Interview Yiwen Jin
The Origins of B-Id
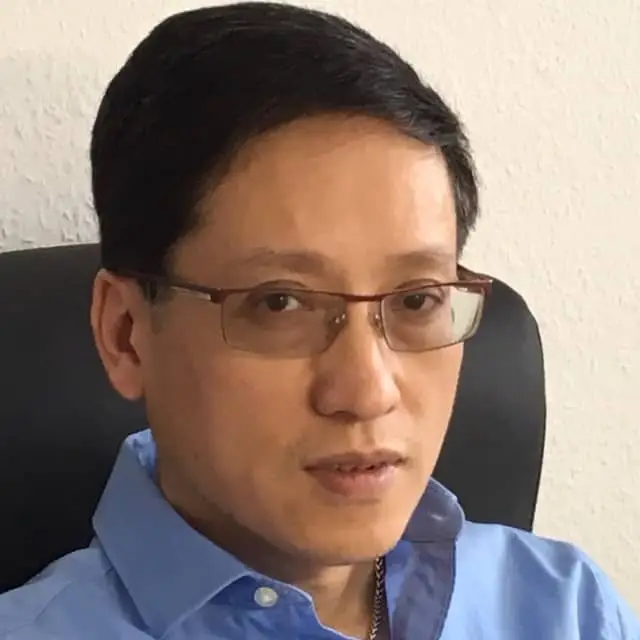
Yiwen Jin, CEO of B-Id
1. Mr. Yin, what skills and experience have you acquired in Germany in the field of RFID and smart cards?
My first encounter with Germany was in 1991, when I started studying experimental physics and computer science at the Ludwig-Maximilians-Universität (LMU) in Munich. This step came after my electronics engineering studies in China, which also included high-frequency engineering, a particularly demanding field. After successfully completing my studies at LMU in 1996, I took up a position in sales for a mechanical engineering company. It was during this time that I first came into contact with RFID technology. After three years, I finally founded my own company. How difficult were your first few years in Germany?
Coming to Germany was of course a challenge for me, as I had to learn a new language. I studied German for a year before starting my studies at LMU and was able to complete my studies with a grade of 1.0. Germany is now my home, even though I travel a lot. My family lives here and my children study here. I also travel regularly to the USA, where I founded another B-Id branch eight years ago. I visit partners and meet with technical experts to discuss the latest topics and innovations.
2. Mr. Jin, you founded B-Id in 2002. How did this come about back then?
I had been working as an employee of a German mechanical engineering company since 1996. I was responsible for the Asia-Pacific region. One day I saw a very interesting product from a customer – a software CD that needed to be protected against counterfeiting and misuse.
My partner at the time had the exciting idea of applying an RFID ID to the body of the CD to prevent counterfeiting. One of the advantages of RFID integration is that the CD would be protected against piracy. As soon as a drive with a CD is started, the software inside reads the RFID chip and checks whether it is an original. Only the n is the user allowed or able to use the CD. We later also acquired a patent for this invention.
I was so impressed by this product that I decided to found a company for the development of RFID products and solutions in Europe. That was the spark that led to the founding of B-id.
3. How has B-Id developed since then?
After being founded in Germany in 2002, we established ourselves in the USA in 2015 and have also been operating production facilities in Shanghai and Taiwan for several years. As a company, we focus mainly on the transponder sector. Our partner network has grown immensely in recent years.
Our partners include business partners such as manufacturers of readers and antennas as well as end users. Some manufacturers buy our transponders so that they can integrate them into their products. They then sell these products directly to the end user.
1. Mr. Yin, what skills and experience have you acquired in Germany in the field of RFID and smart cards?
My first encounter with Germany was in 1991, when I started studying experimental physics and computer science at the Ludwig-Maximilians-Universität (LMU) in Munich. This step came after my electronics engineering studies in China, which also included high-frequency engineering, a particularly demanding field. After successfully completing my studies at LMU in 1996, I took up a position in sales for a mechanical engineering company. It was during this time that I first came into contact with RFID technology. After three years, I finally founded my own company. How difficult were your first few years in Germany?
