Fit for tomorrow: the emergence of a SkillMill for Industry 4.0
M.Sc. Andreas Wagner and M.Sc. Simon Lamoth, research associates at the Chair of Machine Tools and Control Engineering (WSKL) at RPTU Kaiserslautern-Landau, have modernized a 60-year-old milling machine through retrofitting.
The use of a digital twin enables skill-based production, optimized manufacturing processes, and integration into Industry 4.0 environments. In the future, SkillMill could be integrated into data spaces such as Gaia-X or Manufacturing-X to make its skills available to other companies.
When Machines Learn to Think Differently
The SkillMill was developed from a 1.5-ton milling machine built by Friedrich Korradi. It was upgraded with new feed motors, a CNC controller, and a digital twin – enabling it to operate in a skill-based manner. This means that functions like milling rectangular or circular pockets can now be accessed and easily adapted via an OPC UA interface.
The digital twin takes over many tasks traditionally handled by a classic CAM system – it calculates energy requirements, estimates costs, selects optimal tool paths, and checks for collisions. It also provides essential data for quotations and production planning.
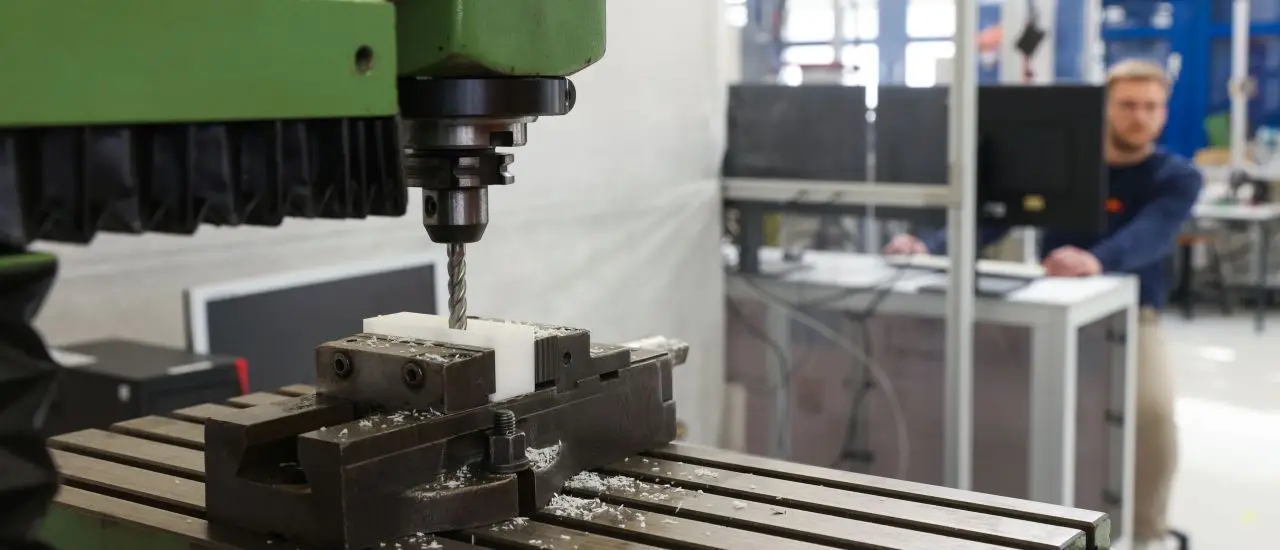
Researchers at RPTU Kaiserslautern-Landau showcased this process using the "rectangular pocket" skill, visually simulating and analyzing the milling operation for a parameterized pocket. (Picture: RPTU Kaiserslautern-Landau)
Skill Adapter and OPC UA
To integrate skill-based production into existing machines, an interface is needed that enables communication between software and hardware. This is where the Skill Adapter comes into play.
The Skill Adapter is a software-based solution that integrates machines into a skill-based production environment. An OPC UA adapter acts as the central interface for communication and control. Based on this, different decision-making algorithms can be applied to optimize machine control efficiently.
The Skill Adapter is especially advantageous when retrofitting older machines originally designed for manual operation. Instead of costly hardware upgrades, software can be used to implement automated, skill-based control. With the retrofitting of motors and CNC systems, the machine becomes fully automated.
Alternatively, manually operated machines can also be integrated into the skill-based production process using the adapter – allowing operators to be purposefully included. The use of OPC UA as a standardized interface ensures flexible and interoperable communication within the Industry 4.0 architecture.
