Advantages
Challenges for Rail Operators
Rail operators and train control systems face a variety of challenges that can affect their efficiency and safety. One of the biggest hurdles is capacity management and congestion on rail networks. As demand continues to grow, it is becoming increasingly difficult to smoothly manage train traffic.
Without intelligent solutions, this can lead to delays and an inefficient use of resources. Another key problem is safety and accident prevention. Given the high traffic density on the rails, control systems must be able to prevent accidents and respond to emergencies at all times.
The implementation of IoT technologies offers promising approaches here: Real-time monitoring, predictive maintenance and automated control systems can significantly reduce these challenges and make the operation of rail systems more efficient, safer, and future-proof.
Kathrein Solutions has provided a comprehensive RFID solution including the CrossTalk software for the Swiss Federal Railways to achieve this.

Vehicle identification through «RFID in Rail» is seen as an enabler technology with which all processes that rely on a vehicle ID can be digitized. Only with «wheel-accurate» vehicle identification can data and information be reliably assigned to the correct vehicle components and the necessary processes automatically triggered using appropriate evaluation methods.
Detecting Critical Developments at an Early Stage
SBB Infrastructure is the operator of the train monitoring systems (“Zugkontrolleinrichtungen” – ZKE). ZKE are stationary measuring devices along the track that enable a comprehensive inspection of passing trains for various safety-relevant properties. The aim of the infrastructure operator is to detect defective vehicles at an early stage and prevent certain incidents through targeted measures.
The train driver is warned, for example, to reduce speed if a temperature of 130 degrees is measured on an axle, which indicates a fault. The route is adjusted to reach the next planned intervention point, where the vehicle is removed from the train. The infrastructure and all vehicles running on it are permanently monitored to ensure that operations are not disrupted.
For safety and cost reasons, SBB wants to avoid unexpected problems with passenger or freight rail vehicles. Proactive maintenance is an important process for a smooth, reliable timetable.
Advantages of the RFID Solution
- Data is captured and transmitted to the responsible railway operators or vehicle keepers
- Digitization and real-time analysis of the data enable early damage detection and axis-specific assignment for triggering alarms
- Automated train monitoring and non-discriminatory control of rolling stock using train monitoring systems
- Generation of added value through reliable vehicle identification at full line speed, including automation of manual processes, vehicle-specific condition monitoring and forecasting of vehicle condition development for the optimization of vehicle maintenance
- The data has the potential to forecast developments in vehicle condition. This would enable a predicted condition development and an increase in availability through vehicle identification.
- Increased safety, condition optimization by eliminating causes and optimizing life cycle costs
- Clear assignment of wheel contact force measurements to individual wheels through vehicle identification with RFID, facilitates tracking of wheel condition development
Vehicle Condition Monitoring
Monitoring of Infrastructure and Vehicles
The basis for the desired quality assurance measures was initially vehicle identification via RFID transponders, which made it possible to assign the data to a vehicle down to the exact axle. This is the only way to reliably track the vehicle status across several train monitoring systems and to detect critical developments at an early stage.
The detection of vehicle axles was ensured via rail contacts installed on the track. By linking this data with the RFID identification data, it was possible to generate an intuitive business event that provided information about the condition and individual vehicle data. The result: Real-time transparency on the condition of the rail vehicles.
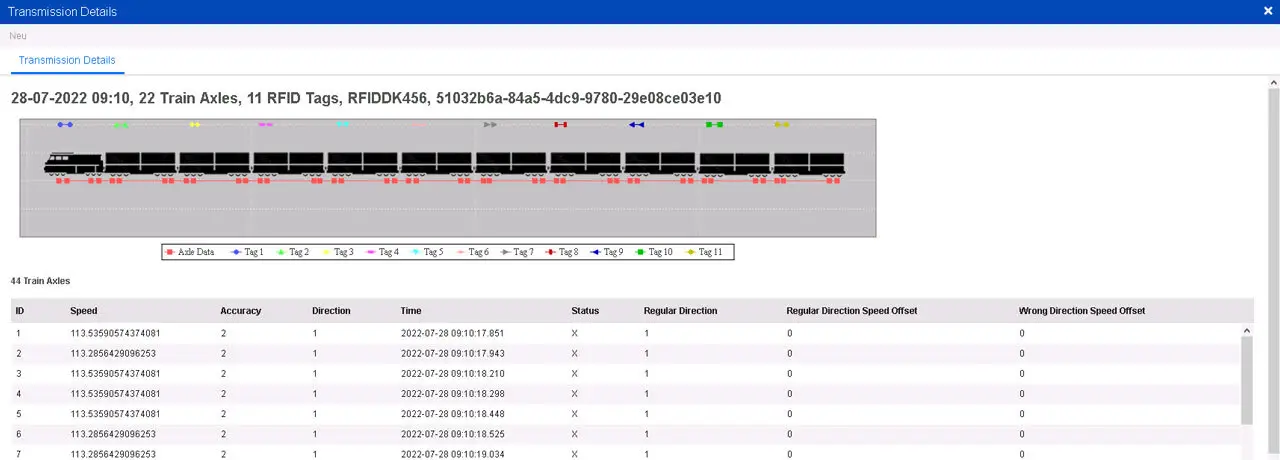
Example excerpt from the SBB application developed by Kathrein Solutions to display the determined vehicle data on mobile devices.