Coming to Germany was of course a challenge for me, as I had to learn a new language. I studied German for a year before starting my studies at LMU and was able to complete my studies with a grade of 1.0. Germany is now my home, even though I travel a lot. My family lives here and my children study here. I also travel regularly to the USA, where I founded another B-Id branch eight years ago. I visit partners and meet with technical experts to discuss the latest topics and innovations.
2. Mr. Jin, you founded B-Id in 2002. How did this come about back then?
I had been working as an employee of a German mechanical engineering company since 1996. I was responsible for the Asia-Pacific region. One day I saw a very interesting product from a customer – a software CD that needed to be protected against counterfeiting and misuse.
My partner at the time had the exciting idea of applying an RFID ID to the body of the CD to prevent counterfeiting. One of the advantages of RFID integration is that the CD would be protected against piracy. As soon as a drive with a CD is started, the software inside reads the RFID chip and checks whether it is an original. Only the n is the user allowed or able to use the CD. We later also acquired a patent for this invention.
I was so impressed by this product that I decided to found a company for the development of RFID products and solutions in Europe. That was the spark that led to the founding of B-id.
3. How has B-Id developed since then?
After being founded in Germany in 2002, we established ourselves in the USA in 2015 and have also been operating production facilities in Shanghai and Taiwan for several years. As a company, we focus mainly on the transponder sector. Our partner network has grown immensely in recent years.
Our partners include business partners such as manufacturers of readers and antennas as well as end users. Some manufacturers buy our transponders so that they can integrate them into their products. They then sell these products directly to the end user.
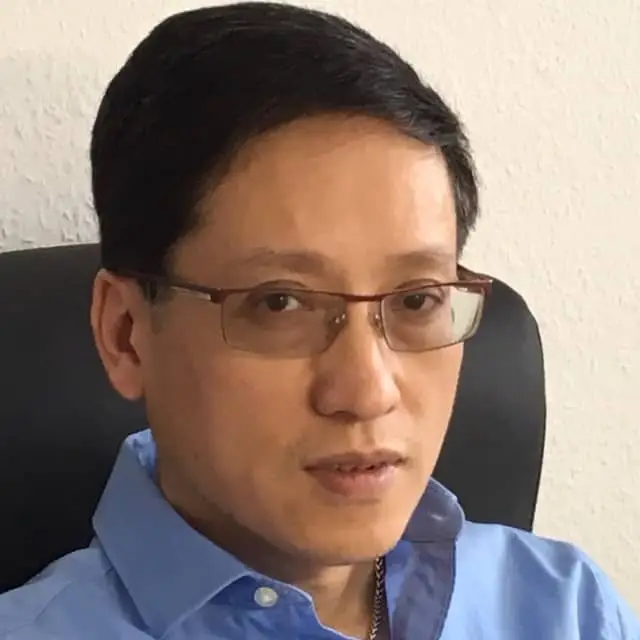
Yiwen Jin, CEO of B-Id
Smart Cards + Key Fob + RFID Transponder
4. Keyword: Product development. Where and with whom does product development take place?
It varies, but the crucial point here is the close cooperation. I myself am responsible for product development projects in the company. As a trained engineer, I have lots of ideas and visions for development. A new product idea is discussed in the team and with partners before a prototype is created. Discussions with customers and specific solution requests from the market provide insights into what the industry needs.
As B-id's partners specialize in different areas of technology, joint project discussions always lead to appropriate and tailor-made solutions or product developments. For example, the partners specialize in topics ranging from materials science, tool-making and plastic injection moulding to antenna production and tuning. After prototyping, the next stage of product development begins, the test phase. This is the standard product development process at B-Id. Mass production only takes place once the test phase has been successfully completed and the samples have been approved.
5. Can you name an early highlight of your product portfolio?
The first RFID products in the portfolio included products for access control. Back then, we developed a very small transponder. At the time, it was known as the smallest antenna transponder in the world with a diameter of 1.5 millimetres and a height of two millimetres.
