsteigerung | Bedarfsorientierte Wartung und Instandhaltung | Traceability | Optimierte Logistikplanung | Daten als Basis für KI in Unternehmen
- Ortung und Echtzeitlokalisierung: Präzise Überwachung von Anlagen, Maschinen, Geräten, Werkzeugen und Produkten | Reduzierung von Suchzeiten | Optimierte Wartungsprozesse | Bewegungsmuster und KI | Verbesserte Produktivität | Arbeitssicherheit | Diebstahlschutz | Digitalisierung der Supply Chain
- Digitalisierung der Supply Chain: Erhöhung der Transparenz | Echtzeit-Überwachung der Supply Chain | Bestandsgenauigkeit | Automatisierte Bestellsysteme und KI-gestützte Prognosemodelle | Optimierte Transportwege und Produktionsprozesse | Ressourceneffizienz | Kostenreduktion | Präzisere Lieferzeiten | Zuverlässige Supply Chain | Kundenzufriedenheit | Bedarfsgerechte Planung | Optimierte Risikobewertung
- Instandhaltung und Predictive Maintenance: Vermeidung von Ausfällen | Maschinenzustandsdaten in Echtzeit | Erhöhte Prozesssicherheit | Reduzierter Wartungsbedarf | Reduzierte Wartungskosten | Erhöhte Sicherheit | Verlängerte Lebensdauer | Bedarfsgerechte Wartung | Optimierung der Ersatzteillogistik | Arbeitssicherheit |
- Condition Monitoring: Früherkennung von Problemen | Überwachung von Betriebszuständen | Vermeidung von Maschinenausfällen | Verschleißreduzierung | Reduzierung von Stillstandszeiten | Produktionssicherheit | Verlängerung der Lebensdauer von Anlagen | Optimierung von Wartungsplänen | Kostenreduzierung | Überwachung kritischer Maschinenkomponenten | Datenanalyse |
- Behältermanagement: Optimierte Transport- und Lagerprozesse | Bedarfsgerechter Einsatz, Umlauf und Menge | Reduzierung von Leerfahrten und Wartezeiten | Kostenreduzierung | Minimierung von Behälterschäden | Optimale Auslastung | Rückverfolgbarkeit und Transparenz | Zuverlässigere Lieferkette | Optimierte Reinigungszyklen |
- Temperaturüberwachung: Qualitätssicherung | Genaue Kontrolle der Prozesstemperaturen | Geringere Sicherheitsrisiken | Prozesseffizienz | Arbeitssicherheit | Längere Lebensdauer der Anlagen | Einhaltung gesetzlicher Vorschriften | Energieeinsparung | Kühlsystemmanagement | Längere Haltbarkeit der Produkte
- Permanente Inventur: Aktuelle Bestandsdaten | Präzise Produktionssteuerung | Kontinuierliche Bestandsüberwachung | Reduzierung von Stillstandszeiten | Geringere Lagerhaltungskosten | Schnelle Reaktion auf Marktveränderungen | Reduzierung von Inventurdifferenzen | Geringerer Aufwand bei der jährlichen Inventur
- Industrielle Kennzeichnung: Rückverfolgbarkeit | Erleichterung der Lagerhaltung | Korrekte Bauteile und Produktionsprozesse | Schnellere Durchlaufzeiten in der Produktion | Bereitstellung von Handhabungshinweisen oder Verfallsdaten | Lokalisierung | Authentizität | Verknüpfung mit sicherheitsrelevanten Informationen wie Gefahrenklassen oder Handhabungen | Automatisierung von Produktionsprozessen | Markenimage und Unterstützung von Marketingstrategien
- Traceability: Rückverfolgbarkeit von Herkunft und Materialien | Reduzierung von Qualitätsproblemen | Einhaltung von Qualitätsstandards | Verbessertes Risikomanagement | Effizienzsteigerung der Lieferkette | Transparenz | Schnelle Reaktion auf Marktveränderungen | Einhaltung gesetzlicher Vorschriften | Fälschungssicherheit | Gezieltes Rückrufmanagement
- Datenmanagement: Bessere Entscheidungsfindung | Datenanalyse | Prozessoptimierung | Kontinuierliche Prozessüberwachung | Identifizierung von Ineffizienzen und Engpässen | Senkung des Energieverbrauchs | Identifizierung von Materialverschwendung | Früherkennung von Qualitätsabweichungen | Risikomanagement | KI-Lösungen | Neue Geschäftsmodelle | Transparenz
Bis 2026 mehr als 50 Prozent aller OEM-Geräte IoT-fähig
Der globale Markt für das industrielle Internet der Dinge (IIoT) wird voraussichtlich stark wachsen. Die prognostizierte Wachstumsrate liegt bei 23,2 Prozent im Zeitraum 2024 bis 2030. Dieser Aufwärtstrend wird in erster Linie durch die zunehmenden Initiativen im Bereich Industrie 4.0, die fortschreitende Implementierung fortschrittlicher Automatisierungssysteme, die Einführung neuer Technologien, den Trend zu intelligenten Fabriken sowie durch staatliche Fördermaßnahmen zur Unterstützung der Einführung des industriellen IoT vorangetrieben.
