Pneumatic Tube System
Transport – Analysis – Diagnostics
University Hospital Carl Gustav Carus
- Hospital of maximum treatment with 26 clinics and polyclinics
- 850 inpatient hospital beds and 9,700 employees
- Over 1,000 doctors
- Over 1,410 beds
- 57,000 inpatients and 277,000 outpatients annually
Medical products – such as sample material from the operating theaters, patient files or medications – are transported over a total of 8.5 kilometers of pneumatic tube system. An outstanding feature is the delivery speed of 30 kilometers per hour.
The result: the pneumatic tube system shortens transport times, so that, for example, analysis results from the laboratories required for diagnostics are available more quickly. The pneumatic tube system is part of a change in logistics, the first construction phase of which was completed in 2019. The next phase of these construction measures concerns the pharmacy and is to be completed by 2024.
Medical products – such as sample material from the operating theaters, patient files or medications – are transported over a total of 8.5 kilometers of pneumatic tube system. An outstanding feature is the delivery speed of 30 kilometers per hour.
The result: the pneumatic tube system shortens transport times, so that, for example, analysis results from the laboratories required for diagnostics are available more quickly. The pneumatic tube system is part of a change in logistics, the first construction phase of which was completed in 2019. The next phase of these construction measures concerns the pharmacy and is to be completed by 2024.
University Hospital Carl Gustav Carus
- Hospital of maximum treatment with 26 clinics and polyclinics
- 850 inpatient hospital beds and 9,700 employees
- Over 1,000 doctors
- Over 1,410 beds
- 57,000 inpatients and 277,000 outpatients annually
Complicated and Long Transport Routes
"Prior to the realization of the pneumatic tube system, the samples were transported on foot, by bicycle, or by car, depending on the distance of the destination. The procedure was inefficient, error-prone and time-consuming. The faster a blood or tissue sample is analyzed in the laboratory, the faster the patient can be treated. Within a single building, walking minutes add up very quickly. Additionally, the distances between the buildings are greater. The solution increases transport speed and transparency, and guarantees the tracking of medical products," explains Benjamin Reppe.
The Pneumatic Tube System in Operation since 2019
The feasibility study of a pneumatic tube system was already carried out in 2009. The new building – House 32 – with a surgical emergency room and adjoining OR center as well as the pneumatic delivery system was realized in parallel. The new construction began in 2014, two years later, the basis for the pneumatic post system was integrated into the existing route.
"The surgical emergency room opened in June 2019. Additionally, the radiology department, nursing stations with a total of 128 beds and interdisciplinary outpatient clinics were integrated into the new building. Over 720 employees work in the new building complex. Other buildings about 500 meters away – including laboratories and the pathology department – were integrated into the pneumatic tube system in 2017. Since June 2019, House 32, with its 10,700 square meters, has been fully operational, which includes the pneumatic delivery system"
