Laundry Solution with RFID Technology at University Hospital Graz in Austria
A 4-Year Planning Phase
The first steps towards RFID technology began back in 2016. Together with my colleagues at KAGes-Textilservice, I looked for innovative solutions to optimize clothing processes. The aim was to streamline logistics processes and thus save both time and costs. A key milestone was our visit to the University Hospital Zurich (USZ). The RFID considerations there provided the decisive impetus for the implementation of an RFID-based laundry solution in our hospital as well. In close cooperation with KAGes-Textilservice, I then fundamentally redesigned the concept of uniforms. We discussed topics such as the depersonalization of clothing, the quality of clothing as well as the colour design and its effects on the washing process. Our goal was a comprehensive restructuring of the entire laundry system.
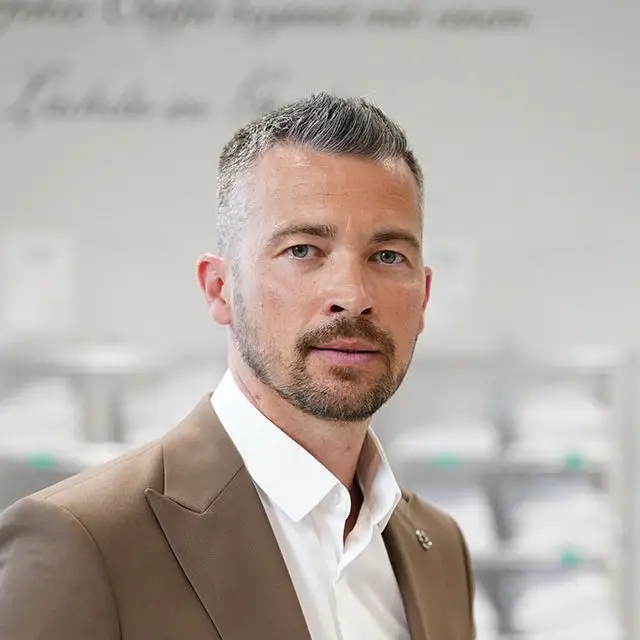
Start: Digital Simulation
In 2018, an initial comprehensive computer simulation was carried out with the support of an external service provider. This PC simulation was used to visualize and optimize not only the possible infrastructural conditions but also the working hours and processes of the planned pilot project at the children's center of University Hospital Graz. The simulation made it possible to identify potential challenges at an early stage and make appropriate adjustments.
Once the PC simulation had been successfully completed, a real-world simulation (shop floor) was next on the agenda. In this phase, the planned clothing room was almost completely reconstructed with wooden or cardboard walls in order to simulate the clothing room as realistically as possible whilst involving all the professional groups concerned – in line with the hospital's lean management approach.
The entire simulation was accompanied and comprehensively documented by a camera team. Checklists and observation posts were used for precise observation. Everyone who entered the room was given a routing slip that assigned them to the relevant simulation area. The simulation was a complete success and provided valuable insights that was then able to be incorporated into the pilot.
Pilot Project in 2020 with 1,000 Employees at the Children's Center
The first clothing room at the children's center was launched in August 2020. The aim of the project was to test the issuance of RFID-chipped, depersonalized uniforms in a specially equipped room with RFID gates.
For this purpose, a rectangular RFID-based clothing room measuring around 80 square meters was set up in the children's center. Around 1,000 employees took part in this pilot project and were able to obtain the work clothing they needed there around the clock. Even during the pilot project, the workwear was offered in several colors to meet the different requirements.
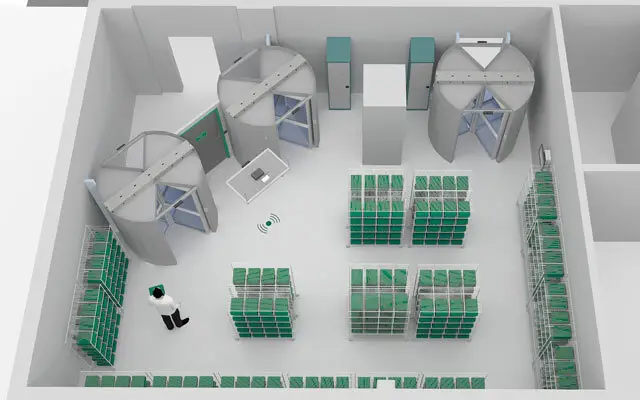
Pilot project: A rarely used swimming pool was converted for the first RFID-based clothing room at the children's center. The results showed that 10 to 20% of the clinic staff had initial difficulties finding their way around the 80 square meter room. However, the majority of employees were able to work without any problems.
