Machines from Bühler
Beginnings in Mechanical Engineering
In 1860, Adolf Bühler Sr. opened an iron foundry in Gupfen in Uzwil, the Canton of St. Gallen. He quickly shifted the production of rollers for the milling industry to the manufacture of complete rolling mills and regular mills. By 1900, he established offices in Spain and France.
Today, Bühler is represented in over 140 countries around the world. The largest business segment of Bühler Group, Grains & Food, performed solidly in 2022, despite disruptions to supply chains, and the grain and energy markets.
Its order intake was CHF 1,663 million, down 6.5 %, while turnover improved by 2.6 % to CHF 1,696 million.
Bühler Group's net profit improved significantly by 35.7 percent to 170 million US dollars (previous year: 125 million US dollars).
Machines in Flour Production
65 % of the world’s grain is processed on Bühler machinery. This requires a number of specialized machines, as the process from raw material to finished product involves several stages. After a preliminary laboratory analysis of the raw material, the cereal grains are pre-cleaned.
After complete cleaning, which includes sorting out stones and AI-controlled color recognition to detect toxic ergot, the grain is conditioned. This involves spraying the grains with water to increase the moisture content (to 15–18 percent) to achieve the desired flour moisture and constant milling characteristics.
About 24 hours later, milling begins. The grain is crushed in the roller mill in several steps. The grain husk is separated and sieved out. The flour that is now available undergoes final quality checks and is then packaged in 25–50 kilogram bags for bakeries.
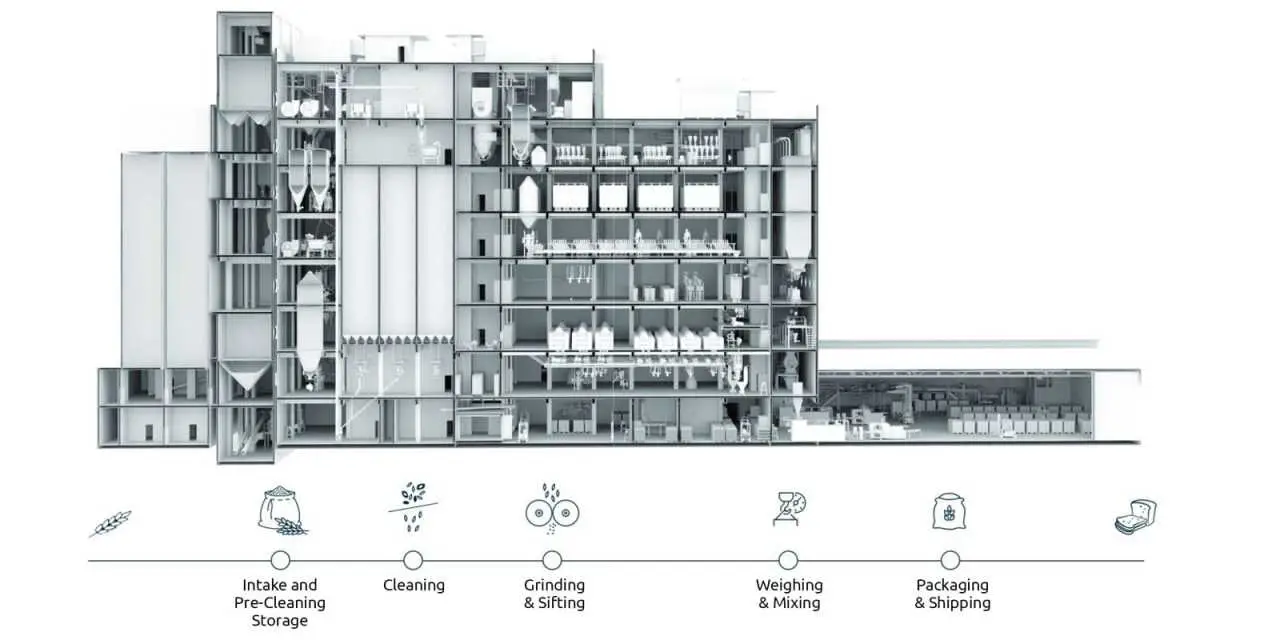
65 Percent of Wheat Flour is Milled on Bühler Machines.
Sustainability Through Digitalization
Bühler Group has committed to having solutions ready to multiply by 2025 that reduce energy, waste, and water by 50 % in the value chains of its customers.
Connectivity in the plants, automation, and smart control via Mercury MES (manufacturing execution system) software are the primary means to achieve this, OPC UA playing a key role throughout as a communications enabler.
Machine Communication
Complicated Machine Communication
The need to improve machine communication became increasingly urgent for Bühler in 2013. Since the installations communicated in different "languages," they had to be programmed specifically for each application.
As a result, each installation had its own unique structure that was not replicated in other installations. The integration effort for each individual installation was, and remained, enormously high.
