What is Maintenance 4.0?
The term Industry 4.0 was first introduced in 2011. It involved the automation of production with advanced technology and the Internet of Things (IoT). The goal was to make machines and systems that were capable of operating without human intervention. As part of the framework of Industry 4.0, Maintenance 4.0, or Maintenance Management 4.0, was the shift towards a more data-centric approach to maintenance and asset management.
It involves the use of technologies including Computerized Maintenance Management Systems (CMMS), visual inspection tools for remote monitoring and inspection, condition monitoring IoT sensors for predictive maintenance, augmented reality (AR) and virtual reality (VR) for remote maintenance and training, and cloud technology for optimized data management and analytics. These technologies will be further explained in this article. Maintenance technicians are able to make more data-driven decisions that improve operational efficiency and increase the operational lifespan of assets.
What is Maintenance 5.0?
Within the framework of Industry 5.0 is Maintenance 5.0. This concept is built upon the foundations of Maintenance 4.0 and involves a human-centric approach that is remotely controlled. The key to success is the harmonious collaboration between humans, hardware, and software. The enablers of Maintenance 5.0 are the evolution of advanced technologies from Industry 4.0. The Internet of Things will evolve to the Internet of Everything (IoE), and Cyber-Physical Systems will evolve to become Cognitive Cyber-Physical Systems, for example. Maintenance 5.0 aims to create a more intelligent, efficient, and sustainable maintenance ecosystem by leveraging cutting-edge technologies and fostering a closer synergy between humans and machines. It leverages more interactive digital twins, extensive IoT and edge computing for real-time data processing, and advanced robotics for flexible and remote maintenance operations. In Maintenance Management 5.0, AI-enabled robots are able to predict machine failures and suggest measures to prevent them. Human maintenance technicians validate these predictions and provide knowledge to further improve the predictive models used by the robots. This shows the symbiotic collaboration between humans and machines (human-robot collaboration (HRC)), which is the core of Maintenance 5.0.
What Are the Different Types of Maintenance?
In order to create the optimal maintenance plan, a maintenance planner needs to know all the different types of maintenance. The selection of the correct maintenance strategy will enable the correct maintenance decisions for each asset or equipment. The aim of maintenance strategies is to ensure the efficient, safe and continuous operation of their systems, machines, and infrastructures. The result: Autonomous maintenance, reduced downtimes and costs. Maintenance can be categorized as one of the following:
- Preventive Maintenance: Scheduled maintenance activities performed at regular intervals to prevent equipment failures and ensure reliable operation. This is currently one of the maintenance strategies that is most used in the digitalization of industry, the digitalization of construction, and in the digitalization of transportation.
- Corrective Maintenance / Reactive Maintenance: Repairs performed after a failure has occurred to restore equipment to operational condition. Also known as “run-to-failure maintenance” or “breakdown maintenance”. Corrective maintenance can either be planned (Planned Corrective Maintenance (CPL)) or unplanned (Unplanned Corrective Maintenance (CNP)).
- Condition-Based Maintenance: Maintenance activities triggered by the actual condition of equipment, as indicated by real-time data and monitoring.
- Planned Maintenance: Maintenance tasks that are pre-scheduled and executed according to a planned timetable to ensure equipment reliability and performance, regardless of the current condition of the equipment.
- Predictive Maintenance (PdM): Uses data analytics, AI, monitoring technologies like IoT sensors, and integrated systems to predict equipment failures and schedule maintenance just in time to prevent them. Information is collected by sensors and software such as Enterprise Resource Planning (ERP) and Enterprise Asset Management (EAM).
- Risk-Based Maintenance: Prioritizes maintenance activities based on risk, focusing resources on assets that pose the highest risk of failure.
- Reliability-Centered Maintenance (RCM): First used in the aviation industry, RCM is a systematic and corporate-level maintenance approach to optimize maintenance programs. Companies implementing RCM also use asset condition monitoring, maintenance planning, preventive maintenance, and predictive maintenance.
- Proactive Maintenance: A combination of preventive and predictive maintenance. Focuses on identifying and addressing root causes of equipment failures to prevent recurrence and extend equipment life.
