Robots against labor shortage and climate change
The Port and Douro wines are distributed worldwide to more than 120 countries. Around 24 million bottles are sold each year. More than 20,000 employees are needed for the harvest in the entire region – Symington employs 800.
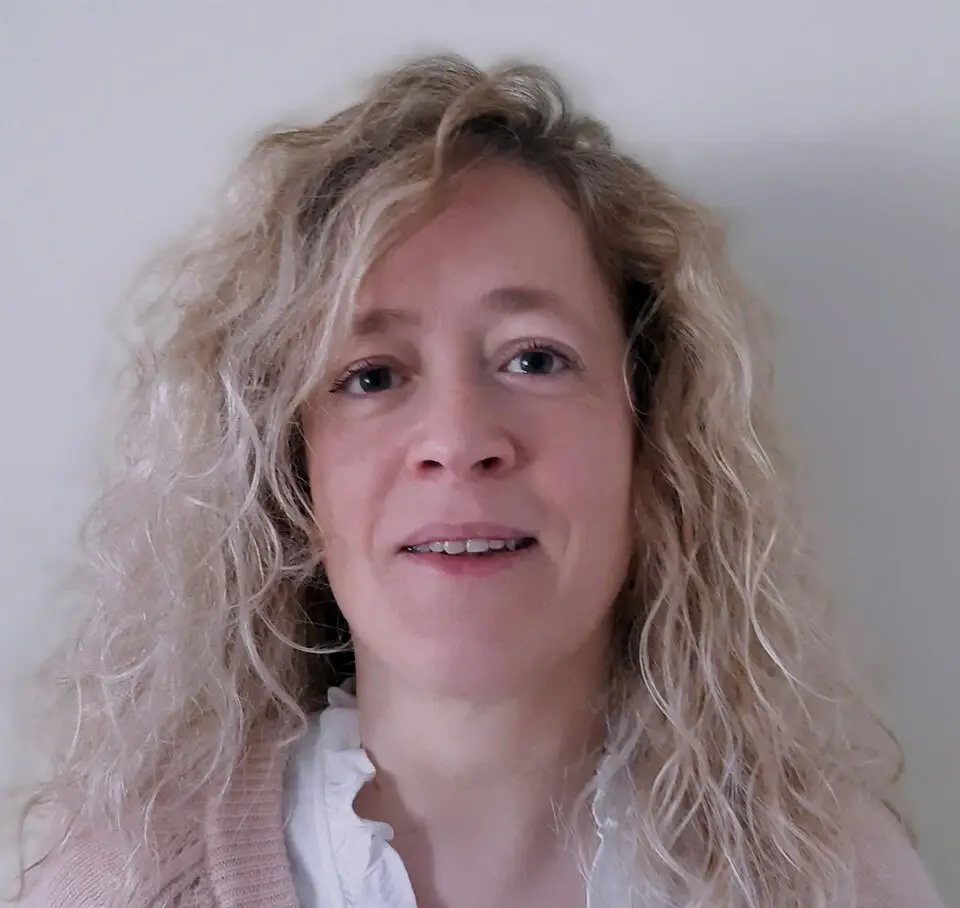
Organic and Experimental
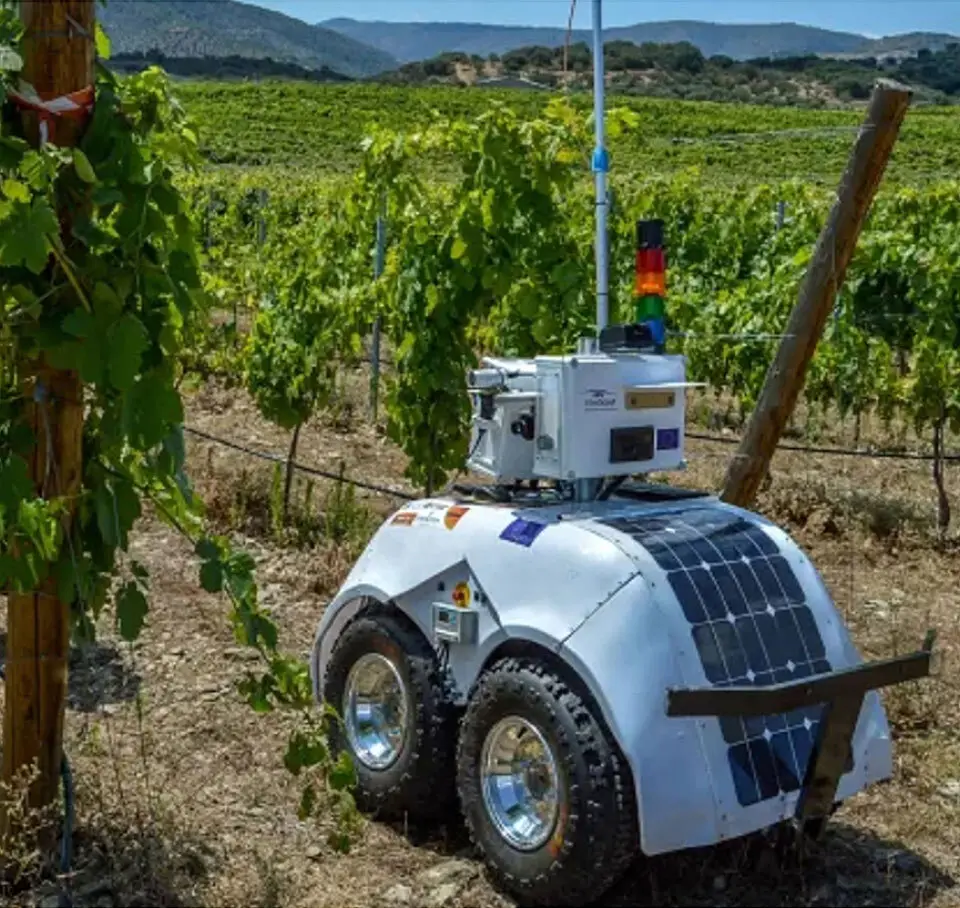
VineScout: Robots against labor shortage and climate change
With approximately 132 hectares, Symington has the largest certified organic vineyard area in northern Portugal. In addition, the company operates experimental vineyards to test new wine varieties. The grape variety libraries in Ataíde (53 grape varieties) and in Bomfim (31 grape varieties), are the largest collection of indigenous grape varieties in Portugal.