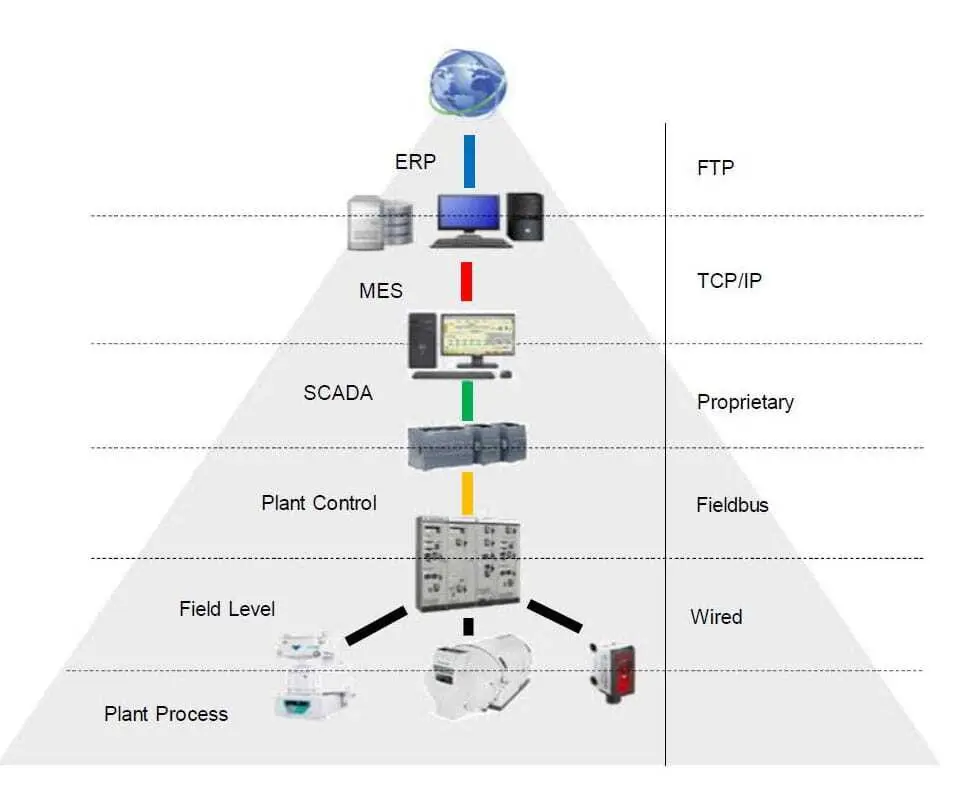
The different levels of an automation pyramid.
Example: Capturing Rotational Speed
If, for example, an operator wanted to request a machine condition parameter such as the rotational speed of a motor from a sensor from the ERP system, then all five levels of the automated process control system had to be “traversed”.
This process can be time consuming and costly due to proprietary data exchange.
“The data we need in this case is in the programmable logic controller (PLC),” explains Samuel Ochsner, Senior Software Architect & Product Owner IIoT at the Bühler Group.
“But we could not access it directly, due to hererogenous protocols and interfaces.” Programming skills were needed to address each level. The error rate in how the different layers interpreted sensor data was 40 percent.
Ralph Häuselmann, Senior Project Manager R&D Corporate Technology at Bühler Group, summarized the situation at the end of 2013 as follows: "There was a need for a solution where the information finally transmitted is correct, where the ERP system at the highest level can access the sensor data directly, and where only one language is spoken."
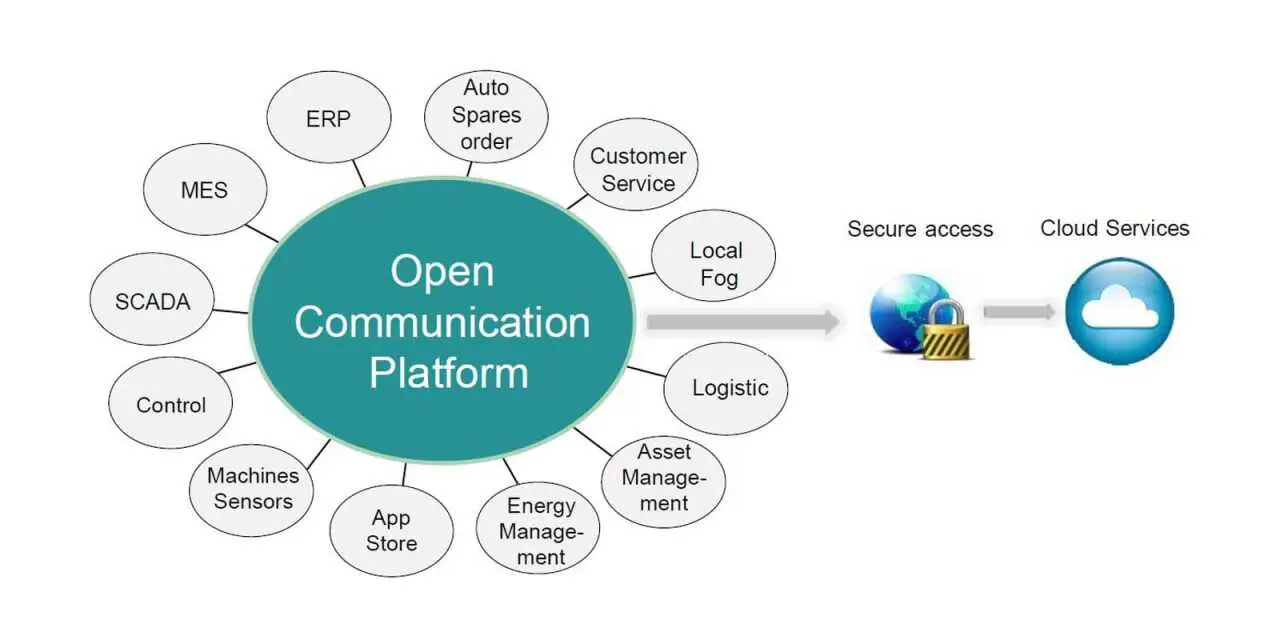
Bühler required simplified machine communication structure transparently solved with OPC UA.
