Digitalization in Production
Customer Requirements
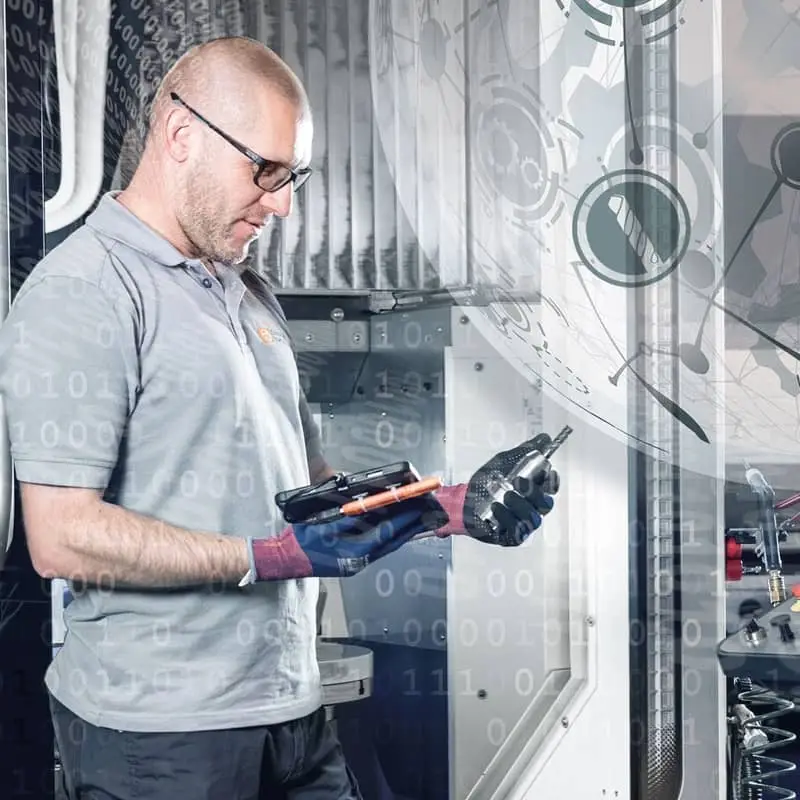
The Hoffmann Group is one of the leading suppliers of quality tools, personal protective equipment (PPE) and factory equipment in Europe.
"Two trends have emerged from discussions with our customers in recent years," explains Nicolas Frank, Team Lead Digital Manufacturing at the Hoffmann Group. "Many customers want to digitize their companies, but don't know how. At the same time, almost all production processes are paper-based and complicated."
This means that information that many people need, is often only held by one person, in the form of memorized expertise. Tools are difficult to find, which results in long idle times (machine downtimes). The Hoffmann Group has been offering digital tool and clamping device management as a solution to this problem since 2019.
"Two trends have emerged from discussions with our customers in recent years," explains Nicolas Frank, Team Lead Digital Manufacturing at the Hoffmann Group. "Many customers want to digitize their companies, but don't know how. At the same time, almost all production processes are paper-based and complicated."
This means that information that many people need, is often only held by one person, in the form of memorized expertise. Tools are difficult to find, which results in long idle times (machine downtimes). The Hoffmann Group has been offering digital tool and clamping device management as a solution to this problem since 2019.
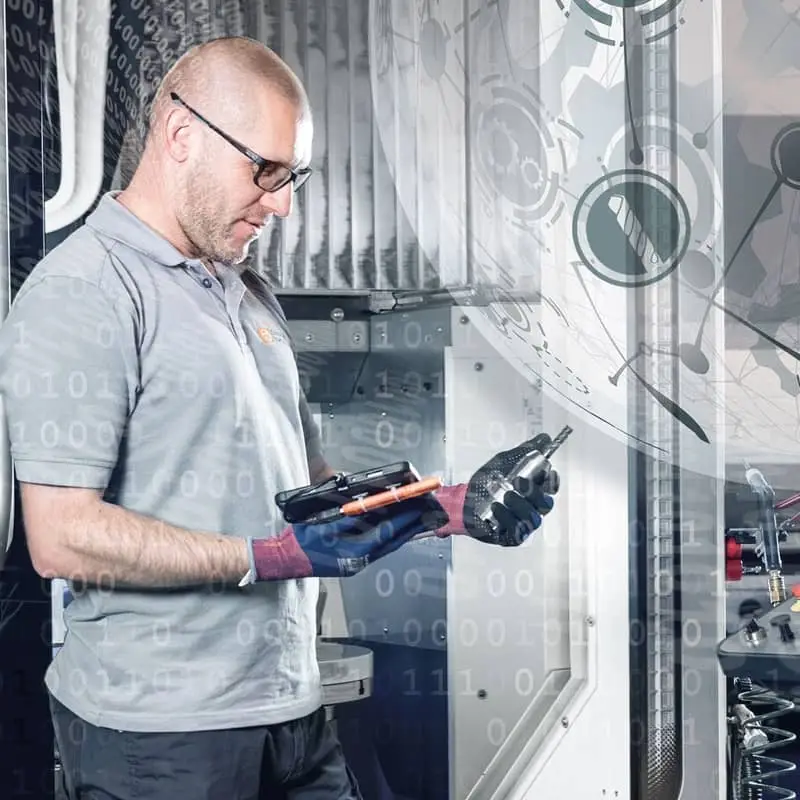
The Hoffmann Group is one of the leading suppliers of quality tools, personal protective equipment (PPE) and factory equipment in Europe.
The Hoffmann Group
Digitalization in Production
Hoffmann Group
- Founded in 1993 under the umbrella of the Munich-based company Hoffmann
- Holex and Garant are brands of the Hoffmann Group
- Over 120,000 products permanently deliverable
- 55,000 certified tools from the GARANT system brand
- 17,000 tools of the quality brand HOLEX
- 500 other leading brands
- 4,000 employees in the Hoffmann Group worldwide
- Company presence in 50 countries and 135,000 customers worldwide
- Connected Manufacturing introduced for the first time in 2019
- Part of the Swiss SFS Group since May 2022
In a typical production environment, there are lathes and milling machines, a presetter and a tool dispensing cabinet. Before the tool can be used, it must be assembled. Using a goods issuing system such as the Hoffmann Group's GARANT Tool24, the employee receives the drill required, for example. He then needs a tool holder; combined, the two form the complete, ready-to-use tool. This must be measured on the presetting device before it can be inserted into the machine.
In traditional paper-based production, it is often time-consuming to find the required tool parts because their last storage location is unknown. Whether they have been used before and if so, how often, are further questions that can only be answered by talking to employees. In addition, it must be determined whether the measured values noted on the tool with a pencil or ballpoint pen are still up-to-date. During this time, the machine remains idle.
The Connected Manufacturing digital tool management system streamlines these processes. It is a modular software tool that provides a complete overview of all tools and their parameters. Each complete tool is serialized and created as a digital twin in Connected Manufacturing. This greatly reduces search and waiting times.
In a typical production environment, there are lathes and milling machines, a presetter and a tool dispensing cabinet. Before the tool can be used, it must be assembled. Using a goods issuing system such as the Hoffmann Group's GARANT Tool24, the employee receives the drill required, for example. He then needs a tool holder; combined, the two form the complete, ready-to-use tool. This must be measured on the presetting device before it can be inserted into the machine.
