App-Based Ordering
A Disparate Range of Systems
In common with many organizations, the IT systems of Paracelsus-Kliniken had evolved in a piecemeal way over many years to comprise a wide range of different systems and applications. Procurement logistics and purchasing were two areas in particular where the group had to contend with a fragmented technology landscape.
As of 2019, the hospital group had three separate materials management systems operating with different master data and functions, while some sites did not have access to dedicated systems at all. Orders were placed by phone, paper and fax, while materials were recorded manually in spreadsheets. This method was inefficient, time-consuming and prone to human error. The hospitals also had no overview of their consumption of goods, no consistent purchasing processes and little cost control.
“The situation was pure data chaos,” recalls Anjali Sherlin Menezes, Acting Head of Purchasing Division, Paracelsus Group.
One App for a Wide Range of Processes
A new solution was clearly needed to enhance ordering. A project team was created, which determined the need for a central database, with standardized article numbers that would enable digital, bundled ordering processes across all sites. Greater transparency and accuracy of data was also a key goal as this would allow the purchasing department to negotiate the best payment and delivery terms for the entire group.
To support the project’s implementation, Paracelsus-Kliniken chose Comed, a Zebra Registered ISV, as its software partner, a specialist in supply chain management and e-commerce solutions in the healthcare sector. Comed’s recommendation to create a versatile solution was compelling. It recommended an advanced cloud architecture to enable app-based orders and electronic data exchange with suppliers while offering a seamless connection to the hospital information system (HIS).
To give hospital staff easy access to the features they need in their everyday work, Comed developed a customized Android app installed on mobile devices. The devices would also manage barcode scanning to record used or delivered materials at the touch of a button.
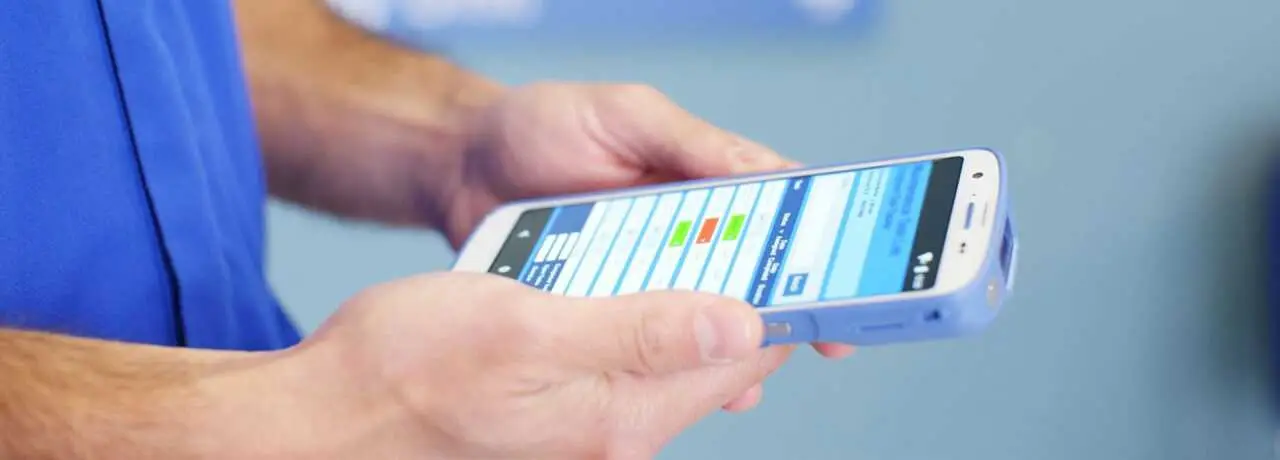
To give hospital staff easy access to the features they need in their everyday work, Comed developed a customized Android app installed on mobile devices.
