Swiss Tropical Wood
Swiss Wood Solutions
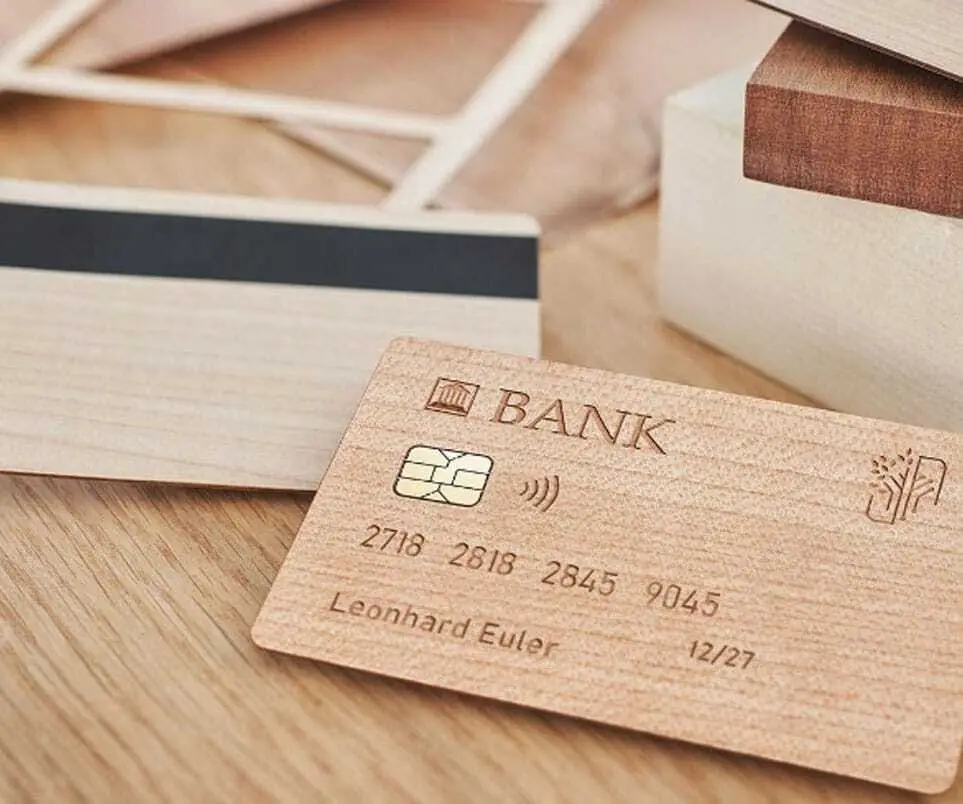
Copecto's leading product is the Timbercard, the world's first plastic-free wooden chip card for the payment and non-payment sector.
Swiss Wood Solutions (SWS) is a spin-off of the Swiss Federal Institute of Technology in Zurich (ETH) and the Swiss Federal Laboratories for Materials Testing and Research (EMPA) and functions as an R&D small and medium-sized enterprise (SME) in the field of innovative wood-based materials. What was initiated in response to the challenge of the procurement of high-quality tropical wood for musical instruments led, among other things, to the the conversion of thin maple veneers into functional girocards and credit cards.
The company aims to offer and customize different types of wood such as maple, oak, and cherry, to ensure the required strength and elasticity for a useful service life of four years. The production of Swiss wood, which has similar properties to tropical wood, is made possible by a special wood press installed at SWS's headquarters in Altdorf/Uri. This innovation, made from local spruce or maple, is characterized by its closed pore structure and is experiencing increasing demand due to its ecological advantages.
Swiss Wood Solutions (SWS) is a spin-off of the Swiss Federal Institute of Technology in Zurich (ETH) and the Swiss Federal Laboratories for Materials Testing and Research (EMPA) and functions as an R&D small and medium-sized enterprise (SME) in the field of innovative wood-based materials. What was initiated in response to the challenge of the procurement of high-quality tropical wood for musical instruments led, among other things, to the the conversion of thin maple veneers into functional girocards and credit cards.
The company aims to offer and customize different types of wood such as maple, oak, and cherry, to ensure the required strength and elasticity for a useful service life of four years. The production of Swiss wood, which has similar properties to tropical wood, is made possible by a special wood press installed at SWS's headquarters in Altdorf/Uri. This innovation, made from local spruce or maple, is characterized by its closed pore structure and is experiencing increasing demand due to its ecological advantages.
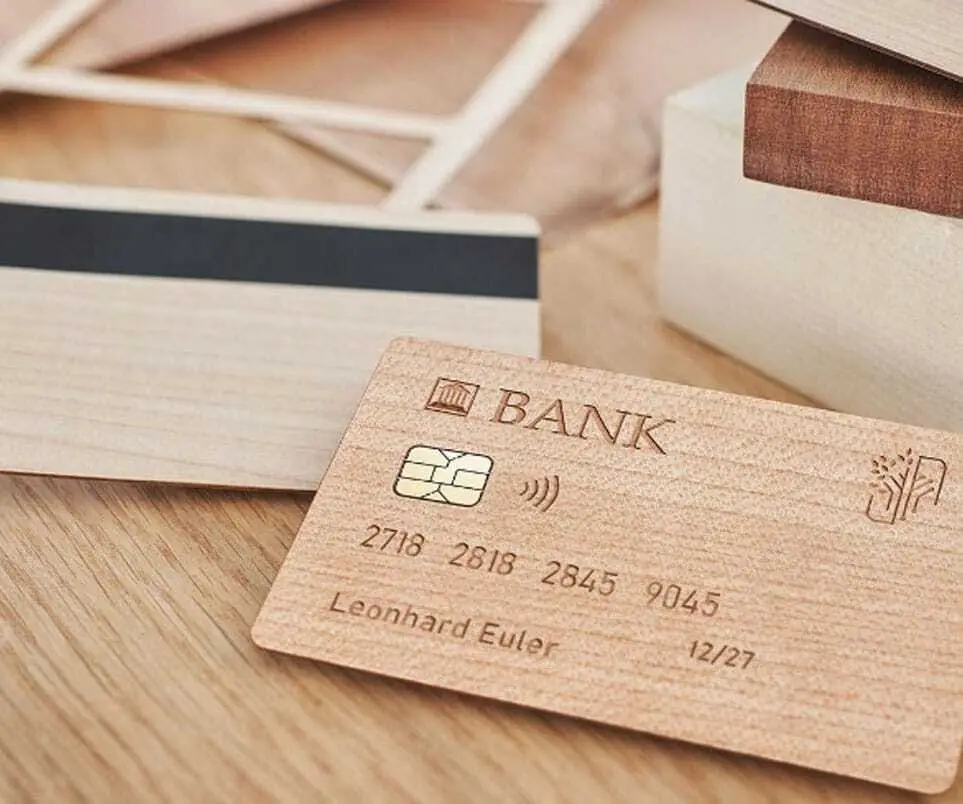
Copecto's leading product is the Timbercard, the world's first plastic-free wooden chip card for the payment and non-payment sector.