The Feasibility Check
The feasibility check determines whether a planned manufacturing step can be successfully executed under the given conditions. It analyzes essential factors such as potential collisions, tool selection, feed rate, spindle speed, time requirements, and energy consumption. A central role is played by collision simulation, which ensures process safety before actual production begins.
In this early phase, all relevant parameters are already identified and evaluated. For example, based on the geometry of the component, a suitable tool is selected, from which the optimal spindle speed can then be derived.
The results of the feasibility check provide a clear decision: is the planned manufacturing step feasible or not? At the same time, time and energy requirements can be calculated, enabling an economic assessment of the production task.
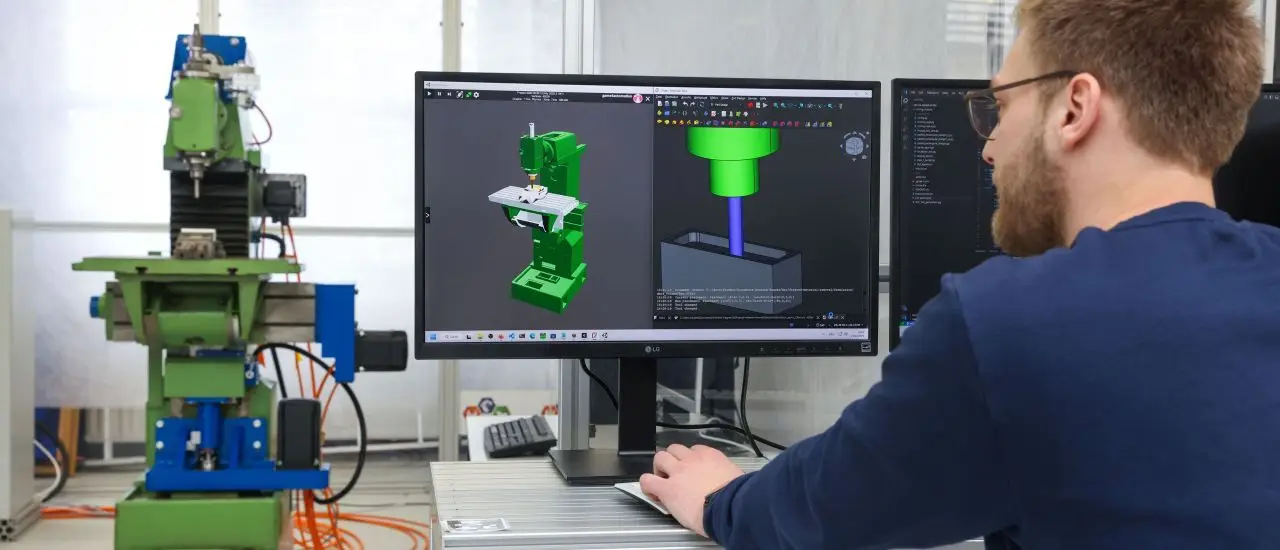
Feasibility check passed: The simulation shows that the “Rectangular Pocket Skill” can be performed safely – the milling process can begin. (Image: RPTU Kaiserslautern-Landau)
Automated Parameter Calculation in the Background
The determination of manufacturing parameters, such as spindle speed, is based on the transmitted geometry data and is carried out automatically. As soon as a CAD file containing the relevant dimensions of a milling contour—such as width, length, and depth—is fed into the system, the software selects a suitable tool. The optimal spindle speed is then determined based on this tool and the material to be processed.
These values are calculated within a multi-agent system, in which specialized software components make decentralized decisions.
Each agent is responsible for a specific task, such as selecting the tools or defining machining parameters. A material removal simulation continuously updates the state of the workpiece, allowing subsequent machining steps to be optimally planned.
Skill-Based Production vs. Conventional CNC Milling
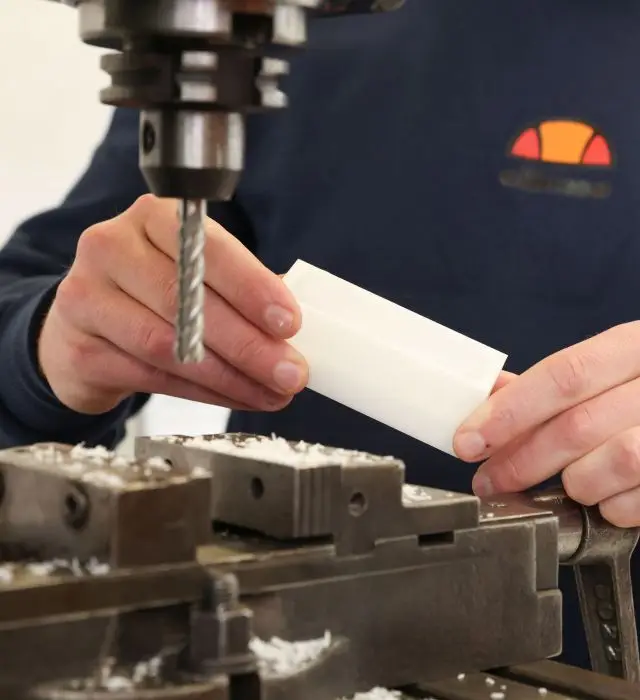
Task completed! (Image: RPTU Kaiserslautern-Landau)
In a conventional manufacturing process, production planning begins with the analysis of technical drawings to define the desired component. Programming machine code is required to carry out a specific operation, such as milling a rectangular pocket.
