Material logistics
What is Required for Efficient Material Logistics?
Efficient material logistics requires much more than simply managing material flows related to production. The primary objective is to optimize processes, reduce costs and ensure smooth operations. Transparency plays a crucial role in managing and controlling transport movements efficiently and flexibly.
This calls for a solution that seamlessly combines as many aspects of material logistics as possible. The flows of information accompanying material must be ensured to achieve the maximum possible productivity and efficiency and prevent bottlenecks. KEB Automation faced this challenge with the intralogistics in the electronics plant.
"Turck's solution gives us the transparency we wanted without any time-consuming manual effort. The capture of the RFID tags is fully automated, allowing warehouse tasks from the SAP Extended Warehouse Management system to be completed or processed at the same time."
DTS in the Production Area
As specialists for drive and control technology, KEB Automation develops, produces and sells drives as well as engines, gearboxes, brakes, clutches and IIoT solutions worldwide. At the production plant in Barntrup, the company wanted to automate all non-value-added warehouse processes as much as possible.
The specific occasion to do this came with the move into a new production hall, in which it was possible to carry out detailed planning right down to the production areas. From the start, the aim was to replace the use of forklifts in the production area with a driverless transport system.
RFID in the Warehouse
Warehouse Control and Pallet Tracking Using RFID Technology
The labels have a unique handling unit number (HU), which gives the load carriers their identity in SAP EWM. The additional labeling of the number as a barcode and plain text makes who identified a pallet, and where and how it was identified unimportant.
A transport order always therefore refers to an HU, also between cross-system warehouse locations, whether executed by the DTS or by conventional industrial trucks. The information exchange between the different systems and SAP is coordinated via middleware.
"We wanted to fully automate the identification and tracking of all pallets on the routes in the production area using RFID tags."
A Mixed Operation of Different Intralogistics Systems
At the automated warehouse, the picked pallets are prepared for the DTS using a conveyor system. From this start point, the pallets are transported to all electronics production halls.
The route includes several individual sections and intermediate buffers, depending on the destination. The individual transport orders are carried out not only by the DTS, but also by manually operated industrial trucks and stationary materials handling equipment.
In this mixed operation of different intralogistics systems, the accurate tracking of pallets and precise control of their movements present challenges that RFID technology is designed to overcome.
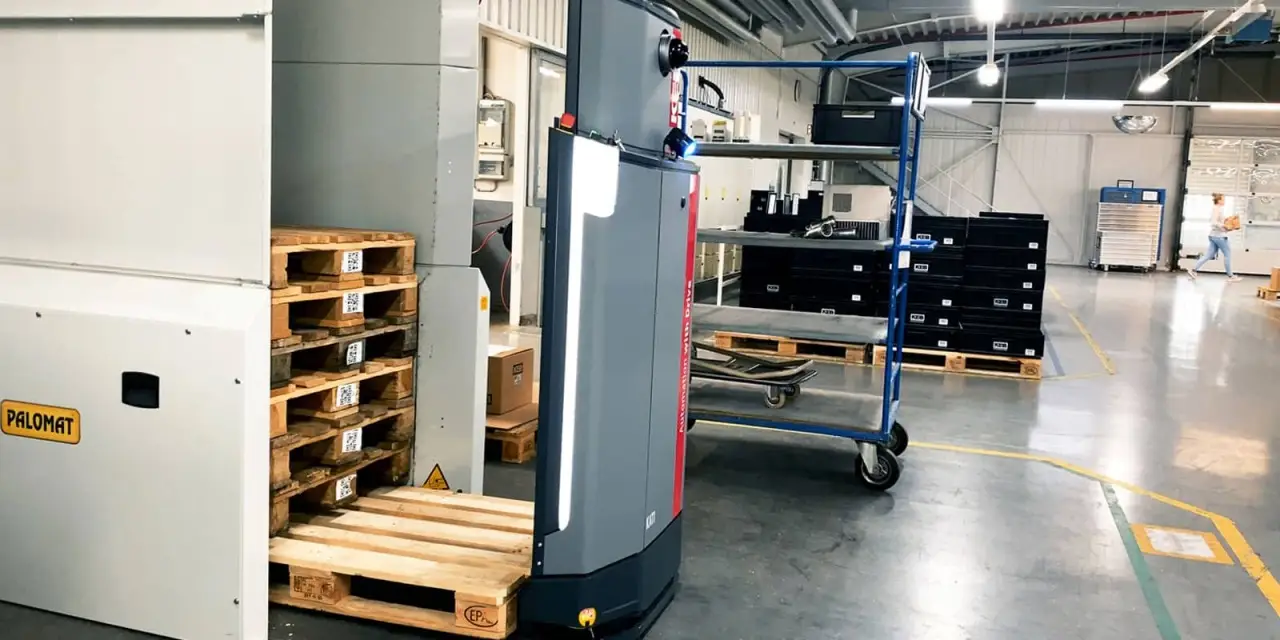
After the transport order is generated, the DTS picks up the pallet at the warehouse location.