In traditional paper-based production, it is often time-consuming to find the required tool parts because their last storage location is unknown. Whether they have been used before and if so, how often, are further questions that can only be answered by talking to employees. In addition, it must be determined whether the measured values noted on the tool with a pencil or ballpoint pen are still up-to-date. During this time, the machine remains idle.
The Connected Manufacturing digital tool management system streamlines these processes. It is a modular software tool that provides a complete overview of all tools and their parameters. Each complete tool is serialized and created as a digital twin in Connected Manufacturing. This greatly reduces search and waiting times.
Hoffmann Group
- Founded in 1993 under the umbrella of the Munich-based company Hoffmann
- Holex and Garant are brands of the Hoffmann Group
- Over 120,000 products permanently deliverable
- 55,000 certified tools from the GARANT system brand
- 17,000 tools of the quality brand HOLEX
- 500 other leading brands
- 4,000 employees in the Hoffmann Group worldwide
- Company presence in 50 countries and 135,000 customers worldwide
- Connected Manufacturing introduced for the first time in 2019
- Part of the Swiss SFS Group since May 2022
Paperless Production
Connected Manufacturing
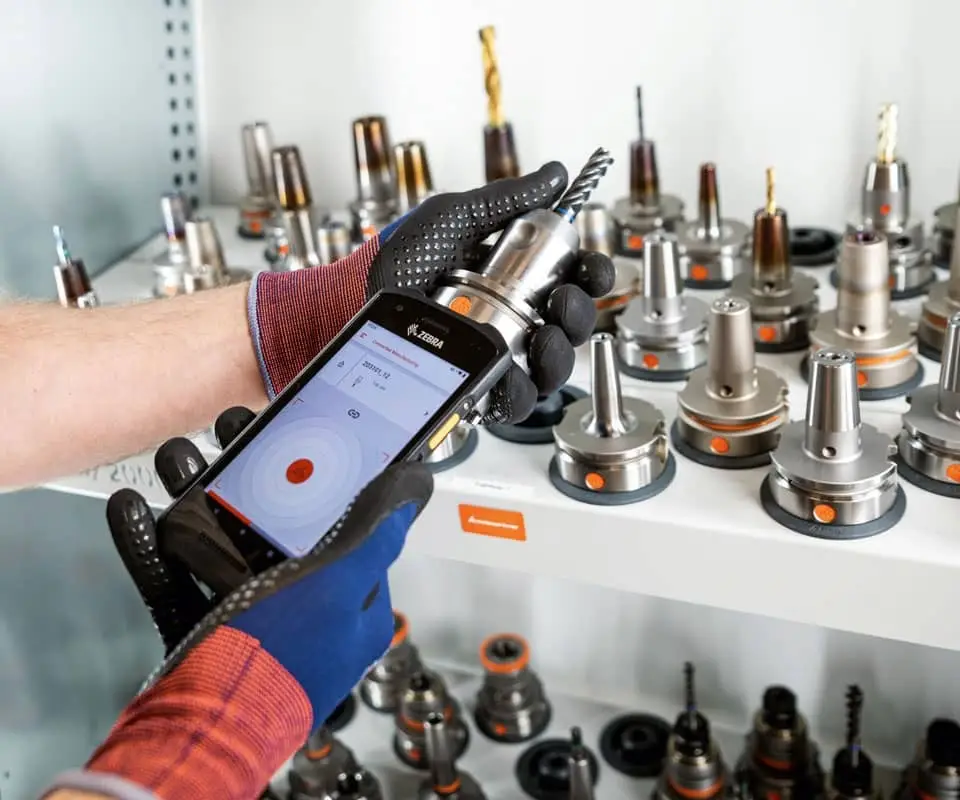
All processes that a tagged tool goes through are saved in the digital twin. The history and status can be viewed.
Connected Manufacturing is a complete cloud-based solution for tool and production management that can optionally be connected to the ERP system via an interface. This is where the order data comes from, to which the production data is subsequently linked. Connected Manufacturing gives employees complete transparency about the tool inventory and its history at all times. Data such as the length and radius of a tool, which the machine operator normally has to enter manually in the control system, is also transferred. All machine tools and orders that are processed on them are managed directly within the software.
Serialization with RFID
HF-RFID is used to enable the unique identification of a tool. Each individual chuck is fitted with a 10 mm round RFID chip from Neosid, which is pressed in and permanently connected. The chip's unique identification number is the serialization number, which is stored centrally in Connected Manufacturing. No information is stored on the chip itself. The chips on the tools are read using readers in the tool dispenser, in the presetting device and on the machines or with mobile devices such as tablets or smartphones.
Connected Manufacturing is a complete cloud-based solution for tool and production management that can optionally be connected to the ERP system via an interface. This is where the order data comes from, to which the production data is subsequently linked. Connected Manufacturing gives employees complete transparency about the tool inventory and its history at all times. Data such as the length and radius of a tool, which the machine operator normally has to enter manually in the control system, is also transferred. All machine tools and orders that are processed on them are managed directly within the software.
Serialization with RFID
HF-RFID is used to enable the unique identification of a tool. Each individual chuck is fitted with a 10 mm round RFID chip from Neosid, which is pressed in and permanently connected. The chip's unique identification number is the serialization number, which is stored centrally in Connected Manufacturing. No information is stored on the chip itself. The chips on the tools are read using readers in the tool dispenser, in the presetting device and on the machines or with mobile devices such as tablets or smartphones.
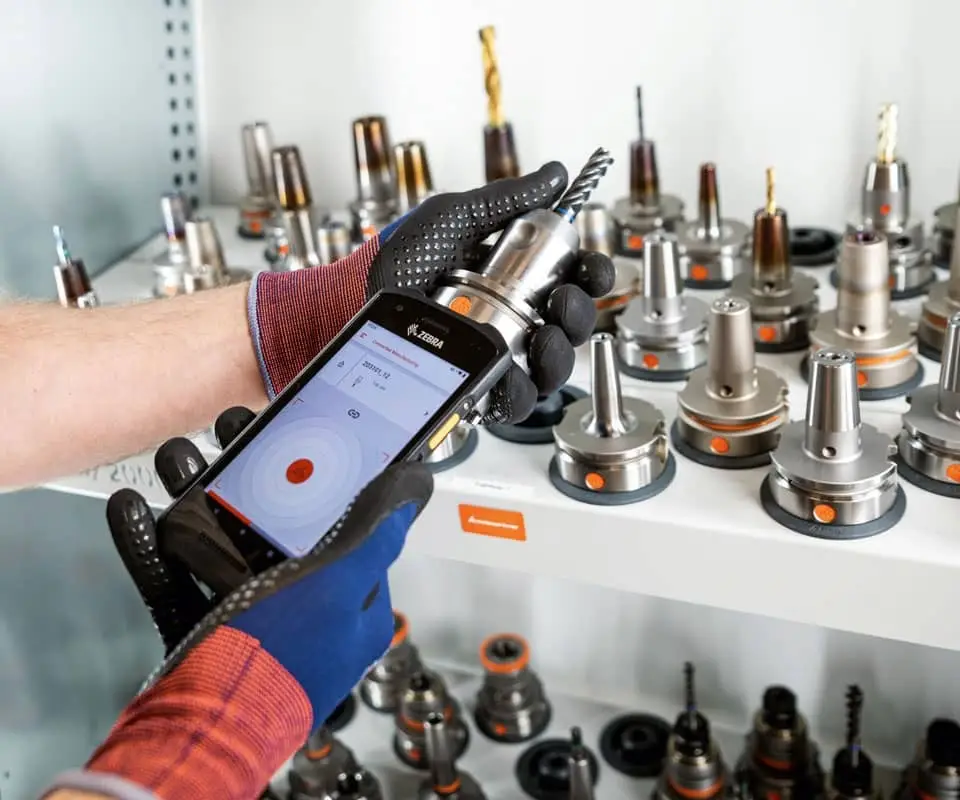
All processes that a tagged tool goes through are saved in the digital twin. The history and status can be viewed.