- Time-Based Maintenance (TBM): Maintenance tasks performed at fixed time intervals, regardless of equipment condition, based on manufacturer recommendations or historical data.
- Emergency Maintenance: Immediate, unscheduled maintenance actions taken to repair equipment that has unexpectedly failed, disrupting normal operations.
- Prescriptive Maintenance (RxM): An advanced maintenance strategy that not only predicts failures but also recommends specific actions to address potential issues and optimize equipment performance. The next step from predictive maintenance.
- Smart Maintenance: Utilizes advanced technologies such as IoT, AI, and big data analytics to continuously monitor, analyze, and optimize maintenance activities, enhancing equipment performance and reliability through real-time insights and predictive capabilities. A sub category of smart maintenance is Lean Smart Maintenance (LSM). This approach combines lean principles with smart maintenance technologies to eliminate waste, improve efficiency, and maximize value in maintenance processes, ensuring that resources are used effectively and maintenance activities are streamlined and data-driven.
Wireless IoT Technologies and Maintenance
IoT Products for Maintenance
IoT products used for maintenance are closely linked to condition monitoring. IoT or machine-to-machine communication devices enable continuous monitoring of the environment in which they are installed. These devices include sensors, IoT gateways, actuators, measuring devices, and programmable logic controllers (PLCs).
Data acquisition systems are used to collect data and prepare it for analysis. Connectivity devices transfer this data to central cloud storage or analysis software. Wired networks, mobile networks such as 5G or Wi-Fi (WLAN IoT) are used for this purpose.
Maintenance can involve different teams and departments that require the same software tools in order to plan and document maintenance work efficiently. Multi-user licenses are used for this purpose, enabling companies to install and use a specific maintenance software on multiple workstations or devices.
OPC UA enables interoperable communication between sensors and devices from different manufacturers. Data analysis software such as AI and machine learning can be used to process and analyze the collected data. This in turn enables predictive maintenance.
RFID and NFC tags are also used to optimize maintenance work. These tags contain all the relevant data required by maintenance personnel and are read by RFID or NFC-enabled devices. In this way, the maintenance supervisor and staff can access the maintenance data and view the maintenance history and maintenance logs for each individual product, device or system.
Facts & Figures
Maintenance is a multi-billion dollar industry. According to the online platform “Finances Online”, the global market for CMMS software is expected to be worth over one trillion USD by 2026. In the manufacturing industry, 76 percent of companies worldwide relied on preventive maintenance in 2020. 60 percent of companies carried out reactive maintenance. It is estimated that over four billion USD will be invested in augmented and virtual reality for industrial maintenance in 2024.
However, the introduction of IoT technologies for maintenance is not yet widespread worldwide. Only around nine percent of manufacturing companies use industrial IoT technologies and cloud computing tools. 32 percent of maintenance executives surveyed believe that IoT can help them understand the condition of machines. 27 percent of them believe that IoT can help predict and prevent machine downtime.
Successful Examples of IoT in Maintenance
The aim of maintenance is to ensure the maximum technical availability and functionality of tools, devices and systems. Maintenance can be carried out in the private, commercial, and industrial sectors, and is crucial to ensure safety. For this reason, maintenance measures for railroads, trains, bridges and airplanes, for example, are especially regulated.
The following solutions show successful real-world examples of how wireless IoT technologies enable more efficient maintenance processes. The areas covered include the tire industry, construction, and digitalization in healthcare.