Optical ID Solution Unsuitable
The DTS always requires instructions or position information to determine the route. "For a simple pallet transport from one workstation to another, this is quite straightforward," explains Phillip Hannesen, digital transformation manager for production at KEB in Barntrup.
"It becomes problematic in zones in which multiple pallets are temporarily stored to be picked up later by another vehicle and taken to another location. When there is a mixing of load carriers, consistent HU-to-location assignment is no longer assured, so vehicles must always be able to identify the loaded pallet."
"By using this RFID solution, we can intentionally allow a certain amount of chaos at this point to enable efficient work. As soon as a pallet leaves the area, the pallet and its destination are automatically recognized."
The Optimal Solution: UHF RFID
In order to ensure reliable identification of the load, the possibility to do this is important regardless of the orientation and positioning of the pallet.
Turck's UHF RFID technology provides a solution for all installation situations of the application and achieves a read rate of almost 100 percent. The versatility and flexibility of the system is demonstrated by a look at the various use cases at KEB.
Pallet Identification
Pallet Identification at the Transfer Point
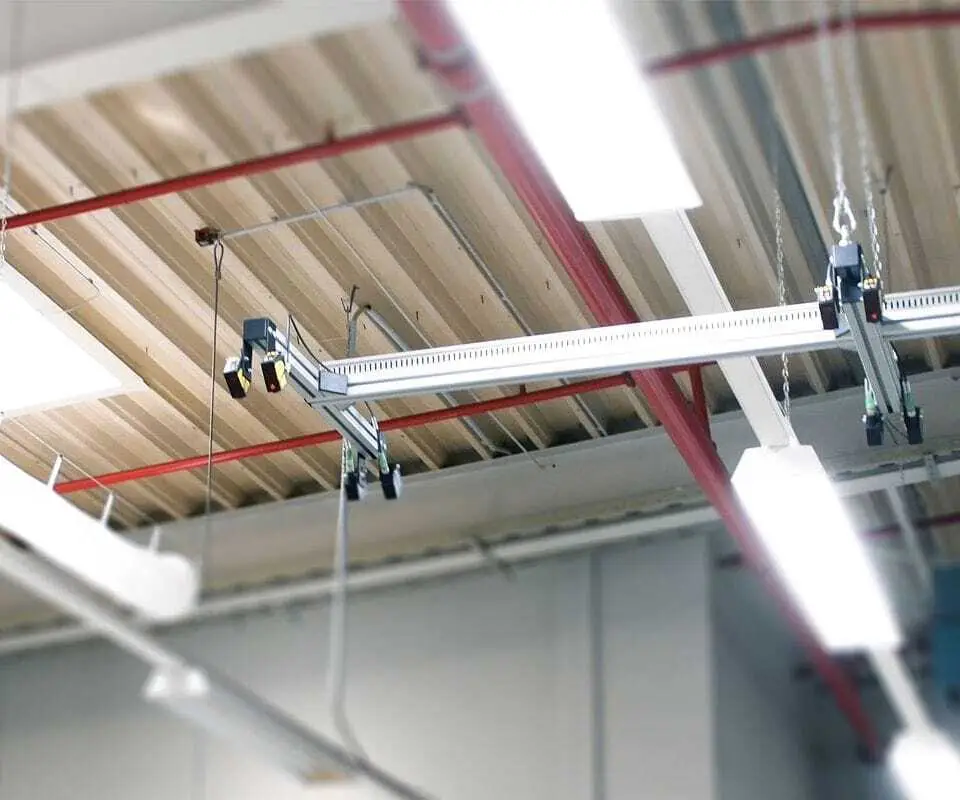
Laser distance sensors detect occupied storage locations
The presence of the pallets at defined storage locations is checked at a transfer point for forklifts and DTS. The Q5X laser distance sensor from Turck's optical partner Banner Engineering is used for this. 20 Q5X sensors with a range of 5 meters are used to detect 20 pallets.