All vineyards – a total of 1,024 hectares – are managed according to strict specifications and with the goal of minimal interference. To market its products, Symington operates four leading port houses and offers a portfolio of Douro wines.
Robots Roll Through the Vineyards
The data collected provides information on the influences of temperature, rain and irrigation. Vineyard irrigation management is remote and automated via sensor technology. In the event of sudden changes in the climate, it is imperative to be able to react within a few hours – this is only possible with digital solutions. Two machines for harvesting the grapes are used on the terraced vineyards.
Information on the degree of ripeness and position is transmitted to the machine. Certain areas can be left out in advance. If the machine is then used the next time, the data from the previous operation is already processed automatically and the next unit is configured correctly.
With approximately 132 hectares, Symington has the largest certified organic vineyard area in northern Portugal. In addition, the company operates experimental vineyards to test new wine varieties. The grape variety libraries in Ataíde (53 grape varieties) and in Bomfim (31 grape varieties), are the largest collection of indigenous grape varieties in Portugal.
All vineyards – a total of 1,024 hectares – are managed according to strict specifications and with the goal of minimal interference. To market its products, Symington operates four leading port houses and offers a portfolio of Douro wines.
Robots Roll Through the Vineyards
The data collected provides information on the influences of temperature, rain and irrigation. Vineyard irrigation management is remote and automated via sensor technology. In the event of sudden changes in the climate, it is imperative to be able to react within a few hours – this is only possible with digital solutions. Two machines for harvesting the grapes are used on the terraced vineyards.
Information on the degree of ripeness and position is transmitted to the machine. Certain areas can be left out in advance. If the machine is then used the next time, the data from the previous operation is already processed automatically and the next unit is configured correctly.
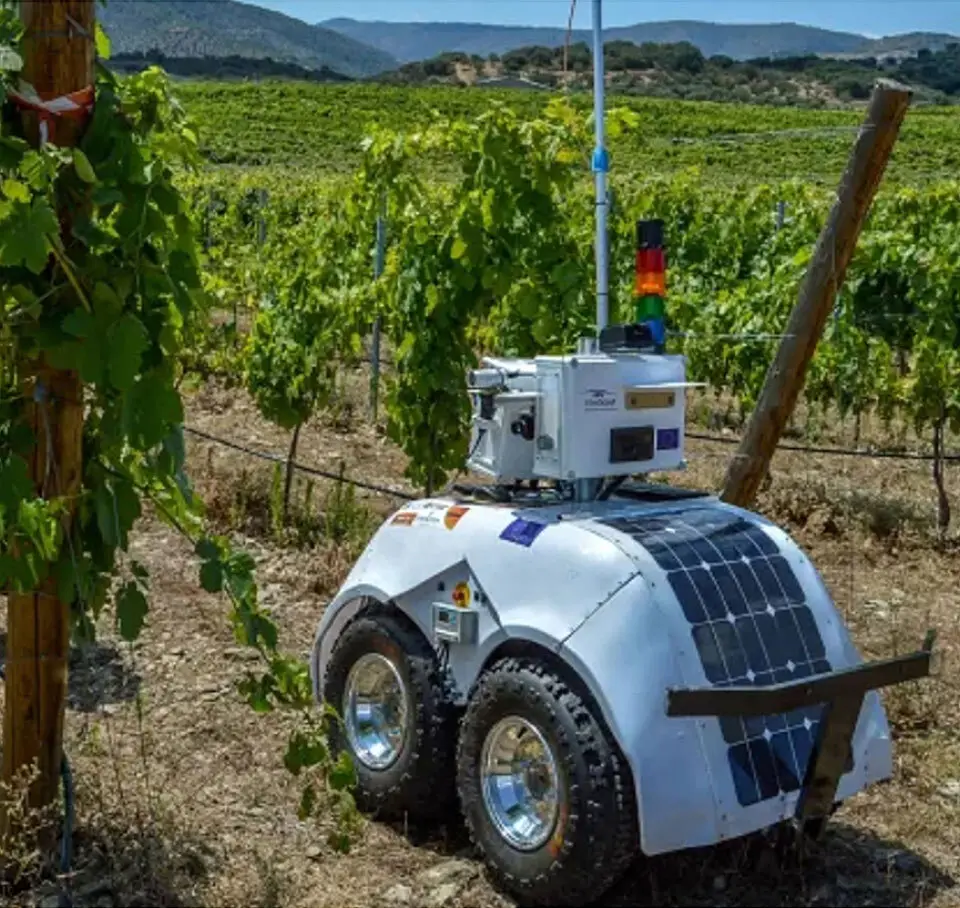
VineScout: Robots against labor shortage and climate change
UHF RFID transponder on lattice boxes
RFID Tracking for All Semi-Finished Products
RFID integration started in 2015 and took place in the production process of semi-finished products in order to streamline internal processes and to eliminate manual errors. In addition, the supply chain was to be optimized. Symington uses EPC Gen2v2 tags with the EPC Binary Coding Scheme SSCC-96 and EPCIS events for communication with SAP. The RFID tags are encoded inhouse. The chip has a 128-bit EPC and a 32-bit user memory. For cost reasons, the finished end products were not initially part of the RFID rollout.