Historical Background
In 2013, SBB set up the first pilot site for the installation of train monitoring systems (ZKE). The aim of this pilot project was to prove that vehicles can be accurately identified down to the axle or wheel, and then combined with the measurement data from the CCS systems under the given railroad operating conditions. For the infrastructure tests, a train with four vehicles was initially equipped with RFID tags.
At the same time, another SBB division, the Passenger Division, also installed an initial system in a car wash. The aim there was to automate the washing process. Billing based on the selected washing program has already been automated. This pilot project therefore took place simultaneously in two divisions in 2013. The washing and cleaning process is still carried out using RFID technology today. The pilot system was already in operation in 2014.
In the following years, the system was tested, refined and financially supported for a nationwide rollout from 2015 to 2018. During this time, all SBB locations were equipped with RFID technology, accompanied by extensive advocacy efforts to encourage vehicle keepers to participate in the tests.
Although the technical implementation of the project was completed in 2018, continuous efforts are being made to integrate additional data sources and encourage more vehicle owners to use the data for maintenance. This iterative process requires time for users to develop trust in the data and fully understand its potential applications.
Hardware & Software
Installed RFID Hardware
Passive RFID technology is being established throughout Europe as a vehicle identification solution in accordance with the GS1 standard “RFID in Rail” and ISO 18000-6C EPC Class1 Gen2. SBB has decided to use “RFID in Rail” across the board and to make some of the captured data available to vehicle keepers free of charge. Already 60 percent of the vehicles running on the SBB infrastructure are equipped with RFID tags for identification.
The installation of the Kathrein readers required structural modifications, which were carried out jointly by ZKE and the supplier. All ZKE installations were equipped with RFID readers. That is around 120 systems at 70 locations. Typically, there is a ZKE site every 30-50 km. Each of the 70 or so locations comprises one to four tracks, each of which is assigned a reader.
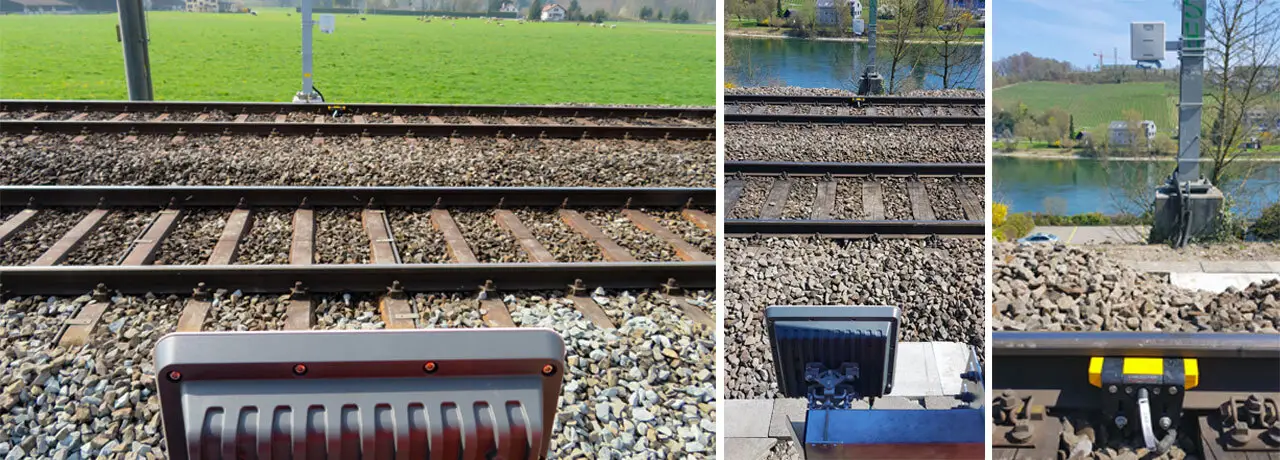
The RFID transponders in trains and the trackbed RFID readers must be extremely robust and withstand all weather conditions.