Deploying Mobile Computers
Selecting the Right Hardware
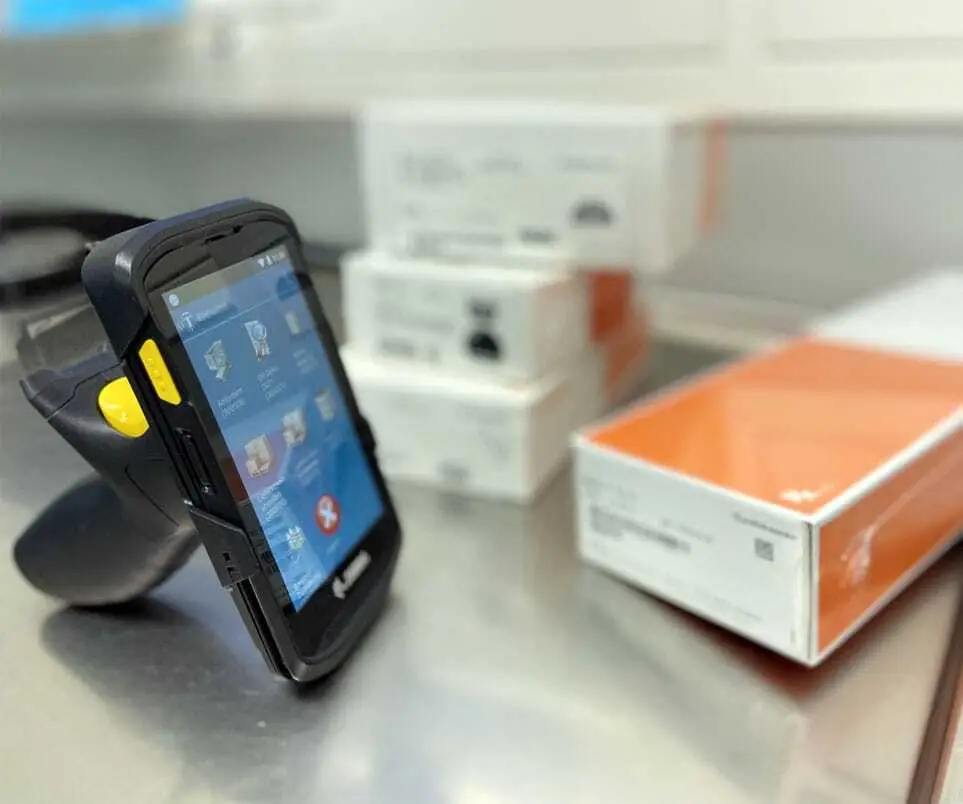
The Paracelsus Group opted for three devices from Zebra’s Android portfolio.
With the aim of finding the best devices, the Paracelsus Group compared products from three manufacturers in a comprehensive benchmark study. It opted for three devices from Zebra’s Android portfolio: the TC21-HC mobile computer (Wi-Fi connectivity), TC26-HC mobile computer (Wi-Fi and cellular connectivity) and TC52-HC mobile computer. The devices were selected for several reasons.
With item scanning essential to the project, the powerful integral scanner available in each Zebra device was seen as a major advantage. So, too, was the full-shift battery life, which can extend to virtually continuous operation by swapping batteries. In addition, both the TC21-HC/ TC26-HC and TC52-HC have a familiar user interface, but each is built rugged to survive the knocks and drops of life in busy clinics.
What’s more, the devices can withstand regular disinfection by powerful infection control chemicals. Comed helped to deploy the devices and took over their management and maintenance.
With the aim of finding the best devices, the Paracelsus Group compared products from three manufacturers in a comprehensive benchmark study. It opted for three devices from Zebra’s Android portfolio: the TC21-HC mobile computer (Wi-Fi connectivity), TC26-HC mobile computer (Wi-Fi and cellular connectivity) and TC52-HC mobile computer. The devices were selected for several reasons.
With item scanning essential to the project, the powerful integral scanner available in each Zebra device was seen as a major advantage. So, too, was the full-shift battery life, which can extend to virtually continuous operation by swapping batteries. In addition, both the TC21-HC/ TC26-HC and TC52-HC have a familiar user interface, but each is built rugged to survive the knocks and drops of life in busy clinics.
What’s more, the devices can withstand regular disinfection by powerful infection control chemicals. Comed helped to deploy the devices and took over their management and maintenance.