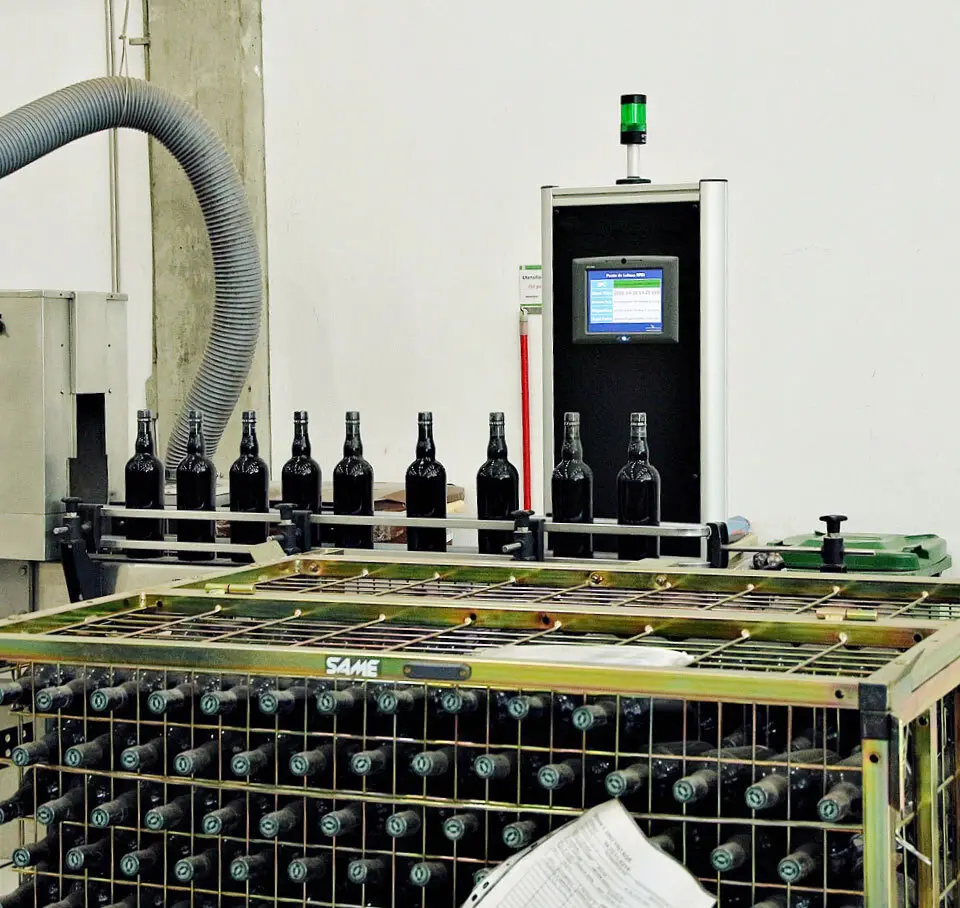
The semi-finished products are in a queue according to the “first in, first out” principle in the production line. RFID detection ensures traceability.
Load Carrier Tracked in Real Time
While the wine is being bottled, two labels with GS1-128 barcodes and RFID SSCC-96 are printed. These are attached to the metal load carrier, which holds around 600 bottles. Once the filling process is complete, the incoming goods are recorded in the ERP system. The RFID transponders guarantee the localization and tracking of the load carrier in real time. The load carrier is then transferred to the warehouse. An RFID reader is located at the entrance gate.
Each time a transponder passes the reader, the location, ID of the handling unit as Serial Shipping Container Code and time zone are forwarded to the ERP system according to the EPCIS standard. A total of three RFID readers are installed. Two at the final production lines and one reader at the entrance gate to the warehouse.
Final Production Process Takes Place After Several Years
The semi-finished product is stored on the load carrier for an extended period of time – in some cases several years – until it is returned to the production hall for the final finishing process. By law, certain products must be filled and stored at a specified time – even if the sale does not take place until years later. When the semi-finished product is taken to the final production lines for the final steps – labeling and packaging – readers on the production lines capture the RFID label. Thus, the entire internal process chain is controlled and monitored. The correct finishing of the product with the corresponding label is guaranteed.
Interview with António Marquez Filipe
Tradition and Innovation Combined
Regional solidarity, cooperation in research projects, goals in sustainability, "Mission 2025" – António Marquez Filipe provides insights into the corporate history and future vision of Symington Family Estates.
Interview
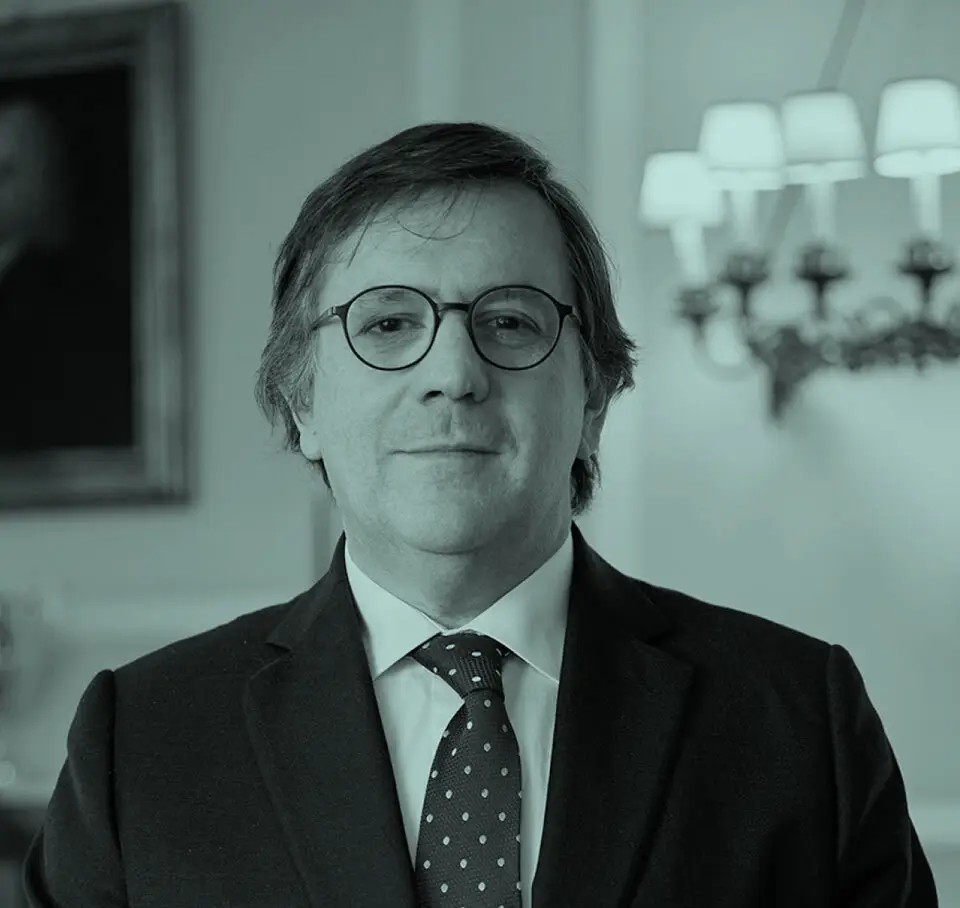
Antonio Marquez Filipe, Chief Operating Officer at Symington Family Estates, has been with the company for more than 30 years.
1. What's so special about Symington?
Symington is already being run by the 5th family generation. Founded in 1882, we are a traditional company that, on the one hand, places great value on its heritage and, on the other, looks to the future with the latest technology and innovations. Symington combines both of these aspects in harmony. We are particularly committed to the Douro region and to operating locally.