Advantages During Idle Times
Connected Manufacturing
- Interface with the ERP system
- Tool requirements are visible from the order
- Overview of available tools
- Automated tool dispensing
- 20–40 % reduction in idle times (search and set-up time, machine downtime)
- Future-proof for further digitalization steps
"Machine downtime incurs high costs. In industry, the main aim is therefore to achieve the highest possible capacity utilization of the systems. The machines have to run," explains Marion Schwenk, Senior Public Relations Manager at the Hoffmann Group. "Connected Manufacturing can contribute to this by reducing downtimes. In addition, recurring orders or repair jobs can be brought back to the machine quickly. This saves nerves, time and costs." It's not just search times that are reduced because tools can be found quickly. The set-up times for machines are also significantly reduced. Transmission or typing errors from tool measurement values to the machine control can no longer occur, which also prevents major damage to the machine.
The Vision of a Fully Connected Manufacturing
Connected Manufacturing is a solution that customers can implement in individual modules on the way to Industry 4.0. It is expected to become fully established in the manufacturing industry within the next 10 years. The latest module is known as "Connected Metrology" and represents the intelligent management of measuring equipment, calibration data exchange and measurement data acquisition.
"Machine downtime incurs high costs. In industry, the main aim is therefore to achieve the highest possible capacity utilization of the systems. The machines have to run," explains Marion Schwenk, Senior Public Relations Manager at the Hoffmann Group. "Connected Manufacturing can contribute to this by reducing downtimes. In addition, recurring orders or repair jobs can be brought back to the machine quickly. This saves nerves, time and costs." It's not just search times that are reduced because tools can be found quickly. The set-up times for machines are also significantly reduced. Transmission or typing errors from tool measurement values to the machine control can no longer occur, which also prevents major damage to the machine.
The Vision of a Fully Connected Manufacturing
Connected Manufacturing is a solution that customers can implement in individual modules on the way to Industry 4.0. It is expected to become fully established in the manufacturing industry within the next 10 years. The latest module is known as "Connected Metrology" and represents the intelligent management of measuring equipment, calibration data exchange and measurement data acquisition.
Connected Manufacturing
- Interface with the ERP system
- Tool requirements are visible from the order
- Overview of available tools
- Automated tool dispensing
- 20–40 % reduction in idle times (search and set-up time, machine downtime)
- Future-proof for further digitalization steps
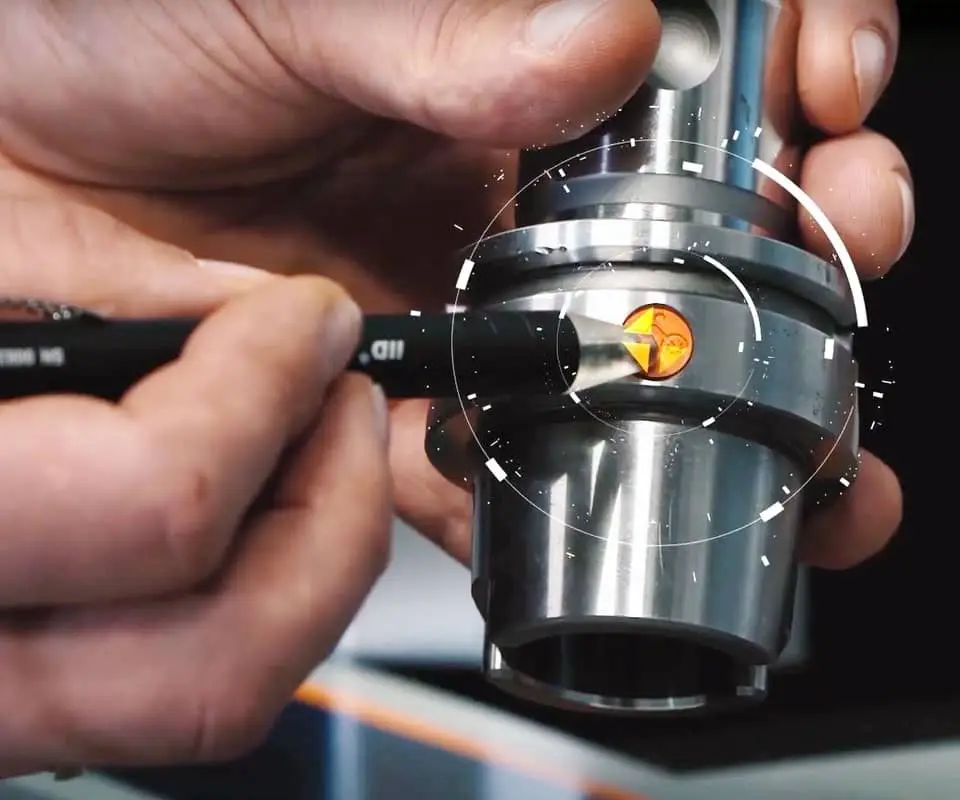
In-Metal Tags
In-Metal Transponders from Neosid
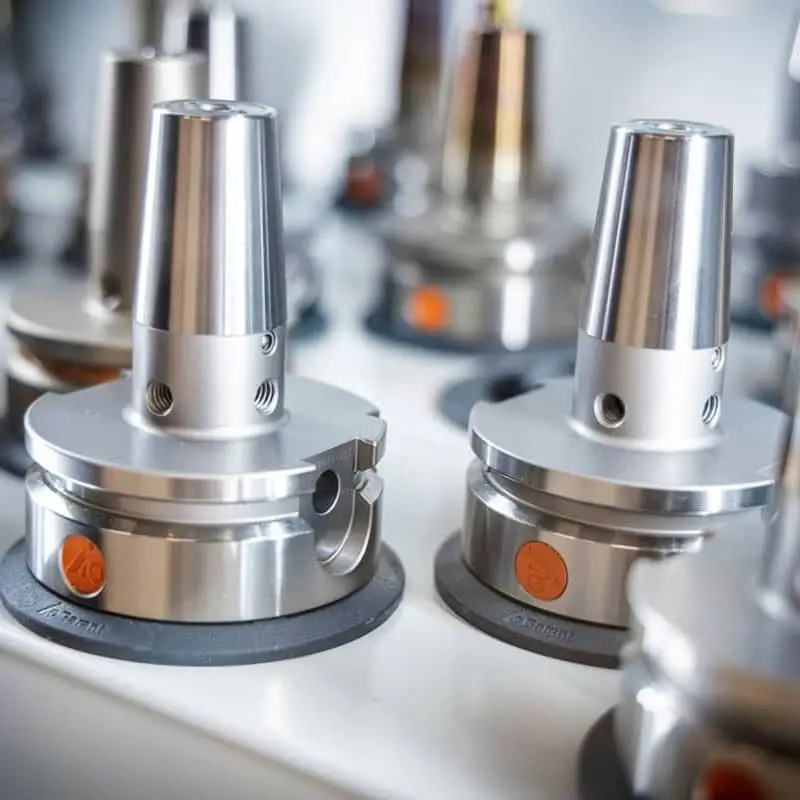
Radio localization in a metallic environment is a challenge in itself. Metal changes the RFID radiation pattern and the frequency of the waves.