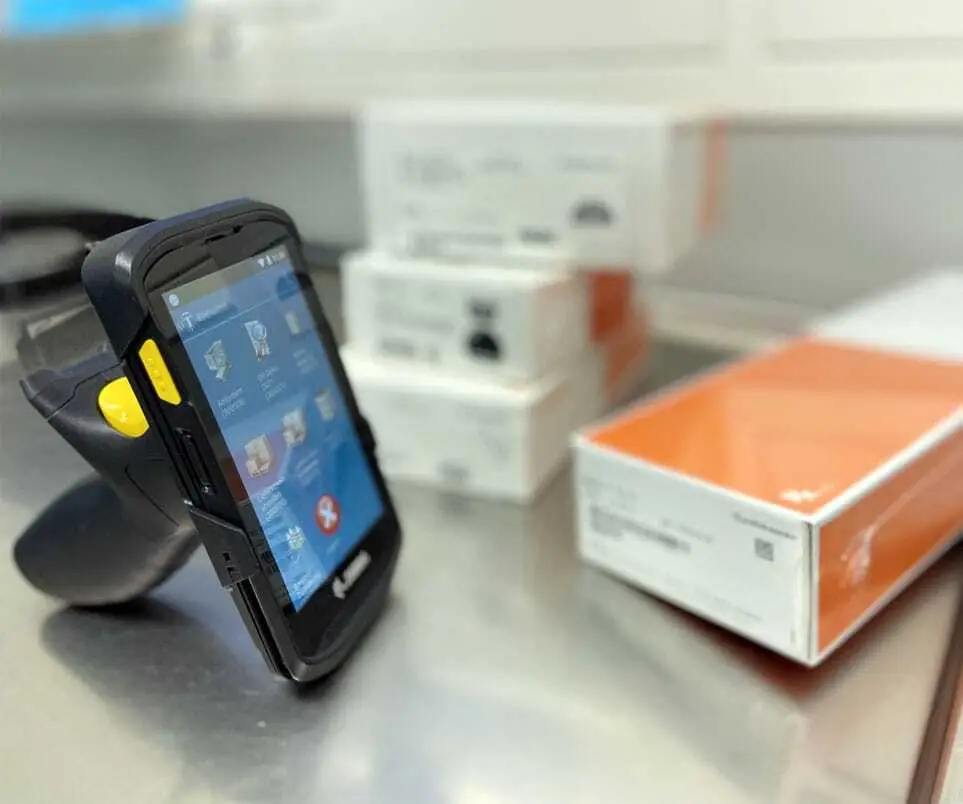
The Paracelsus Group opted for three devices from Zebra’s Android portfolio.
Agile Rollout During the Pandemic
Paracelsus Group rolled out the central materials management system across the group in 15 months, despite the COVID-19 pandemic. Implementation began in the rehab clinics in March 2020.
The emergency care clinics followed at intervals of often only four weeks, including training of 50 to 100 users per site. In some cases, remote rollouts were required. But thanks to the use of Agile project management methodologies to accelerate delivery, the system successfully went live in June 2021.
"Zebra’s mobile computers were selected due to their powerful integral scanner, full-shift battery life, a familiar user interface, and the ability to withstand harsh environments."
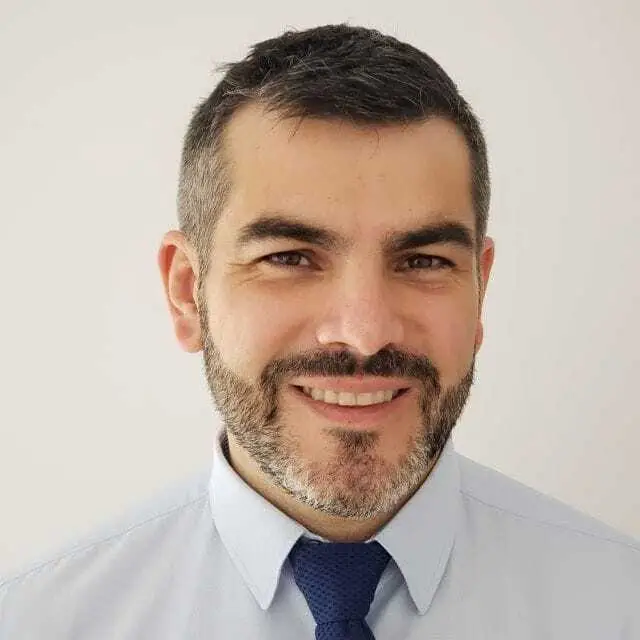
Materials Handling
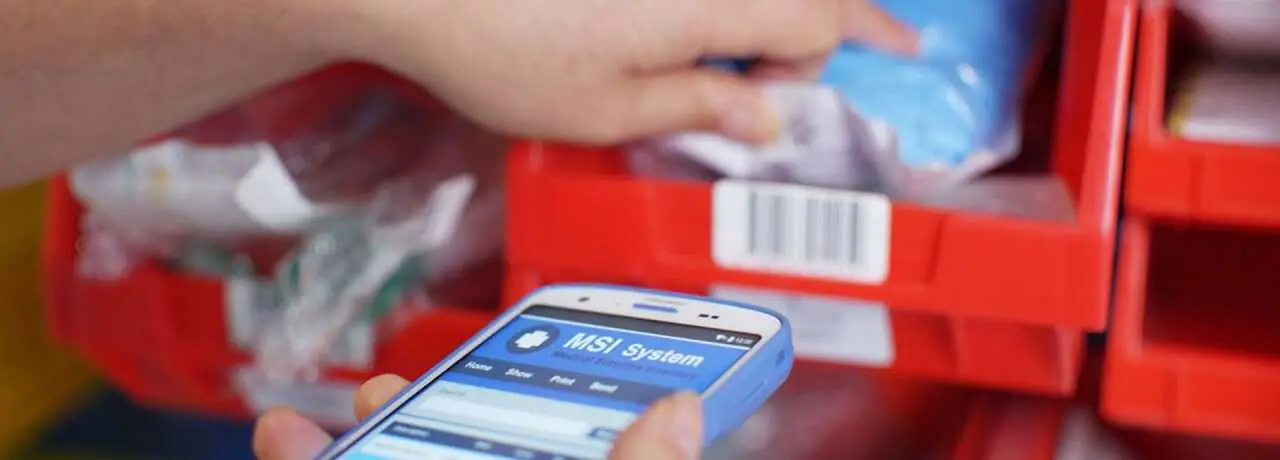
All incoming and outgoing goods are digitally recorded by a scanner.
Materials Handling with Mobile Computers
Zebra mobile computers are deployed anywhere that materials are handled, from goods arrival at the warehouse to wards. For example, all incoming and outgoing goods are digitally recorded by a scanner.