The Symington family has very strong ties to the region. Although they also have British roots, the passion for their home, the Douro region, is immense. They have strong ties to the region, which is something very special in my opinion. As such, Symington is involved in a number of local projects that support sustainability goals and the preservation of the region.
2. Which environmental projects are currently being actively supported?
We are involved in a whole range of environmental projects. We have recently launched a special edition of Altano wine, for example. Part of the proceeds from sales goes directly to "Rewilding Portugal" to create biotopes in Foz Côa in northern Portugal. In this reserve, wildlife can roam freely. We also maintain partnerships with three universities in Portugal – in Vila Real, in Porto and in Aveiro. As part of this partnership, we are involved in a biodiversity study which involves the population of black wheatear, the so-called "Port Wine Bird".
The study evaluates how we can maintain and also increase this population on our properties.
3. In 2001, the Douro region was recognized as a UNESCO World Heritage Site. Does this also have a direct influence on Symington?
The Douro region is the oldest demarcated wine region in the world. In total, the vineyards cover 45,726 hectares. Much of it is planted on steep, terraced land. We have personally rebuilt many of these terraces on our property. In total, 93 kilometers of handmade stone terraces stretch across our property.
A few years ago, a biologist pointed out to us that the stones were lined up too closely. The open, small spaces between the stones are typically inhabited by insects and snakes. We have accordingly changed our construction technique to ensure sufficient spaces in-between, thus promoting biodiversity.
4. What certifications does Symington already have today?
We are the leading organic wine producer in northern Portugal and we conduct research and development studies to expand the boundaries of organic viticulture. At Quinta do Ataíde, we are building the very first winery in Portugal to obtain a LEED (Leadership in Energy and Environmental Design) certification. We are also B Corporation certified.
The company's objective is therefore not only defined by financial profit, but is linked to the goal of adding value to society and solving social and environmental problems. Symington had already embodied many of these policies prior to certification.
Among them, consideration for the environment, local communities and employees.
5. What challenges do you face? Keyword: Labor Shortage.
The interior of Portugal in particular is characterized by migration towards large cities, low birth rates and a rising median population age. With regard to proportionality, Symington alone requires around 800 workers per year – the entire region 20,000. This is why we are working on a number of solution integrations.
6. What is the significance of robots and drones in vineyards?
We use robotics to increase the number and quality of data collection points in the vineyards. The data collected provides information on the influences of temperature, rain and irrigation. To prevent impacts and possible diseases, we have invested in satellite imagery, drones and robotics.
Vineyard irrigation management is remote and automated via sensor technology. We do not use irrigation to maximize yields, but simply to keep the vines alive. In the event of sudden changes in the climate, it is imperative to be able to react within a few hours – this is only possible with digital solutions.
7. How does the harvesting process take place?
We use two machines to harvest the grapes from the terraces. These machines have been specially designed by us so that only ripe grapes are picked.
Information about the degree of ripeness and position is possible to be transmitted to the machine. This technology is being developed but not fully implemented. For instance, we can leave out certain areas in advance. When the machine is next used, the data from the previous operation is already automatically processed and the start of the next unit is correctly configured.
8. What does "Mission 2025" entail?
For "Mission 2025", four cross-company working groups have been deployed to develop sustainability initiatives in the following areas: Viticulture & Biodiversity, Water, Energy & Buildings, Packaging & Waste, and Team & Community.
In total, we have defined 10 goals to be achieved by 2025 at the latest. All energy will then be derived from certified renewable energy sources, 20 percent of which we will generate ourselves. All passenger cars are to be electric or hybrid vehicles. For every liter of wine bottled, CO² emissions are to be reduced by 35 percent, water consumption by 10 percent and electricity consumption by 10 percent. Numerous ecosystems will be reforested.
The new winery will be awarded the Gold LEED certification as a sustainable building. 80 percent of employees shall be involved in volunteer programs. A new social and environmental impact fund is established. And last but not least, the goal of obtaining a B-Corp certification has already been achieved.
1. What's so special about Symington?
Symington is already being run by the 5th family generation. Founded in 1882, we are a traditional company that, on the one hand, places great value on its heritage and, on the other, looks to the future with the latest technology and innovations. Symington combines both of these aspects in harmony. We are particularly committed to the Douro region and to operating locally.
The Symington family has very strong ties to the region. Although they also have British roots, the passion for their home, the Douro region, is immense. They have strong ties to the region, which is something very special in my opinion. As such, Symington is involved in a number of local projects that support sustainability goals and the preservation of the region.
2. Which environmental projects are currently being actively supported?
We are involved in a whole range of environmental projects. We have recently launched a special edition of Altano wine, for example. Part of the proceeds from sales goes directly to "Rewilding Portugal" to create biotopes in Foz Côa in northern Portugal. In this reserve, wildlife can roam freely. We also maintain partnerships with three universities in Portugal – in Vila Real, in Porto and in Aveiro. As part of this partnership, we are involved in a biodiversity study which involves the population of black wheatear, the so-called "Port Wine Bird".
The study evaluates how we can maintain and also increase this population on our properties.
3. In 2001, the Douro region was recognized as a UNESCO World Heritage Site. Does this also have a direct influence on Symington?
The Douro region is the oldest demarcated wine region in the world. In total, the vineyards cover 45,726 hectares. Much of it is planted on steep, terraced land. We have personally rebuilt many of these terraces on our property. In total, 93 kilometers of handmade stone terraces stretch across our property.
A few years ago, a biologist pointed out to us that the stones were lined up too closely. The open, small spaces between the stones are typically inhabited by insects and snakes. We have accordingly changed our construction technique to ensure sufficient spaces in-between, thus promoting biodiversity.
4. What certifications does Symington already have today?
We are the leading organic wine producer in northern Portugal and we conduct research and development studies to expand the boundaries of organic viticulture. At Quinta do Ataíde, we are building the very first winery in Portugal to obtain a LEED (Leadership in Energy and Environmental Design) certification. We are also B Corporation certified.
The company's objective is therefore not only defined by financial profit, but is linked to the goal of adding value to society and solving social and environmental problems. Symington had already embodied many of these policies prior to certification.
Among them, consideration for the environment, local communities and employees.
5. What challenges do you face? Keyword: Labor Shortage.
The interior of Portugal in particular is characterized by migration towards large cities, low birth rates and a rising median population age. With regard to proportionality, Symington alone requires around 800 workers per year – the entire region 20,000. This is why we are working on a number of solution integrations.