Neosid has been offering innovative transponders for identification in metallic environments for 10 years: RFID transponders with a soft magnetic ferrite core. Ferrites are electrically non-conductive or poorly conductive ceramic materials that have a high magnetic conductivity. Neosid has been an expert in the manufacture of electronic components since 1933. In the 1930s, this included antenna rods for the first radio receivers – for which ferrites were used, among other materials.
The ferrite core that Neosid uses for the inlays of RFID transponders has high strength, high resistance to mechanical stress and chemical substances as well as high heat resistance. The ferrite cores are manufactured by injection molding and are available in many shapes.
Neosid has been offering innovative transponders for identification in metallic environments for 10 years: RFID transponders with a soft magnetic ferrite core. Ferrites are electrically non-conductive or poorly conductive ceramic materials that have a high magnetic conductivity. Neosid has been an expert in the manufacture of electronic components since 1933. In the 1930s, this included antenna rods for the first radio receivers – for which ferrites were used, among other materials.
The ferrite core that Neosid uses for the inlays of RFID transponders has high strength, high resistance to mechanical stress and chemical substances as well as high heat resistance. The ferrite cores are manufactured by injection molding and are available in many shapes.
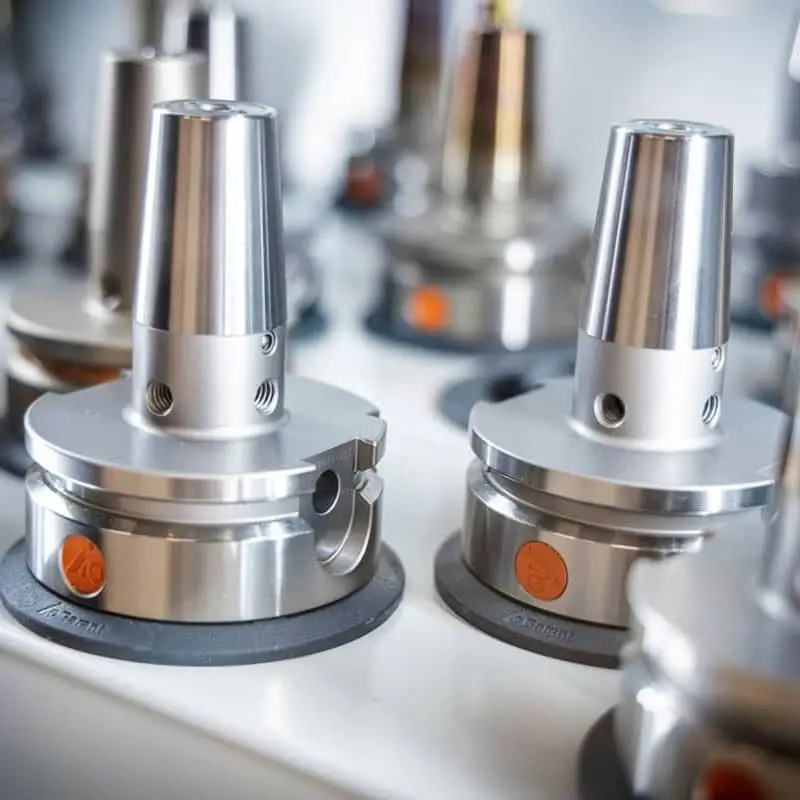
Radio localization in a metallic environment is a challenge in itself. Metal changes the RFID radiation pattern and the frequency of the waves.
Neotag(R) Plug MFG10340
Neotag(R) Plug MFG10340
- Circumference 10.3 mm, height 4 mm
- Passive tag
- Read range 110–210 mm
- For temperatures between -40–+85°C
- For short-term exposure to temperatures up to 275°C
- Durable for 50 years
The RFID tag used by the Hoffmann Group is the Neotag(R) Plug MFG10340 from Neosid. It has a circumference of 10.3 mm and a height of 4 mm, and is designed for a drill hole on the tool with a diameter of 10.0±0.05 and a depth of at least 4.1 mm. The tag is pressed into this hole.
The Neotag(R) Plug MFG10340 is a passive tag without a battery. It receives its ability to transmit and store data from the electromagnetic field of the reader. The signal from the RFID reader is converted into energy. The read range of this tag is short. It is between 110-210 mm in a metal test specimen. Reading is therefore carried out via a point measurement: The reader is brought directly up close to the tag and then activated. Hoffmann uses readers from Industria Oberländer for reading.
The Neotag(R) Plug MFG10340 can withstand ambient temperatures from -40 to +275°C. It is insensitive to moisture and extremely break-proof, i.e. it can withstand being dropped from great heights. At a maximum operating temperature of 55°C, the contents of the memory can be stored for 50 years.
The RFID tag used by the Hoffmann Group is the Neotag(R) Plug MFG10340 from Neosid. It has a circumference of 10.3 mm and a height of 4 mm, and is designed for a drill hole on the tool with a diameter of 10.0±0.05 and a depth of at least 4.1 mm. The tag is pressed into this hole.
The Neotag(R) Plug MFG10340 is a passive tag without a battery. It receives its ability to transmit and store data from the electromagnetic field of the reader. The signal from the RFID reader is converted into energy. The read range of this tag is short. It is between 110-210 mm in a metal test specimen. Reading is therefore carried out via a point measurement: The reader is brought directly up close to the tag and then activated. Hoffmann uses readers from Industria Oberländer for reading.
The Neotag(R) Plug MFG10340 can withstand ambient temperatures from -40 to +275°C. It is insensitive to moisture and extremely break-proof, i.e. it can withstand being dropped from great heights. At a maximum operating temperature of 55°C, the contents of the memory can be stored for 50 years.
Neotag(R) Plug MFG10340
- Circumference 10.3 mm, height 4 mm
- Passive tag
- Read range 110–210 mm
- For temperatures between -40–+85°C
- For short-term exposure to temperatures up to 275°C
- Durable for 50 years
Interview with Nicolas Frank, Marion Schwenk and Yilmaz Benzer
Transparency for All Tools
RFID & Wireless IoT Global spoke to Nicolas Frank and Marion Schwenk from the Hoffmann Group and Yilmaz Benzer from Neosid about connected manufacturing and RFID tags.