The Conclusion of the Pilot and Strategic Decisions
The pilot project proved to be a great success and provided valuable insights for the further successful implementation of the technology at the university hospital. One of the most important findings of the simulation and the pilot project was the installation of a second exit carousel.
Although the original goal was to initially only equip the RFID project in the children's center with colorful workwear, due to the success and positive demand, it was decided to also equip all other clothing rooms in the entire hospital with colorful workwear. Furthermore, following the successful pilot project, the RFID system was installed in other clothing rooms from 2021 onwards.
The pilot project confirmed that the clothing room plays a central role in the depersonalized workwear concept. The decision to implement the RFID-supported laundry solution and depersonalize workwear was made after the pilot project was completed.
Based on real data, students evaluated the RFID-supported clothing project in addition to the positive experiences from the pilot project. The results showed that the RFID installation generated economic added value, simplified handling processes, and significantly increased employee satisfaction thanks to the depersonalized workwear.
A Positive Evaluation
Overall, the feedback from everyone involved in the pilot project was sensationally positive. This was the basis for the implementation of the next milestone – the first clothing room at KAGes and in Styria and the second of its kind in Austria. We were really at the forefront of this innovation. The solution was well received and the final decision was made in favor of the RFID room solution. The entire washing process, finishing and sorting system have been simplified. The depersonalization of workwear has made daily handling much easier for us. Every process step has been revised. As the garments no longer need to be personalized, the time and effort required to process each individual garment has been reduced. Employee satisfaction has increased. Garments that were designed for around 50 washes are now washed at least 70 times.
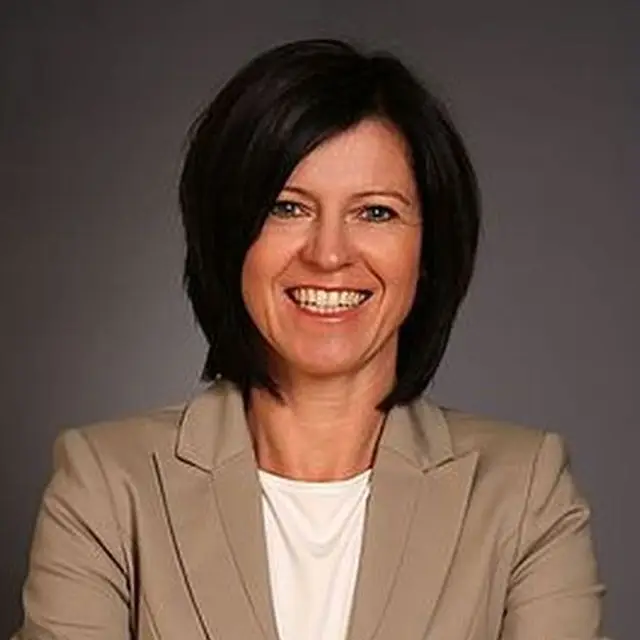
University Hospital Graz and KAGes-Textilservice
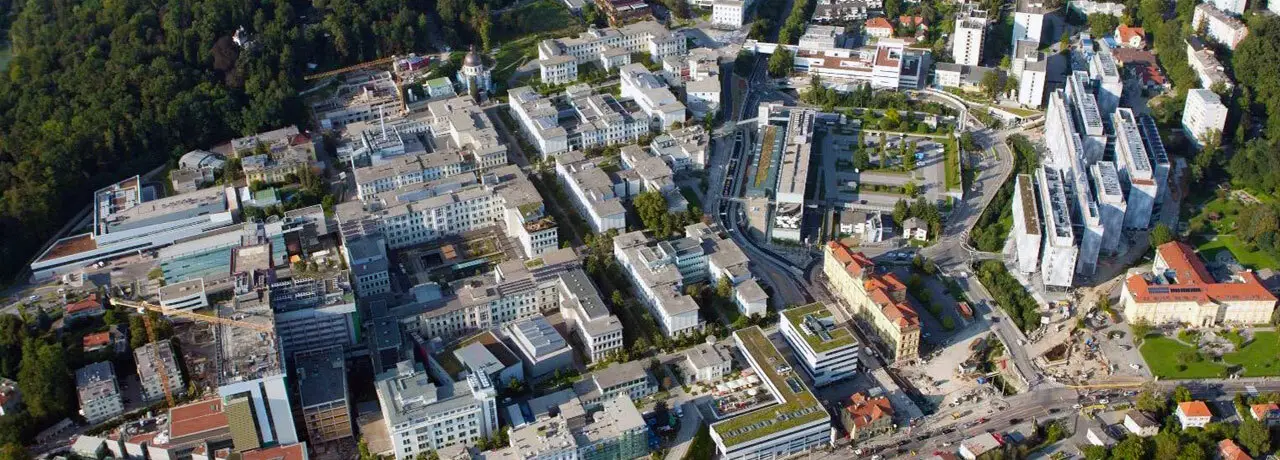
University Hospital Graz has an area of around 340,000 square meters. This area is roughly equivalent to 69 soccer pitches. This makes the hospital one of the largest hospitals in Europe in terms of surface area. 7,500 employees care for patients, for whom 1,500 beds are available. All in all, it is a gigantic complex that has existed as a pavilion system with kilometers of underground tunnels since 1910, the year it was fundamentally redesigned. It is precisely these supply or logistics tunnels that today make it possible to transport the 20 tons of laundry that has to be handled every day.