6. What is the significance of robots and drones in vineyards?
We use robotics to increase the number and quality of data collection points in the vineyards. The data collected provides information on the influences of temperature, rain and irrigation. To prevent impacts and possible diseases, we have invested in satellite imagery, drones and robotics.
Vineyard irrigation management is remote and automated via sensor technology. We do not use irrigation to maximize yields, but simply to keep the vines alive. In the event of sudden changes in the climate, it is imperative to be able to react within a few hours – this is only possible with digital solutions.
7. How does the harvesting process take place?
We use two machines to harvest the grapes from the terraces. These machines have been specially designed by us so that only ripe grapes are picked.
Information about the degree of ripeness and position is possible to be transmitted to the machine. This technology is being developed but not fully implemented. For instance, we can leave out certain areas in advance. When the machine is next used, the data from the previous operation is already automatically processed and the start of the next unit is correctly configured.
8. What does "Mission 2025" entail?
For "Mission 2025", four cross-company working groups have been deployed to develop sustainability initiatives in the following areas: Viticulture & Biodiversity, Water, Energy & Buildings, Packaging & Waste, and Team & Community.
In total, we have defined 10 goals to be achieved by 2025 at the latest. All energy will then be derived from certified renewable energy sources, 20 percent of which we will generate ourselves. All passenger cars are to be electric or hybrid vehicles. For every liter of wine bottled, CO² emissions are to be reduced by 35 percent, water consumption by 10 percent and electricity consumption by 10 percent. Numerous ecosystems will be reforested.
The new winery will be awarded the Gold LEED certification as a sustainable building. 80 percent of employees shall be involved in volunteer programs. A new social and environmental impact fund is established. And last but not least, the goal of obtaining a B-Corp certification has already been achieved.
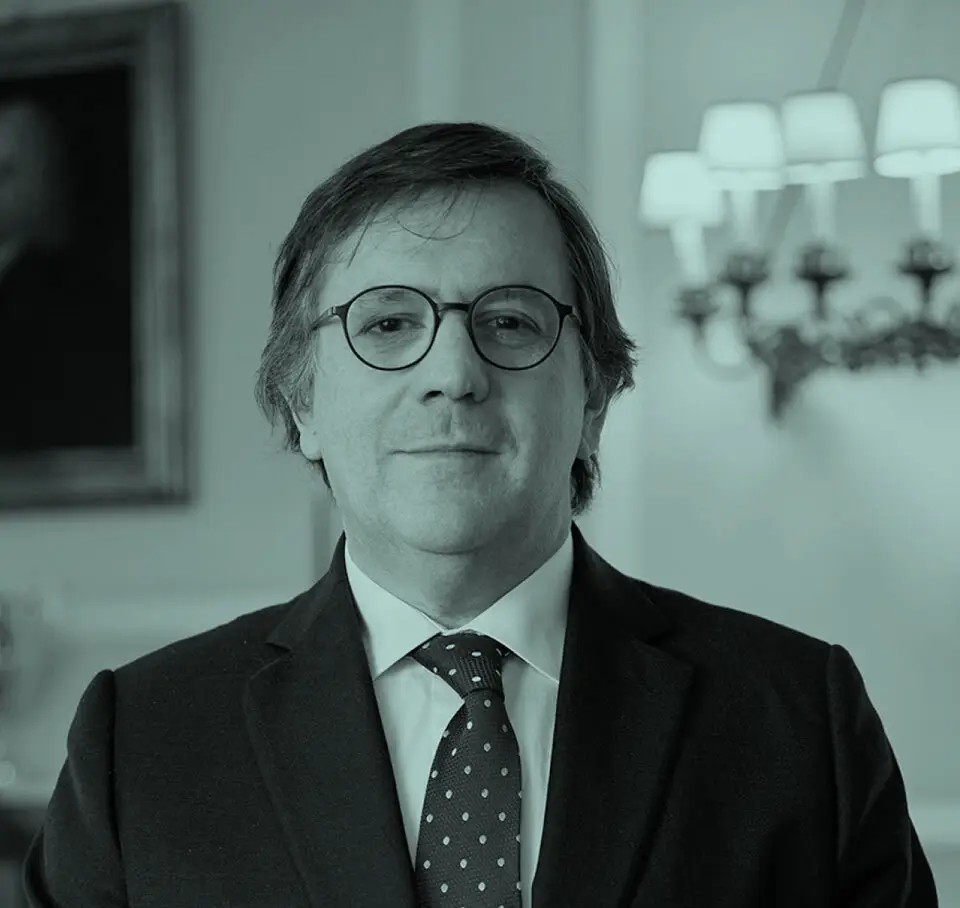
Antonio Marquez Filipe, Chief Operating Officer at Symington Family Estates, has been with the company for more than 30 years.
Localization with RFID
All Production Lines to be RFID-Enabled by 2021
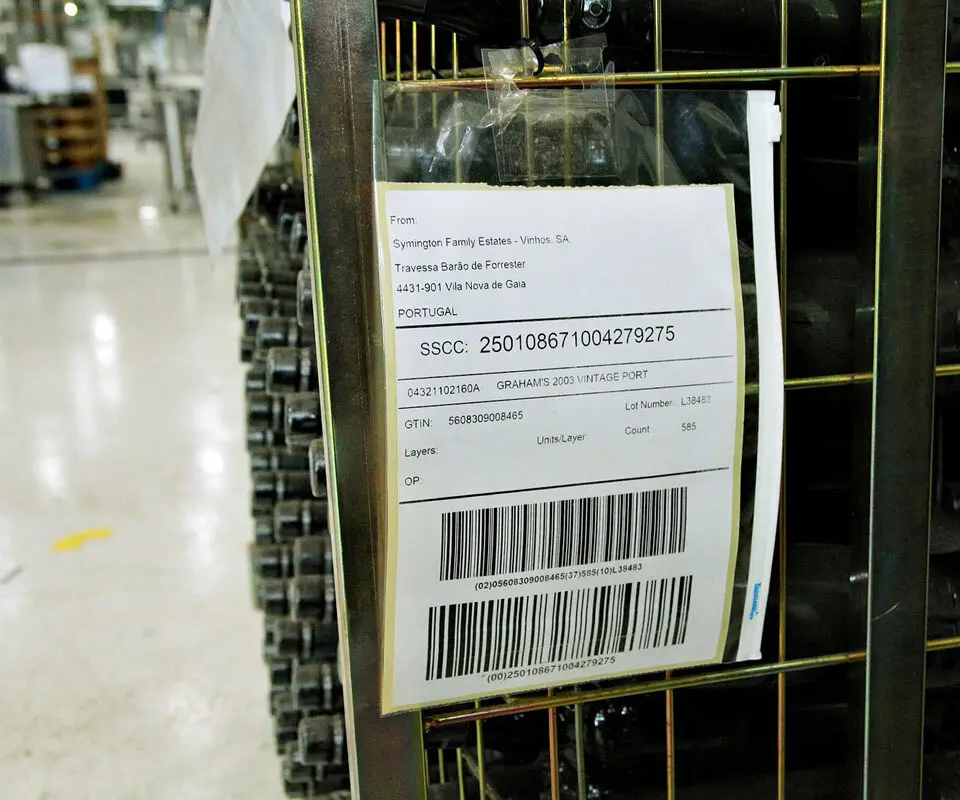
The RFID labels are printed and coded in-house. Two labels with GS1-128 barcodes and RFID SSCC-96 are applied per load carrier.