Einem Bericht von IoT Analytics zufolge haben Originalgerätehersteller (OEMs) bei ihren IoT-Strategien erhebliche Fortschritte erzielt. Dies wurde durch die Integration innovativer Software für die industrielle Produktion, erweiterter Dienstleistungen und neu gestalteter Geschäftsmodelle erreicht. Es wird erwartet, dass bis 2026 mehr als 50 Prozent der Produkte von OEMs IoT-fähig sein werden. Im Jahr 2023 gab es weltweit mehr als 16 Milliarden aktive IoT-Geräte. Durchschnittlich 40 Prozent der im Jahr 2023 verkauften Produkte waren vernetzt, bis 2026 wird mit einem Anstieg auf 54 Prozent gerechnet.
Ein konkretes Beispiel für die Anwendung von IoT-Lösungen in der Industrie ist der OEM Schindler, der weltweit mehr als 500.000 IoT-vernetzte Aufzüge installiert hat. Insbesondere in der Automobilindustrie wird bis 2026 ein deutlicher Anstieg des Anteils vernetzter Produkte von 34 Prozent auf 54 Prozent erwartet. Diese Entwicklung spiegelt die rasante Entwicklung der IoT-Integration in der modernen Produktionslandschaft wider.
Lagersteuerung und Palettenverfolgung bei KEB Automation
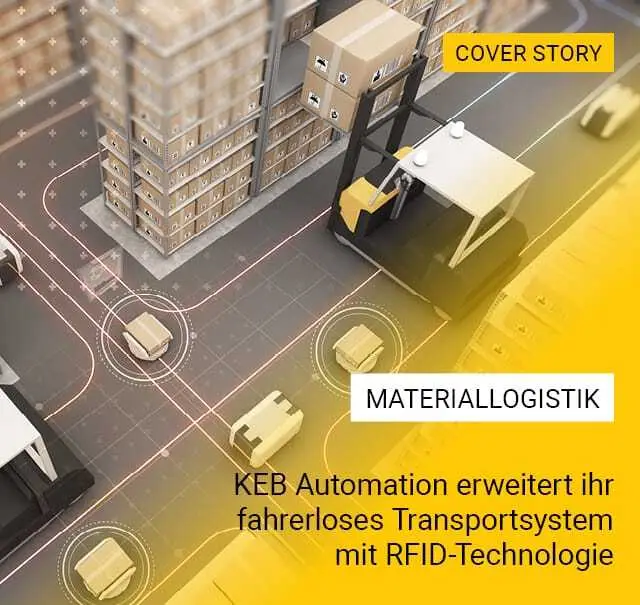
KEB Automation, Spezialist für Antriebs- und Steuerungstechnik, setzt die RFID-Technologie zur Lagersteuerung und Palettenverfolgung ein. Die RFID-Tags enthalten eine eindeutige Handling Unit (HU)-Nummer. Damit werden die Ladungsträger im SAP Extended Warehouse Management (EWM) identifiziert.
Die Bereitstellung der kommissionierten Paletten für das fahrerlose Transportsystem (FTS) erfolgt im Automatiklager über ein Fördersystem. Von dort werden die Paletten in die Produktionshallen transportiert. An den Übergabepunkten zwischen Stapler und FTS sind in drei Metern Höhe 20 Q5X-Sensoren von Turck installiert. Diese Sensoren erkennen die Anwesenheit der Paletten für den Transport. Sobald der Sensor eine Palette erkennt, wird ein Transportauftrag für das DTS generiert. Die Palette wird dann vom DTS abgeholt und durch ein RFID-Gate geführt. Auf diese Weise werden die HU-Informationen von SAP EWM empfangen.