OPC UA Integration
The Beginnings via Software Toolbox
The first step toward OPC UA integration was made was made in 2014 via the American company Software Toolbox, which offers industrial automation software tools. Bühler used an installation with the OPC server, which was immediately successful.
"We suddenly obtained real time data from every level of the automation pyramid quite easily. After this first adoption, OPC UA was integrated in many other areas."
Retrofitting
Newer plants and those on which connectivity has been retrofitted can already communicate using OPC UA. In general, about 20 percent of all mills in the last 20 years have been retrofitted. 1,500 mills are to be equipped with the comprehensive Mercury plant control system for fully automated processes.
Current Status
90 percent of all new installations and upgrades are connected via OPC UA. "All the major hardware manufacturers have already integrated OPC UA," explains Samuel Ochsner. "The PLCs already have OPC UA integrated. This is why the effort to add a new machine to the structure is comparatively small today."
The Die Casting department participates in a companion specification working group, and other companion specifications are being developed. Internally, standardizations are being built to facilitate the onboarding of equipment with OPC UA.
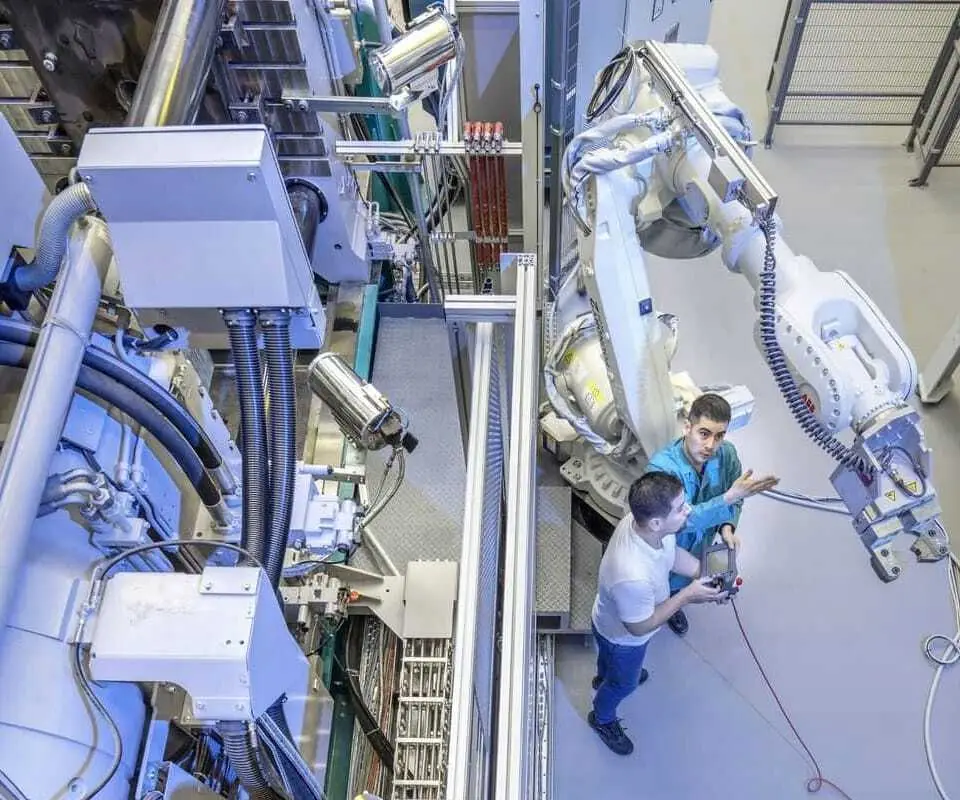
Half of the equipment at Bühler already communicates via OPC UA.
Automation with OPC UA
Connectivity with Bühler Insights
Bühler is connecting the industrial plants with the Bühler Insights platform. Machines are transformed into networked devices via an IoT gateway connected to the platform. Plant operators and Bühler Product Teams use the data from sensors, machines, and machine control devices to optimize the efficiency of their plants and reduce maintenance effort, energy consumption, and wear.
The 'Pluto' Software Platform
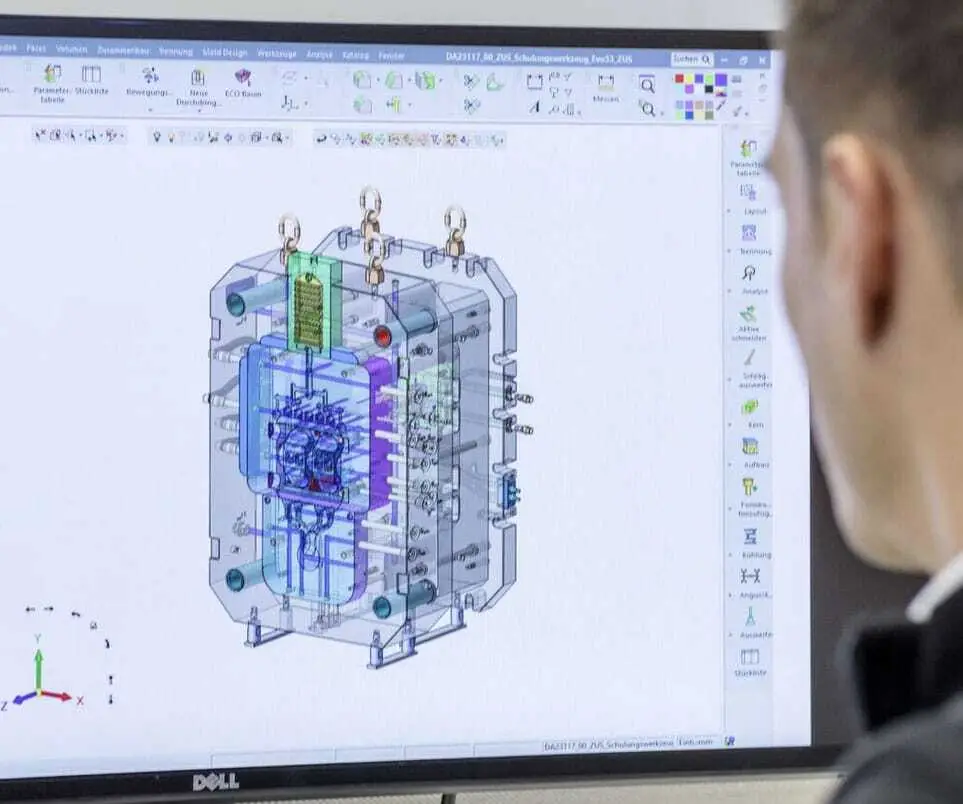
The central digitalization platform, Bühler Insights, is the the basis for the software platforms 'Pluto' and 'Mercury MES'.