Hospital and Textile Service Pull Together
University Hospital Graz is owned by the Province of Styria, which belongs to the Styrian Hospital Association (Steiermärkische Krankenanstaltengesellschaft). University Hospital Graz is the central hospital for Styria.
KAGes-Textilservice is an internal service provider of Stmk. Krankenanstaltenges.m.b.H. and was established in 1997. In addition to University Hospital Graz, KAGes-Textilservice supplies a further 8 locations with patient laundry (with the exception of sterile laundry) and uniforms. In a two-shift operation – from Monday to Friday – around 20 tons of laundry are washed every day.
University Hospital Graz is currently the largest customer, accounting for 60 percent of the laundry distribution.
Status Quo Before the RFID Implementation
The Initial Situation
The main objective of University Hospital Graz was to reassess the concept of hospital workwear as part of the overall logistics concept drawn up in 2014. This involved not only reassessing the entire supply chain, but also the laundry processes.
Until then, workwear had mainly been issued on a personalized basis and stored by employees in lockers. As a result, many items of laundry were very rarely used and there was no regular laundry cycle. The aim was to optimize laundry management and save time and operating costs while maintaining the same quality.
A frequent problem was, for example, worn work clothes that were forgotten in changing room lockers. This clothing represented tied-up capital that was not being used. Thanks to the RFID tag, the missing clothing can be tracked and reassigned.
A Brief Historical Digression on the Heart of Logistics
As part of the construction of the hospital in the extensive park area, cellar corridors were built from 1910, and it was not until around 80 years later that the logistics tunnel was constructed, which today plays a central role in the logistics of University Hospital Graz. With a total length of 1.9 kilometers, this underground network enables efficient supply of the hospital.
The two-lane logistics tunnel connects the hospitals with the care center, which opened in 2015. It is used for the transportation of both goods and patients. The tunnel overcomes a gradient of six to eight percent and is the heart of the hospital's logistics infrastructure. Transportation is carried out exclusively by electric vehicles, with around 1,400 journeys being made every day. Each driver covers a distance of around 50 kilometers, resulting in a total of 450,000 journeys per year.
Around 20 tons of laundry are also transported in the logistics tunnel every day. This underground logistics structure enables the entire hospital to be supplied smoothly and efficiently.
Two Hurdles Had to Be Overcome
- The first challenge concerned the acceptance of all hospital departments and employees. Initially, there was some resistance to the switch to non-personalized clothing. Some employees argued against the removal of titles and names. On the other hand, the higher quality workwear increased acceptance and employee satisfaction.
- The second challenge was to find strategic locations and spaces for the clothing rooms. The first changing room in the children's center was originally a swimming pool that had been closed due to lack of use. This pilot room was ideal as it was located right next to the changing rooms.
RFID Installation
How Does the RFID Solution Work?
After dropping off the used workwear in the return chute, the staff member enters the clothing room. Thanks to the patched RFID tags, the system automatically records the number of items of clothing returned and distinguishes between pants and tops. The returned clothing is credited to the employee's personal quota. The quota is automatically updated in real time.
The carousel is activated using the employee ID card, which authorizes access to the room. Employees can take pants and tops from the clothing room according to the available quota. As a rule, a maximum of three tops and three pairs of pants are provided per employee. Once the required items of clothing have been selected, the employee leaves the room through an exit gate.