Externe Antennen werden verwendet, um die RFID-Tags auf jeder Palette zu erfassen. Es wird eine Leserate von nahezu 100 Prozent erreicht. Diese Antennen sind auf beiden Seiten des Hallentors angebracht und mit einem Q300 UHF RFID-Lesegerät verbunden. Dies ermöglicht die Identifikation der Ladung unabhängig von der Position der Palette. Beim Passieren des RFID-Gates sendet das DTS eine Anfrage an eine Middleware. Diese Middleware sammelt die Paletteninformationen von der Antenne und fragt dann das SAP-System nach dem Bestimmungsort der Palette ab. Die gesammelten Daten werden dann an das DTS übermittelt.
KEB Automation, Spezialist für Antriebs- und Steuerungstechnik, setzt die RFID-Technologie zur Lagersteuerung und Palettenverfolgung ein. Die RFID-Tags enthalten eine eindeutige Handling Unit (HU)-Nummer. Damit werden die Ladungsträger im SAP Extended Warehouse Management (EWM) identifiziert.
Die Bereitstellung der kommissionierten Paletten für das fahrerlose Transportsystem (FTS) erfolgt im Automatiklager über ein Fördersystem. Von dort werden die Paletten in die Produktionshallen transportiert. An den Übergabepunkten zwischen Stapler und FTS sind in drei Metern Höhe 20 Q5X-Sensoren von Turck installiert. Diese Sensoren erkennen die Anwesenheit der Paletten für den Transport. Sobald der Sensor eine Palette erkennt, wird ein Transportauftrag für das DTS generiert. Die Palette wird dann vom DTS abgeholt und durch ein RFID-Gate geführt. Auf diese Weise werden die HU-Informationen von SAP EWM empfangen.
Externe Antennen werden verwendet, um die RFID-Tags auf jeder Palette zu erfassen. Es wird eine Leserate von nahezu 100 Prozent erreicht. Diese Antennen sind auf beiden Seiten des Hallentors angebracht und mit einem Q300 UHF RFID-Lesegerät verbunden. Dies ermöglicht die Identifikation der Ladung unabhängig von der Position der Palette. Beim Passieren des RFID-Gates sendet das DTS eine Anfrage an eine Middleware. Diese Middleware sammelt die Paletteninformationen von der Antenne und fragt dann das SAP-System nach dem Bestimmungsort der Palette ab. Die gesammelten Daten werden dann an das DTS übermittelt.
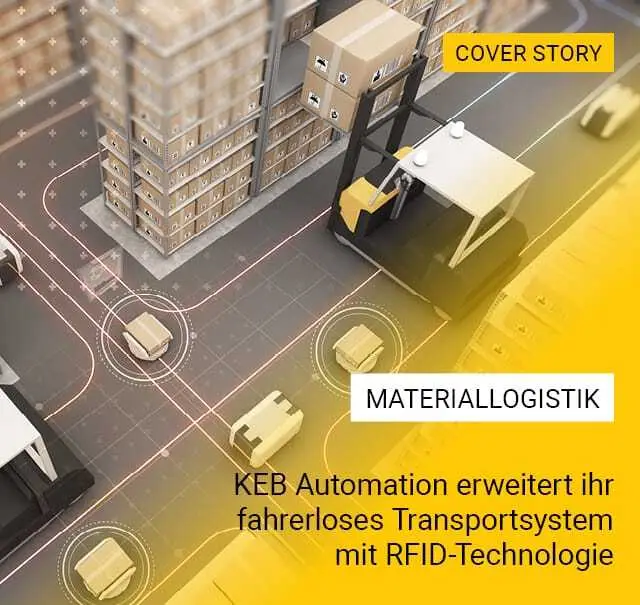
„Die Lösung von Turck verschafft uns die gewünschte Transparenz ohne zeitraubenden manuellen Aufwand. Die Erfassung der RFID-Tags erfolgt vollautomatisch, so dass gleichzeitig Lageraufgaben aus dem SAP Extended Warehouse Management System durchgeführt oder bearbeitet werden können.“
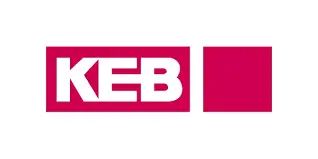
Viktor Derksen
Head of Industrial Engineering
Optimierte Waschmaschinenfertigung mit OPC UA
Miele, Anbieter von Premium-Hausgeräten, setzt seit 2018 OPC UA der OPC Foundation ein, um die Datenkommunikation im Pressen- und Karosseriebau der Waschmaschinenproduktion zu modernisieren und zu vereinfachen. Innerhalb von drei Wochen wurde das Altsystem abgelöst und neue Kommunikationsebenen inklusive der OPC UA-Schnittstellen im Presswerk in Gütersloh integriert.