Interview
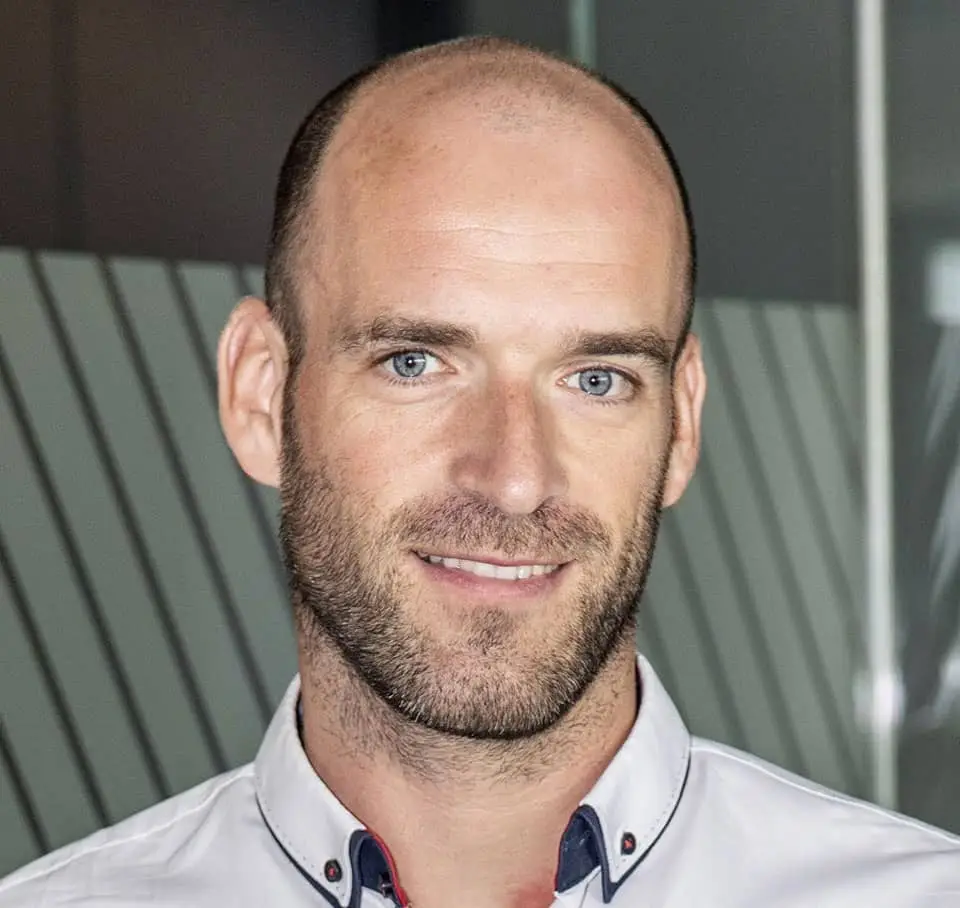
Nicolas Frank is the Team Lead of Digital Manufacturing at the Hoffmann Group.
1. There are many tool manufacturers; what makes the Hoffmann Group stand out?
Nicolas Frank: Apart from the high quality of our tools, it is definitely the close and trustworthy customer relations. There's no other way to put it. We have a very strong field service. For major customers, a Hoffmann consultant is sometimes present on-site once a week. We have a total of 1,400 consultants, and the close contact with the companies enables us to gather a lot of practical knowledge about the individual work areas. We benefit greatly from this. The first digital solution ideas, for example, were developed together with customers.
2. Who are your customers?
Marion Schwenk: Our customers are companies of all sizes. In the field of digital manufacturing solutions, however, we have a clear focus on small and medium-sized companies in the metalworking and machining industries. Our sales staff maintain personal contact with our customers, and if customers need indepth specialist advice, other proven specialists are available to provide support. In machining, for example, these are application engineers who have often worked on the machine themselves for many years as machinists. In the other areas, these are factory equipment consultants and experts in personal protective equipment. This enables us to offer solutions that noticeably increase the customer's productivity.
1. There are many tool manufacturers; what makes the Hoffmann Group stand out?
Nicolas Frank: Apart from the high quality of our tools, it is definitely the close and trustworthy customer relations. There's no other way to put it. We have a very strong field service. For major customers, a Hoffmann consultant is sometimes present on-site once a week. We have a total of 1,400 consultants, and the close contact with the companies enables us to gather a lot of practical knowledge about the individual work areas. We benefit greatly from this. The first digital solution ideas, for example, were developed together with customers.
2. Who are your customers?
Marion Schwenk: Our customers are companies of all sizes. In the field of digital manufacturing solutions, however, we have a clear focus on small and medium-sized companies in the metalworking and machining industries. Our sales staff maintain personal contact with our customers, and if customers need indepth specialist advice, other proven specialists are available to provide support. In machining, for example, these are application engineers who have often worked on the machine themselves for many years as machinists. In the other areas, these are factory equipment consultants and experts in personal protective equipment. This enables us to offer solutions that noticeably increase the customer's productivity.
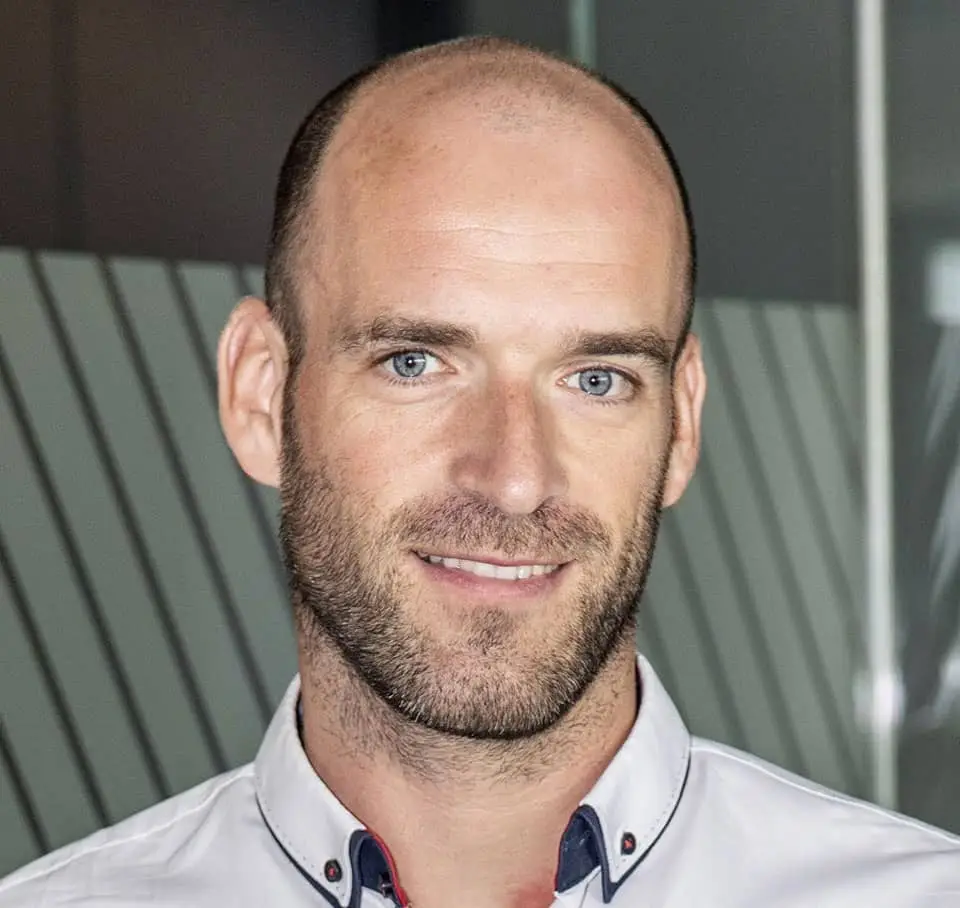
Nicolas Frank is the Team Lead of Digital Manufacturing at the Hoffmann Group.