Copecto
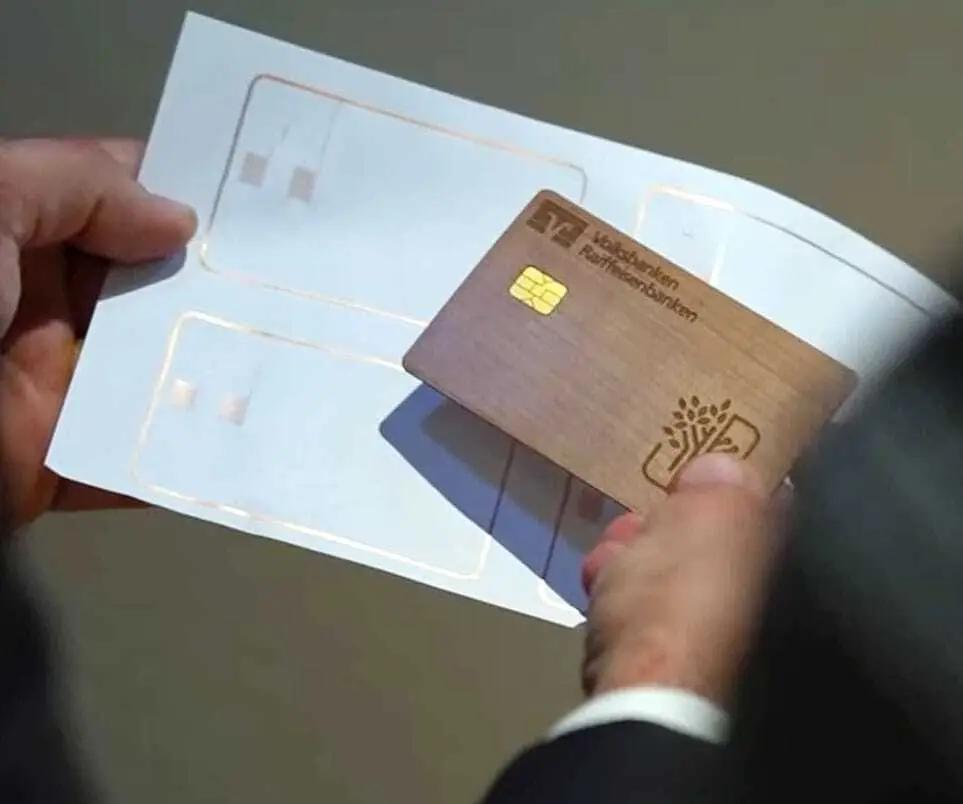
The electronics already work. Apart from the magnetic strip, the chip and the antenna are the only components that are not compostable.
Copecto, founded on May 31st, 2023 and headquartered in Wiesbaden, Germany, is a subsidiary of DG Nexolution. In cooperation with Swiss Wood Solutions, Copecto holds exclusive and worldwide licenses for the distribution and production of Timbercard. The first sub-license for the mass production of the wooden cards has already been granted to Raiffeisendruckerei. The company's leading product is the Timbercard, the world's first plastic-free wooden card for the payment and non-payment sector.
Copecto is responsible for global sales, marketing and organizing the production of the wooden cards. In line with Copecto's corporate philosophy – “Do Good Use Wood” – the company's vision is to have at least one Timbercard in every wallet worldwide.
The goal: to revolutionize the card industry.
Copecto, founded on May 31st, 2023 and headquartered in Wiesbaden, Germany, is a subsidiary of DG Nexolution. In cooperation with Swiss Wood Solutions, Copecto holds exclusive and worldwide licenses for the distribution and production of Timbercard. The first sub-license for the mass production of the wooden cards has already been granted to Raiffeisendruckerei. The company's leading product is the Timbercard, the world's first plastic-free wooden card for the payment and non-payment sector.
Copecto is responsible for global sales, marketing and organizing the production of the wooden cards. In line with Copecto's corporate philosophy – “Do Good Use Wood” – the company's vision is to have at least one Timbercard in every wallet worldwide.
The goal: to revolutionize the card industry.