Michelin Enables Predictive Maintenance
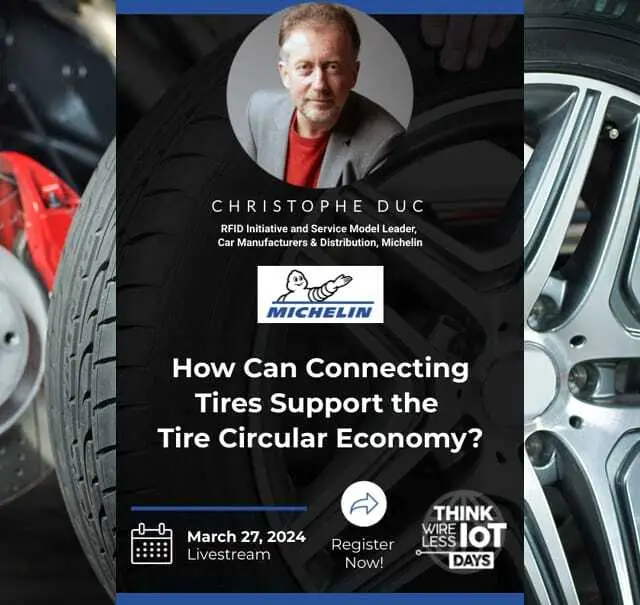
Tire manufacturer Michelin is driving the digitalization of the tire industry with the integration of embedded UHF RFID in tires. Michelin truck tires are already equipped with RFID. By the beginning of 2025, Michelin will be able to produce all car and light truck tires with RFID. The RFID tags from Hana RFID, Beontag and Murata are encoded with the GS1 standard SGTIN-96. The tag data is captured by wireless RFID readers. Michelin is currently working with car manufacturers on RFID-based solutions for predictive maintenance.
Tire manufacturer Michelin is driving the digitalization of the tire industry with the integration of embedded UHF RFID in tires. Michelin truck tires are already equipped with RFID. By the beginning of 2025, Michelin will be able to produce all car and light truck tires with RFID. The RFID tags from Hana RFID, Beontag and Murata are encoded with the GS1 standard SGTIN-96. The tag data is captured by wireless RFID readers. Michelin is currently working with car manufacturers on RFID-based solutions for predictive maintenance.
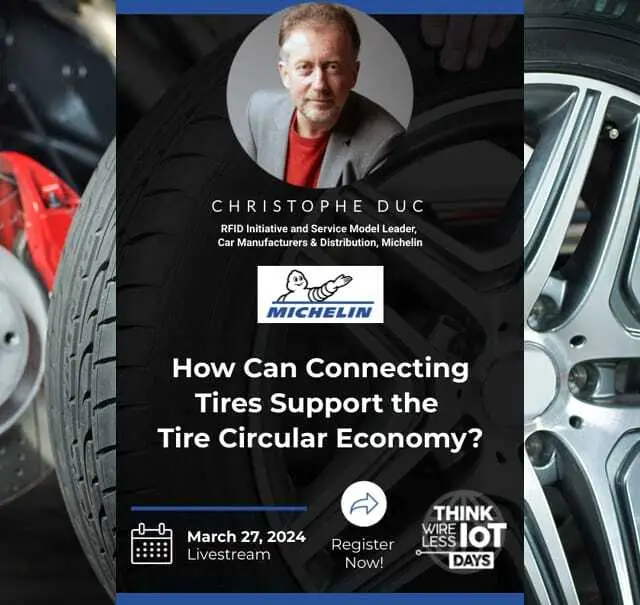
“Some of the use cases that we are starting to investigate and work with very specifically with automotive manufacturers are typically predictive maintenance. RFID is great for predictive maintenance.”
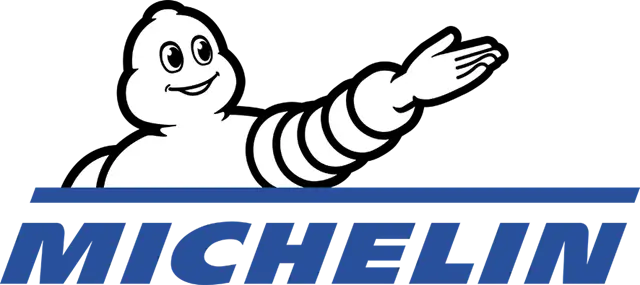
Christophe Duc
RFID Initiative and Service Model Leader, Car Manufacturers & Distribution
University of Catalonia Digitizes Maintenance
As part of the ASHVIN collaboration project, the Polytechnic University of Catalonia is working on the development of digital twins for 10 different assets, including bridges, buildings, and more. The project covers all construction phases, from design to construction and maintenance. An IoT platform is used to create a virtual replica of an asset. Data is received from sensors, monitoring devices, and edge computing devices. The platform's mathematical tools read and analyze all collected data to optimize maintenance processes.