Pluto is a completely OPC UA-based automation software for Industry 4.0. It is web-based and generates a graphical user interface for easy operation. Pluto generates solutions automatically and in real time, based on accumulated data. Pluto, thus, reduces the complexity of plant automation. Bühler Insights Gateway collects data from OPC UA Servers.
The main areas of application, so far, are wheat mills, rice mills, and silo handling. Installation efforts are also reduced by Pluto, which uses pre-programmed objects and automatically creates the software for PLCs with them. Smooth machine communication is, thus, guaranteed from the moment of installation. In this respect, Pluto requires OPC UA not only for data exchange, but for digital transformation itself.
Pluto is a completely OPC UA-based automation software for Industry 4.0. It is web-based and generates a graphical user interface for easy operation. Pluto generates solutions automatically and in real time, based on accumulated data. Pluto, thus, reduces the complexity of plant automation. Bühler Insights Gateway collects data from OPC UA Servers.
The main areas of application, so far, are wheat mills, rice mills, and silo handling. Installation efforts are also reduced by Pluto, which uses pre-programmed objects and automatically creates the software for PLCs with them. Smooth machine communication is, thus, guaranteed from the moment of installation. In this respect, Pluto requires OPC UA not only for data exchange, but for digital transformation itself.
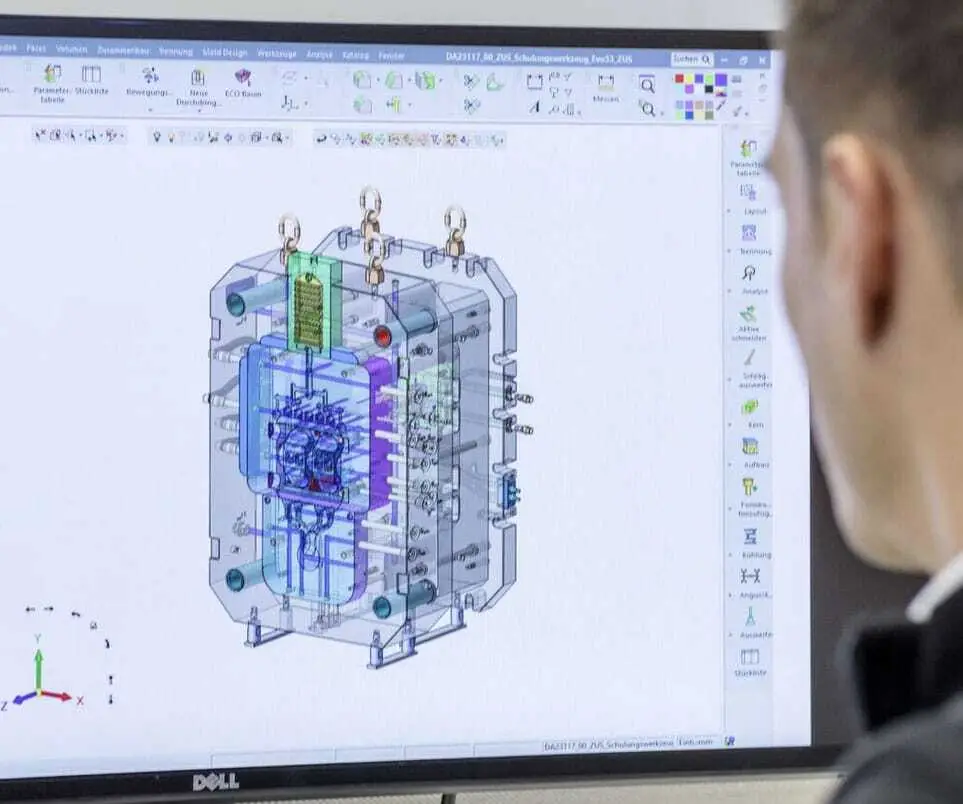
The central digitalization platform, Bühler Insights, is the the basis for the software platforms 'Pluto' and 'Mercury MES'.
"Every function in the PLC, every Boolean logic, every timer is an OPC UA tag. So a mill with 60 machines automatically generates 10,000 nodes in OPC UA."
No Data Highway
Nevertheless, Pluto's primary goal is to provide plant operators with selective access to relevant data as quickly and as straightforwardly as possible. "Producing a large amount of data and then just searching through it for important KPIs (key performance indicators) is probably not the right approach," says Samuel Ochsner. "In most installations, carefully selected data is queried. The selection here depends on the digital objective."