In der Waschmaschinenproduktion nutzt ein Materialflusssimulator die über OPC UA übertragenen Daten, um verschiedene Produktionsszenarien zu testen. Diese Daten bilden die Grundlage für die Optimierung der Produktion. Zunächst wurden die Produktionsplanungsdaten aus SAP mit Rüstzeiten, Kosten, Kapazitäten, Arbeitsschichten und Materialnummern mit den realen Anlagendaten verknüpft. Um die Daten über OPC UA abrufen zu können, wurden Schnittstellen integriert und Datenformatstandards definiert.
Für was ist OPC UA gut? OPC UA ermöglicht nicht nur die Generierung, Verarbeitung und Auswertung von Daten, sondern auch die nahtlose Übergabe von Daten an andere Systeme. Live-Daten werden vom Materialflusssimulator über die OPC UA-Schnittstellen aus Datenquellen abgerufen. Dies ermöglicht die sekundenschnelle Übertragung von Produktionssignalen, z.B. aus dem Presswerk, an den Simulator. Anlagenzustandsdaten werden im Simulator erfasst und visualisiert. Die Anlagen sind bereits als virtuelle 3D-Modelle im Simulator abgebildet. Durch die Anreicherung mit realen Daten können Simulationsmodelle und ‘digital twin’ Konzepte umgesetzt werden.
„Das hohe Sicherheitsniveau von OPC UA ist für Miele ein entscheidender Faktor. Die Kommunikation mit OPC UA funktioniert nach dem Prinzip secure by default". Alle Daten werden verschlüsselt und sicher übertragen. Mit diesen Sicherheitsstandards werden die Anlagen und Produktionsdaten der Wäscherei in die Azure Cloud von Microsoft übertragen.“
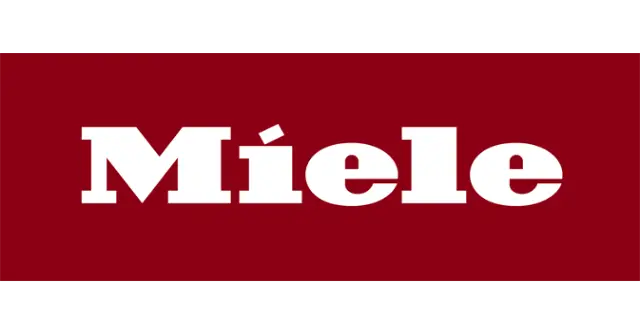
Christian Stickling
Information Technology in Appliance
Mit RFID Fehler in der Pharmaproduktion minimieren
Der Pharmahersteller Engelhard Arzneimittel minimiert Produktionsfehler durch RFID und Automatisierung. Bei der Herstellung von Medikamenten müssen Schlauchverbindungen richtig ausgewählt und verschlossen werden. Engelhard hat die Enden dieser Schläuche mit passiven RFID-Tags ausgestattet, um sicherzustellen, dass die Schläuche richtig angeschlossen sind und um mögliche Fehler bei den Schlauchverbindungen auszuschließen. Die Schlauchmuffe ist mit zwei Führungsringen ausgestattet.
Der lose innere Ring ist mit Gewichten beschwert und frei drehbar. Der RFID-Chip bewegt sich mit dem losen Ring mit. So ist sichergestellt, dass er immer in der richtigen Position zum Lesen ist, egal in welche Richtung der Mitarbeiter den Schlauch dreht. Zum Auslesen des Tags wird nur ein Lesekopf benötigt. Dieser wird an der Schlauchkupplung angebracht. Sobald der Bediener den Schlauch anschließt, bestätigt er diesen Vorgang sofort im Kontrollsystem. Das System liest daraufhin den Datenträger aus. Erst wenn die Steuerungssoftware den richtigen Schlauchanschluss erkannt hat, wird der nächste Prozessschritt eingeleitet.