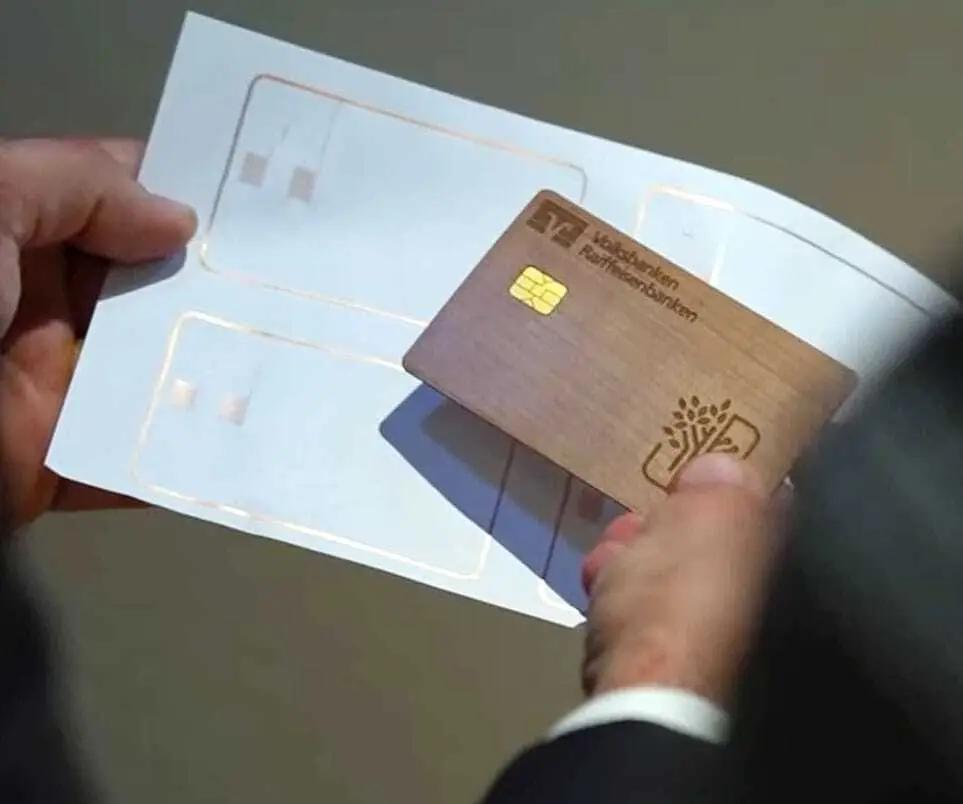
The electronics already work. Apart from the magnetic strip, the chip and the antenna are the only components that are not compostable.
"Our wooden card has all the technical features of conventional cards, including antenna, chip, magnetic stripe, and contact and contactless functionality. It is designed for a service life of at least four years, and has successfully passed extensive certification tests in accordance with the international requirements of global payment transactions. The Timbercard is therefore not only a symbol for more sustainable payment transactions, but also a unique ambassador for nature in your wallet. We are certain that the Timbercard is the future in the payment and non-payment sector."

Raiffeisendruckerei
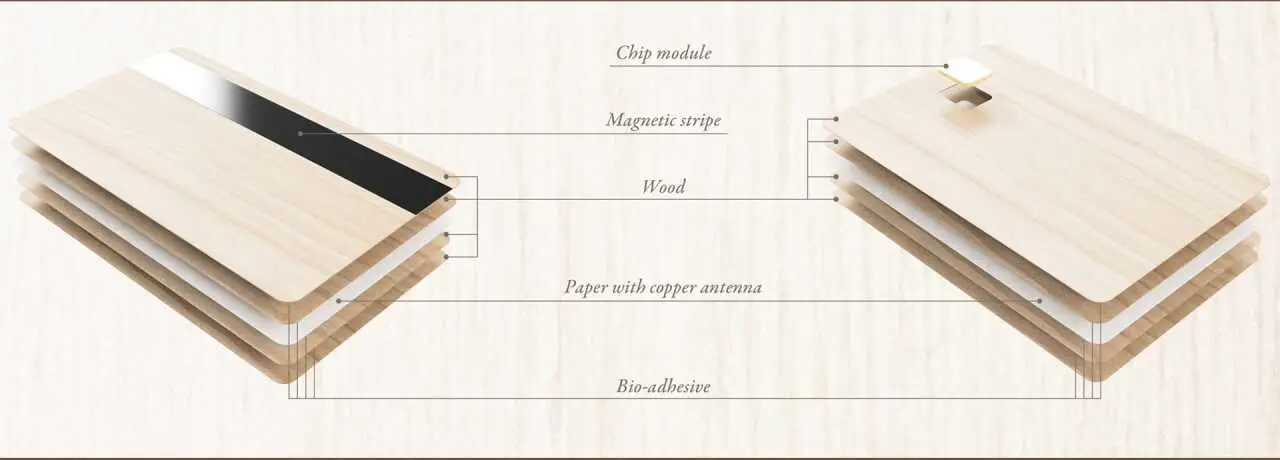
Raiffeisendruckerei has successfully completed the FSC certification process for the Timbercard.
Raiffeisendruckerei
Raiffeisendruckerei (RD) is a Payment Card Industry (PCI)-certified provider of payment cards in the financial and banking sector. Its main business is the production of payment cards for the cooperative financial network in Germany, which includes almost 700 banks.
RD specializes in the production of card bodies with various add-ons as well as the embedding of chips, personalization and dispatch to end customers in accordance with Mastercard and Visa specifications. As a subsidiary of the cooperative service provider DG Nexolution, Raiffeisendruckerei ensures the production and industrialization of the global innovation Timbercard - for the German cooperative banks and beyond.
The company has successfully completed the FSC certification process for the Timbercard. The wooden cards with the FSC label therefore originate from sustainable and environmentally friendly forestry in Germany.
In order to obtain the FSC certificate and label its own products with the FSC label, all production, processing and trading processes of the certification candidate are thoroughly checked by the experts at SCS Global Services Europe throughout the entire supply chain. Raiffeisendruckerei has established an internal FSC management system for this purpose. The Timbercard has been produced at the Raiffeisendruckerei in Neuwied since 2024.
DG Nexolution
DG Nexolution was founded more than 100 years ago under the name "DG Verlag". Today, the company employs a team of around 400 people whose aim is to promote the Volksbanken and Raiffeisenbanken, the goods and services cooperatives and the companies in the cooperative network.
Its customers include more than 700 people's banks, Sparda banks, PSD banks, partners of the cooperative financial group and over 2,000 goods and services cooperatives in Germany. DG Nexolution's subsidiaries and holdings include Copecto, Raiffeisendruckerei and Swiss Wood Solutions.
