Information From the ERP System in Real Time
The Six ‘Rs’ of Logistics
In material management, Chinese companies and service providers also have to be measured by the “six Rs” of logistics: the right product, quality, amount, place, time and cost. However, the trend in this sector towards greater automation and increasing logistics performance only started around ten years ago. One reason for this delayed development could be the handling of hazardous substances and the special safety requirements and technology associated with it.
An increasing number of manufacturers, however, are catching up worldwide in order to transfer the already high degree of automation in the chemical industry likewise onto logistics tasks. This is demonstrated by one of the largest energy and chemicals companies in China.
Together with Turck and system integrators New Trend International Logistics Technology, the company installed RFID technology in a digital goods distribution center situated in the southwest of the industrial metropole of Guangzhou. The contactless detection of incoming and outgoing goods now provides those involved with considerably greater transparency of stock levels.
"The contactless recording of incoming and outgoing goods via RFID provides a much higher transparency of the warehouse inventory."
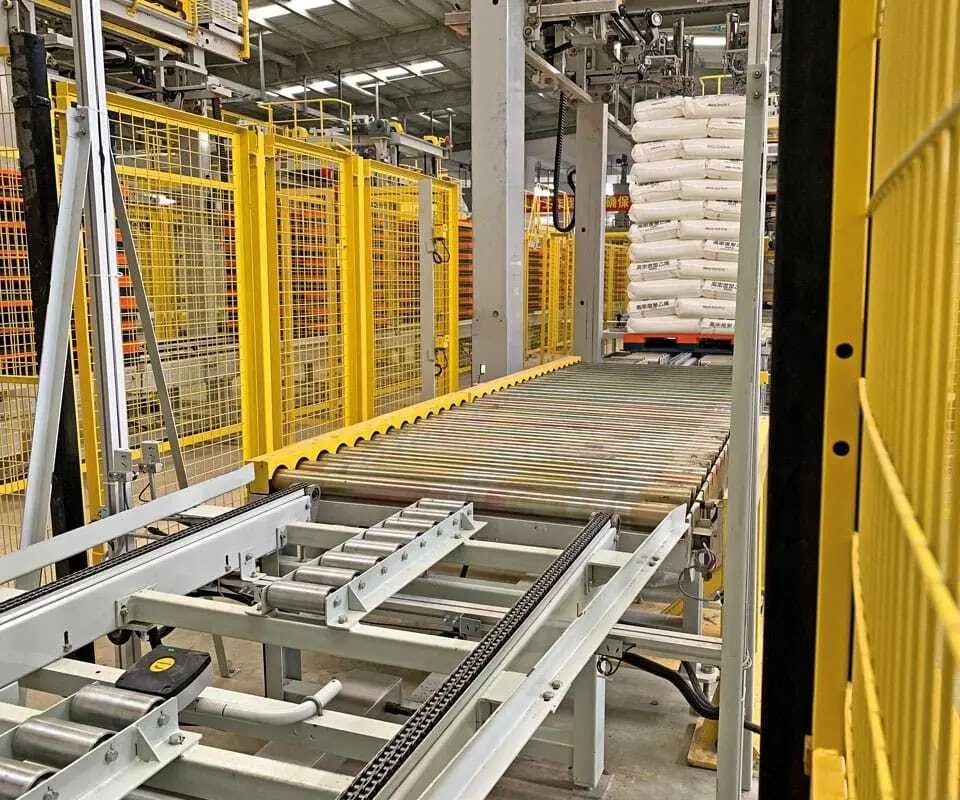
The processes in the goods center were optimized with RFID communication. The read/write heads (bottom left) transfer material data via UHF RFID to the transport pallets.
Inventory Control in Focus
The operator of petrochemical plants previously used here a combination of standardized manual steps and semiautomated computer management in the warehouse.
This neither produced the required logistics efficiency nor minimized error quotas. An excessively large number of work steps were required just to place or find material or organize the stock levels for slightly varying types of goods. In view of the increased demand for the quality of logistics services, it was particularly necessary to ensure correct purchasing and inventory controls.
More Real-Time ERP Information with UHF RFID
When did material reach or leave the warehouse and how much? What items were involved? Where are the products stored? The ERP system has to make this information visible in real time and provide it on demand on the transported material. The Chinese system integrator therefore opted for data transmission via UHF RFID.
In brief: read/write heads use a high frequency signal to write or read a specific amount of information to or from passive RFID tags and to transfer it to the IT network via an interface. Thanks to the UHF technology the exchange is carried out between the reader and the tag over several meters. Information is also captured when objects pass at high speed.