"This project is called ASHVIN. This is about digital twins as assistants for improving productivity, safety, resource efficiency, and economy in infrastructure systems. It covers design, construction, and maintenance phases of our sectors."
Maintenance at West Park Health Centre
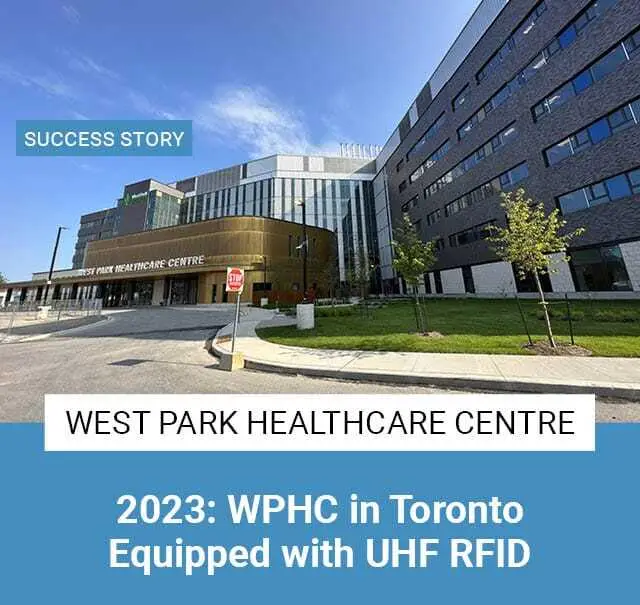
The West Park Health Centre in Canada has installed a passive UHF RTLS system covering 730,000 square meters. The system includes 608 antennas, 120 readers and 50 multiplexers. RFID tags from HID, Beontag and Metalcraft are used. The RFID system is also used to identify and locate assets, such as wheelchairs, in each area of the building that need to be serviced or maintained. Technicians and maintenance staff use handheld devices to filter out the assets that need servicing from the total inventory.
The West Park Health Centre in Canada has installed a passive UHF RTLS system covering 730,000 square meters. The system includes 608 antennas, 120 readers and 50 multiplexers. RFID tags from HID, Beontag and Metalcraft are used. The RFID system is also used to identify and locate assets, such as wheelchairs, in each area of the building that need to be serviced or maintained. Technicians and maintenance staff use handheld devices to filter out the assets that need servicing from the total inventory.
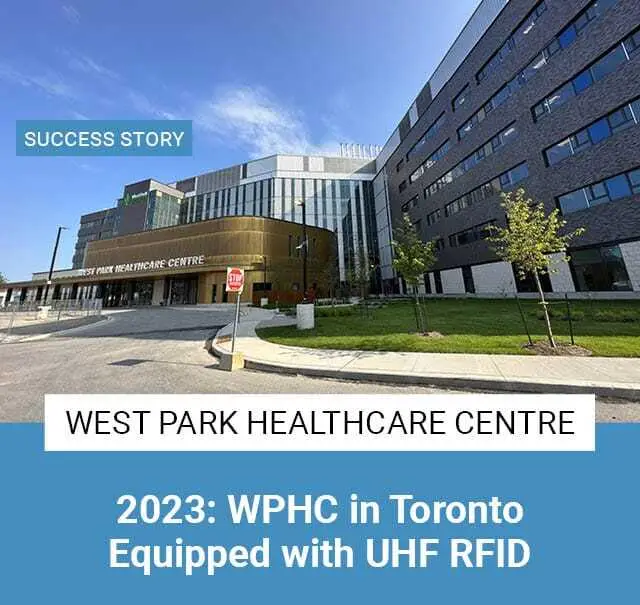
“Hospitals are under great pressure to be efficient. The RTLS solution not only allows acute search queries to be answered quickly, but above all data analyses can also be carried out.”
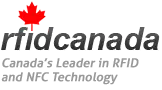
Khaled Elshimy
CEO
More Stories on Maintenance
How Has Digitalization Transformed Maintenance?