Connected Manufacturing and Tagged Tools
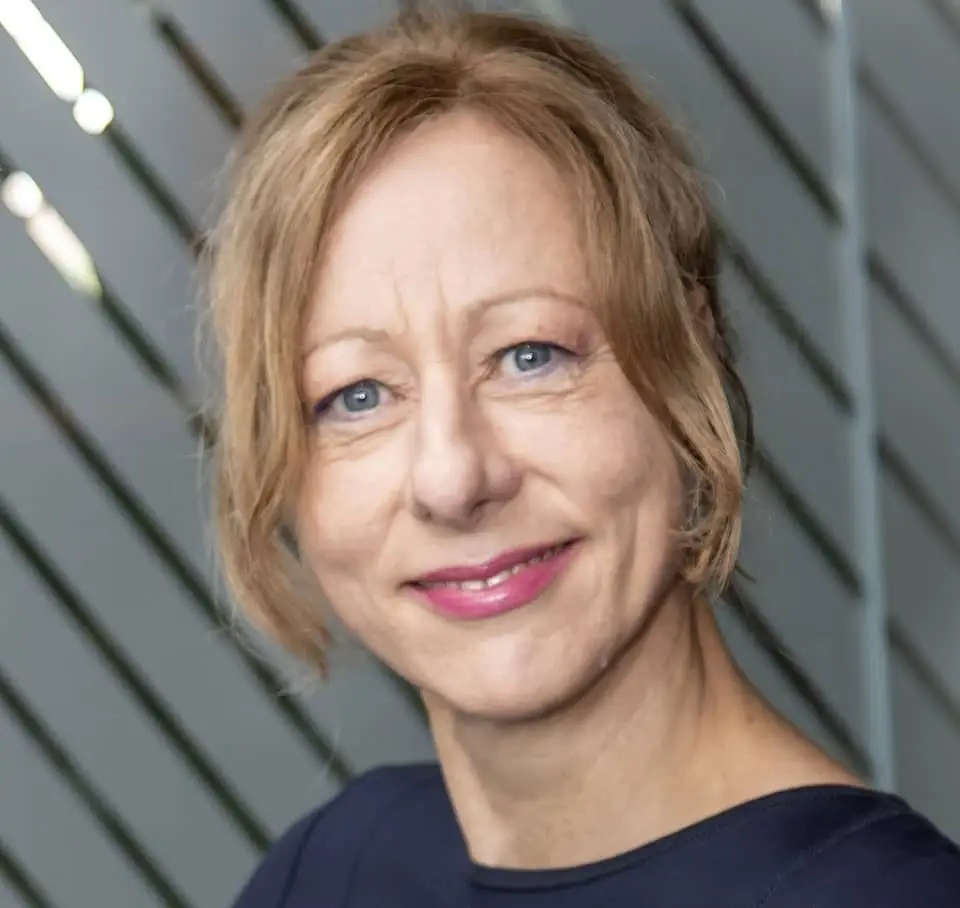
Marion Schwenk is Senior Public Relations Manager at the Hoffmann Group.
3. What is the story behind the Connected Manufacturing software tool?
Frank: In conversations with customers a few years ago, two things kept coming up as concerns or trends. The first is digitalization. For many customers, it is an abstract concept that keeps them very busy. Everyone wants to digitize something, even if there is no concrete use case yet. The second is the strong paper-based nature of production. Since everything is recorded on individual pieces of paper or punched cards, there is no overview, and the entire production process is somewhat disorganized. Production expertise is tied to individual people and not anchored across the board. This is why we considered digitizing and expanding the services that we had previously provided purely through the tool trade.
4. The solution includes tagged tools. Was it clear from the start that HF RFID was the right technology for the identification of tools?
Frank: Yes, in fact. For our customers, process reliability is the most important thing, and RFID is simply more robust than optical options. The chip is also incredibly durable. The small size of the chip and the simple pressfit application were two other important decision criteria.
3. What is the story behind the Connected Manufacturing software tool?
Frank: In conversations with customers a few years ago, two things kept coming up as concerns or trends. The first is digitalization. For many customers, it is an abstract concept that keeps them very busy. Everyone wants to digitize something, even if there is no concrete use case yet. The second is the strong paper-based nature of production. Since everything is recorded on individual pieces of paper or punched cards, there is no overview, and the entire production process is somewhat disorganized. Production expertise is tied to individual people and not anchored across the board. This is why we considered digitizing and expanding the services that we had previously provided purely through the tool trade.
4. The solution includes tagged tools. Was it clear from the start that HF RFID was the right technology for the identification of tools?
Frank: Yes, in fact. For our customers, process reliability is the most important thing, and RFID is simply more robust than optical options. The chip is also incredibly durable. The small size of the chip and the simple pressfit application were two other important decision criteria.
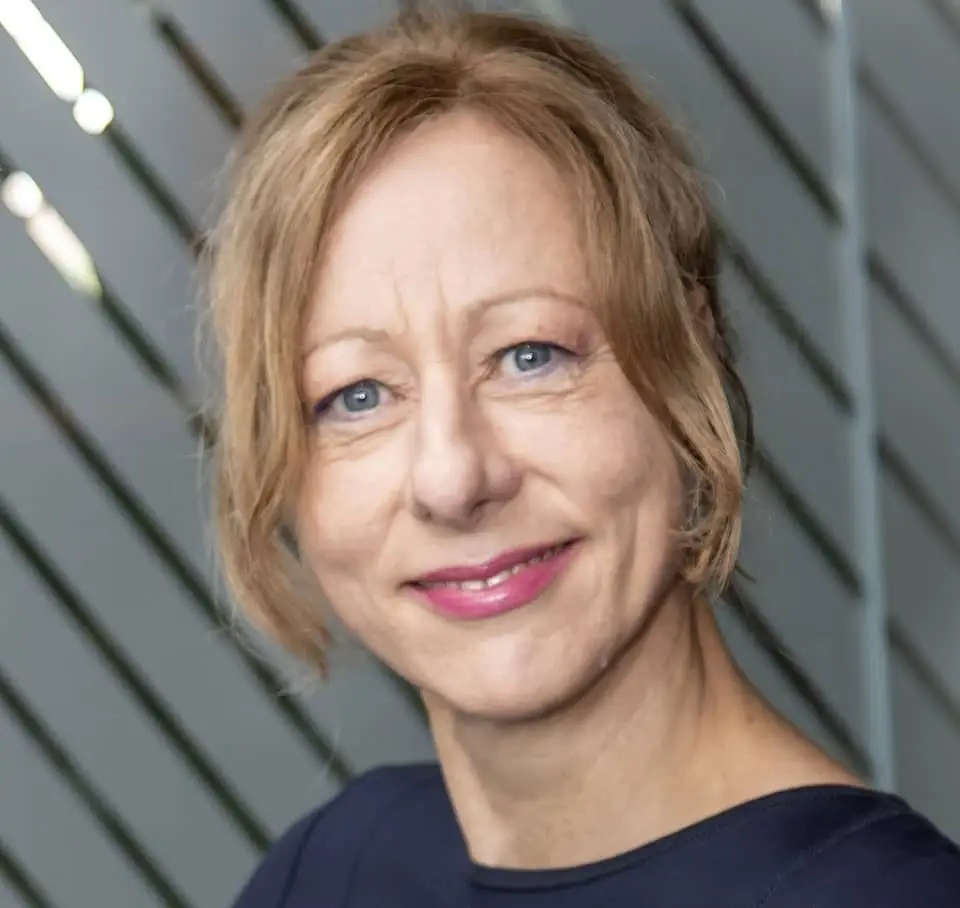
Marion Schwenk is Senior Public Relations Manager at the Hoffmann Group.