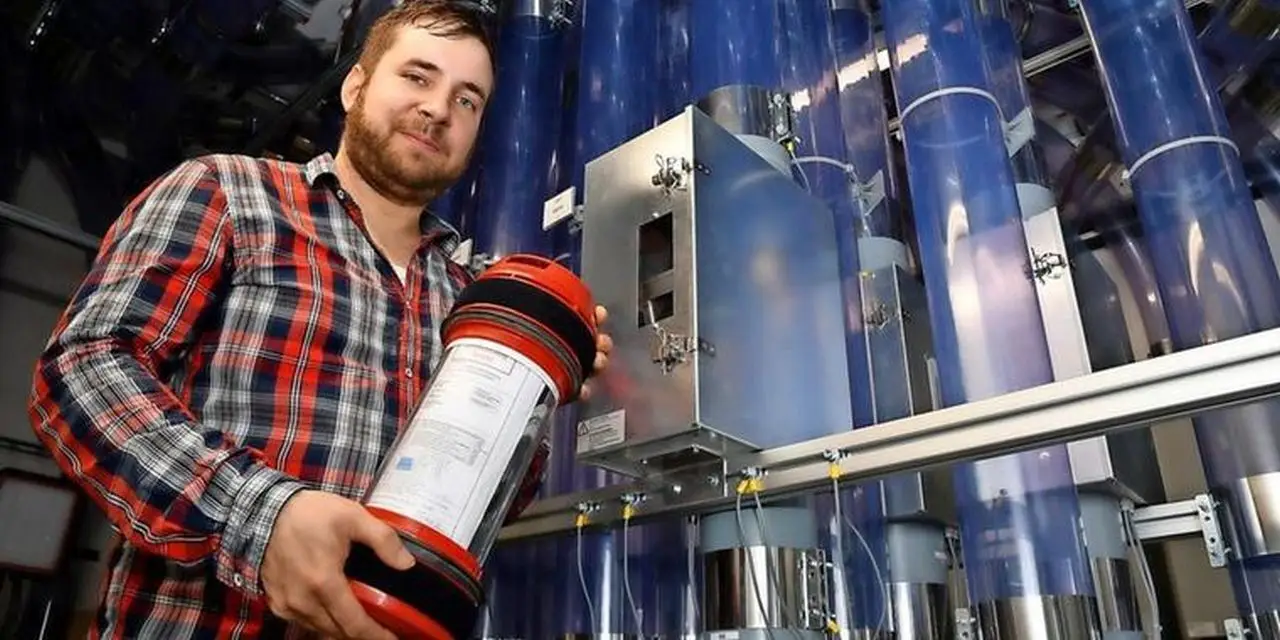
At present, 8.5 kilometers of piping have been installed. Half of it underground. In the ring-shaped installation, the pipes run parallel. Around 40 stations are in operation so far and approximately 600 canisters are dispatched or received daily. (Source DNN Image by Anja Schneider)
The goal is a paperless hospital
8.5-Kilometer Route Length
At present, 8.5 kilometers of piping have been installed. Half of it underground. In the ring-shaped installation, the pipes run parallel. Around 40 stations are in operation so far. Approximately 600 canisters are dispatched or received daily. The canisters are transported with a slight distance between them in the plastic pipes, which have a diameter of 160 millimeters.
At the terminals of the pneumatic post stations, the RFID tag on the canister is labeled with the destination and priority information. The transport speed is up to eight meters per second, which corresponds to about 30 kilometers per hour. Each canister reaches its destination within 10 minutes – regardless of the distance covered. This corresponds to a 50 percent reduction in transport times.
"The University Children's Women's Center is currently being connected to the pneumatic tube system. The installation and commissioning of the entire system was handled by Aerocom, the company for transport automation."
How is Logistics Organized?
The hospital premises are equipped with WLAN throughout the entire area. A digital locking system with specific access authorizations, depending on the area and employee, controls access. The authorizations are assigned by a central administration according to categories and stored in the RFID transponder of the respective employee. Readers installed at the doors detect the transponders with a reading range of up to 30 centimeters. Only a few areas are currently still offline. Most of the staff also have another RFID chip for time recording and parking access.
RFID-Tagged Laundry
The hospital also relies on automated solutions for handling laundry. All items of laundry are fitted with RFID transponders and dispensed via automatic laundry machines. "The loading of the machines is still done manually, but the removal of laundry by the staff is already fully automated," explains Benjamin Reppe. The logistics processes were analyzed in cooperation with Fraunhofer IML. The recommendations were and are being implemented in sub-projects.
Asset Management with Data Matrix Codes
The maintenance of inventory is recorded digitally. For this purpose, the assets are provided with a Data Matrix Code and manually read by a handheld device.
Sterile Goods Processing is Digital with an In-House ID
The automation process also takes place in the sterile supply area. Surgical instruments must be properly reprocessed before each use. In the past, the procedure and the duration of the cleaning process of surgical instruments was documented by hand. Currently, all surgical instruments and instruments in the hospital are provided with a Data Matrix Code and the required information is stored digitally.
The hospital has also integrated an in-house ID into the barcode, which reveals the affiliation to the Dresden University Hospital when read out by a handheld device. The entire history of the medical instruments can thus be viewed and tracked.
