Interview with Ramin Hassan
1. Why is the interaction between label, hardware and system so important for successfully controlled process automation?
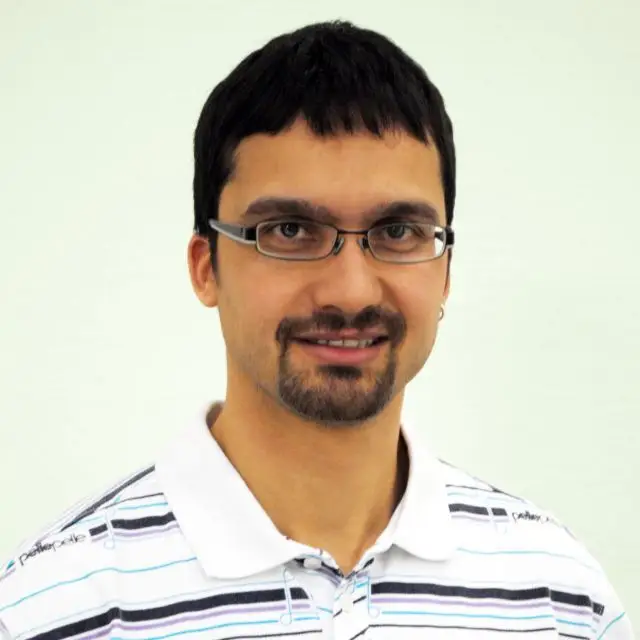
As Managing Director of GERA-IDENT, Ramin Hassan has been responsible for the strategic and operational management of the company since its inception in 2005. His core responsibilities include developing and implementing corporate strategies, driving innovation in passive HF and UHF RFID technology, and ensuring efficient operations. In addition, he is responsible for maintaining and developing partnerships with customers and business partners to develop customized and practical solutions.
Ramin Hassan: The interaction between the label, the hardware and the system is essential to ensure smooth and efficient process automation. Labels must be precisely matched to the products they are intended to identify and be able to run through the entire process chain without interference.
The hardware must be designed to read these labels accurately. At the same time, it must be optimally integrated into the system to provide the required data at the relevant process steps.
As each production process consists of different steps, the customer expects certain information or data links at certain stages, e.g. booking into an assembly step or confirming an inspection. The hardware must therefore not only be robust and precise, but must also be able to cope with the environmental conditions and the number and arrangement of the tags. Only when all elements are optimally coordinated can the complex requirements of modern process automation be met.
Particularly in high-volume applications, such as packaging, where many tags need to be read at the same time, precise alignment of the hardware with the environment and all other requirements is essential. But there are also possibilities with the labels.
In addition to the choice of chip, antenna and material, the form in which the labels are supplied is also crucial to the application method, e.g. whether and how defective labels are removed in the production process.
Ramin Hassan: The interaction between the label, the hardware and the system is essential to ensure smooth and efficient process automation. Labels must be precisely matched to the products they are intended to identify and be able to run through the entire process chain without interference.
The hardware must be designed to read these labels accurately. At the same time, it must be optimally integrated into the system to provide the required data at the relevant process steps.
As each production process consists of different steps, the customer expects certain information or data links at certain stages, e.g. booking into an assembly step or confirming an inspection. The hardware must therefore not only be robust and precise, but must also be able to cope with the environmental conditions and the number and arrangement of the tags. Only when all elements are optimally coordinated can the complex requirements of modern process automation be met.
Particularly in high-volume applications, such as packaging, where many tags need to be read at the same time, precise alignment of the hardware with the environment and all other requirements is essential. But there are also possibilities with the labels.
In addition to the choice of chip, antenna and material, the form in which the labels are supplied is also crucial to the application method, e.g. whether and how defective labels are removed in the production process.
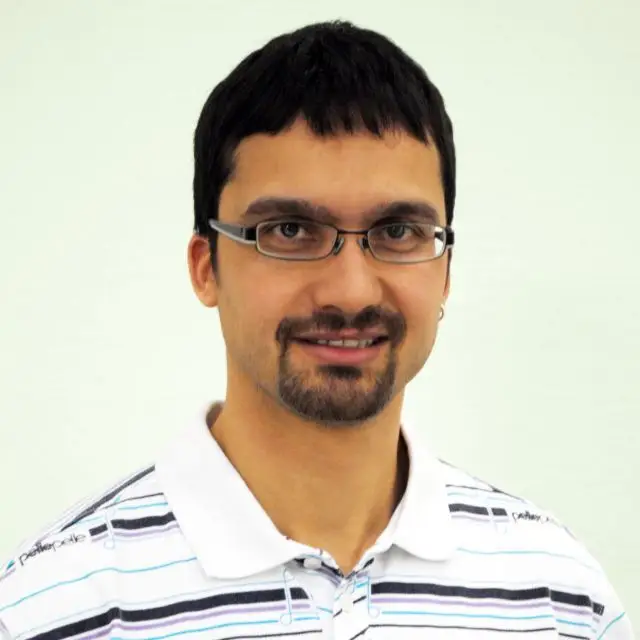
As Managing Director of GERA-IDENT, Ramin Hassan has been responsible for the strategic and operational management of the company since its inception in 2005. His core responsibilities include developing and implementing corporate strategies, driving innovation in passive HF and UHF RFID technology, and ensuring efficient operations. In addition, he is responsible for maintaining and developing partnerships with customers and business partners to develop customized and practical solutions.