Miniaturized Transponders from Neosid
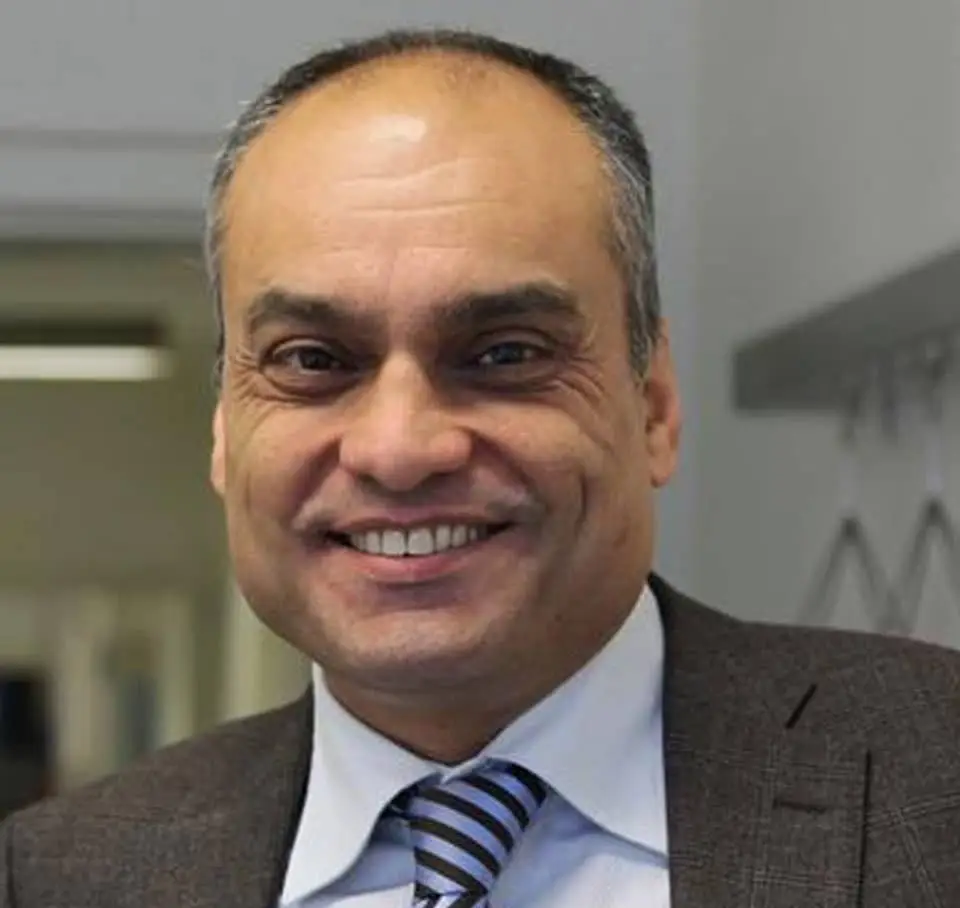
Yilmaz Benzer is Managing Director of Neosid Pemetzrieder
5. Is that why the Neotag(R) Plug MFG10340 was chosen?
Yilmaz Benzer: Neosid caught the Hoffmann Group's attention with its miniaturized transponders. We had demonstrated a very robust transponder that was convincing and for which we could guarantee availability. This led to the collaboration. We adapted the antenna for Hoffmann, which was not a problem. The overall package was simply a very good fit.
6. The Neosid plugs are part of the Hoffmann design, so they don't shine in the usual Neosid blue. How did this come about?
Benzer: We have produced a customized version of the 10mm plug for Hoffmann. The easy-to-insert plug-in housing is orange and features the Hoffmann logo. This is something we do quite often. Many customers want to use their own transponder in their applications. For this reason, they often use the 10 mm or 8 mm plug-in housing and a customer-specific logo. In tool-making, we are increasingly focusing on being able to make such adaptations for customers.
7. When customers purchase holders from the Hoffmann Group, are they immediately chipped so that Connected Manufacturing can be implemented without any problems?
Frank: That is our goal, but at the moment it is not yet the case. The typical case is that customers have already bought several thousand tool holders without a chip. If a customer opts for the Connected Manufacturing software product, these can be chipped without any problems.
8. Is it time-consuming to apply the tags?
Benzer: Not at all. The size of the hole on the tool components is explained in the transponder data sheet. It is often already there anyway. The transponders are supplied in a blister pack and simply pressed into the drill hole. Assigning the ID and creating the object in tool management then takes a little longer.
9. How has Connected Manufacturing been received?
Schwenk: Companies are interested, but are still a little cautious. However, the benefits really speak for themselves. Mühlhoff Umformtechnik GmbH installed Connected Manufacturing in 2020 and reduced its downtimes by 30% overall.1
As part of the introduction, Mühlhoff put all processes to the test. This was a somewhat larger project. The development is still in its infancy, but already has positive results.
10. How has the pandemic affected your customers?
Schwenk: Differently. Despite the Corona crisis, production has continued for many customers. When the order situation dropped, this meant that fewer or no extra shifts had to be worked. Many of our customers are always working at the limit. Anything that makes their work more efficient is a real help to them. However, the introduction of Connected Manufacturing is often a comprehensive project that is not done on the side.
11. What is the challenge when installing Connected Manufacturing?
Frank: In general, Connected Manufacturing is designed to be modular and as lean as possible, so that no major initial outlay is required. Nevertheless, some preliminary work is necessary if transparency is to be achieved across the entire manufacturing process. This applies to the CAM database, for example. Structures may first have to be created here, for instance, by naming the individual tools.
12. How has Mühlhoff Umformtechnik GmbH implemented this?
Schwenk: Our employees were on-site at the start and were of course always there when support was needed. Mühlhoff also assigned an internal employee to streamline and optimize the production processes for three months. Overall, the employees were very motivated because they were able to work with tablets from then on and supported the processes.
13. Smart tools are a central component of Industry 4.0. What do German SMEs think about Industry 4.0?
Benzer: Anyone who comes to us is already convinced of RFID. From our point of view, RFID has arrived as a technology; demand has stabilized. There is a strong trend in tool technology and medical technology. Readability with a smartphone is an important topic at the moment.
Frank: From our point of view, things are a little different. Our target customer is the classic medium-sized company with between 2 and 30 production machines, and in this group the level of digitalization is frankly below average. A change is often only possible with a generation shift in management.