Purchase requisitions for consumables such as bandages and gloves can be scanned and transmitted in seconds directly at the point of need, for example at the ward’s medicine storage cabinet. In the operating theatres, staff use the interface with the HIS to scan and document materials with their batch information.
For example, during surgery, clinicians scan medical devices such as implants or pacemakers to read their unique device identifier (UDI) codes and associate these with a patient’s record.
Real-Time Data and Process Optimization
All data is transferred in real time to the hospital’s information and financial accounting systems. This helps with batch traceability and avoids errors that could occur with manual documentation.
As a process optimization step to avoid additional touching of items for an order, automatic reordering is programmed for some product groups – such as consignment goods – if these materials are used during an operation. The Paracelsus Group has also set up direct interfaces with some of its 400 suppliers.
For example, web shops for physiotherapy, ergotherapy, IT hardware, sanitary, housekeeping and office supplies are seamlessly connected to the ordering platform. Further integrations are being planned.
A Central MMS
Real-Time Data – the Prescription for a Host of Benefits
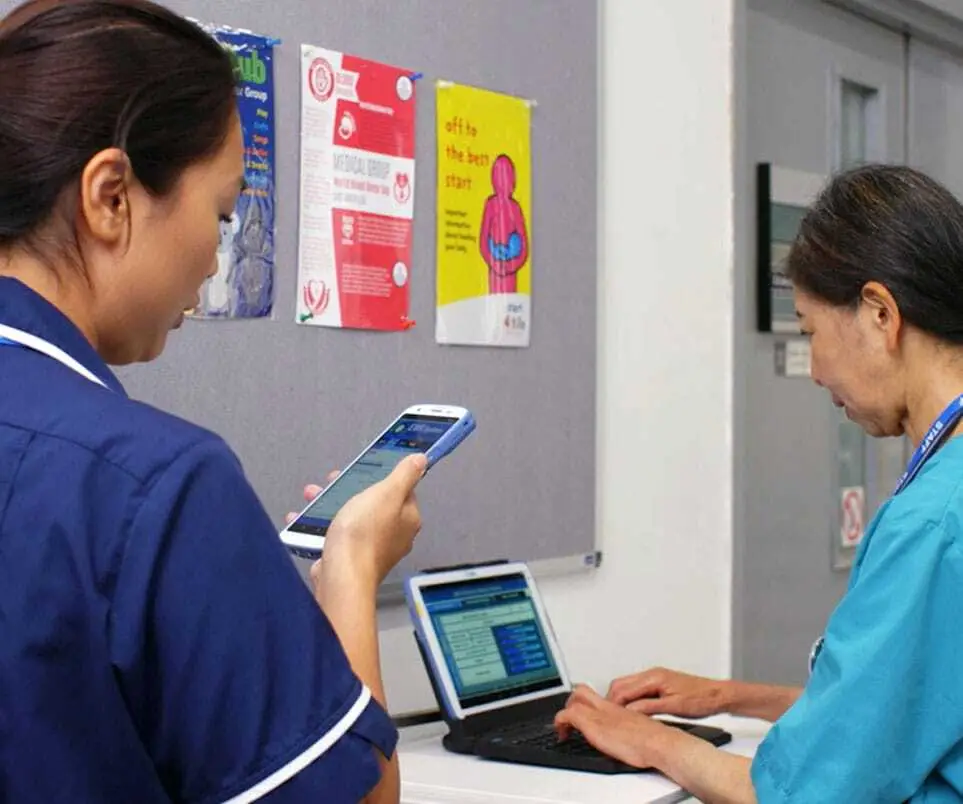
Since all orders are bundled via purchasing, the hospitals and clinics always have an overview of their current stock levels.