As technology develops, maintenance is becoming increasingly intelligent and automated. As a result of digitalization, various concepts such as maintenance 4.0, intelligent maintenance, predictive and health management (PHM), and digital maintenance have emerged. Smart factories, for example, require smart maintenance strategies.
The Industrial Internet of Things (IIoT), big data solutions, cloud computing, extended reality technologies like AR and VR, additive manufacturing, and autonomous robots are the most important prerequisites for digital maintenance. These technologies are the future of intelligent maintenance systems.
These technologies learn about assets such as machines, tools, or systems, make predictions about performance and condition, and enable the necessary hardware maintenance tasks to maintain the functionality of the assets.
Despite the increasing automation of maintenance tasks, human personnel are still an indispensable part of maintenance activities. Human workers monitor and maintain the automated systems and are also essential for complex tasks such as quality control and inspection. The emerging trend towards wearables supports human operators and maintenance personnel. This includes augmented reality glasses and voice-controlled headsets. They enable remote control of workers.
An increasing number of manufacturers are slowly switching to digitalized maintenance strategies. Interest in the use of advanced technologies and data-driven solutions to optimize maintenance activities is growing. This allows machine downtimes to be reduced or avoided, thus saving costs.
Nevertheless, there are still many companies that are reluctant to introduce intelligent maintenance strategies. Frequently asked questions are: How does the transition from preventive to predictive maintenance take place? How is the value of data determined and what data and data quality is required? Are both the company and customers ready for new business models? How can assets be connected to the IoT? Is an investment in a new IT platform required?
Computerized Maintenance Management Systems (CMMS)
Computerized Maintenance Management Systems (CMMS), also known as a Computerized Maintenance Management Information System (CMMIS), is a software solution that is used to automate and increase the efficiency of maintenance operations.
CMMS is used in industries where physical infrastructure is important. This includes the oil and gas industry, production, and is part of the digitalization of construction, and the digitalization of the transportation industry.
Today’s CMMS systems are cloud-based and mobile. Central to a CMMS system is the database with a data model. Here, information about the assets to be maintained is organized. Information such as the purchase date, warranty information, and maintenance history is recorded.
Work order management is the main function of a CMMS system. It automates the generation of work orders and manages materials and maintenance and repair operation (MRO) equipment. The status of every asset can be reviewed in a CMMS system, and asset downtime can be tracked. Maintenance costs are also recorded. CMMS supports preventive maintenance by scheduling regular maintenance tasks to prevent equipment breakdowns and extend asset lifespan.
A CMMS system can be integrated with other systems like Enterprise Resource Planning (ERP) systems, Building Automation Systems (BAS), and Building Management Systems (BMS). This provides maintenance workers with a more comprehensive overview of maintenance operations.
Virtual Inspection Tools
Virtual inspection tools for modern maintenance are advanced technologies that enable a remote, efficient, and accurate inspection of equipment and facilities. These tools leverage various technologies to streamline maintenance processes, ensuring high standards of safety and operational efficiency. Here are some key types of virtual inspection tools:
Drones, Unmanned Aerial Vehicles (UAVs), robotics, and Unmanned Ground Vehicles (UGVs) can be equipped with high-resolution cameras and sensors to inspect areas that are dangerous, or hard to reach. They provide real-time visuals and data and increase safety for maintenance workers.
Augmented reality (AR) and virtual reality (VR) technologies allow maintenance personnel to visualize equipment and processes in a virtual environment. AR can overlay digital information onto physical objects, aiding in real-time and remote troubleshooting and training. VR can simulate complex maintenance scenarios for training and planning purposes.
IoT sensors and smart devices are also used as virtual inspection tools. IoT sensors can be installed on equipment to monitor various parameters like temperature, vibration, and pressure. In other words, they enable the condition monitoring of assets. These sensors provide continuous real-time data, enabling predictive maintenance and early detection of potential issues.
Remote monitoring systems use a combination of sensors, cameras, and software to monitor equipment from a distance. They provide real-time data and alerts, allowing maintenance teams to perform diagnostics and inspections without being physically present. Smart glasses are also used for remote maintenance and inspection.
