Logopak Systeme GmbH & Co. KG
We are Logopak Systeme GmbH & Co. KG
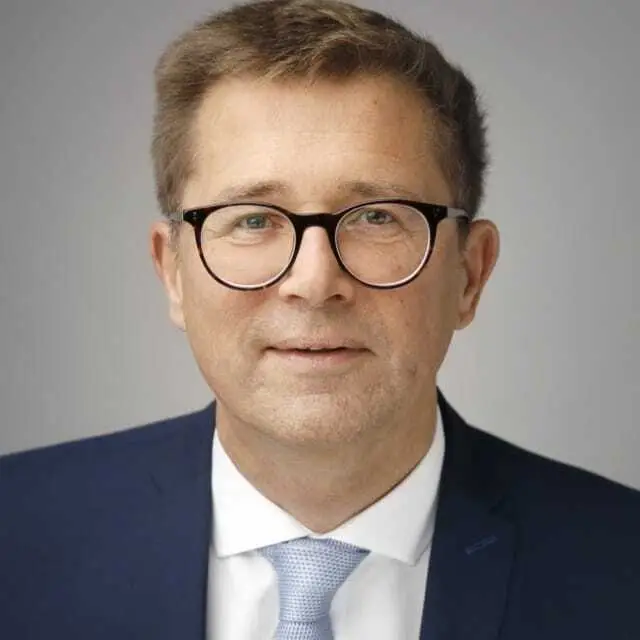
Steffan Gold
Managing Director
"Since the company's founding in 1978, our USP is the manufacture of high-quality and long-lasting machines. This is how we have established a position as a leading manufacturer of integrating tagging systems and software for logistics and industrial printers, and provide intersection between production and logistics for our customers. Logopak Systeme, as part of the Possehl Group, includes 300 staff members that offer on-site service for the customer."
Product Identification & Labeling is Our Business
Logopak is a leading manufacturer of logistically integrated labeling systems, labeling software as well as barcode and industrial printers. In addition, Logopak offers the ideal consumables for direct and indirect labeling of a large variety of product and packaging types. The consumables are used for labeling product packaging for the point of sale (primary labeling), group packaging or containers (secondary labeling) as well as carriers, such as pallets (tertiary labeling).
Logopak’s vast product range also includes smart labels and tags for RFID (Radio-Frequency Identification). The company headquarters is located in Hartenholm near Hamburg, Germany, and was founded in 1978. It is represented worldwide through nine corporate locations. Logopak provides extensive experience for a wide range of applications.
Both standard machines and custom solutions are developed in-house and manufactured in Germany. The operator-friendly systems are easily installed and simple to maintain. Logopak is a member of the industry associations RAIN, AIM and GS1.
Our Products – Easy to Install – Easy to Use – Easy to Maintain
Radio Frequency Identification enables automatic identification of products in a variety of environments. Almost all Logopak systems are available with RAIN RFID technology. The high quality and robust modular design also allows for later conversion. With RFID Tag-On-Demand technology, the RFID-Tags can be applied as required independent of the barcode-labels, all under machine software control.
What Are the Advantages of RFID?
By not requiring a line-of-sight for identification purposes, RFID are
- Less sensitive to damage, dirt and badly placed labels.
- Easier and faster to read.
- Possible to read through the packaging
In addition, there is no need to visually search for a barcode in order to record it.
- Load Carrier Management
- Packaging
- Warehouse Management
- Labeling and Identification
- Track and Traceability
- Data Management
- Inventory
- Supply Chain
- Asset Tracking
- Logistics
- Industrial Manufacturing
- Retail
- Agriculture
- Automotive Industry
- Construction Industry
- Healthcare
Success Stories with Logopak
News from Logopak
Products of Logopak
We’re Here For You!

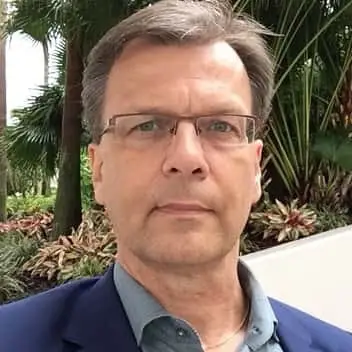
Lars Thuring
Senior Manager Strategy and Innovation