"At the specific request of the GLS Bank to obtain a payment card made purely from natural and renewable materials in addition to the antenna, magnetic strip and chip, we started production in 2022 in the style of a manufactory with a lot of manual work. We are currently working on mass-producing the Timbercard with the new machinery. At the same time, we are researching further Timbercard innovations with our partners in order to meet current and future customer requirements. This year, it is all the more gratifying to see the work of our entire team honored with the TOP 100 seal as one of the 100 most innovative medium-sized companies in Germany."
Timbercard
Timbercard as a World Premiere
The Timbercard, an innovative solution in the payment and non-payment sector, is initially aimed at companies in the payment card value chain, such as card manufacturers, distributors and personalizers, as well as banks looking for a sustainable alternative for payment cards. The card functions as a giro card as well as a Mastercard and Visa credit card and is available to bank customers via house banks. The Timbercard is currently already available at 33 credit unions in Germany. The special feature of this innovation is that it is the first completely plastic-free wooden card body for payment cards, made from certified regional wood and paper layers, combined with a biodegradable bio-adhesive.
Unlike wood-plastic hybrid cards, the Timbercard does not require a plastic layer to integrate antennas and chip technology or to achieve the mechanical durability of a payment card. Only the chip, the antenna, and the magnetic strip are made of different materials. The surface remains untreated and is smooth and closedpored, without chemical or plastic additives, thanks to a Swiss Wood Solutions process that is currently being patented. The Timbercard meets the high international ISO or CQM requirements for payment cards and has no plastic core.
Introduction of the Timbercard
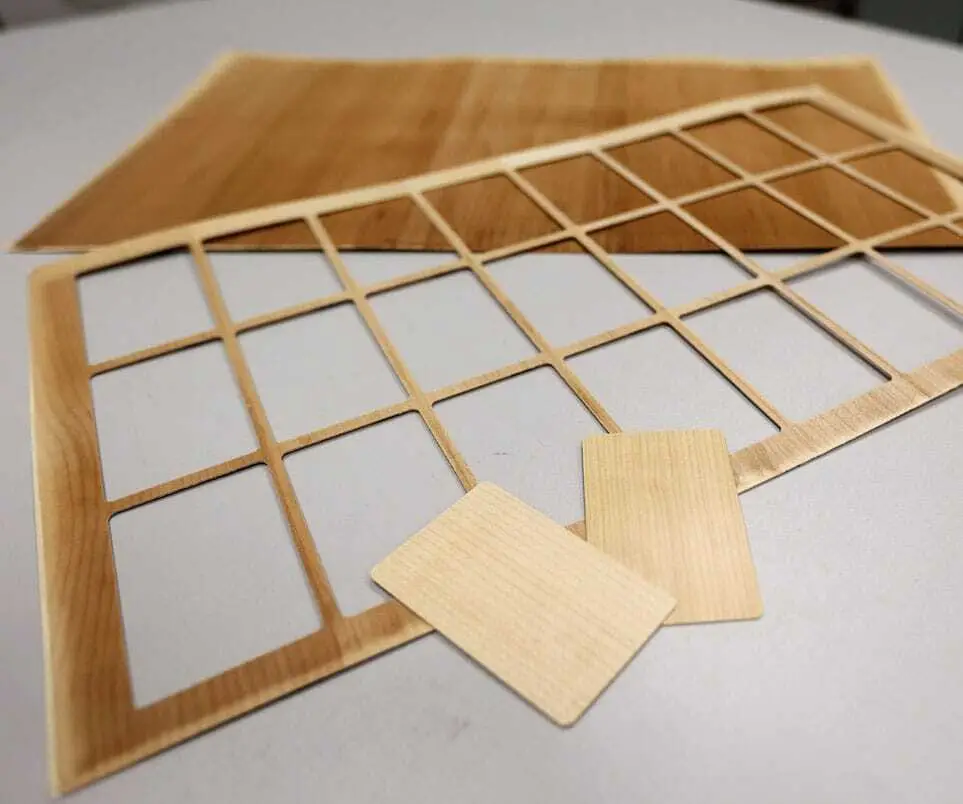
A further 11 banks in Germany have already placed orders and will introduce the card in the coming months.
The first pilot project using the first series of EMV-certified cards was launched with GLS Bank in September 2022 and has been running smoothly ever since. In 2023, around 60,000 wooden cards were already produced in a pilot plant.
Further pilot projects with 17 credit unions were carried out in Germany and Switzerland until the end of 2023. The banks involved include the Volksbank Haselünne, Hamburger Volksbank, Hannoversche Volksbank and Volksbanken Starnberg-Herrsching-Landsberg, Breisgau-Markgräflerland and Stendal. In Switzerland, a pilot project was launched in August 2023 with 1,500 cards for customers of Zürcher Kantonalbank and four other banks.
The first pilot project using the first series of EMV-certified cards was launched with GLS Bank in September 2022 and has been running smoothly ever since. In 2023, around 60,000 wooden cards were already produced in a pilot plant.
Further pilot projects with 17 credit unions were carried out in Germany and Switzerland until the end of 2023. The banks involved include the Volksbank Haselünne, Hamburger Volksbank, Hannoversche Volksbank and Volksbanken Starnberg-Herrsching-Landsberg, Breisgau-Markgräflerland and Stendal. In Switzerland, a pilot project was launched in August 2023 with 1,500 cards for customers of Zürcher Kantonalbank and four other banks.