The solution has paid for itself in less than 12 months. Using the central merchandise management system has enabled the group to standardize its ordering processes and established rigorous processes for strategic procurement. As a result, the annual ancillary order costs have fallen by a five-figure amount, while procure-to-pay process times have been halved. Since all orders are bundled via purchasing, the hospitals and clinics always have an overview of their current stock levels.
Duplicate orders are avoided and the number of products that must be thrown away due to expired shelf-life dates is minimal. With a real-time view of inventory, the group can also respond flexibly to supply chain problems in the market and quickly find alternatives if a product is not available.
The solution has paid for itself in less than 12 months. Using the central merchandise management system has enabled the group to standardize its ordering processes and established rigorous processes for strategic procurement. As a result, the annual ancillary order costs have fallen by a five-figure amount, while procure-to-pay process times have been halved. Since all orders are bundled via purchasing, the hospitals and clinics always have an overview of their current stock levels.
Duplicate orders are avoided and the number of products that must be thrown away due to expired shelf-life dates is minimal. With a real-time view of inventory, the group can also respond flexibly to supply chain problems in the market and quickly find alternatives if a product is not available.
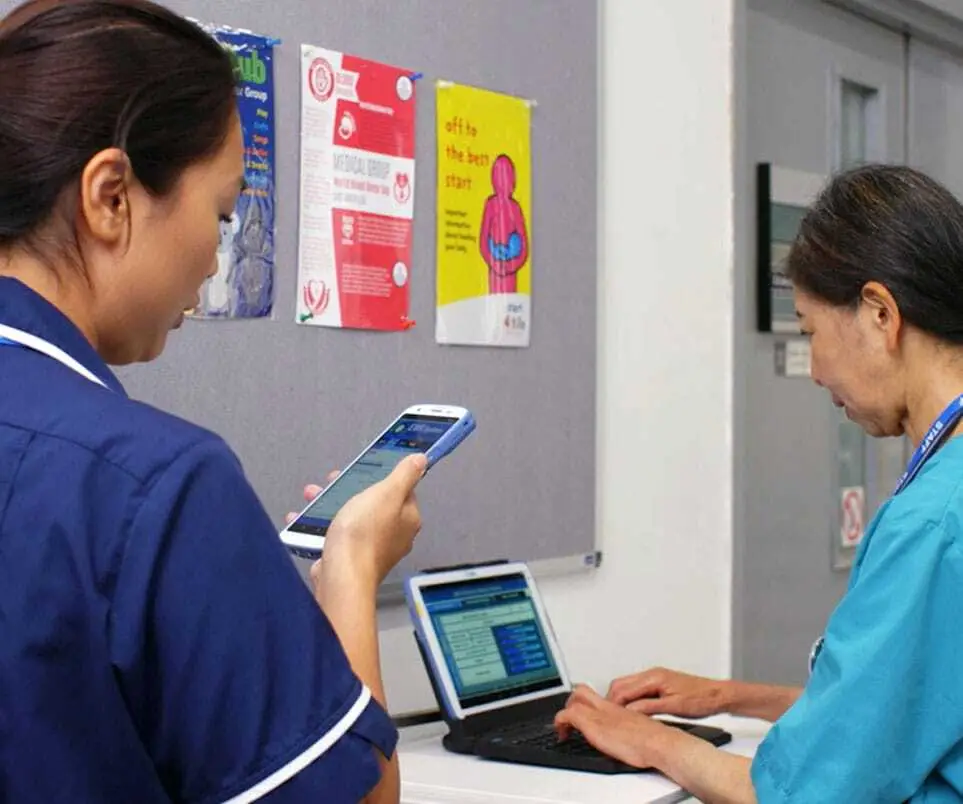
Since all orders are bundled via purchasing, the hospitals and clinics always have an overview of their current stock levels.