The Q5X sensors, mounted at a height of 3 meters, determine whether there are pallets at the transfer point that can be transported.
As soon as the distance sensor has detected the presence of a pallet, a transport order is generated for the DTS. This picks up the pallet, passes through the RFID gate and finally receives the HU information from SAP EWM.
The presence of the pallets at defined storage locations is checked at a transfer point for forklifts and DTS. The Q5X laser distance sensor from Turck's optical partner Banner Engineering is used for this. 20 Q5X sensors with a range of 5 meters are used to detect 20 pallets.
The Q5X sensors, mounted at a height of 3 meters, determine whether there are pallets at the transfer point that can be transported.
As soon as the distance sensor has detected the presence of a pallet, a transport order is generated for the DTS. This picks up the pallet, passes through the RFID gate and finally receives the HU information from SAP EWM.
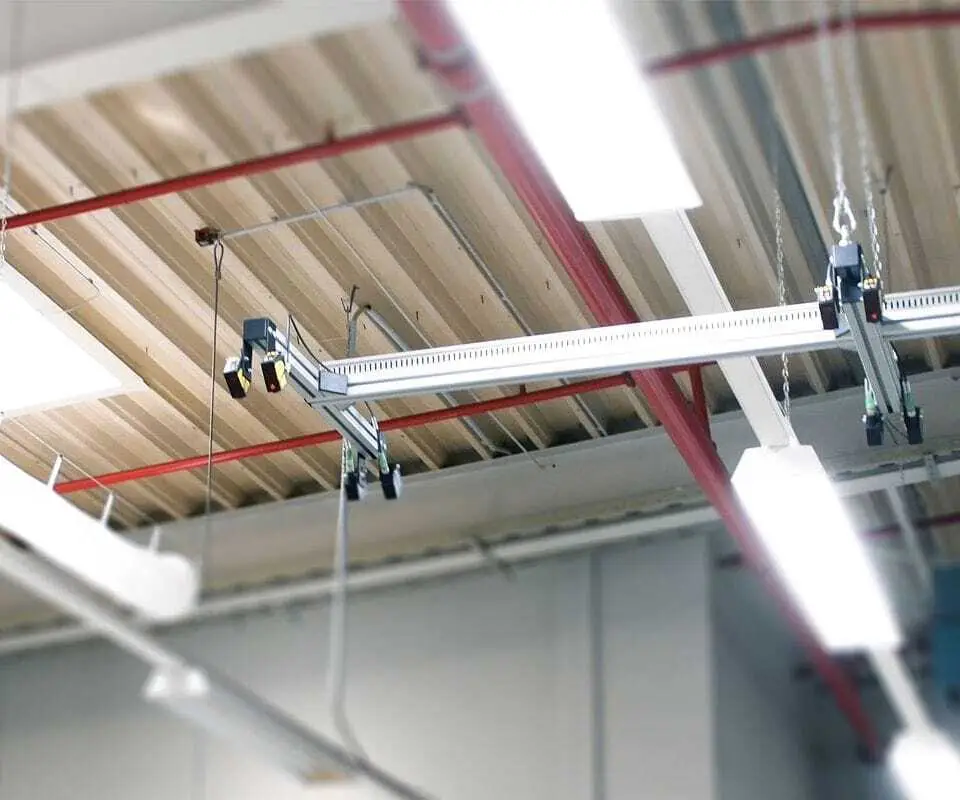
Laser distance sensors detect occupied storage locations
Laser Distance Sensors Detect Occupied Storage Locations
The system checks whether the destination may already be occupied before a transport order is generated. Before Q5X sensors were used, the DTS first had to move to the destination to determine this.