6. How did you come up with the idea of developing and producing RFID transponders for industry and production?
The decision to develop and manufacture RFID transponders for use in industry and production was based on the increasing relevance of key fobs and smart cards in the first few years after the company was founded. At that time, RFID was still a relatively new concept, but just two to three years later, numerous companies recognized the potential and easily started producing RFID products, including smart cards and RFID key fobs.
To differentiate ourselves from the competition, we introduced the customization of our key fobs. Customers had the option of printing their logo in three different ways. We offer pad printing, laser engraving and integration of the logo into the tool. In addition, customers can choose different case colors and other personalization options. This customization service is still very popular today. Later, I established more contacts with the semiconductor industry, particularly in Taiwan. Our aim was to develop new products, not just for access control.
During this phase, I noticed the growing interest of the German industry in integrating RFID into their production processes. In discussions with various customers, I realized that they had specific challenges to overcome, be it in terms of temperature, reading distance, customerspecific designs or other factors. These companies were looking for customized solutions for their production requirements. Based on these dialogues, we developed prototypes and thus began our entry into the production of customized RFID transponders for industry and production. This shift towards customer-specific solutions marked an extremely positive development for me.
High-Tech Transponder
7. What is a high-tech transponder?
High-tech transponders represent the standard that we at B-Id consistently develop and manufacture. An outstanding example of this is our Vehicle Tag. In the production of UHF labels and inlays, we consistently rely on surface-mounted device (SMD) technology. This means that we precisely remove individual chips from the wafer and package the chip in such a way that two surfaces are created for connection to the antenna.
This procedure not only ensures that the chip is protected, but also enables a robust connection between chip and antenna, as we solder the antenna directly to the chip. In contrast to the use of conductive adhesive, this soldering technique offers a much more resistant bond.
A special feature is the choice of antenna materials. Conventional aluminum antennas are not compatible with soldering. We therefore use copper antennas for the production of all ODM transponders. The decision to use copper not only offers a robust soldered connection, but also has other advantages. Copper is more elastic than aluminum and has better conductivity, resulting in improved overall performance.
8. Why did B-Id decide to develop high-tech transponders?
The decision to develop high-tech transponders was made more than a decade ago and was a reaction to the emerging dynamics in the UHF market. In the early days, the focus was primarily on the price of the UHF tag and the production volume. Subsequently, however, the demand for individual, customized products from companies increased.
For this reason, we adapted our development strategy and began to design and manufacture HF and RF transponders as well as specialty products. This marked a deliberate shift away from standardized mass production towards the production of highly specialized high-tech transponders.
Industrial Transponders
RFID Industrial Transponders for Indoor and Outdoor Use
Key Facts:
- Materials: PVC, PET, nylon, ABS, POM, PP, fiberglass FR4
- Antenna material: copper
- Soldered antenna and chip enable stable operation under harsh conditions
- Operating temperatures: -20 – +250 °C
- Frequency: 125 kHz (LF), 13.56 MHz (HF), 850–950 MHz (UHF)
- Possible Applications in demanding environments
B-Id offers robust industrial transponders that have been specially developed for the UHF, HF and LF frequency ranges, both for indoor and outdoor use, and can withstand challenging environmental conditions such as extreme temperature fluctuations, aggressive chemicals or metallic surfaces.
The portfolio includes various types of transponders, including cable transponders, UHF RFID transponders, ferrite core transponders, on-metal transponders, PVC tags and e-units. Particularly noteworthy is our standard UHF RFID Vehicle Tag, which is an excellent solution for a wide range of industrial applications.
The versatile industrial transponders from B-Id are used in various environments with demanding conditions. Examples of such applications include vehicle identification and the labeling of medical devices. The labels are designed to withstand even aggressive sterilization processes in autoclaves, for example in dentistry.
The specially developed on-metal transponders are ideal for tracking metal objects or in metal environments. An outstanding product in this category is the on-metal transponder, which was developed for the precise tracking of metal bottles and drums.
The flexible shape of this transponder makes it easy to attach by gluing it 100 percent to the bottles. The intelligent antenna design uses the metal of the bottle as reinforcement, resulting in robust tags that can withstand being sandblasted twice. Another example is the on-metal transponder specially designed for extreme temperatures in the semiconductor industry.