Increased Transparency and Data Accuracy
The hospitals and clinics benefit, too, from greater transparency and data accuracy. This allows costs to be correctly assigned to individual patients and the exact material expenditure of an operation to be determined in next to no time. And the platform has also dramatically reduced time spent on administrative tasks.
The automated documentation, ordering and billing processes alone have helped save 90 minutes per day, which is spread across the operating theaters, purchasing/warehousing and finance and accounting areas. The benefits of the new system come to the fore in annual inventory checks. While previously it took up to two full working days per warehouse to record the stock manually, the inventory is now done in less than four hours, thanks to the mobile scanners.
A Positive Response from Hospital Staf
Alongside these benefits, staff are pleased with the 120 Zebra devices used across the group. Both clinical and operations teams report significant improvements to the way they work. Staff say devices are easy to use and work continuously thanks to the long battery life and the option to swap batteries and while they are rugged and robust, they are lightweight to carry and are ergonomically designed.
With scanning central to workflows, the devices quickly and accurately capture codes, even those that are faint, scratched or otherwise compromised. And, with a dedicated scanning button on both sides of their devices, both left- and right-handed team members can instinctively read codes.
Future Outlook
Plans for Future Rollouts
In operating theaters, the rugged TC52-HC is able to withstand the rigorous disinfection protocols required for all equipment used in those environments. And, by capturing UDI codes, an accurate inventory of implants is maintained so, critically, patients can be recalled immediately if issues with implants come to light in the future.
With the project exceeding expectations, the group now plans its phased rollout to all other key operational areas, including legal and consulting, marketing, IT supplies and recruitment. In time, all orders, inventory management and logistics will be run by the central ordering system. The hospital can be confident of its future costs, with its devices managed by Comed for a set fee over the planned lifecycle.
"We’re delighted with the success of this project to centralize ordering, inventory and logistics across our clinics, hospitals and support operations. It’s improving care for our patients and helping our teams work more efficiently. We are seeing clear cost and time savings, our data is accurate and collected in real time, and there is greater transparency in all areas. We are impressed by how stable the solution is and now want to expand it to all order processes in hospital procurement."
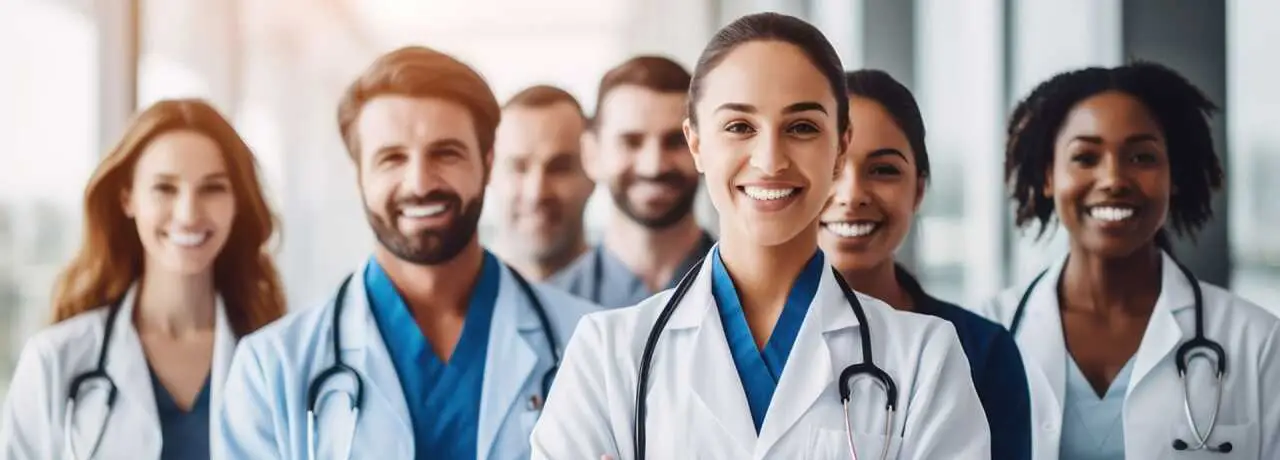
Alongside the benefits, staff are pleased with the 120 Zebra devices used across the group. Both clinical and operations teams report significant improvements to the way they work.