In this case, the DTS waited in front of the blocked storage location until an employee cleared it. Today, the vehicle receives information in advance about whether the destination is occupied and only starts the journey if it is free – this prevents empty runs and wait times and ultimately improves performance.
A sensor initiates standardized communication between the controller and DTS by sending a 24- volt signal to the controller when it detects the transport system. The PLC in turn transmits the information to the DTS via the TCP/IP network.
Near-Field Antennas in Use
Pallet Identification at Full Speed
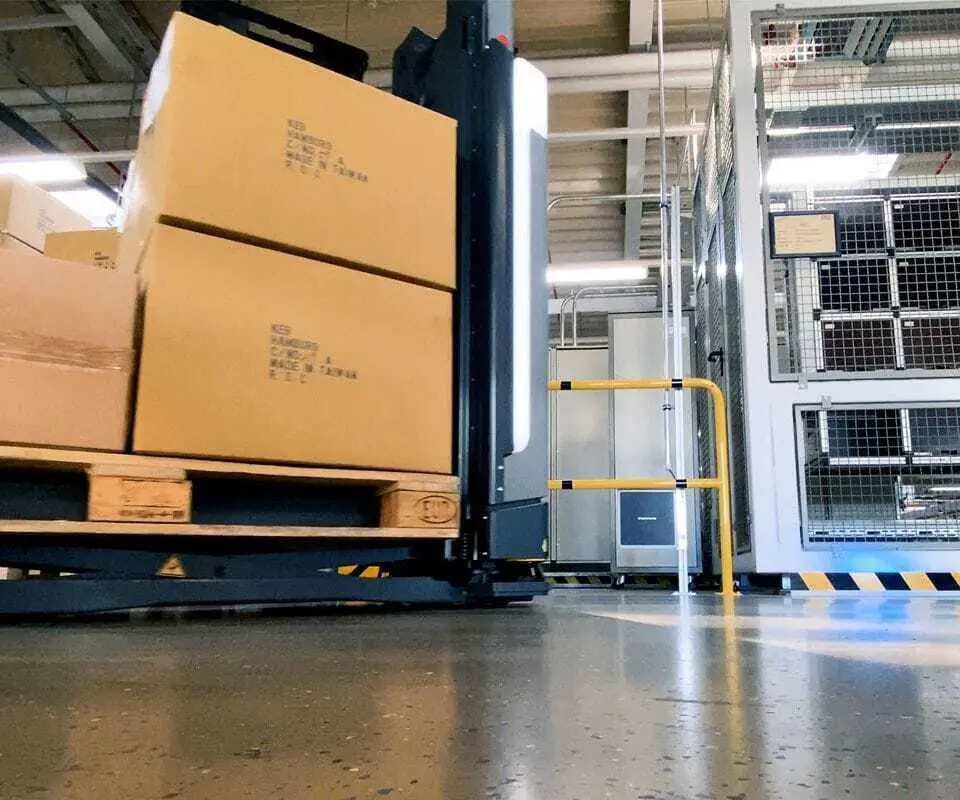
External antennas on the high-speed door detect tags on the pallet over a long distance, regardless of the direction of travel.
External antennas are mounted on each side of a hall door and connected to the UHF RFID reader. The external antennas ensure reliable detection of the RFID labels on the pallets, regardless of the orientation of the respective pallet on the DTS. As the DTS approaches the door, it sends a signal to the Q300 via the network to start the recording.
A store order, i.e. the order to transport the load carrier from A to B, is present in SAP EWM for the HU that the Q300 detects. Once the DTS has passed the gate, it sends a request to the middleware. This retrieves the pallet information from the antenna and then asks the SAP system for the destination of the pallet. The data captured is then transferred to the DTS.
External antennas are mounted on each side of a hall door and connected to the UHF RFID reader. The external antennas ensure reliable detection of the RFID labels on the pallets, regardless of the orientation of the respective pallet on the DTS. As the DTS approaches the door, it sends a signal to the Q300 via the network to start the recording.