„Mit der konkreten Projektplanung ab 2019 war klar, dass RFID für die Benutzeridentifikation an den Bedienpulten und für den Schlauchanschluss eingesetzt werden sollte. Grundsätzlich musste der Schlauchanschluss für die Produktion vorhanden sein, aber Ende 2019 kam eine neue Anforderung hinzu: Wie stellen wir sicher, dass die Schläuche nicht mehr verwechselt werden können? Das funktioniert jetzt mit RFID.“
Weitere Artikel über IoT in der Fertigungsindustrie
Digitalisierung der Fertigungsindustrie
Die fortschreitende Digitalisierung von Unternehmen in der Fertigungsindustrie und das Konzept von Industrie IoT (IIoT) erfordern eine nahtlose und effiziente Datenkommunikation. In der Prozessindustrie ist dies besonders entscheidend, um Produktivität, Effizienz und Anpassungsfähigkeit zu steigern. Ein zentraler Aspekt hierbei ist der Einsatz von OPC UA (Open Platform Communications Unified Architecture) als Kommunikationsstandard. OPC UA ermöglicht die sichere Anbindung und Vernetzung von IoT-Geräten mit der Cloud in der Industrie dar. Damit entsteht eine robuste Basis für Industrie 4.0-Anwendungen.
Neben OPC UA spielen auch neuere Konzepte wie Manufacturing X und Gaia X eine wichtige Rolle. Diese Plattformen zielen darauf ab, die Dateninfrastruktur und -souveränität europäischer Unternehmen zu stärken und die Zusammenarbeit innerhalb der Industrie zu erleichtern. Durch die Verwendung dieser Rahmenwerke können Unternehmen ihre digitalen Ressourcen besser verwalten und optimieren, was letztlich zur Realisierung von Industrie 4.0 beiträgt.
Ein weiterer wichtiger Aspekt der Digitalisierung in der Fertigung sind kollaborative Roboter (Cobots in der Produktion), Datenbrillen und IoT-Wearables. Diese Technologien verbessern die Interaktion zwischen Mensch und Maschine (Mensch-Roboter-Kollaboration (MRK)) und erhöhen die Flexibilität der Produktionsprozesse. Cobots zum Beispiel können Seite an Seite mit Menschen arbeiten, ohne dass umfassende Sicherheitsvorkehrungen nötig sind. Datenbrillen und Wearables wiederum ermöglichen es den Arbeitern, Informationen in Echtzeit zu erhalten und damit ihre Aufgaben effizienter und präziser auszuführen.
Insgesamt bildet die Integration von fortgeschrittener Kommunikationstechnologie, innovativen Plattformen und interaktiven Geräten die Grundlage für eine intelligente und vernetzte Produktionsumgebung. Diese Elemente sind entscheidend, um die Vision von Industrie 4.0 zu verwirklichen und den Unternehmen in der Fertigungsindustrie einen Wettbewerbsvorteil zu verschaffen.
Machine Vision und OPC UA
Die Kombination von Machine Vision und OPC UA ermöglicht eine nahtlose Integration visueller Daten in das Gesamtsystem der industriellen Automation. Machine Vision Systeme können Bilder und Informationen erfassen, die für Qualitätskontrollen, Präzisionsmessungen oder für die Robotik notwendig sind. OPC UA standardisiert die Art und Weise, wie diese Informationen gesammelt, übertragen und genutzt werden, und sorgt für Interoperabilität zwischen verschiedenen Geräten und Systemen. Dies ist besonders wichtig in komplexen Produktionsumgebungen, wo Machinen und Anlagen verschiedener Hersteller und Technologien zusammenarbeiten müssen.
Darüber hinaus ermöglicht OPC UA die sichere und zuverlässige Kommunikation in Echtzeit, was für die Anwendungen von Machine Vision kritisch ist, da Entscheidungen oft in Millisekunden getroffen werden müssen. Beispielsweise kann in der automatisierten Fertigung eine durch Machine Vision erkannte Anomalie sofort verarbeitet und an das Steuerungssystem übermittelt werden, welches dann entsprechend reagieren kann, um Produktionsfehler zu vermeiden.
Spezialisierte Partner für Fertigungslösungen
Welche Bedeutung hat RFID für die industrielle Produktion?
Die Bedeutung von RFID für die Industrie ist in den letzten Jahren erheblich gestiegen und hat vielfältige Anwendungen von RFID in verschiedenen Sektoren gefunden. Insbesondere in der Fertigung hat RFID-Technologie die Qualitätskontrolle revolutioniert. Durch den Einsatz von RFID-Tags und RFID-Readern können Unternehmen den Fertigungsprozess in Echtzeit überwachen und sicherstellen, dass alle Produktionsschritte präzise und gemäß den Qualitätsstandards ablaufen. Diese Technologie ermöglicht es, potenzielle Fehler frühzeitig zu erkennen und sofortige Korrekturmaßnahmen zu ergreifen, was die Gesamtqualität der Endprodukte verbessert.