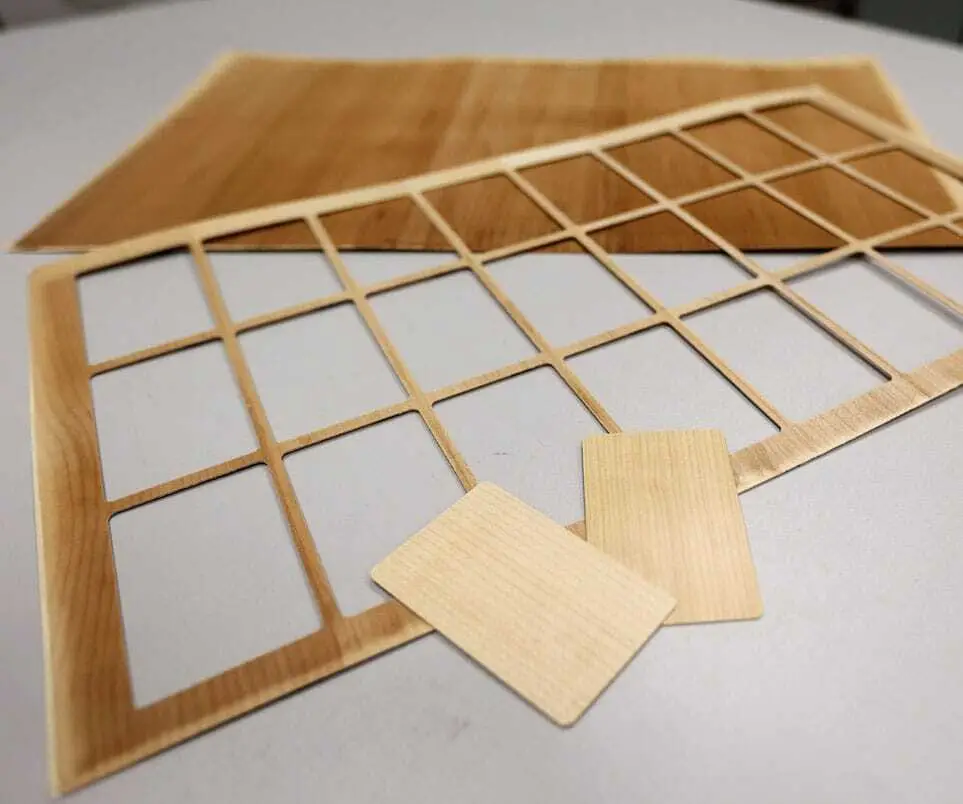
A further 11 banks in Germany have already placed orders and will introduce the card in the coming months.
An Eco-Friendly Solution
The payment card industry produces around 6 billion cards worldwide every year, which is equivalent to 30,000 tons of PVC or the weight of 150 Boeing 747s. The Timbercard, made primarily from compostable materials, was developed as a sustainable solution for this industry. The wood used to make the card comes from FSC-certified forests in the EU and Switzerland, as does the wood-based paper for the antenna inserts.
Around 100,000 Timbercards can be produced from one cubic meter of logs, while this amount of wood grows back in the German forest in only around a quarter of a second [1]. Regular timber harvesting increases the growth potential of forests and supports the economic, ecological and social function of forest areas. The Timbercard decomposes just as quickly as conventional solid wood when it comes into contact with microorganisms in the soil, which makes a significant contribution to reducing global plastic waste pollution.
Production of the Wooden Card
Tests in the ETH Laboratory
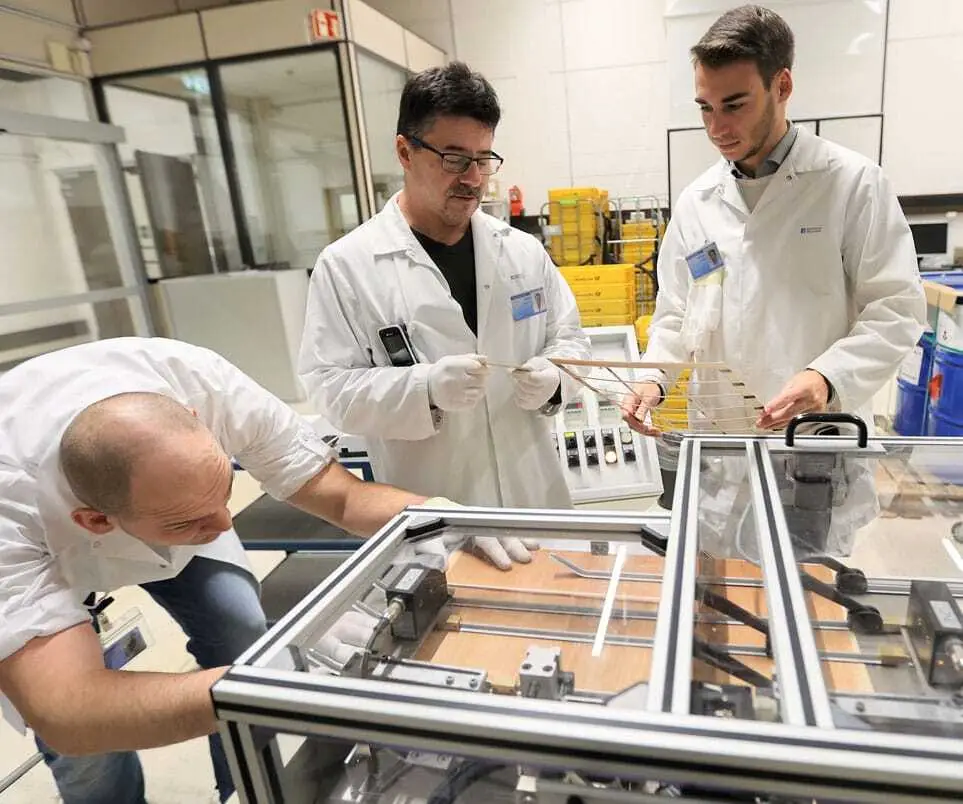
Through a process of high-pressure compression, a material similar to tropical wood is created from Swiss spruce or maple.