Around 5,000 RFID-tagged metal load carriers are in circulation at Symington every year. Manual errors are reduced and potential sources of error are located more quickly. Production line downtime and packaging errors
are reduced. Manual scanning by personnel is no longer required. Load carriers are managed efficiently and transparently as each load carrier can be precisely located. By the end of 2021, all remaining production lines in both production halls and the central warehouse will also be equipped with RFID technology.
Around 5,000 RFID-tagged metal load carriers are in circulation at Symington every year. Manual errors are reduced and potential sources of error are located more quickly. Production line downtime and packaging errors
are reduced. Manual scanning by personnel is no longer required. Load carriers are managed efficiently and transparently as each load carrier can be precisely located. By the end of 2021, all remaining production lines in both production halls and the central warehouse will also be equipped with RFID technology.
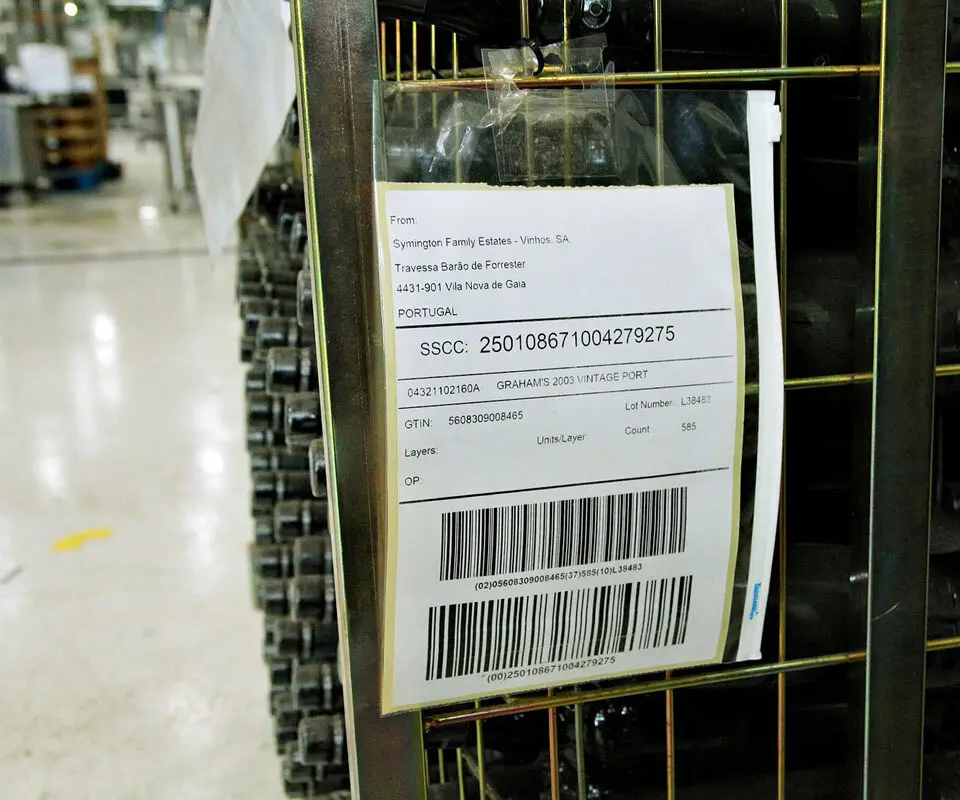
The RFID labels are printed and coded in-house. Two labels with GS1-128 barcodes and RFID SSCC-96 are applied per load carrier.
Containerpool with RFID

José Salazar, Analyst Developer, IT Department at Symington
José Salazar, Analyst Developer, IT Department, Symington, is responsible for the RFID integration of the logistic processes with the external suppliers. The transport of RFID-tagged containers, with delivered grapes, is ensured from the point of incoming goods to the production plant.
Each container is assigned to the correct wine production. The empty containers are then transferred from the production facility back to the warehouse. From there, the containers are transferred to the suppliers once again.
José Salazar, Analyst Developer, IT Department, Symington, is responsible for the RFID integration of the logistic processes with the external suppliers. The transport of RFID-tagged containers, with delivered grapes, is ensured from the point of incoming goods to the production plant.
Each container is assigned to the correct wine production. The empty containers are then transferred from the production facility back to the warehouse. From there, the containers are transferred to the suppliers once again.

José Salazar, Analyst Developer, IT Department at Symington
Supplier Identification
The EPC-GEn2v2 with GRAI-96 tag coding is used. The logistic processes with the suppliers – identification of the supplier, the number of delivered grapes, as well as the return of empty containers – are thereby controlled.
Interview with Isabel Freitas
Driving Technological Innovations Forward
Isabel Freitas is committed to the implementation of technological innovations. She is primarily responsible for RFID integration in logistics and explains what challenges had to be solved and what expectations were set for RFID integration, as well as what future technologies are in focus.