Ein weiterer entscheidender Vorteil von RFID in der Industrie ist die Prozessoptimierung. RFID-Systeme ermöglichen eine lückenlose Verfolgung von Materialien und Produkten entlang der gesamten Wertschöpfungskette. Dies führt zu einer effizienteren Bestandsverwaltung, einer besseren Planung und Steuerung der Produktion sowie einer Reduzierung von Ausfallzeiten. Insbesondere in der Bekleidungsindustrie, wo die Nachfrage nach schnellen und flexiblen Produktionsprozessen hoch ist, bietet RFID-Lösungen eine optimale Möglichkeit, den Überblick über Lagerbestände und Lieferketten zu behalten.
RFID in der Produktion trägt maßgeblich zur Digitalisierung bei. Durch die Integration von RFID-Systemen in industrielle Anwendungen wird die Produktion zunehmend digitalisiert und automatisiert. Diese Transformation ermöglicht es, Daten in Echtzeit zu sammeln und zu analysieren, wodurch fundierte Entscheidungen getroffen werden können. Dies führt zu einer höheren Effizienz und einer besseren Auslastung der Produktionsanlagen.
Industrielle Anwendungen von RFID sind vielfältig und umfassen die Verfolgung von Werkzeugen und Maschinen, das Management von Wartungsprozessen und die Optimierung von Lieferketten. RFID-Technologie wird auch in der Lagerverwaltung eingesetzt, um die Ein- und Auslagerung von Waren zu automatisieren und Inventuren zu vereinfachen. In der gesamten Industrie sind RFID-Lösungen zu einem unverzichtbaren Bestandteil moderner Produktionsprozesse geworden.
Zusammengefasst hat RFID für die Industrie eine zentrale Bedeutung erlangt. Die Technologie unterstützt die Qualitätskontrolle in der Fertigung, optimiert Produktionsprozesse und trägt zur umfassenden Digitalisierung der Produktion bei. Durch die vielfältigen industriellen Anwendungen von RFID können Unternehmen ihre Effizienz steigern, Kosten senken und die Qualität ihrer Produkte verbessern. Dies macht RFID zu einer Schlüsseltechnologie für die moderne Industrie und deren zukünftige Entwicklung.
RFID, eine Schlüsseltechnologie in Industrie 4.0
RFID in der Industrie steht für vielseitige Anwendungen und Effizienzsteigerung. In der modernen Industrielandschaft spielt RFID eine entscheidende Rolle in verschiedenen Branchen. RFID-Technologie bietet effiziente Möglichkeiten, Produkte und Materialien ohne direkten Sichtkontakt zu identifizieren und zu verfolgen, was zu erheblichen Verbesserungen in der Logistik und im Betriebsmanagement führt. Das ist der Grund warum an dieser Stelle noch einmal explizit die Funktechnologie RFID am Beispiel der Pharma-, Textil- und Lebensmittelindustrie in den Mittelpunkt gerückt wird.
RFID in der Lebensmittelindustrie
In der Lebensmittelindustrie wird RFID eingesetzt, um die Rückverfolgbarkeit und Sicherheit von Lebensmitteln zu verbessern. Durch das Anbringen von RFID-Tags an Verpackungen oder Paletten können Unternehmen die Herkunft von Produkten schnell identifizieren und den Weg durch die Lieferkette nachverfolgen. Dies erhöht nicht nur die Effizienz in der Distribution, sondern ermöglicht auch schnelle Reaktionen bei Lebensmittelsicherheitsproblemen.
RFID in der Pharmaindustrie
Die Pharmaindustrie profitiert ebenfalls erheblich von der RFID-Technologie. RFID-Tags helfen, die Authentizität von Medikamenten zu gewährleisten und Fälschungen zu vermeiden. Zudem verbessert die Technologie die Lagerverwaltung und das Bestandsmanagement in Apotheken und Krankenhäusern, indem sie eine genaue Kontrolle über Medikamentenbestände und deren Verfallsdaten ermöglicht.
RFID in der Textilindustrie
In der Textilindustrie wird RFID eingesetzt, um Artikel zu verfolgen und die Lieferkette zu optimieren. Von der Produktion bis zum Einzelhandel ermöglichen RFID-Tags eine genauere Bestandsführung und eine effizientere Handhabung der Waren. In Einzelhandelsgeschäften können RFID-Systeme beispielsweise dabei helfen, Lagerbestände schnell zu aktualisieren und die Verfügbarkeit von Produkten in Echtzeit zu überwachen. Auch der RFID-Diebstahlschutz wird regelmäßig eingeführt.