Machines on More Than 1000 Construction Sites
Partner Consortium Networks Millions of GPS Data
Bouygues Construction Matériel, a subsidiary of the Bouygues Construction Group, has contracted Omniscient, a startup founded by Bouygues SA, at the end of 2019 to network 20,000 devices for remote real-time management.
The IT expertise and IoT platform are provided by Omniscient. Bouygues Telecom is responsible for connectivity. Abeeway, a subsidiary of the French company Actility, supplies the LoRaWAN sensors. Bouygues Construction Matériel is responsible for managing all of the group's machines and equipment. This includes ensuring that each construction site is equipped with functioning machinery and equipment in a timely manner.
Every day, tens of thousands of pieces of equipment are serviced and distributed to all of the construction sites in France. To this end, Omniscient has developed a solution for Bouygues Construction Matériel based on multi-technology trackers from Abeeway, a specialist in ultra- low power geolocation solutions. The IT know-how and the IoT platform come from Omniscient. Bouygues Telecom is responsible for connectivity. Objective: To optimize site operations for data collection and analysis.
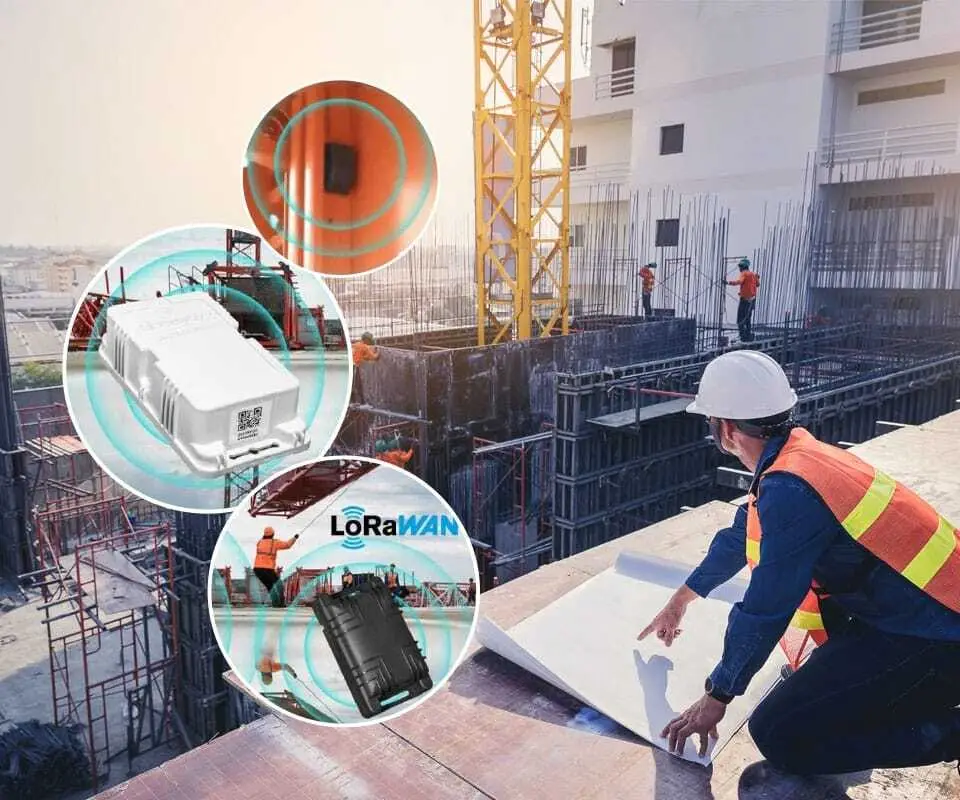
The large-scale project involves approximately one hundred employees who monitor the devices at more than one thousand construction sites, spread over five technical locations. This corresponds to the installation of sensors on more than 20,000 devices and millions of GPS data.
Management of Equipment Worth One Million Euros
French construction giant Bouygues Construction Group expects to achieve annual savings of five to 10 percent in fleet management and maintenance by introducing sensor-based equipment networking. ROI is expected to be achieved in three years.
Savings Potential of the LoRaWAN Solution:
- Simplified Invoicing: All information related to equipment input/output or utilization rate is captured on all job sites, making invoicing faster and easier.
- Efficient Use of Resources: Unused equipment on construction sites is identified and can be mobilized to avoid external rentals.
- Equipment Lifecycle: Devices reaching the end of their life cycle are prioritized to avoid upgrade costs and to ensure regular maintenance of the devices for a longer lifespan.
- Reduced Inventory Costs: An optimal overview of the total inventory enables the minimization of stock per depot.
- Real-Time Management: Decisions are made quickly, information is immediately available and up-to-date, freeing up operating time for value-adding tasks.
LoRaWAN in the Construction Industry
Requirements for Transparency, Robustness, and Durability Covered by One Technology
The implementation of construction projects requires large quantities of electricity, water and building materials as well as a large number of employees. The lack of clarity on (large) construction sites makes it difficult to monitor and protect equipment and machinery against theft.