A store order, i.e. the order to transport the load carrier from A to B, is present in SAP EWM for the HU that the Q300 detects. Once the DTS has passed the gate, it sends a request to the middleware. This retrieves the pallet information from the antenna and then asks the SAP system for the destination of the pallet. The data captured is then transferred to the DTS.
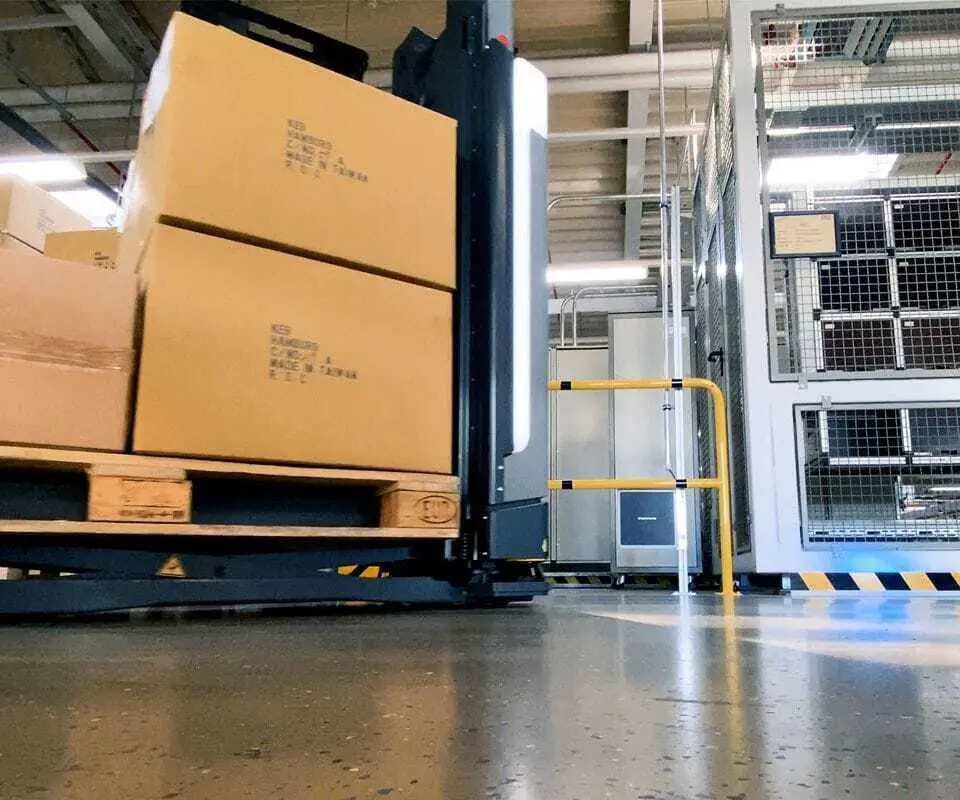
External antennas on the high-speed door detect tags on the pallet over a long distance, regardless of the direction of travel.
Efficient Identification Even in the Near Field
Two production halls are connected via a bridge with stationary pallet conveyor technology, which was also equipped with RFID technology. Unlike the application at the hall door, where RFID labels have to be detected over long distances, the challenge in this application is to only read RFID labels in the immediate vicinity, i.e. at a distance of up to about 10 cm. This is achieved with near-field antennas positioned to the left and right of the pallet conveyor. These near-field antennas only detect the RFID label of the pallet that is directly in front of them.
A Smooth Transfer Process
At the transfer points, the conveyor system communicates with the DTS to ensure a smooth transfer process. When the pallet is placed, the DTS sends a request to the middleware to identify the pallet via the near-field antennas of the Q300 reader. This information is returned to the middleware, which determines the warehouse tasks for this pallet from the SAP EWM data. After the pallet has been placed at the transfer point, the conveyor system transports the pallet to the next hall, where it is again detected using RFID.
Full Transparency
The RFID solution offers KEB the key advantage of end-to-end transparency. The location of a pallet can be seen at any time – whether it is still on the conveyor system, has been picked up by the industrial truck or has already arrived at its destination. In some situations, it is possible to automate the acknowledgment of EWM warehouse tasks using RFID. This is supplemented by the manual operation of mobile devices.