The packaging material of these transponders withstands pH values of 1–13 and can withstand temperatures of up to 230 °C for at least 20–30 minutes. These products impressively demonstrate the resilience and adaptability of our industrial transponders in extreme environments.
B-Id offers robust industrial transponders that have been specially developed for the UHF, HF and LF frequency ranges, both for indoor and outdoor use, and can withstand challenging environmental conditions such as extreme temperature fluctuations, aggressive chemicals or metallic surfaces.
The portfolio includes various types of transponders, including cable transponders, UHF RFID transponders, ferrite core transponders, on-metal transponders, PVC tags and e-units. Particularly noteworthy is our standard UHF RFID Vehicle Tag, which is an excellent solution for a wide range of industrial applications.
The versatile industrial transponders from B-Id are used in various environments with demanding conditions. Examples of such applications include vehicle identification and the labeling of medical devices. The labels are designed to withstand even aggressive sterilization processes in autoclaves, for example in dentistry.
The specially developed on-metal transponders are ideal for tracking metal objects or in metal environments. An outstanding product in this category is the on-metal transponder, which was developed for the precise tracking of metal bottles and drums.
The flexible shape of this transponder makes it easy to attach by gluing it 100 percent to the bottles. The intelligent antenna design uses the metal of the bottle as reinforcement, resulting in robust tags that can withstand being sandblasted twice. Another example is the on-metal transponder specially designed for extreme temperatures in the semiconductor industry.
The packaging material of these transponders withstands pH values of 1–13 and can withstand temperatures of up to 230 °C for at least 20–30 minutes. These products impressively demonstrate the resilience and adaptability of our industrial transponders in extreme environments.
Key Facts:
- Materials: PVC, PET, nylon, ABS, POM, PP, fiberglass FR4
- Antenna material: copper
- Soldered antenna and chip enable stable operation under harsh conditions
- Operating temperatures: -20 – +250 °C
- Frequency: 125 kHz (LF), 13.56 MHz (HF), 850–950 MHz (UHF)
- Possible Applications in demanding environments
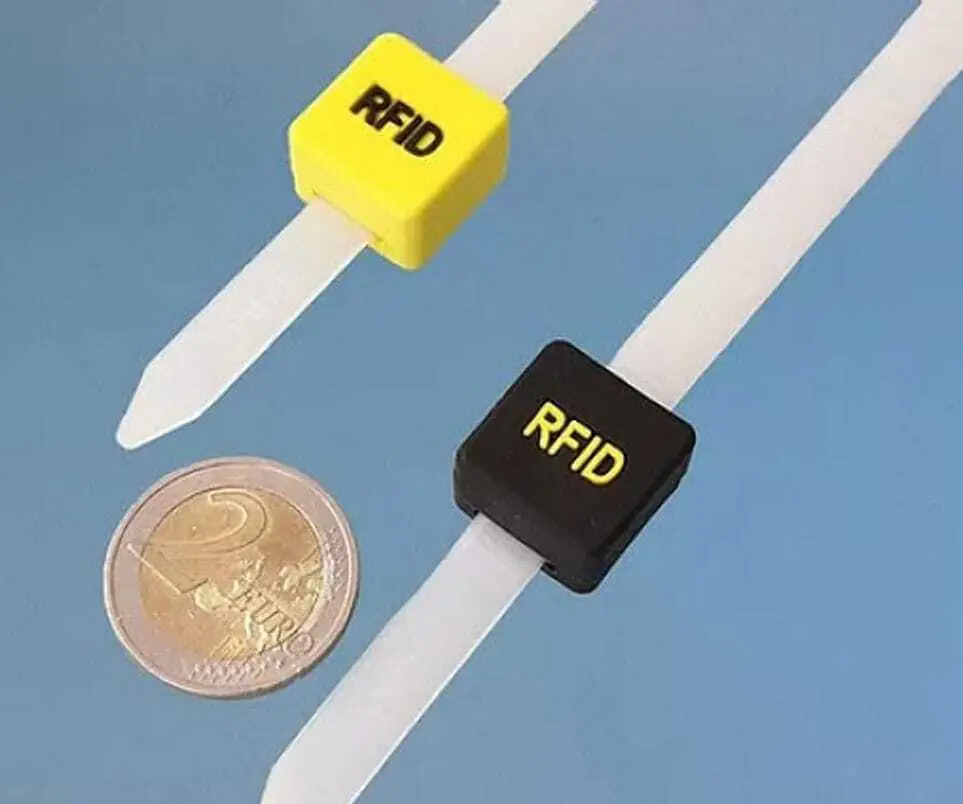
Tag1818: The ideal cable tie solution for outdoors or in harsh environments.