In other cases, such as with Bühler Insights Replay, the customer wants to see a playback of the MES system over time, which means that all data must be uploaded. In all cases, data selection with OPC UA can be tailored to the customer's objective.
A Complete Solution for All Plants
Pluto is a plant control system and is used for process control. It is used in smaller plants with up to a maximum of 150 machines. Larger plants, with more than 150 machines, are equipped with the Pluto-based production planning and control software, Mercury MES. As soon as recipes are required, Mercury MES is also used.
KÄGI in Switzerland
Swiss Chocolate Wafers from Kägi
Kägi Söhne AG is a traditional company that has been producing a wafer bar with chocolate coating, the Kägi Fret, since 1934. In order to continue producing high-quality bars under all conditions, the management decided to make production data measurable and, thus, optimize processes. In 2019, Kägi and the Bühler service team conducted a performance assessment workshop to find out how improvements could be made in the production process.
"By linking and visualizing the data in Bühler Insights, Kägi expects an increase of between five and eight percent in overall equipment effectiveness."
Digitalization of Production
All factors relevant to production were analyzed and translated into a detailed process analysis. Based on this, the team identified potential for improvement and drew up individual action plans that formed the basis for production optimization.
The workshop also revealed that occasional quality fluctuations were due to the fact that production decisions were often based on the experience and intuition of employees. Instead, decisions should be made based on data in the future.
Bühler Insights at Kägi
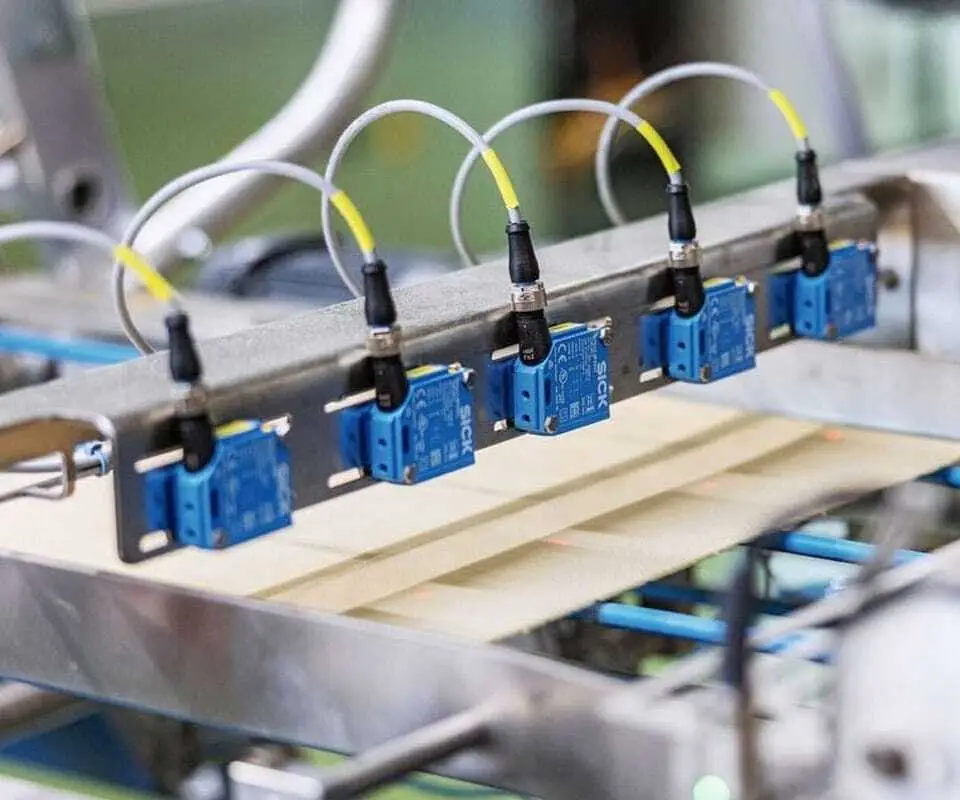
Bühler's fully automated inline inspection system WIS-EAGLE is equipped with 25–30 measuring points. Sensors can be seen above a wafer sheet.
Kägi's connection to the Bühler Insights platform creates transparency about process and machine data during ongoing operation. From the raw materials, to the baking and filling of the wafer sheets, to the chocolate coating, the data is now captured, analyzed, and interpreted at any time. On average, 25 to 30 data points are connected in each machine.
All process-relevant data and KPIs for each production step are visualized via dashboards. In this way, every operator can see how well the respective subprocess is running and influence it directly. This was all accomplished with OPC UA.
Kägi's connection to the Bühler Insights platform creates transparency about process and machine data during ongoing operation. From the raw materials, to the baking and filling of the wafer sheets, to the chocolate coating, the data is now captured, analyzed, and interpreted at any time. On average, 25 to 30 data points are connected in each machine.
All process-relevant data and KPIs for each production step are visualized via dashboards. In this way, every operator can see how well the respective subprocess is running and influence it directly. This was all accomplished with OPC UA.