"Turck's solution gives us the transparency we wanted without any time-consuming manual effort," Derksen said. "The capture of the RFID tags is fully automated, allowing warehouse tasks from the SAP Extended Warehouse Management system to be completed or processed at the same time."
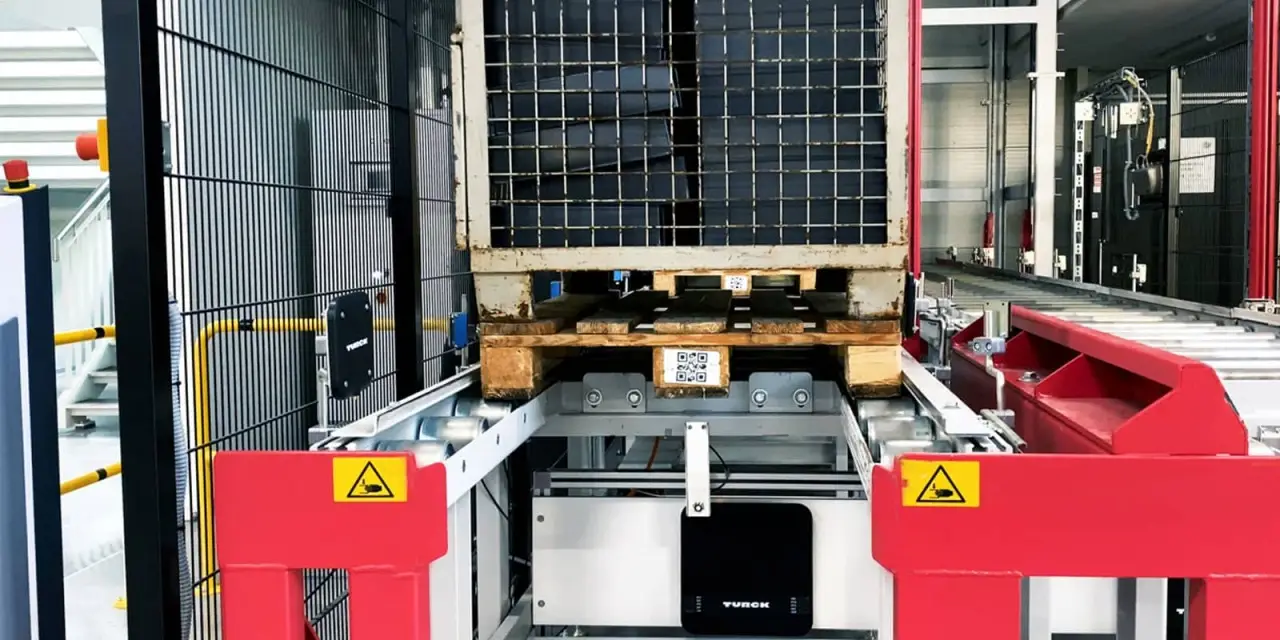
External RFID near-field antennas on the conveyor system only detect the pallet directly in front of them.
Agile Warehouse Management Allows Controlled Chaos
Another benefit of the RFID solution is that it allows mixed traffic in the production hall. This means that both DTS and employees with lift trucks or forklifts could load and unload simultaneously in the staging area. Separate storage space management is not required, as each pallet can be identified at each fork.
"By using this RFID solution, we can intentionally allow a certain amount of chaos at this point to enable efficient work. As soon as a pallet leaves the area, the pallet and its destination are automatically recognized," explains Hannesen, who also emphasizes the good cooperation with Turck: "Turck's service and short communication channels enable efficient cooperation, and we are happy to rely on this trusting and well-established partnership."
Outlook
The successful use of the DTS with Turck's RFID technology has led to the planning of further expansions. Waste disposal was also successfully integrated into the system: Containers in which used cardboard is collected are picked up by the DTS. It is planned for these containers to be transferred directly to a new waste compactor, which would mean fully automated disposal.
The laser distance sensors will also be equipped with Turck IO-Link modules in the future, which will independently perform control tasks through the use of Turck's ARGEE logic software. This includes, for example, the acquisition and evaluation of sensor values. They will also autonomously and efficiently manage the required communication with middleware or DTS, resulting in an extremely lean overall solution.