If no comparable code exists, a complete reprogramming is necessary, which requires in-depth knowledge of G-codes and machine commands. This process is time-consuming, especially when dealing with custom customer requirements.
The skill-based approach reduces this effort. Key parameters such as length, width, and depth of a rectangular pocket are predefined and stored in a standardized interface, enabling the machine to automatically make the necessary adjustments to tools and processes. This eliminates manual code creation, making the manufacturing process more flexible and efficient.
In a conventional manufacturing process, production planning begins with the analysis of technical drawings to define the desired component. Programming machine code is required to carry out a specific operation, such as milling a rectangular pocket.
If no comparable code exists, a complete reprogramming is necessary, which requires in-depth knowledge of G-codes and machine commands. This process is time-consuming, especially when dealing with custom customer requirements.
The skill-based approach reduces this effort. Key parameters such as length, width, and depth of a rectangular pocket are predefined and stored in a standardized interface, enabling the machine to automatically make the necessary adjustments to tools and processes. This eliminates manual code creation, making the manufacturing process more flexible and efficient.
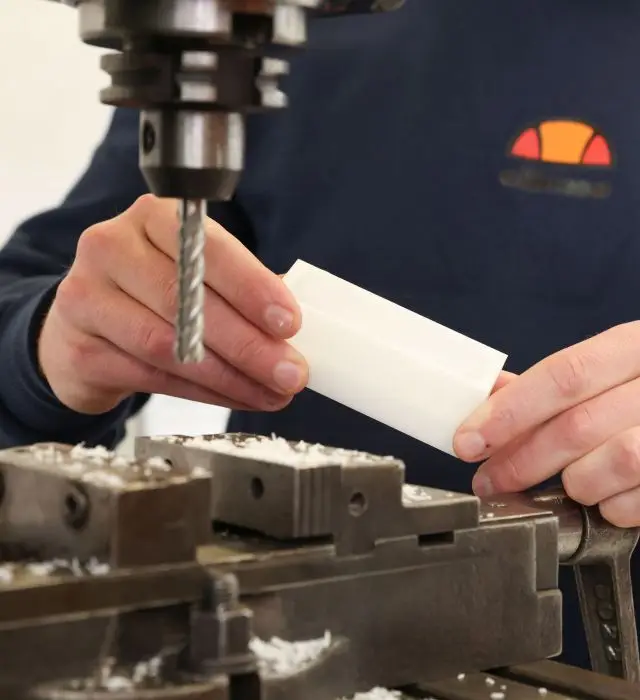
Task completed! (Image: RPTU Kaiserslautern-Landau)
Interview with Andreas Wagner
1. How easy is it to retrofit a machine into a SkillMachine?
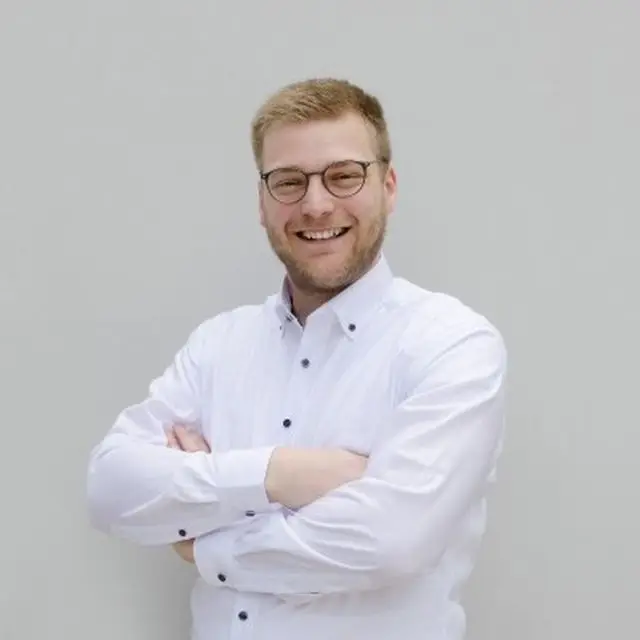
Andreas Wagner is researcher at the RPTU Laiserslautern-Landau.