Interview
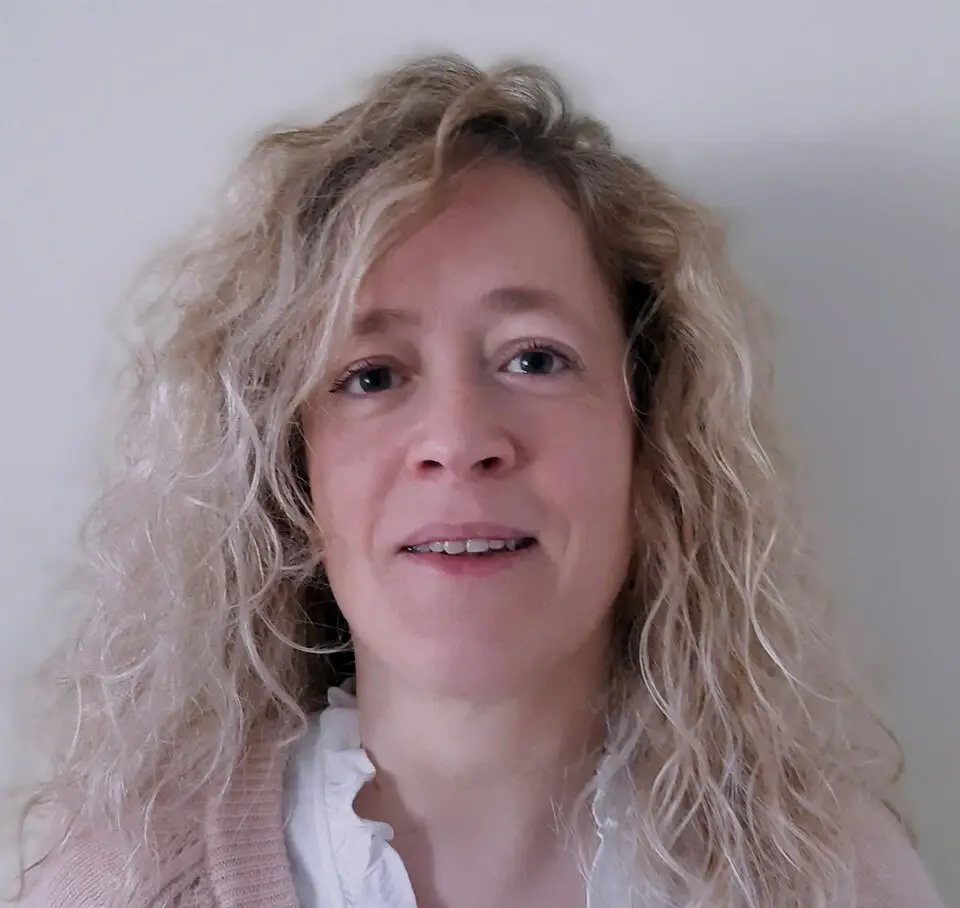
Isabel Freitas, Analyst Developer, Symington Family Estates, has been with the company since 1999.
1. What technological challenges does Symington face, particularly with regard to the product range and its product life cycle?
Due to the long service life of our products, we had to ask ourselves the question: Is the technology we are implementing now still innovative and applicable in the future? What will this technology look like perhaps 20 years from now when the wine is sold? If the technology no longer works properly at that time, the customer may have concerns about product authenticity. Therefore, future technology developments and possible technological degradation must be considered. Furthermore, we work with metal and liquids – neither of which are easy conditions for the integration of RFID technology.
2. Why did Symington specifically choose the Serial Shipping Container Code?
Initially, we evaluated whether to use GRAI (Global Returnable Asset Identifier) or SSCC (Serial Shipping Container Code) since the metal load carriers are owned by us and do not leave our internal production facilities. At that time, SSCC was much more prevalent within the supply chain. Therefore, we ultimately decided to go with the SSCC-96.
3. What expectations preceded the solution integration?
The overall goal was to stay ahead of future supply chain requirements. The dynamics within the supply chain are increasingly changing. An increasing number of companies are now investing in digital transformation and standardization in the supply chain. When we switched to RFID in 2015, we are also interested in reducing inventory time. The case study on our semi-finished products was not optimal, since environmental influences like metal and liquid, as well as the way our stock is stored, made RFID data capture difficult.
However, the environment surrounding our finished products is different and although reading is on the SSCC level, we still consider RFID tracking to be a good option in the near future.
4. Should the use of RFID be expanded in the future?
For cost reasons, we did not include the finished wine products in the first RFID integration phase. In the future, however, we want to integrate all products into the RFID solution. We are currently planning to expand the RFID integration to all production and logistics processes. This includes not only the production lines, but also the warehouses for semi-finished products, finished products and the warehouse for raw materials. The cost of RFID tags has dropped significantly since 2015. Therefore, RFID deployment is becoming increasingly cost-effective. We are currently evaluating the use of drones for inventory in the warehouse for example. Another motivating factor for our projects is that some of our suppliers are also starting to use RFID.
5. RFID is also used for the delivery of grapes from external winegrowers. How does this process work?
RFID deployment on the containers is used for three different processes involving the cooperation with external winegrowers. First, the pool circuit of the carriers between Symington and the growers is monitored. This means that we always know exactly where and how many load carriers are located. The return or delivery of empty RFID-tagged containers is also automatically captured.
The second RFID process involves the winegrowers and their delivery quantities. We automatically and contactlessly monitor the quantity of delivered grapes and assign this quantity to the respective winegrower.
The winegrower is identified via the RFID label on the container. In this way, we document how many containers and which quantities of grapes are to be assigned to a winegrower.
The third RFID-supported process does not concern the external winegrowers, but the internal logistics processes at Symington. This includes the transport of load carriers from the point of incoming goods to the production facility, as well as the allocation of load carriers to the correct wine production.
The transport of empty load carriers from the production plant to the receiving warehouse or from the receiving warehouse to production is also monitored contactlessly. Essentially, all logistics processes are captured digitally so that all container movements can be traced. For this, we use EPCGEn2v2 with the GRAI-96 tag coding.
6. What other solutions and technologies are currently being evaluated?
We are currently evaluating a variety of other automation solutions. For instance, we are testing the use of NFC for customer loyalty and interaction. A dual-frequency tag could be used in the future to realize both logistics automation and customer experience. How can we engage customers and strengthen brand loyalty in the future?
These are questions that Symington is currently addressing. The world is changing so rapidly, and the lifespan of some of our wines is far ahead of us. This is another challenge we have to deal with. With all the solutions and new technologies, we are looking at standardizing them so that we can take advantage of them in all segments of the supply chain. At the same time, this ensures compliance with the strict regulations of the beverage and food industry.
1. What technological challenges does Symington face, particularly with regard to the product range and its product life cycle?