Up to Nine Stacked Empty Pallets Are Read Simultaneously
Read/Write Head Marries Material Data with the Pallet
The chemicals company transports goods on returnable pallets. An RFID tag which is provided with a unique ID is embedded in each transport pallet in order to link the data closely to the material or product conveyed. This tag is written for the first time in the packaging area. It is here that TN-Q120 read/write head virtually “marries” the specific material information with the pallet before it reaches the goods center.
The transmission of the cube-shaped UHF reader complies with ISO 18000-6C, and thanks to its IP67 protection type can operate if necessary in harsh environments with temperatures between -20 and +50 °C.
Other type TN-Q120 RFID readers are installed in the warehouse along the automated conveying line. They record incoming and outgoing goods movements and also register the exact position of the pallets. The TN-Q175 read/write head is used at other locations wherever a particularly high level of power is required. These enable the reliable reading of nine stacked empty pallets.
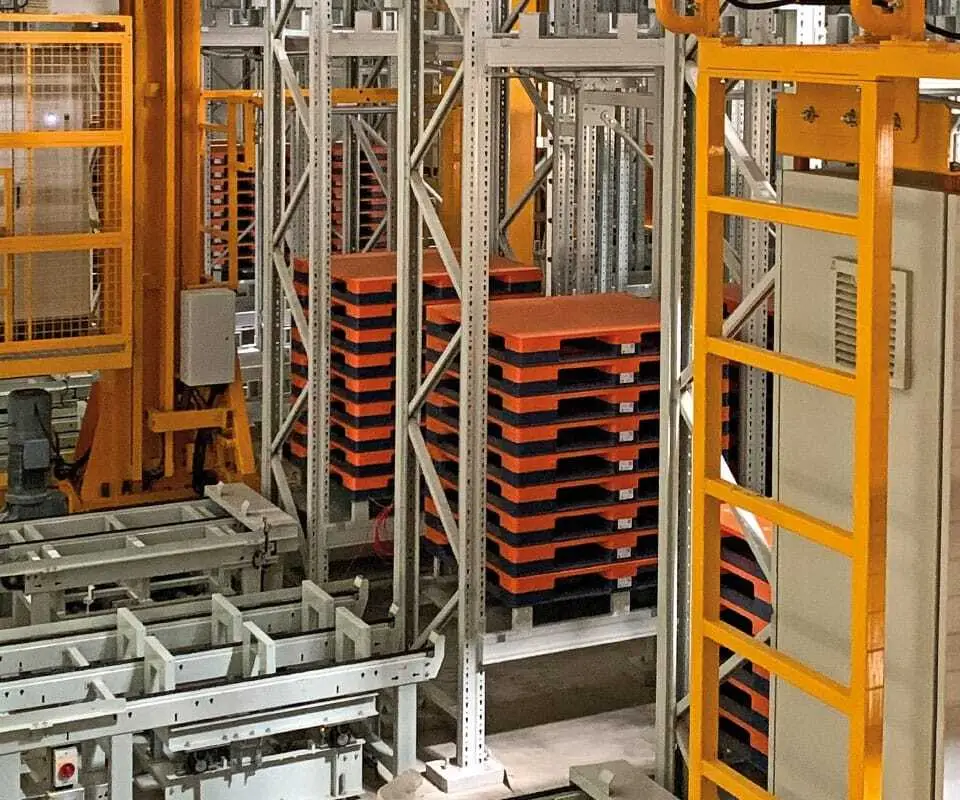
The RFID interface TBEN-S2-2RFID-4DXP between RFID reader and and IT network is easy to configure and powerful enough to read the data of the RFID reader even in the case of multiple pallet captures.
IP67 Interface for Direct RFID Integration
The TBEN-S2-2RFID-4DXP RFID interface is used between the RFID reader and the IT network in order transfer the information from the read/write heads rapidly to a production control system in the ERP.
The ultra-robust RFID module (IP67/IP69K) is designed for mounting outside of the control cabinet and allows the connection of two UHF read/write head as well as sensors and actuators at the same time. “The interface is easy to configure and powerful enough to transfer data from the RFID readers to the PLC quickly, even when multiple pallets are being read,” says Han Qingyun, electronics engineer at New Trend International Logistics Technology.
The special feature of the compact module is its simple system integration without the need for any programming effort or function blocks. The TBEN-S also “speaks” three Ethernet protocols: Profinet, EtherNet/IP and Modbus TCP.
Conclusion
Better Warehouse Utilization, Greater Security
The data on incoming and outgoing goods enables the ERP system to continuously synchronize inventory levels. For users this is a major relief, especially since they can also access real time information about available capacity or the position of transport pallets. It enables the optimum use of space resources. Knowing where and which goods movements are taking place, however, also meets the safety requirements of the chemicals industry.
Greater efficiency ultimately also has an effect on costs. In other words, far fewer manual operating steps and material costs are required for warehouse management. Identification processes via RFID are automated; and rewritable tags enable the multiple use of transport pallets.