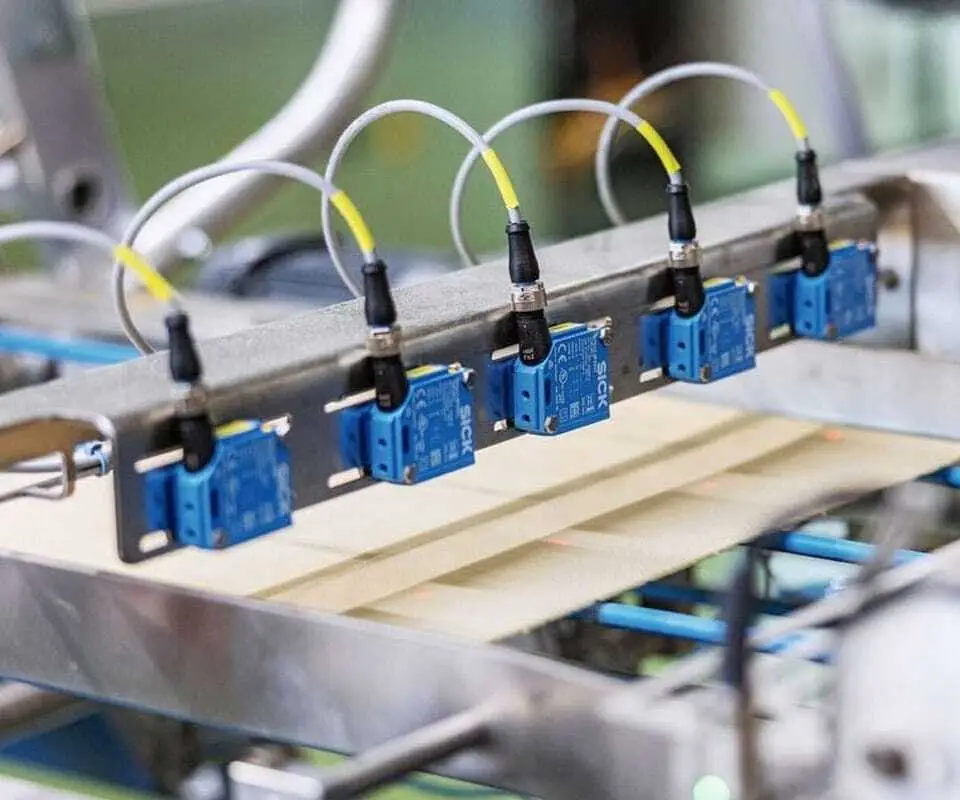
Bühler's fully automated inline inspection system WIS-EAGLE is equipped with 25–30 measuring points. Sensors can be seen above a wafer sheet.
Application & Training Center in India and Smart Mill in the UK
Application & Training Centers
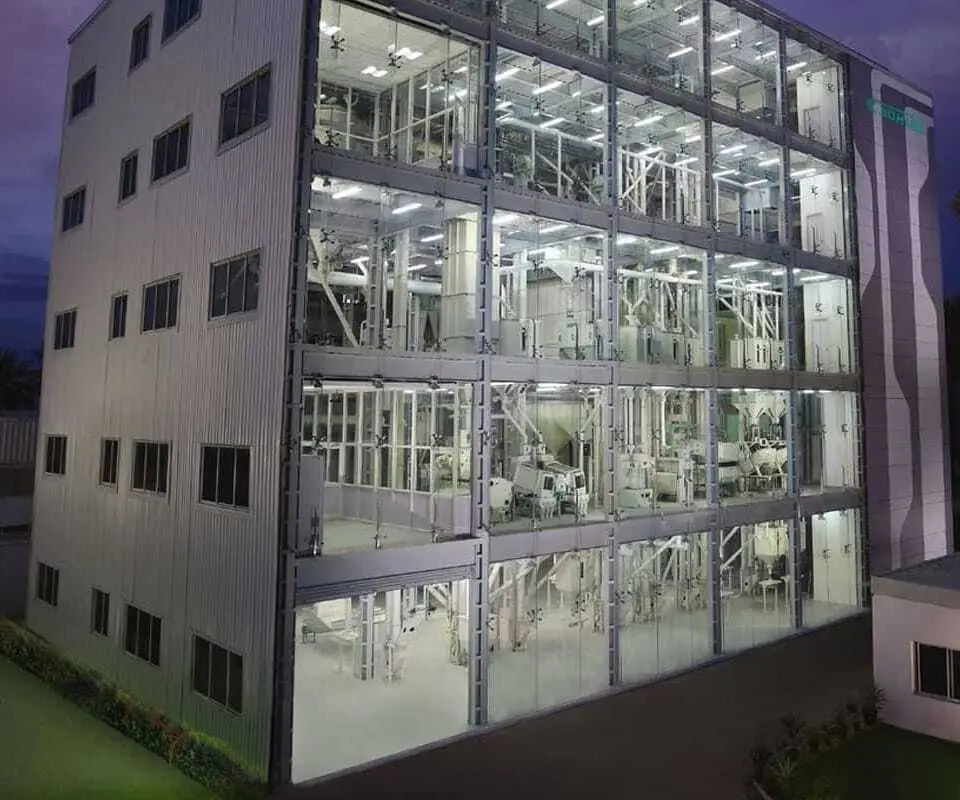
The ATC in Bengaluru is housed in a former rice mill, which is partially glazed to provide a view of machinery and operations inside.
Bühler Group maintains a network of Application & Training Centers (ATC) worldwide, where customers can test new products or recipes in small batches or receive further training. The ATCs are equipped with stateof- the-art machines and are fully digitized.
By collecting test data, using the Bühler Insights platform, and with the help of on-site analysis labs, the Bühler team can plan and conduct tests together with its customers in real time and adapt machines or processes.
Bühler Group maintains a network of Application & Training Centers (ATC) worldwide, where customers can test new products or recipes in small batches or receive further training. The ATCs are equipped with stateof- the-art machines and are fully digitized.