The airlock is equipped with RFID technology so that the clothing items are automatically captured in real time. The removal is automatically deducted from the employee's available quota.
The clothing room is designed as a simple yet efficient solution. It is equipped with practical shelves on which the folded, clean work clothes are stored.
The fresh clothing is delivered by the textile service and transported to the clothing room by employees of the university hospital. Each individual item of clothing is provided with an RFID tag on delivery, and the entire delivery is scanned by an RFID reader when it is brought into the room and assigned to the room. The stocks are updated in real time.
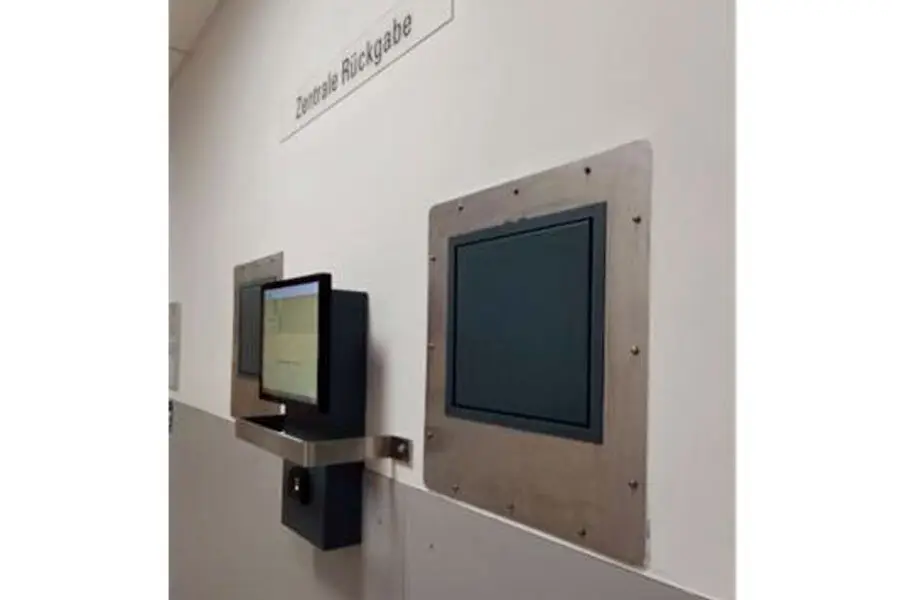
The image shows the “floorless return cabinet”, which is similar to a conventional return cabinet, but is designed without a floor and with a direct connection to the laundry chute. This cabinet is available in different versions and was developed for University Hospital Graz.
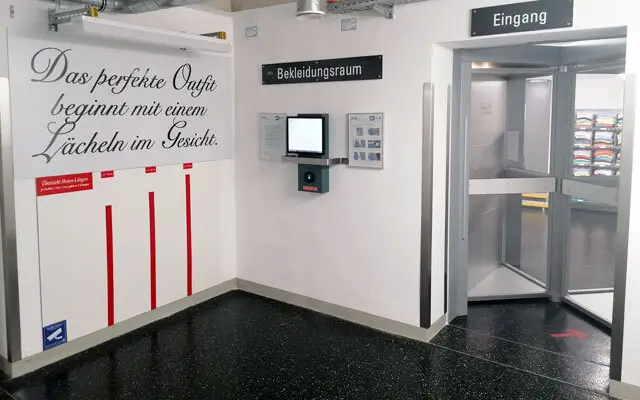
The entrance to the clothing room is designed to be transparent and friendly. Each user can view their current stock at the terminal. The quota and access check is carried out quickly and easily directly at the carousel. Arrows on the sheet show the direction of movement. The carousel adapts to the user's walking speed as it is not motorized.
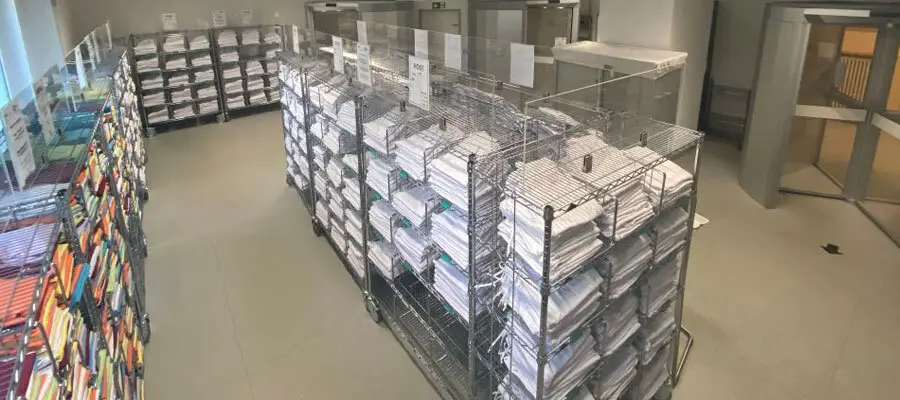
Employees select the required depersonalized clothing themselves according to the desired color. When leaving the clothing room through the revolving door, the washable RFID transponder is automatically captured and charged to the employee's allocation. This means that in addition to real-time documentation of which employee has taken what and how much, stocks are always up to date. This data is invaluable for replenishment.