Patient Data are Stored Digitally
The goal of the digitalization measures is a paperless hospital with complete electronic medical records. Digital process and quality control should be ensured at all times. All patient data is already digitally stored. Staff can, for example, view the daily schedules for all operations. This not only facilitates internal coordination, but also leads to time and cost savings. Furthermore, the issuing of prescriptions is simplified. Prior to digitalization, these could only be signed off by specialists. Now, they can also be issued by nurses and subsequently confirmed by a specialist. The medical staff can view all relevant information digitally.
Outlook
Internal Networking Thanks to the 'Orbis' IT Platform
Repetitive paper-based processes within the hospital are converted into automated, digital solutions. The internal IT department has designed the IT system 'Orbis' in cooperation with external consultants. "The platform bundles all data digitally, minimizing paper printouts," explains Benjamin Reppe, and adds, "Every clinic and institute will be modernized as part of the integration of this management platform. Since everyone involved uses the same system, the individual wards are digitally linked to each other, and data can be viewed and exchanged".
Step-by-Step Expansion of the Pneumatic Tube System
The pharmacy and other institutes and clinics have already been connected with 15 to 20 kilometers of piping. This corresponds to a total distance of around 20 kilometers. If all buildings were to be connected to the pneumatic tube system, about 100 kilometers of pipes would have to be installed. However, this is not planned.
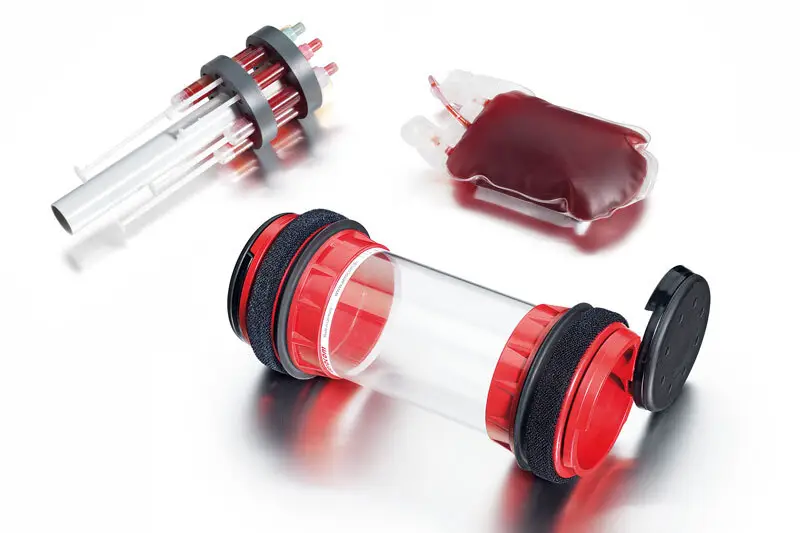
A pneumatic post box for the dispatch of blood preserves.
Future RFID Integration in Transfusion Medicine
In the next stage of expansion, blood reserves are to be sent directly from the blood bank via the pneumatic tube system. The challenge here is the necessary cooling of the transported goods. Plans for the future include the use of RFID technology for the track and trace of blood reserves. However, an RFID chip in transfusion medicine is not yet cost-effective. There are also considerations about the use of RFID wristbands in the infant ward. This should ensure a higher safety standard.
Comparing Quality Standards Worldwide
Within the next five years, level 7, the highest level, of the Electronic Medical Records Adoption Model (EMRAM) should be reached. One of the first stages of digitalization includes the use of laboratory information and management systems, a radiology information system, and pharmaceutical knowledge software.
The ultimate goal of digitalization is a paperless hospital with a complete electronic medical record, where digital process and quality control are possible at any time. The model indicates the degree of digitalization of hospitals for an international comparison.
“The solution increases transport speed and transparency, guarantees the tracking of medical devices and minimizes the error rate. Transport in the pneumatic tube system is carried out at 30 kilometers per hour. Within 10 minutes – regardless of the distance covered – each canister reaches its destination. The faster a blood or tissue sample is analyzed in the laboratory, the faster the patient can be treated.”