How can requirements for transparency, robustness and durability be covered by one technology? The ranges of passive technologies, for example RFID, are too short. GPS does not penetrate the entire interior space. Mobile phone applications generate network usage costs and offer additional services that are not required, including large bandwidths and high data transmission speeds.
One technology that addresses all requirements without driving up infrastructure costs is LoRaWAN. This low-power wide-area network offers an open, global, interoperable standard. The investment in hardware infrastructure is low compared to other wireless technologies. The sensors ensure battery runtimes of over ten years, depending on the frequency of information retrieval. For construction site applications, low latencies combined with large data packets play a secondary role.
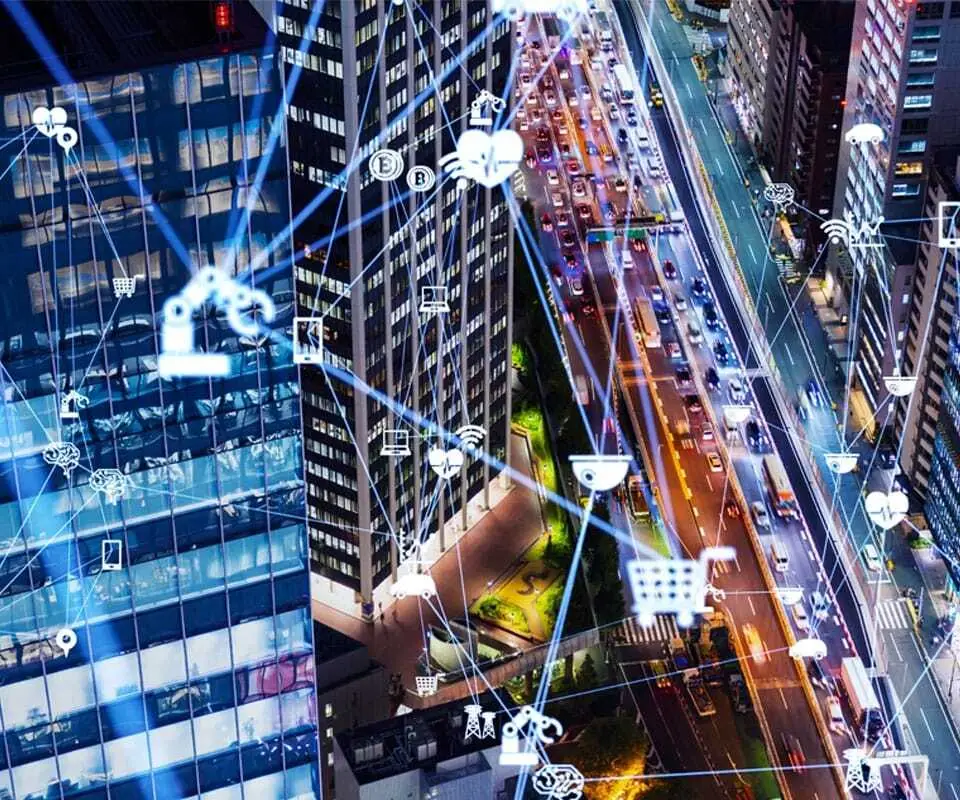
Tracking, localization or sensor data capture can be exchanged over long distances via LoRaWAN.
LoRaWAN-Based Application Examples on the Construction Site
- Geolocation and tracking of equipment, construction materials/load carriers and personnel
- Optimized utilization and condition monitoring of construction vehicles and machines
- Predictive maintenance plans based on captured data such as mileage, engine hours, energy consumption and idle time
- Acquisition of measurement data such as temperatures, humidity or vibration from the construction
- Collision avoidance and detection of construction vehicles
- Indoor and outdoor air pollution and quality monitoring
- Monitoring of safety zones for equipment and workers (geofencing)
- Capture of energy and water consumption
Why LoRaWAN on the Construction Site?
LoRaWAN operates in unlicensed frequency bands that can be used free of charge. Communication takes place in regionally different frequency ranges in the ISM and SRD bands – in Europe, for example, in the ranges 433.05 to 434.79 and 863 to 870 MHz.
The technology combines the features of cellular and Wi-Fi connectivity – long range, secure communications and high indoor performance – with long battery life for the end devices. LoRaWAN offers the construction industry the possibility to integrate different tracking, localization or sensor data collection solutions.
Interview with Nicolas Lemaire and Stephane Sisse
Networking Construction Site Equipment with LoRaWAN
Savings potential, analysis functions, further implementation possibilities – Nicolas Lemaire and Stephane Sisse provide insights into the LoRAWAN project at Bouygues Construction Matériel.
Nicolas Lemaire has been in the telecommunications industry for 15 years and is the CEO of Omniscient, a operations monitoring platform dedicated to the construction industry.
Stephane Sisse is a graduate with an engineering degree in mathematics and an MBA from a business school and currently serves as Sales Director at Actility.