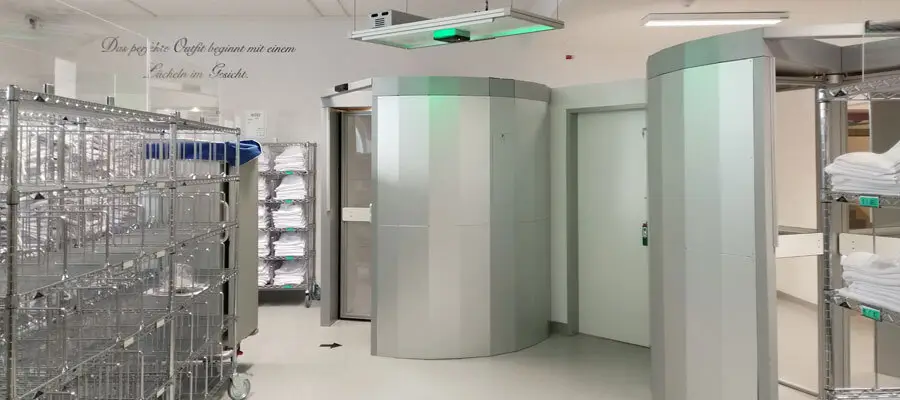
A system is used specifically for bulk reading within closed containers, where the laundry is booked into a container in the laundry. This process is also known as “teach-in”. The container is fitted with a special transponder, which is identified in the room by the trolley scan. All laundry is automatically assigned to the room. This method optimizes the process and can also be fully automated with AGVs (automated guided vehicles) and ensures seamless integration of the logistics processes in laundry management.
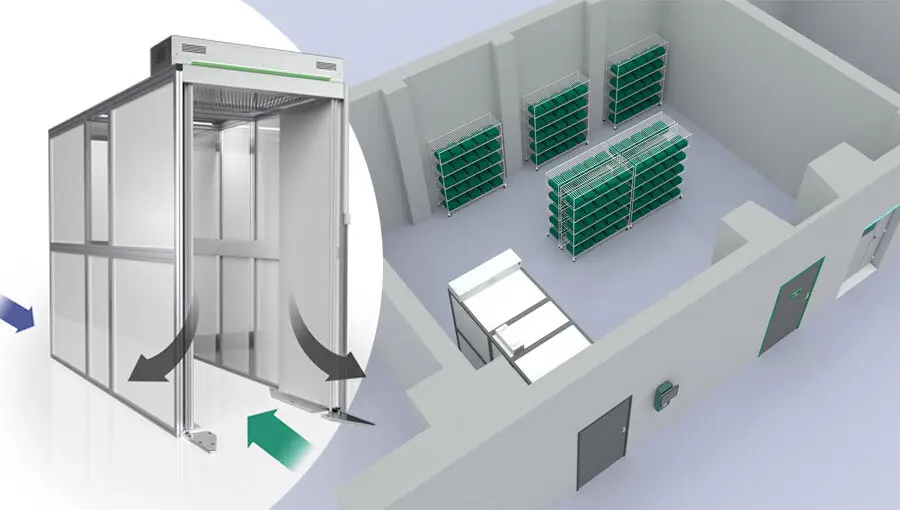
Flap Gates from Deister Electronic are used in smaller laundry rooms. These innovative systems combine the function of an airlock with an RFID-controlled exit. As the flap gates are designed to be barrier-free, they can also be passed through by wheelchair users without any obstacles.
Success and Implementation Results
- The new laundry management system offers KAGes-Textilservice and University Hospital Graz full transparency regarding the workwear in circulation. The hospital monitors at department level how many items of clothing each employee has removed, with a maximum of three items of outerwear and three items of underwear permitted. If this quota is exceeded, access to the clothing room is blocked.