2. What do you mean by "the right information in the right place" in the context of RFID systems and process automation?
Ramin Hassan: The use of RFID is not an end in itself, but rather a way to collect and transmit data. Companies should ask themselves what information they need at what time and at what point in the process to best manage their operations.
It's not just about collecting data, it's about extracting specific information from components and using it to make fast, automated decisions.
Once these requirements are clear, the necessary reading points can be determined. This determines the choice of the right tags, the appropriate hardware and the design of the entire RFID system. A classic example is a painting robot that uses the appropriate hardware to read the RFID tag of a window component hanging from the cross beam, and then independently selects and processes its component-specific painting pattern.
So the key question is: What does the company want to know internally and where in the automated process, and what information may need to be provided externally, for example in supply chain applications or for the digital product passport?
3. How do you identify and remove faulty labels in the production process and ensure that the entire process, including hardware and label production, meets customer requirements?
GERA-IDENT
- Manufacturer of customized RFID labels, tags, readers and antennas
- Founded in December 2005 in Gera (Thuringia, Germany)
- Technologies: passive HF, UHF, dual-frequency
- Customers: companies worldwide
Ramin Hassan: In our production processes, some of which are multi-stage, defective labels are detected and removed using various inspection methods.
This includes basic machine production with a product inspection that goes beyond a simple go-no-go check to detect defective labels at an early stage and remove them from the production process. In later production steps, if additional process-specific tests are required, any additionally detected defective labels can be sorted out again.
During the finishing process, e.g. during programming or printing of the labels, care is also taken to ensure that defective labels are detected and removed.
These inspection and removal processes are always performed in accordance with specific customer requirements to ensure high quality and precision throughout the manufacturing process.
Ramin Hassan: In our production processes, some of which are multi-stage, defective labels are detected and removed using various inspection methods.
This includes basic machine production with a product inspection that goes beyond a simple go-no-go check to detect defective labels at an early stage and remove them from the production process. In later production steps, if additional process-specific tests are required, any additionally detected defective labels can be sorted out again.
During the finishing process, e.g. during programming or printing of the labels, care is also taken to ensure that defective labels are detected and removed.
These inspection and removal processes are always performed in accordance with specific customer requirements to ensure high quality and precision throughout the manufacturing process.
GERA-IDENT
- Manufacturer of customized RFID labels, tags, readers and antennas
- Founded in December 2005 in Gera (Thuringia, Germany)
- Technologies: passive HF, UHF, dual-frequency
- Customers: companies worldwide
4. Keyword: Entry into the process chain. Why is the decision of which step and how labels are integrated into the process chain central to the success of the entire process?
Ramin Hassan: A process chain consists of different process steps or sub-steps. The decision of which step and how labels are integrated into the process chain is critical because it significantly affects the economic benefit of labeling.
The earlier the label is applied, the longer the label can be used in the process chain to generate data, gain insights, or optimize processes. At the same time, it is important to determine when labeling makes physical sense.
If labeling is done too late, for example on packaging, important information is lost in the internal process chain. Earlier labeling is therefore desirable. However, it must be done in a way that allows both labeling and subsequent use. For example, applying a label to a plastic part that is then packaged in a metal housing would negatively impact the usability of the RFID label.
Optimal integration therefore requires a customer-specific analysis that takes into account factors such as assemblies, process steps and environment, as well as the technology requirements for HF or UHF RFID.
5. What practical examples can you give us of processes that have been successfully harmonized?
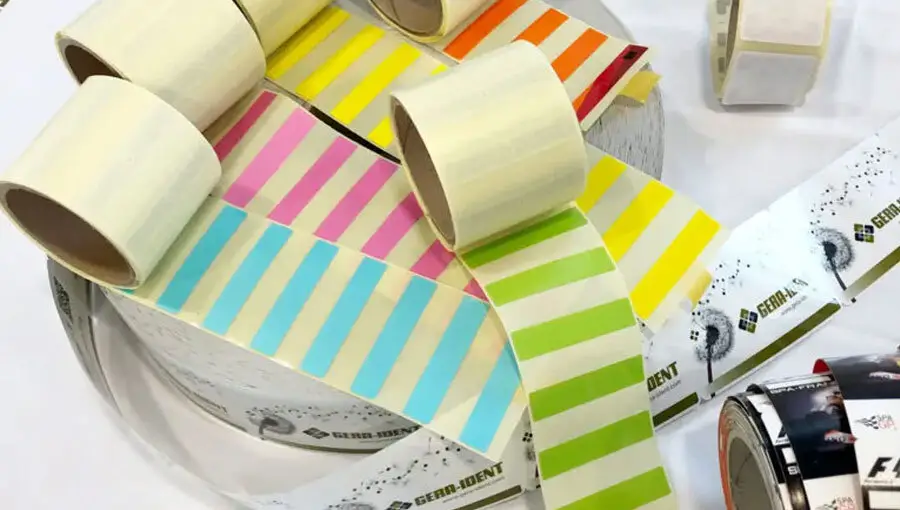
Gera-Ident offers RFID solutions in different frequencies and frequency combinations (HF/NFC, UHF/RAIN). The chips and antennas are adapted to different surfaces such as plastic, wood, metal or ESD materials and to specific operating conditions. Customized solutions such as printed or programmed RFID labels are also available.