Due to the long service life of our products, we had to ask ourselves the question: Is the technology we are implementing now still innovative and applicable in the future? What will this technology look like perhaps 20 years from now when the wine is sold? If the technology no longer works properly at that time, the customer may have concerns about product authenticity. Therefore, future technology developments and possible technological degradation must be considered. Furthermore, we work with metal and liquids – neither of which are easy conditions for the integration of RFID technology.
2. Why did Symington specifically choose the Serial Shipping Container Code?
Initially, we evaluated whether to use GRAI (Global Returnable Asset Identifier) or SSCC (Serial Shipping Container Code) since the metal load carriers are owned by us and do not leave our internal production facilities. At that time, SSCC was much more prevalent within the supply chain. Therefore, we ultimately decided to go with the SSCC-96.
3. What expectations preceded the solution integration?
The overall goal was to stay ahead of future supply chain requirements. The dynamics within the supply chain are increasingly changing. An increasing number of companies are now investing in digital transformation and standardization in the supply chain. When we switched to RFID in 2015, we are also interested in reducing inventory time. The case study on our semi-finished products was not optimal, since environmental influences like metal and liquid, as well as the way our stock is stored, made RFID data capture difficult.
However, the environment surrounding our finished products is different and although reading is on the SSCC level, we still consider RFID tracking to be a good option in the near future.
4. Should the use of RFID be expanded in the future?
For cost reasons, we did not include the finished wine products in the first RFID integration phase. In the future, however, we want to integrate all products into the RFID solution. We are currently planning to expand the RFID integration to all production and logistics processes. This includes not only the production lines, but also the warehouses for semi-finished products, finished products and the warehouse for raw materials. The cost of RFID tags has dropped significantly since 2015. Therefore, RFID deployment is becoming increasingly cost-effective. We are currently evaluating the use of drones for inventory in the warehouse for example. Another motivating factor for our projects is that some of our suppliers are also starting to use RFID.
5. RFID is also used for the delivery of grapes from external winegrowers. How does this process work?
RFID deployment on the containers is used for three different processes involving the cooperation with external winegrowers. First, the pool circuit of the carriers between Symington and the growers is monitored. This means that we always know exactly where and how many load carriers are located. The return or delivery of empty RFID-tagged containers is also automatically captured.
The second RFID process involves the winegrowers and their delivery quantities. We automatically and contactlessly monitor the quantity of delivered grapes and assign this quantity to the respective winegrower.
The winegrower is identified via the RFID label on the container. In this way, we document how many containers and which quantities of grapes are to be assigned to a winegrower.
The third RFID-supported process does not concern the external winegrowers, but the internal logistics processes at Symington. This includes the transport of load carriers from the point of incoming goods to the production facility, as well as the allocation of load carriers to the correct wine production.
The transport of empty load carriers from the production plant to the receiving warehouse or from the receiving warehouse to production is also monitored contactlessly. Essentially, all logistics processes are captured digitally so that all container movements can be traced. For this, we use EPCGEn2v2 with the GRAI-96 tag coding.
6. What other solutions and technologies are currently being evaluated?
We are currently evaluating a variety of other automation solutions. For instance, we are testing the use of NFC for customer loyalty and interaction. A dual-frequency tag could be used in the future to realize both logistics automation and customer experience. How can we engage customers and strengthen brand loyalty in the future?
These are questions that Symington is currently addressing. The world is changing so rapidly, and the lifespan of some of our wines is far ahead of us. This is another challenge we have to deal with. With all the solutions and new technologies, we are looking at standardizing them so that we can take advantage of them in all segments of the supply chain. At the same time, this ensures compliance with the strict regulations of the beverage and food industry.
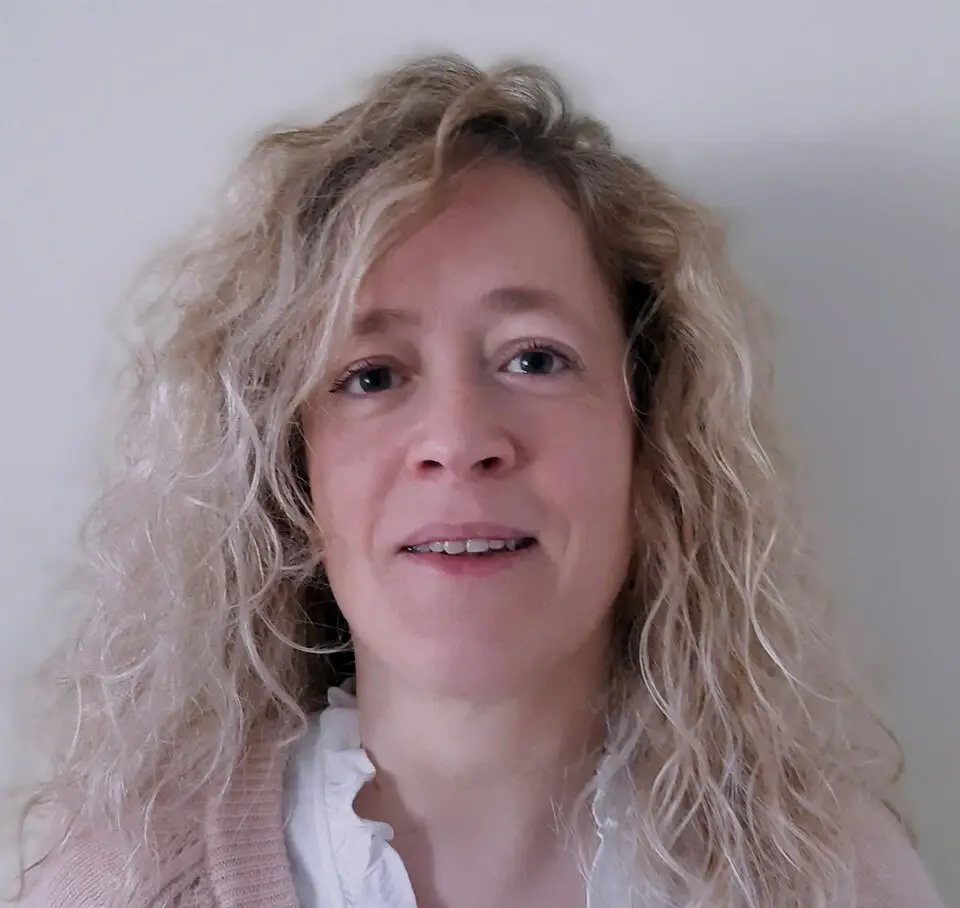
Isabel Freitas, Analyst Developer, Symington Family Estates, has been with the company since 1999.