Key Fobs
RFID Key Fobs in a Variety of Shapes and Sizes
Key Facts
- Materials: PVC, fiberglass FR4, PC
- Operating temperatures: -20 – +70 °C
- Frequency: 125 kHz (LF), 13.56 MHz (HF)
- Customizable with laser engraving, housing color and graphics
- Applications in access control and time recording
The company also offers a selection of RFID key fobs in a variety of shapes and sizes, including the KF1x to KF5x variants. These key fobs are ready for operation in LF and HF frequencies. A combination of two frequencies with two chips and two antennas is also possible.
RFID key fobs are increasingly being used in the area of access control. Typically, these tags are used to regulate employee access to specific areas or to control certain machines. Additional areas of application include access control for hotel rooms, public transportation and e-payment solutions. RFID key fobs can also be used for time recording at sporting events.
The company also offers a selection of RFID key fobs in a variety of shapes and sizes, including the KF1x to KF5x variants. These key fobs are ready for operation in LF and HF frequencies. A combination of two frequencies with two chips and two antennas is also possible.
RFID key fobs are increasingly being used in the area of access control. Typically, these tags are used to regulate employee access to specific areas or to control certain machines. Additional areas of application include access control for hotel rooms, public transportation and e-payment solutions. RFID key fobs can also be used for time recording at sporting events.
Key Facts
- Materials: PVC, fiberglass FR4, PC
- Operating temperatures: -20 – +70 °C
- Frequency: 125 kHz (LF), 13.56 MHz (HF)
- Customizable with laser engraving, housing color and graphics
- Applications in access control and time recording
Smart Cards
RFID cards, including ISO cards and clamshell cards
Key Facts
- Materials: PVC, PETG, ABS
- Operating temperatures: 0 °C – 70 °C
- Frequency: 125 kHz (LF), 13.56 MHz (HF), 850-950 MHz (UHF)
- Offset, screen, thermal transfer, inkjet printing, laser engraving
- Used in labeling, access control & contactless payment
B-Id offers a comprehensive selection of RFID cards, including ISO cards and clamshell cards that operate in the LF, Hf and UHF frequency ranges. The ISO cards stand out in particular as they can be equipped with up to three chips that cover different frequency ranges. This enables versatile use in various scenarios.
The standard ISO cards, equipped with one or more chips, play an indispensable role in numerous identification applications. RFID smart card technology enables versatile applications such as identification, access control and contactless payment in various sectors such as public transportation, healthcare, industry, agriculture and beyond.
B-Id offers a comprehensive selection of RFID cards, including ISO cards and clamshell cards that operate in the LF, Hf and UHF frequency ranges. The ISO cards stand out in particular as they can be equipped with up to three chips that cover different frequency ranges. This enables versatile use in various scenarios.
The standard ISO cards, equipped with one or more chips, play an indispensable role in numerous identification applications. RFID smart card technology enables versatile applications such as identification, access control and contactless payment in various sectors such as public transportation, healthcare, industry, agriculture and beyond.