Ramin Hassan: Over the years, we have implemented a wide range of solutions for applying labels and tags. I can give you many examples.
One example is an OEM in the automotive industry that receives pre-cut, individual hang tags and applies them using a robot with a suction device. This process is fully automated and customized for their system.
A customer in the plastics industry, on the other hand, receives completely blank labels on a roll and applies them manually because they have enough time in their process step. He uses tabletop printers and sometimes add-ons such as a peel bar or liner winder.
In another example, a customer in the same industry with very similar processes has developed its own applicator with standard components that automatically applies the packaging, but it is not a fully automated application.
In another application, labels are automatically applied with the printed side to a glass surface, similar to windshield labels. We supply these printed and programmed on a roll. However, no additional checks are made in the application system.
Therefore, the customer is completely confident that the labels we deliver are 100 percent correct. This is because the first registration in the process takes place after several assembly steps, and the product can only be rejected at a late stage. In this case, every faulty label means a faulty product.
Other customers receive pre-programmed labels that they then print and program themselves, with special requirements for the delivery form, such as single, on a roll - sometimes with perforation - or as a leporello.
In all of these cases, we also help our customers with hardware selection and integration, as well as implementation, commissioning, and ramp-up.
Ramin Hassan: Over the years, we have implemented a wide range of solutions for applying labels and tags. I can give you many examples.
One example is an OEM in the automotive industry that receives pre-cut, individual hang tags and applies them using a robot with a suction device. This process is fully automated and customized for their system.
A customer in the plastics industry, on the other hand, receives completely blank labels on a roll and applies them manually because they have enough time in their process step. He uses tabletop printers and sometimes add-ons such as a peel bar or liner winder.
In another example, a customer in the same industry with very similar processes has developed its own applicator with standard components that automatically applies the packaging, but it is not a fully automated application.
In another application, labels are automatically applied with the printed side to a glass surface, similar to windshield labels. We supply these printed and programmed on a roll. However, no additional checks are made in the application system.
Therefore, the customer is completely confident that the labels we deliver are 100 percent correct. This is because the first registration in the process takes place after several assembly steps, and the product can only be rejected at a late stage. In this case, every faulty label means a faulty product.
Other customers receive pre-programmed labels that they then print and program themselves, with special requirements for the delivery form, such as single, on a roll - sometimes with perforation - or as a leporello.
In all of these cases, we also help our customers with hardware selection and integration, as well as implementation, commissioning, and ramp-up.
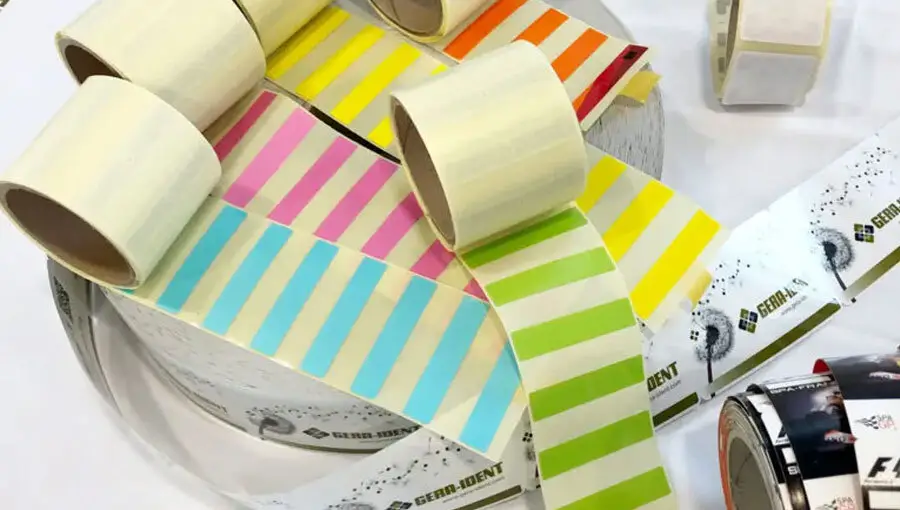
Gera-Ident offers RFID solutions in different frequencies and frequency combinations (HF/NFC, UHF/RAIN). The chips and antennas are adapted to different surfaces such as plastic, wood, metal or ESD materials and to specific operating conditions. Customized solutions such as printed or programmed RFID labels are also available.