In 2019, Swiss Wood Solutions installed a massive press for wood processing for the first time on the Empa site in Dübendorf. The aim is to offer a variety of wood species, including sycamore maple, oak and cherry, to produce innovative products such as wooden credit cards. A small series of these credit cards was first produced in 2021. Through a process of high-pressure compression, a material similar to tropical wood is created from Swiss spruce or maple. This process began in an ETH laboratory, where researchers soaked Swiss wood in liquid and carried out tests with a laboratory press.
Thin maple veneers are soaked in liquid, extremely compressed, glued, and embossed. In addition to a copper antenna, a chip, and a magnetic strip are installed, and the cards are inscribed with a special laser. The demand for ecological wood is high, which explains the capacity utilization of the press for the next two years. Although the Swiss alternative to tropical wood is currently still comparatively expensive, this price reflects its quality and environmental friendliness compared to real tropical wood.
In 2019, Swiss Wood Solutions installed a massive press for wood processing for the first time on the Empa site in Dübendorf. The aim is to offer a variety of wood species, including sycamore maple, oak and cherry, to produce innovative products such as wooden credit cards. A small series of these credit cards was first produced in 2021. Through a process of high-pressure compression, a material similar to tropical wood is created from Swiss spruce or maple. This process began in an ETH laboratory, where researchers soaked Swiss wood in liquid and carried out tests with a laboratory press.
Thin maple veneers are soaked in liquid, extremely compressed, glued, and embossed. In addition to a copper antenna, a chip, and a magnetic strip are installed, and the cards are inscribed with a special laser. The demand for ecological wood is high, which explains the capacity utilization of the press for the next two years. Although the Swiss alternative to tropical wood is currently still comparatively expensive, this price reflects its quality and environmental friendliness compared to real tropical wood.
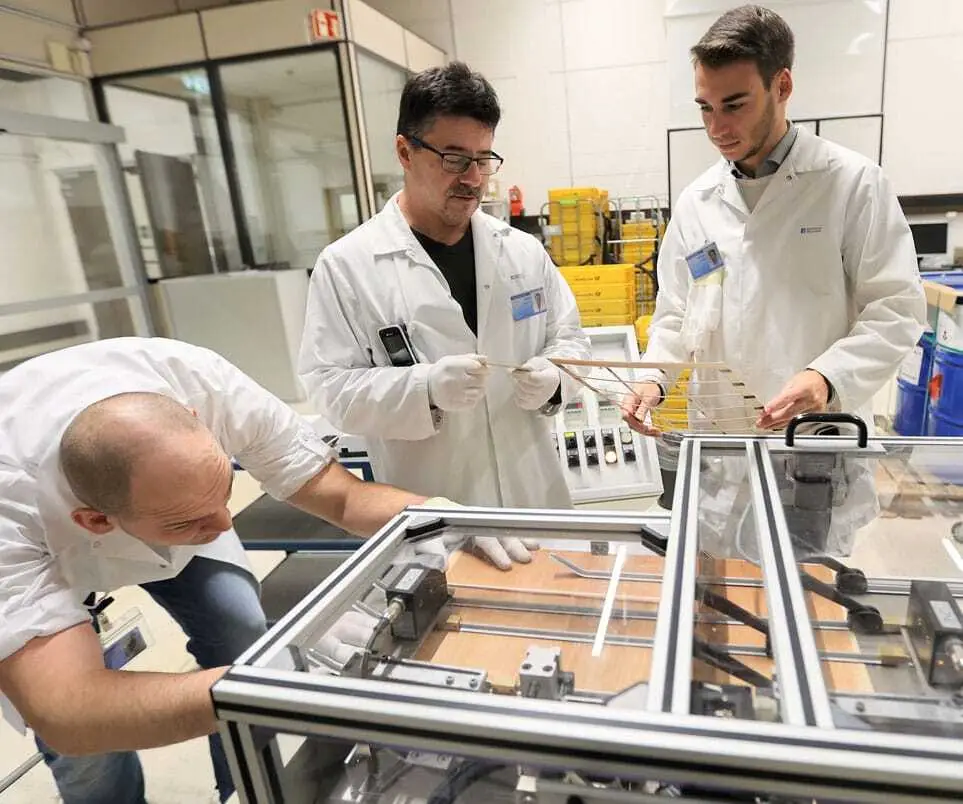
Through a process of high-pressure compression, a material similar to tropical wood is created from Swiss spruce or maple.
Increase in Production Capacity in 2024
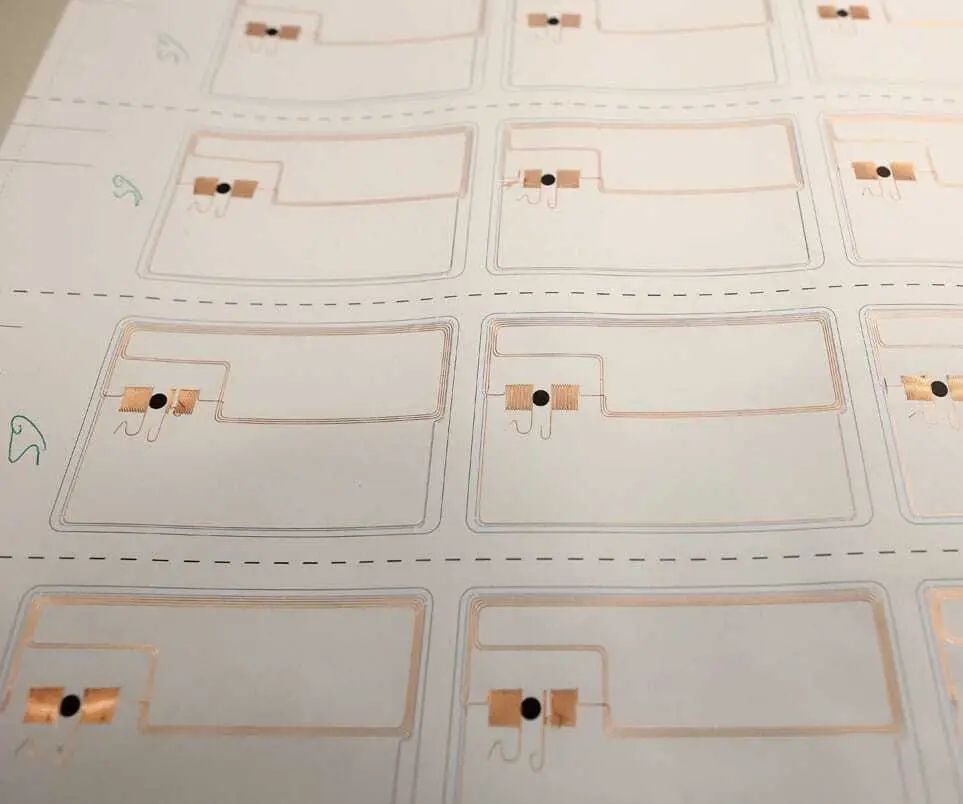
Apart from the magnetic strip, the chip and the antenna are the only components in the Timbercard that are not compostable.