By collecting test data, using the Bühler Insights platform, and with the help of on-site analysis labs, the Bühler team can plan and conduct tests together with its customers in real time and adapt machines or processes.
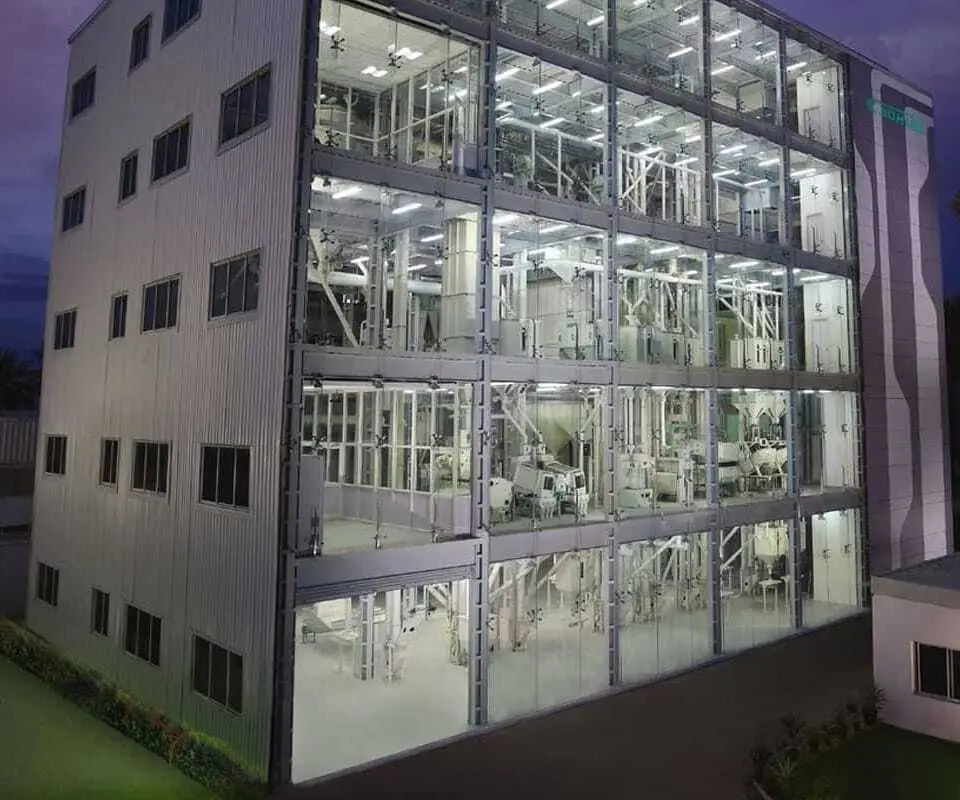
The ATC in Bengaluru is housed in a former rice mill, which is partially glazed to provide a view of machinery and operations inside.
ATC in Bengaluru, India
The processes that are demonstrated and tested here can run automatically, semi-automatically and manually.
Customers coming with valuable commodities such as coffee, pulses and spices can perform product tests to learn about the process, technology and performance of the machines under the guidance of experienced technologists before making an investment decision.
Training for the Rice Industry
India is the world's second largest rice producer with nearly 160 million tons. The global crop yield per year is 503 million metric tons. Bühler offers mill operators complete solutions including the supply of complete plants and equipment for cleaning, dehulling, whitening, polishing and sorting, and final installation and commissioning.
Mill owners, mill managers, and mill operators can attend training courses here to improve their skills and learn new operating techniques for profitable mill operation, maintenance, and management.
Innovative Mill Type Mill E3
The 'Mill E3' is an end-to-end digitized mill built from prefabricated modules and commissioned in 2021. At the heart of the Mill E3 are more than 15,000 data points that collect information on all steps in the production process. The name E3 refers to the three advantages this new type of mill offers them in terms of space requirements, installation time, and energy savings.
Revolution in Design...
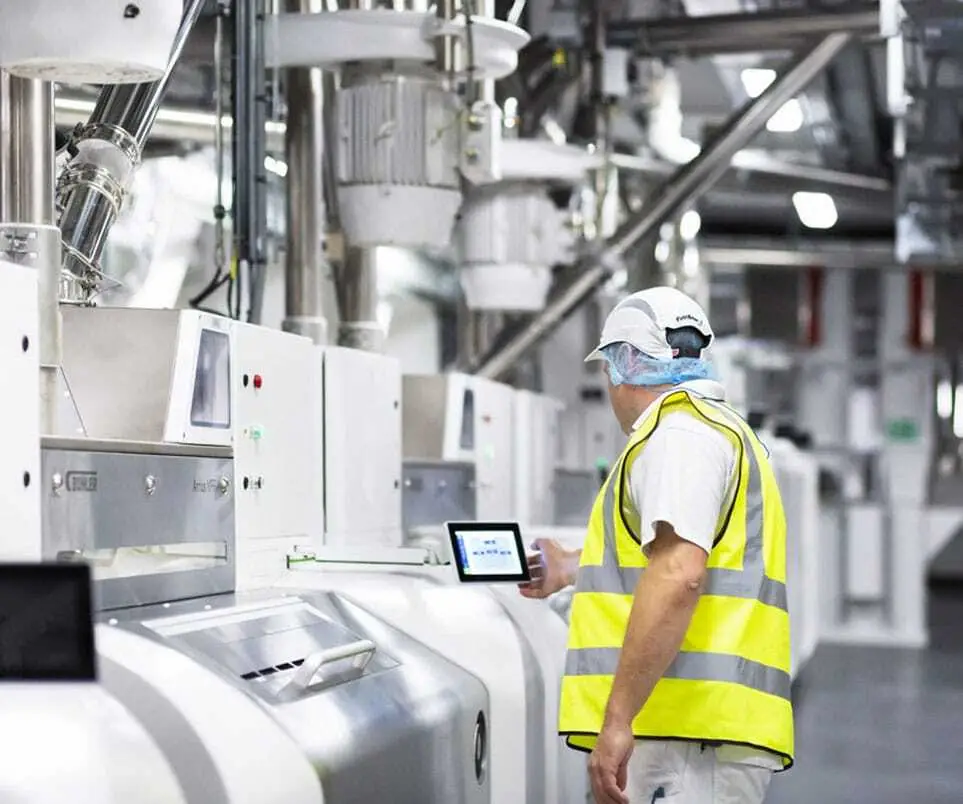
The first Mill E3 is located in Yorkshire in the north of England and is operated by Whitworth Bros. Ltd, the largest flour producer in the UK.