Key Facts
- Materials: PVC, PETG, ABS
- Operating temperatures: 0 °C – 70 °C
- Frequency: 125 kHz (LF), 13.56 MHz (HF), 850-950 MHz (UHF)
- Offset, screen, thermal transfer, inkjet printing, laser engraving
- Used in labeling, access control & contactless payment
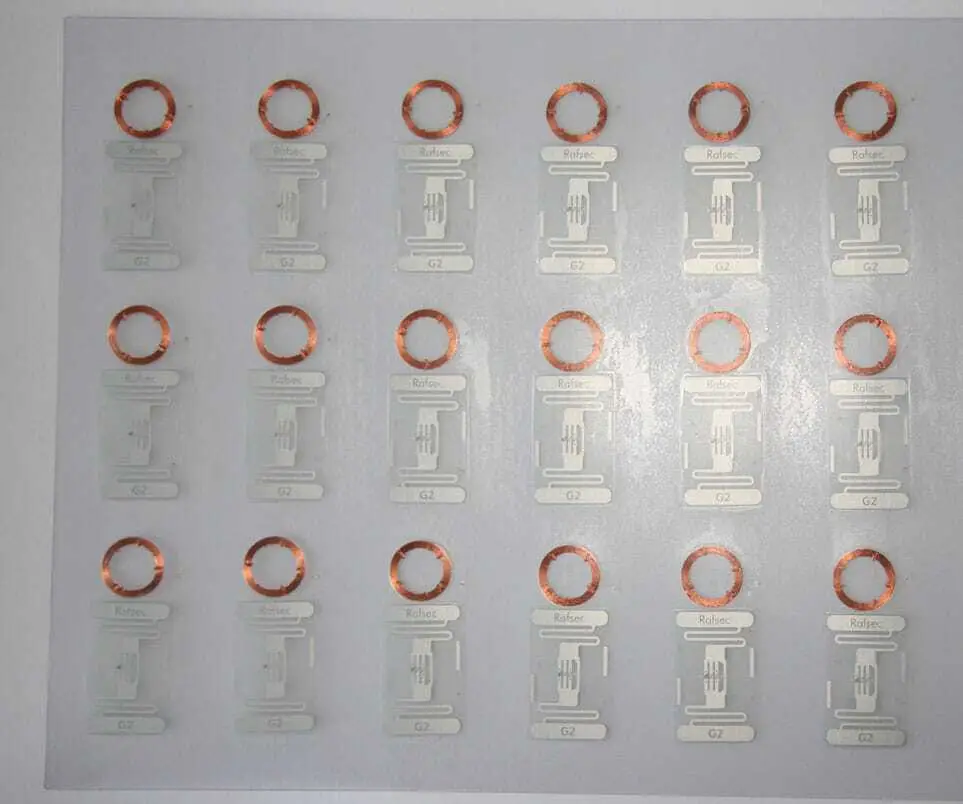
RFID hardware of various materials, properties and designs are designed, developed and realized according to customer requirements.
RFID Readers
RFID Read and Write Devices
Key Facts
- Frequency: 125 kHz (LF) and 13.56 MHz (HF)
- Interfaces: RS485/Wiegand232, USB1.1 HID Keyboard Device
- Compatibility: ISO 14443 A and ISO 15693
- Used in inventory management & seamless tracking
With the help of RFID read and write devices, RFID transponders can not only be read contactlessly, depending on the application, but also written and encoded directly. B-Id provides a user-friendly RFID "plug-and-play" reader in the form of a USB stick.
The RFID data captured is treated as keystrokes (HDI) on the computer and can be processed immediately in applications such as Word, Excel or other programs. The company also offers the WM9918 RFID reader in a sleek design that is suitable for fixed mounting on walls.
RFID readers are used to capture the data stored in RFID tags. This is particularly beneficial for precise inventory management and a comprehensive overview of all items.
With the help of RFID read and write devices, RFID transponders can not only be read contactlessly, depending on the application, but also written and encoded directly. B-Id provides a user-friendly RFID "plug-and-play" reader in the form of a USB stick.
The RFID data captured is treated as keystrokes (HDI) on the computer and can be processed immediately in applications such as Word, Excel or other programs. The company also offers the WM9918 RFID reader in a sleek design that is suitable for fixed mounting on walls.
RFID readers are used to capture the data stored in RFID tags. This is particularly beneficial for precise inventory management and a comprehensive overview of all items.
Key Facts
- Frequency: 125 kHz (LF) and 13.56 MHz (HF)
- Interfaces: RS485/Wiegand232, USB1.1 HID Keyboard Device
- Compatibility: ISO 14443 A and ISO 15693
- Used in inventory management & seamless tracking