Mobile applications enable maintenance personnel to perform inspections using smartphones or tablets. These apps often include features for data collection, photo documentation, and integration with CMMS, facilitating efficient and accurate inspections.
The Advantages of Smart Maintenance
Advantages of Wireless IoT
- Automated maintenance activities
- Real-time condition monitoring
- Reduction of downtime and costs
- Remote guidance for maintenance personnel
- Increased efficiency in production
The implementation of intelligent maintenance strategies offers numerous advantages. Computerized maintenance management systems (CMMS) automate maintenance activities. In addition, data on work orders, preventive plans, and inventory is centralized. The IoT enables remote monitoring of equipment through sensor data. Problems are detected and identified at an early stage, and devices and machines retain their optimum functionality, higher productivity and longer service life. Predictive analytics uses machine learning to predict future plant conditions. This also improves the safety of machines and systems. AI detects anomalies and analyzes performance data for better decision-making. Industry 4.0 methods, such as augmented reality, support technicians with complex tasks remotely. Automation, including robotic arms, reduces labor costs and speeds up production. Overall, smart maintenance increases machine efficiency, reduces machine and equipment downtime, and saves costs.
The implementation of intelligent maintenance strategies offers numerous advantages. Computerized maintenance management systems (CMMS) automate maintenance activities. In addition, data on work orders, preventive plans, and inventory is centralized. The IoT enables remote monitoring of equipment through sensor data. Problems are detected and identified at an early stage, and devices and machines retain their optimum functionality, higher productivity and longer service life. Predictive analytics uses machine learning to predict future plant conditions. This also improves the safety of machines and systems. AI detects anomalies and analyzes performance data for better decision-making. Industry 4.0 methods, such as augmented reality, support technicians with complex tasks remotely. Automation, including robotic arms, reduces labor costs and speeds up production. Overall, smart maintenance increases machine efficiency, reduces machine and equipment downtime, and saves costs.
Advantages of Wireless IoT
- Automated maintenance activities
- Real-time condition monitoring
- Reduction of downtime and costs
- Remote guidance for maintenance personnel
- Increased efficiency in production
Partners Spezialized in Maintenance Solutions
The Challenges of Smart Maintenance
The implementation of smart maintenance is associated with various challenges.
When using AI in companies for smart maintenance, large amounts of data must be made available so that the AI can be properly trained. Companies need to implement data management strategies that allow them to collect and analyze large amounts of data over an extended period of time. A biased AI can lead to false alarms and unnecessary downtime.
The right data acquisition devices must be selected for smart maintenance. To select the right devices, companies need to know exactly which parameters need to be monitored. Managing large amounts of data places high demands on the data infrastructure. Data security and data protection are also of great importance, as networked technologies increase the risk of cyber attacks.
When introducing smart maintenance, high implementation costs can be incurred in order to integrate IoT sensors, CMMS, and predictive analytics systems. Integration into existing IT infrastructures and machinery can be complex and time-consuming.
There is a shortage of specialists with the necessary technical and IT knowledge. Appropriate technical knowledge of the devices is required to implement intelligent maintenance strategies. Maintenance staff must be trained accordingly.
The scalability of solutions across different locations can also be difficult. For systems, machines, or devices that are located in remote areas or operate in harsh environments, efficient remote management of employees can also be challenging.
Outlook – Next-Level Maintenance
New maintenance models, AI, machine learning, and augmented reality are just some of the current trends in maintenance.
Maintenance-as-a-Service (MaaS)
Maintenance-as-a-Service (MaaS) is a subscription-based model that is critical to streamlining maintenance processes and optimizing overall asset performance. This model is becoming increasingly important as cloud computing and cloud-based business models transform industrial maintenance.
Artificial Intelligence and Machine Learning
Predictive maintenance is becoming more intelligent through the use of AI and machine learning. Collected data is analyzed and accurate predictions are made based on this data. Predictions based on AI and machine learning support decision-making and determine the best times for maintenance activities.
Augmented Reality (AR)
Augmented reality (AR) is seen as a ground-breaking innovation in maintenance. On-site and remote maintenance employees can be guided in real time with the support of AR glasses, for example. This eliminates the need for employee training.