Bühler and Whitworth have a long-standing business partnership. With the Mill E3, Bühler has successfully tested a plug-and-play system for the installation of a mill that reduces the installation effort by 30 percent. The mill features a compact design with only three levels instead of the standard five or six.
Channels of stainless- steel pneumatic pipes run from ceiling to floor on each level, providing constant visibility into the process of converting wheat into flour. There is uncomplicated access to all equipment for maintenance and to check the seamless process flow. The energy requirement of Mill E3 is reduced by up to 10 percent.
... and Process Control
Bühler Insights established the connectivity of equipment in Mill E3. The Mercury MES production control system collects the operating data, stores the recipes, and manages production planning. Sensors and integrators form the basis of plant automation. Bühler has subsequently integrated OPC UA.
All aspects of production, from the delivery of raw materials to the sealing of trucks loaded with flour, and delivery to customers, are digitally mapped and controlled in Mercury MES. Only one operator is needed for the entire mill.
Bühler and Whitworth have a long-standing business partnership. With the Mill E3, Bühler has successfully tested a plug-and-play system for the installation of a mill that reduces the installation effort by 30 percent. The mill features a compact design with only three levels instead of the standard five or six.
Channels of stainless- steel pneumatic pipes run from ceiling to floor on each level, providing constant visibility into the process of converting wheat into flour. There is uncomplicated access to all equipment for maintenance and to check the seamless process flow. The energy requirement of Mill E3 is reduced by up to 10 percent.
... and Process Control
Bühler Insights established the connectivity of equipment in Mill E3. The Mercury MES production control system collects the operating data, stores the recipes, and manages production planning. Sensors and integrators form the basis of plant automation. Bühler has subsequently integrated OPC UA.
All aspects of production, from the delivery of raw materials to the sealing of trucks loaded with flour, and delivery to customers, are digitally mapped and controlled in Mercury MES. Only one operator is needed for the entire mill.
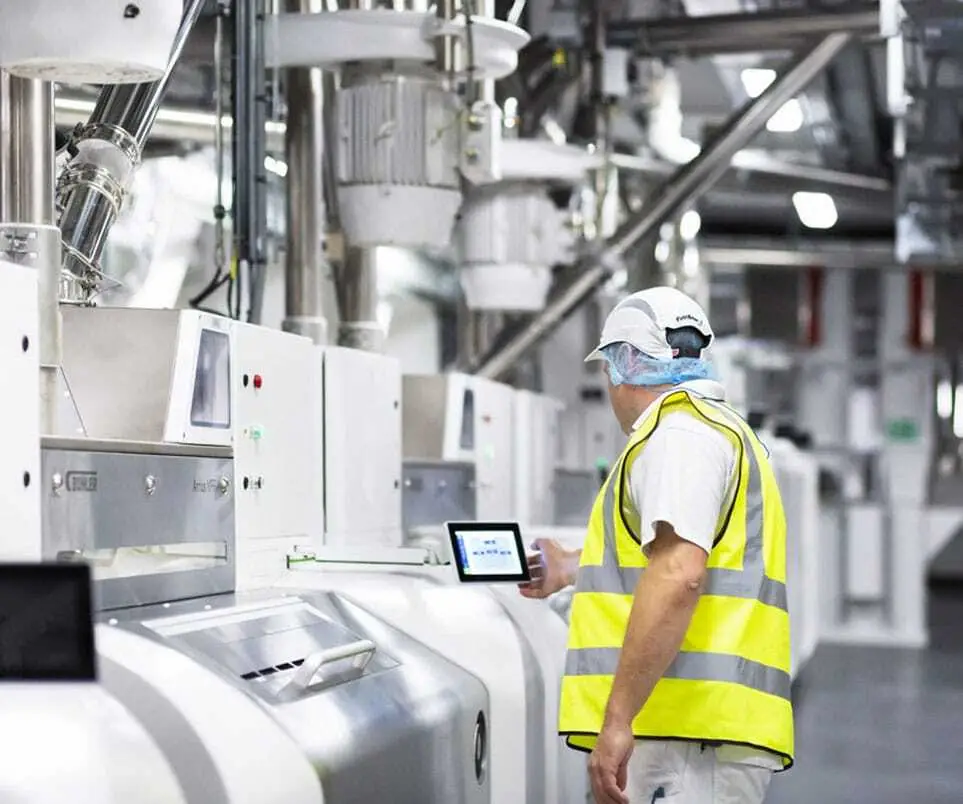
The first Mill E3 is located in Yorkshire in the north of England and is operated by Whitworth Bros. Ltd, the largest flour producer in the UK.