14. Is there an intermediate step that companies can take to make it easier to implement Connected Manufacturing?
Frank: One of the reasons why Connected Manufacturing is modular is so that customers can set it up according to their own level of digitalization and slowly during operation. For example, it can take over order management tasks. This is a good introduction to Connected Manufacturing, especially for customers who still work with a routing card in production and are more paper-driven. Other customers already have a sophisticated ERP system and would be able to jump straight into the tool management phase. It really is suitable for everyone.
5. Is that why the Neotag(R) Plug MFG10340 was chosen?
Yilmaz Benzer: Neosid caught the Hoffmann Group's attention with its miniaturized transponders. We had demonstrated a very robust transponder that was convincing and for which we could guarantee availability. This led to the collaboration. We adapted the antenna for Hoffmann, which was not a problem. The overall package was simply a very good fit.
6. The Neosid plugs are part of the Hoffmann design, so they don't shine in the usual Neosid blue. How did this come about?
Benzer: We have produced a customized version of the 10mm plug for Hoffmann. The easy-to-insert plug-in housing is orange and features the Hoffmann logo. This is something we do quite often. Many customers want to use their own transponder in their applications. For this reason, they often use the 10 mm or 8 mm plug-in housing and a customer-specific logo. In tool-making, we are increasingly focusing on being able to make such adaptations for customers.
7. When customers purchase holders from the Hoffmann Group, are they immediately chipped so that Connected Manufacturing can be implemented without any problems?
Frank: That is our goal, but at the moment it is not yet the case. The typical case is that customers have already bought several thousand tool holders without a chip. If a customer opts for the Connected Manufacturing software product, these can be chipped without any problems.
8. Is it time-consuming to apply the tags?
Benzer: Not at all. The size of the hole on the tool components is explained in the transponder data sheet. It is often already there anyway. The transponders are supplied in a blister pack and simply pressed into the drill hole. Assigning the ID and creating the object in tool management then takes a little longer.
9. How has Connected Manufacturing been received?
Schwenk: Companies are interested, but are still a little cautious. However, the benefits really speak for themselves. Mühlhoff Umformtechnik GmbH installed Connected Manufacturing in 2020 and reduced its downtimes by 30% overall.1
As part of the introduction, Mühlhoff put all processes to the test. This was a somewhat larger project. The development is still in its infancy, but already has positive results.
10. How has the pandemic affected your customers?
Schwenk: Differently. Despite the Corona crisis, production has continued for many customers. When the order situation dropped, this meant that fewer or no extra shifts had to be worked. Many of our customers are always working at the limit. Anything that makes their work more efficient is a real help to them. However, the introduction of Connected Manufacturing is often a comprehensive project that is not done on the side.
11. What is the challenge when installing Connected Manufacturing?
Frank: In general, Connected Manufacturing is designed to be modular and as lean as possible, so that no major initial outlay is required. Nevertheless, some preliminary work is necessary if transparency is to be achieved across the entire manufacturing process. This applies to the CAM database, for example. Structures may first have to be created here, for instance, by naming the individual tools.
12. How has Mühlhoff Umformtechnik GmbH implemented this?
Schwenk: Our employees were on-site at the start and were of course always there when support was needed. Mühlhoff also assigned an internal employee to streamline and optimize the production processes for three months. Overall, the employees were very motivated because they were able to work with tablets from then on and supported the processes.
13. Smart tools are a central component of Industry 4.0. What do German SMEs think about Industry 4.0?
Benzer: Anyone who comes to us is already convinced of RFID. From our point of view, RFID has arrived as a technology; demand has stabilized. There is a strong trend in tool technology and medical technology. Readability with a smartphone is an important topic at the moment.
Frank: From our point of view, things are a little different. Our target customer is the classic medium-sized company with between 2 and 30 production machines, and in this group the level of digitalization is frankly below average. A change is often only possible with a generation shift in management.
14. Is there an intermediate step that companies can take to make it easier to implement Connected Manufacturing?
Frank: One of the reasons why Connected Manufacturing is modular is so that customers can set it up according to their own level of digitalization and slowly during operation. For example, it can take over order management tasks. This is a good introduction to Connected Manufacturing, especially for customers who still work with a routing card in production and are more paper-driven. Other customers already have a sophisticated ERP system and would be able to jump straight into the tool management phase. It really is suitable for everyone.
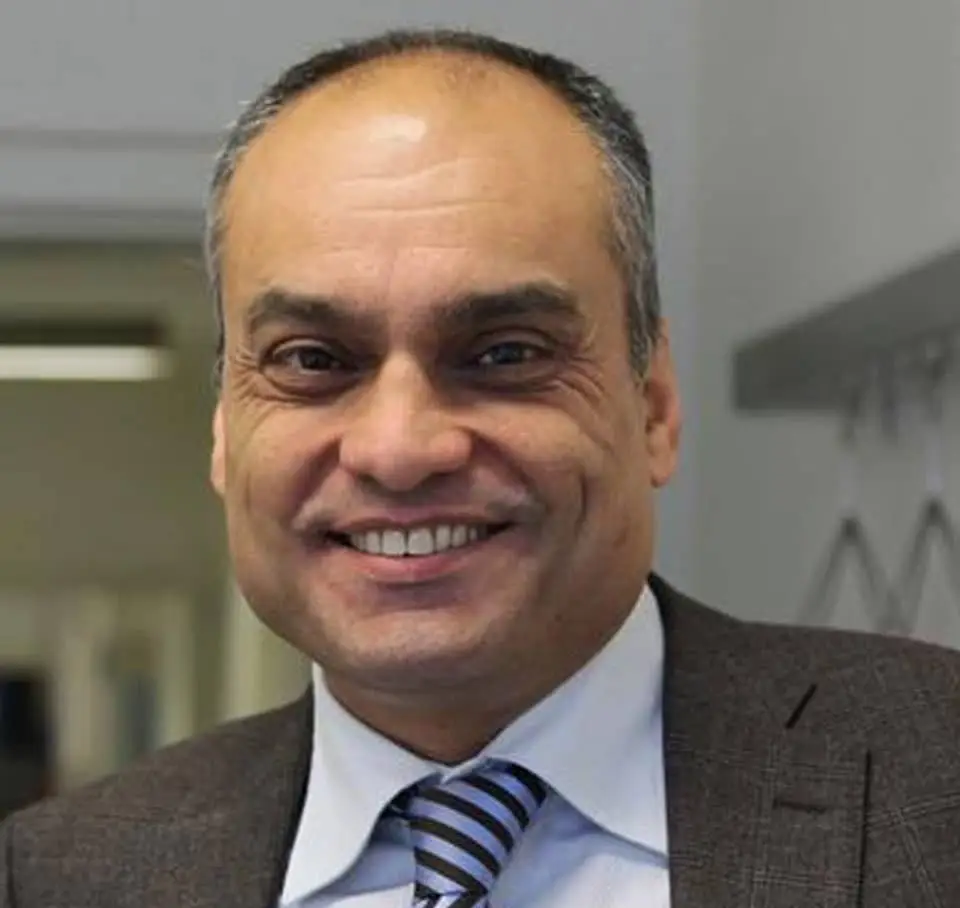
Yilmaz Benzer is Managing Director of Neosid Pemetzrieder