Interview
1. What is the objective of Bouygues Construction Matériel with the integration of LoRaWAN sensors?
Lemaire: A large number of employees and devices or machines are involved in the implementation of construction projects. Large amounts of electricity, water and construction materials are consumed and the complexity of construction sites makes it difficult to monitor the condition and location of machines. Bouygues Construction Matériel wanted to develop a solution that would bring transparency to all logistical operations, protect equipment from theft, and also facilitate maintenance.
2. When did the technology consortium start the LoRaWAN project?
Lemaire: Initial discussions with all three partners began in 2019, followed by the proof of concept. The project then officially started in June 2020. The launch followed at the beginning of 2021. Around 3,000 sensors are currently already installed and a total of 10,000 sensors are to be integrated by the end of 2021.
3. What advantages does the solution generate and what potential savings do you see?
Sisse: The solution brings significant operational and financial benefits. Overall, around 5 to 10 percent in maintenance costs are saved annually. First, the invoicing process is greatly simplified as all information – equipment input and output, as well as rates of utilization – is captured across all construction sites. Resources are identified more efficiently, since unused construction site equipment can immediately be ready for use.
Lemaire: Furthermore, the operating time and maintenance intervals of the devices and machines are precisely documented. This results in the targeted use of all machinery.
Once the 1st phase of the 20,000 connected equipments is finalized, there will be about 70 connected devices per construction site on average. It can go up to 300 for large project.
The next challenge will be to connect the next 50,000 smaller devices. A device can last up to 10 years. We are targeting a minimum 5 year battery life for the device, so we only have to change the battery once. The efficient and exact overview of the total inventory minimizes the stock in the depot and thus also reduces inventory costs. Real-time management ensures fast decision-making processes. All information is up-to-date and immediately available. The work of the personnel involved is thus streamlined and valuable working time is freed up for other tasks.
Sisse: Based on analysis and monitoring, a real-time inventory of all equipment – whether it is being used onsite or is still in storage at one of the sites – is possible. This is a small revolution for operational teams. By networking construction sites and providing on-site visibility, the performance of the entire sector is significantly optimized.
4. How is the solution designed?
Sisse: The solution can be used both indoors and outdoors. The sensors used last for several years. This means that the investment pays off in the long term. The multimodal concept allows easy adaptation and configuration for a wide range of use cases. Integrating devices in isolated and sometimes challenging environments is also guaranteed by the wide range of technologies. For example, LoRaWAN technology offers the advantage of energy autonomy over several years. At the same time, bidirectional communication and high penetration capability in buildings as well as in basements is realized.
5. What product features and performance do the multi-technology trackers have?
Sisse: The multi-technology trackers are based on ultra- low power consumption and are extremely versatile. The tracker is equipped with embedded sensors – GPS, low-power GPS, Wi-Fi sniffer, BLE and LoRaWAN TDoA geolocation technology. The device offers multiple modes of operation and enables seamless object tracking, activity rate monitoring and proximity detection. Geo-zone detection allows the device to be divided into specific zones. Position reports can be received during the start and end events of a movement. The compact and rugged form factor can withstand the harsh environmental conditions of a construction site.
6. The IoT platform is a fundamental pillar of the project. Please describe the features of this platform.
Lemaire: The developers of the IoT platform, employees of Omniscient, have years of expertise in the construction industry. The main goal of the platform: To map the entire ecosystem of a construction site. This impacts overall productivity. This includes digital fleet management – small equipment operated manually as well as cranes weighing tons. With just one click, workers can navigate a virtual map.
The location of each piece of equipment is visualized in real time. The real-time collection of geolocation and activity data from engines allow us to monitor construction processes in real-time. The Omniscient platform provides a ready to use dashboard for project managers that give them real-time insights on their project, help them identify bottlenecks in the process and make the right decision to ensure their projets stay on schedule. It can also be used to control equipment configurations on-site.
Sisse: However, the most important key feature and innovation of the solution is its tremendous adaptability. This is because the combination of different geolocation technologies allows GPS to be used in an open environment and Wi-Fi sniffing to be used between buildings. BLE is used to scan the environment and to detect other small devices that are also tagged with BLE.
7. You explained the functions of the IoT platform in an interesting way. Can you explain the analysis functions?
Lemaire: The algorithms developed in-house enable and simplify numerous analysis functions. For example, the data collected by the sensors is used to accurately calculate and evaluate performance indicators for fleet management. These include the number of turnarounds, equipment utilization, inventory by technical basis, and inventory by location and by number of billable days.
8. Lastly, a question about your future visions: What other prospects and implementation possibilities do you see for wireless IoT technologies in the construction industry?
Lemaire: The cooperation between our three companies offers further potential. There is a wide range of possibilities for additional solutions that can increase efficiency. These include measuring machine productivity, optimizing transport routes, and increasing the safety of personnel. Let's take the example of occupational safety. Installed sensors can zone specific areas and monitor them in real time. Thus, personnel can be warned via the back-end system if they are about to enter restricted areas or if the occupancy rate of personnel in that area is too high. The latter concept is particularly essential for social distancing measures and is currently all the more in demand. The configurable warnings offer additional options for action and safety measures for personnel deployment on construction sites.