Robust RFID Labels and Readers
Passive RFID transponders are attached to the vehicles, which are read by RFID readers at transit speeds of up to 180 km/h. The RFID transponders on the trains and the RFID readers installed on the track bed require special robustness that can withstand all weather conditions. This is particularly important in winter in Switzerland, where the weather conditions can be extreme.
The Kathrein ARU 3500 reader is specially designed for harsh environments and is therefore ideally suited to these conditions. The hardware costs were kept within limits for a single-track application thanks to the ARU 3500's internal antenna. For a dual-track application, an additional Kathrein Reader ARU 3500 was connected as a slave. Using the configured IDs (master and slave) on the main reader, each acquisition can then be assigned to the track accordingly.
The rail vehicles are marked with an RFID tag in accordance with the DIN standard EN17230. The readers used have a wide-angle antenna with a 65° wide angle and use the UHF-RF unit with a bandwidth of 865-868 MHz, with optimum connectivity via PoE+.
Data Acquisition at 200 km/h, in Snow or Heavy rain
The read requirements of the RFID transponders on the vehicles included the vehicle number. The ZKE measurement data is enriched with target data such as timetable, formation, and load information for intervention and analysis. In addition, the data acquisition had to be reliable in a range from 5 km/h to 180 km/h.
Software and Data Visualization
Kathrein's CrossTalk software was used for this project. For user-friendly visualization, Kathrein Solutions developed an app tailored to SBB to display the recorded vehicle data (presence, vehicle number, axles) on various end devices. This visualization depicts each vehicle with each individual axle and provides an immediate overview and transparency for each rail vehicle recorded.
The RFID Solution
Capturing and Intelligently Processing Data
Once the RFID readers have captured the data, it is transferred to the app specially developed for SBB via the Kathrein CrossTalk software. Each reading point transmits the data to three servers: A production server, a backup server, and a test server. The RFID hardware is monitored centrally via an internal SBB system, which receives the reader status data via the Kathrein CrossTalk agent and the CrossTalk server.
Kathrein CrossTalk also enables the RFID hardware to be integrated into SBB's leading system. The Kathrein RFID reader is made intelligent by means of the CrossTalk agent so that it can provide the SBB system with its status data.
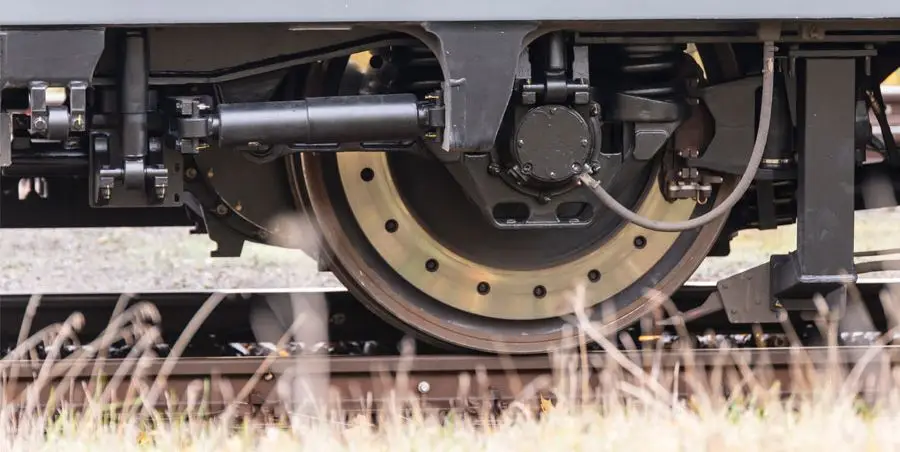
RFID tags provide the vehicle number and thus enable predictive maintenance.
Real-Time Data for Predictive Maintenance
Kathrein Solutions has equipped SBB's 70 train monitoring systems with around 120 RFID readers to ensure comprehensive safety monitoring. These sophisticated measuring and sensor systems record around 11,000 trains per day, and continuously and autonomously perform a variety of monitoring tasks.
Equipping vehicles with RFID tags is a prerequisite for predictive maintenance. The analysis of vehicle data such as temperature, axle load, brake, and load data enables problems to be identified at an early stage. More than 40 million axles are measured every year. This includes around 10 million vehicle measurements.
Early detection improves vehicle condition and reduces damage to infrastructure and service interruptions. Sensors in the SBB network monitor important parameters such as axle temperature and brake functionality, and detect anomalies. Real-time data analysis enables proactive intervention to prevent risks and ensure safety.