Due to the explicit wish of the GLS Bank to obtain a payment card made exclusively from natural and renewable materials, the Raiffeisendruckerei began production in 2022. Since then, Copecto has tackled the global marketing of the Timbercard. Copecto and DG Nexolution are currently in talks with 150 banks and have already initiated the global marketing of the product.
A further 11 banks in Germany have already placed orders and will introduce the card in the coming months. Around 60,000 wooden cards were produced in 2023, and the Raiffeisendruckerei has invested in its machinery to enable series production of the Timbercard. In January 2024, a 30-ton laminator was delivered, which is used to press the individual wood veneers of the card.
The Timbercard has been produced industrially at the Raiffeisendruckerei in Neuwied since April 2024. With the planned increase in production capacity in the same year, significantly larger quantities will be available. At the same time, further research into Timbercard innovations is being carried out with partners in order to meet current and future customer requirements.
Due to the explicit wish of the GLS Bank to obtain a payment card made exclusively from natural and renewable materials, the Raiffeisendruckerei began production in 2022. Since then, Copecto has tackled the global marketing of the Timbercard. Copecto and DG Nexolution are currently in talks with 150 banks and have already initiated the global marketing of the product.
A further 11 banks in Germany have already placed orders and will introduce the card in the coming months. Around 60,000 wooden cards were produced in 2023, and the Raiffeisendruckerei has invested in its machinery to enable series production of the Timbercard. In January 2024, a 30-ton laminator was delivered, which is used to press the individual wood veneers of the card.
The Timbercard has been produced industrially at the Raiffeisendruckerei in Neuwied since April 2024. With the planned increase in production capacity in the same year, significantly larger quantities will be available. At the same time, further research into Timbercard innovations is being carried out with partners in order to meet current and future customer requirements.
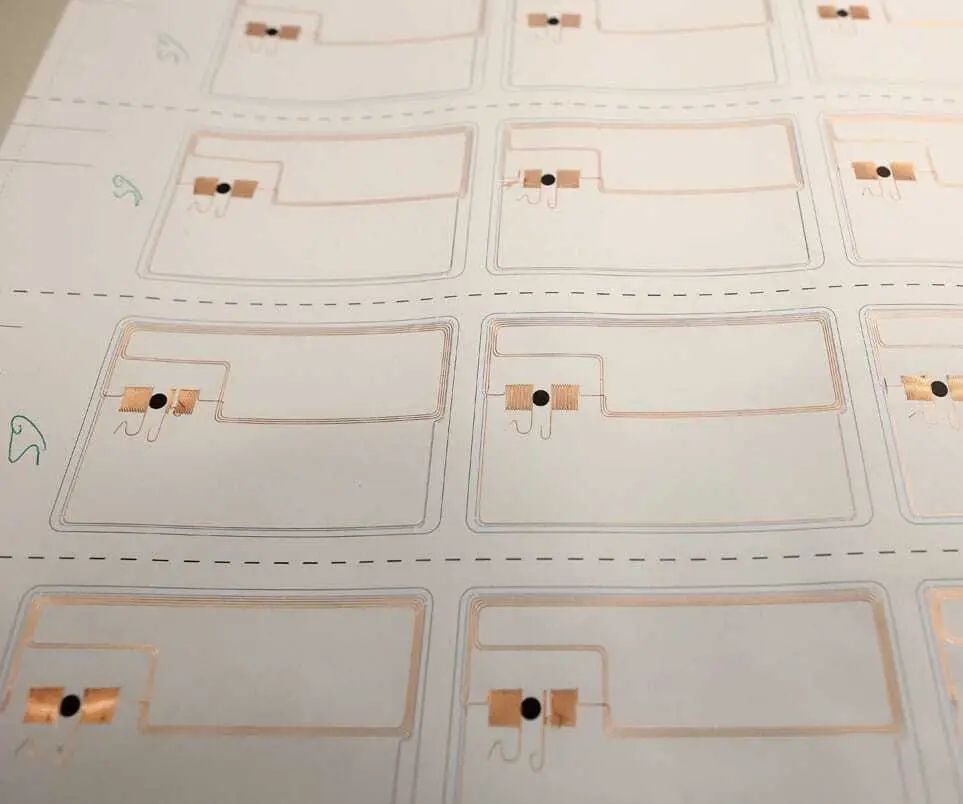
Apart from the magnetic strip, the chip and the antenna are the only components in the Timbercard that are not compostable.