Andreas Wagner: That depends on the equipment of the machine and the intended goal. Full automation isn't always necessary. In the first step, it's sufficient to digitally describe the machine and make it controllable. This can also be implemented for manually operated machines.
In our case, we equipped the machine with a CNC controller and feed motors, which required significantly more effort. In return, an "autonomous" operation via skills becomes possible.
In any case, a so-called Skill Adapter is required – a piece of software that makes the machine accessible on the network via a standardized interface (usually OPC UA).
Andreas Wagner: That depends on the equipment of the machine and the intended goal. Full automation isn't always necessary. In the first step, it's sufficient to digitally describe the machine and make it controllable. This can also be implemented for manually operated machines.
In our case, we equipped the machine with a CNC controller and feed motors, which required significantly more effort. In return, an "autonomous" operation via skills becomes possible.
In any case, a so-called Skill Adapter is required – a piece of software that makes the machine accessible on the network via a standardized interface (usually OPC UA).
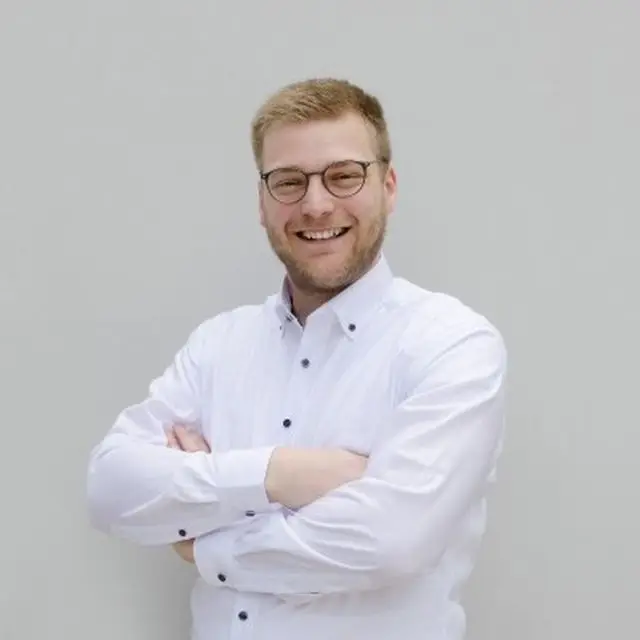
Andreas Wagner is researcher at the RPTU Laiserslautern-Landau.
2. Does retrofitting to a SkillMachine require adapting the entire infrastructure and machine park?
Andreas Wagner: No, a skill-based system can be introduced and expanded step by step. At a minimum, you need one machine with a Skill Adapter, a control software unit, and software that can generate production plans.
We’ve developed the latter two (control software and production planning) as a single plug-in for a CAD system (Siemens NX and Fusion 360). In other words: a Skill Adapter for one machine plus a CAD plug-in is sufficient for a minimum viable product (MVP), which can run in parallel with the existing infrastructure.
3. What specific advantages does the Skill approach offer for controlling and maintaining the milling machine?
Andreas Wagner: Since the skills independently plan and verify the manufacturing process, the manual CAM process is completely eliminated. Only the geometric information from the CAD model is extracted and passed on to the corresponding skills. This saves an enormous amount of time and can be fully automated. In our research, this already works for a wide range of standard features.
Because the Skill Adapters, or rather digital twins, of the machines can be freely programmed and adapted to customer requirements, their intelligence can be increased as needed. For example, it’s possible to integrate algorithms for predictive maintenance and similar use cases.
4. What challenges are there in retrofitting older machines with SkillMill technology?
Andreas Wagner: The milling machine we presented is an extreme example. It required feed motors, new ball screws, a CNC controller, and various structural modifications. However, many machines already have feed motors and CNC controllers, which significantly reduces the hardware-related challenges.
In that case, the biggest challenge is implementing the transmission of the program code and enabling communication between the Skill Adapter and the machine. If no CAD models of the machine exist, it's also a challenge to implement collision simulation for that machine within the digital twin.
About the Project
The project is part of ongoing research within the SmartFactory-KL, a network of around 50 partners from industry and academia working together on the advancement of Industry 4.0 technologies.