- One major step forward is the introduction of colored clothing. While doctors and nursing staff traditionally wore white uniforms and paramedics wore striped uniforms, the new colorful uniforms no longer differentiate between professional groups.
- Another success of the project can be attributed to the application of the lean philosophy. The implementation of the project required close cooperation between various departments, including IT, the staff representatives, KAGes-Textilservice, and the hospital management. The Board of Directors and the Rectorate were also heavily involved.
- Thanks to the circular economy, considerable savings have been made on the purchase costs. These savings will quickly amortize the initial investment. The funds freed up will be reinvested in the procurement of high-quality uniforms.
- An additional advantage of the digital capture of logistics processes is the transparent display of all core logistics processes. Employees can use the terminal to view the processes that have already been recorded. This transparency has led to a high level of acceptance of the project within the workforce.
- Overall, data management is rated positively and is constantly being improved. Thanks to the embedded RFID chips, every item of workwear can be precisely tracked and located, which reduces shrinkage to a very low level.
Optimizations until 2026
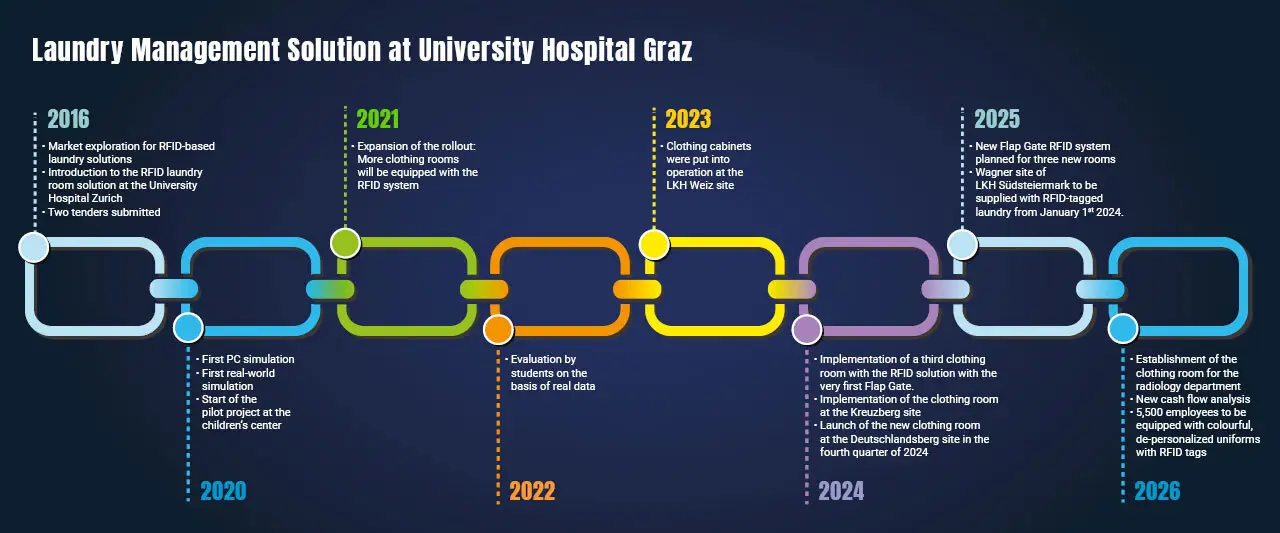
The graphic shows that the RFID solution at KAGes-Textilservice and University Hospital Graz is undergoing continuous further development. The next development steps, such as the future RFID clothing rooms, the installation of additional Flap Gates and the expansion of the clothing pool to include additional clothing variants in modern colors, are also being planned. Overall, both interviewees draw a clear conclusion: “The RFID solution and the collaboration with Deister Electronic have been a great success.”
Agenda for the Future
The next step in the rollout of the clothing room is the implementation of the new RFID system in three other areas: the University Clinic for Internal Medicine, which serves 1,400 employees, Surgery (800 employees) and Radiology, which is currently under construction. The radiology clothing room will serve around 500 employees and will go into operation in 2026.
Once the project is provisionally completed, a total of around 5,500 employees will have coloured, depersonalized workwear equipped with RFID tags.
Evaluation issues will also be further refined as part of data management and monitoring. University Hospital Graz is striving to optimize these processes. A further expansion step of the project could be the integration of artificial intelligence for reporting in the flap gate or the carousels together with the company Deister Electronic.