The Production Process
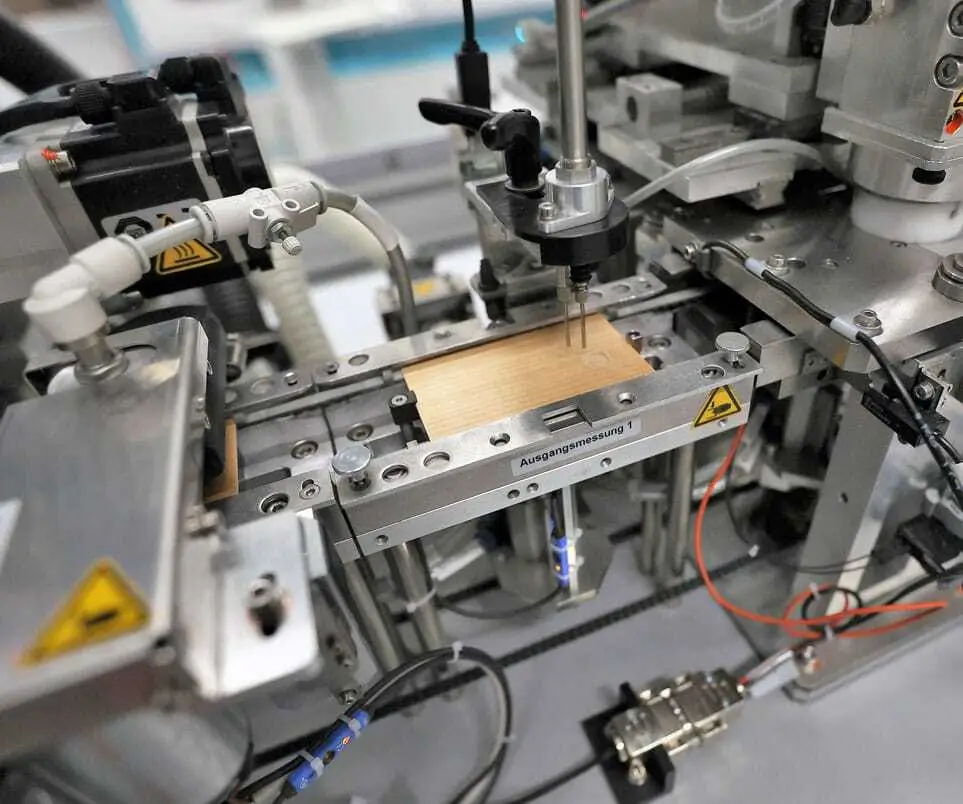
The Timbercard has been produced industrially at the Raiffeisendruckerei in Neuwied since April 2024.
Production at Raiffeisendruckerei begins with the folding and pressing of the individual layers of wood veneer and paper, and the subsequent punching of card blanks from a wooden sheet, consisting of 4 layers of veneer and one layer of paper, without plastic. Volume reduction and increased density produce a hard, smooth, and non-porous material.
The hologram is applied using a hot stamping machine before the chip is connected to the antenna using solder paste and firmly implanted in the previously milled cavity of the wooden card. This is the core of the production process and makes the card fully functional. Personalization is then carried out by writing data on the chip before a laser is used to inscribe the cards and write on the magnetic strip in the final step.
Production at Raiffeisendruckerei begins with the folding and pressing of the individual layers of wood veneer and paper, and the subsequent punching of card blanks from a wooden sheet, consisting of 4 layers of veneer and one layer of paper, without plastic. Volume reduction and increased density produce a hard, smooth, and non-porous material.
The hologram is applied using a hot stamping machine before the chip is connected to the antenna using solder paste and firmly implanted in the previously milled cavity of the wooden card. This is the core of the production process and makes the card fully functional. Personalization is then carried out by writing data on the chip before a laser is used to inscribe the cards and write on the magnetic strip in the final step.
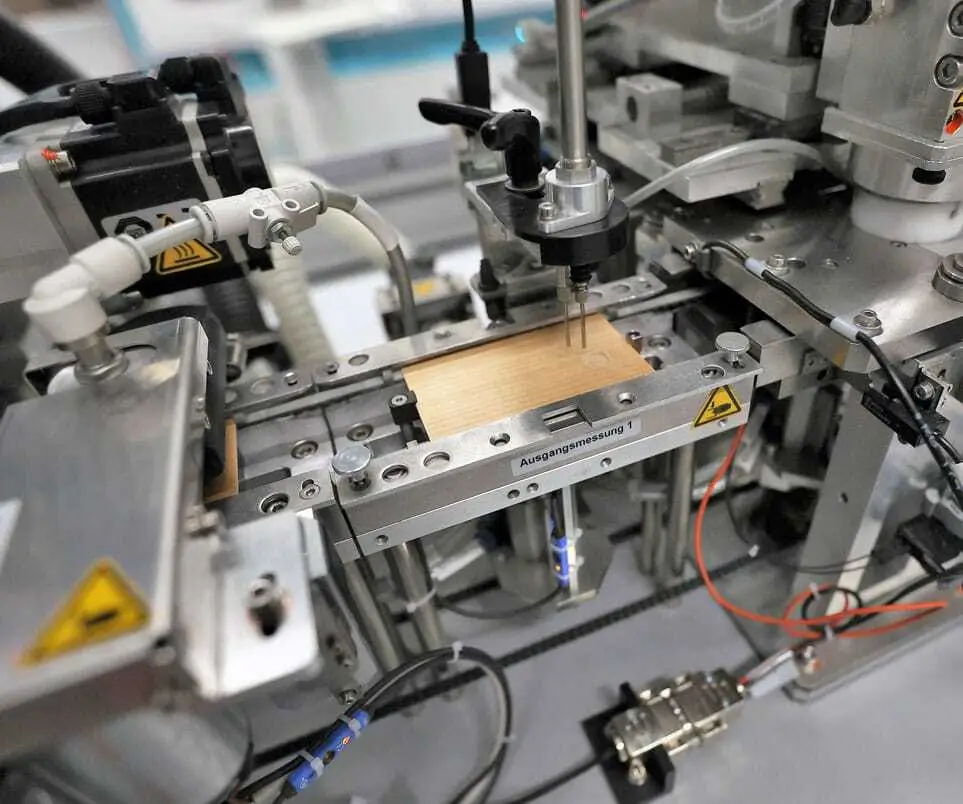
The Timbercard has been produced industrially at the Raiffeisendruckerei in Neuwied since April 2024.