Arctic Circle
Life in the Arctic Circle
The Nordland region lies predominantly in the subarctic climate zone. With an average annual temperature of 5.0 degrees Celsius in Bodø, the administrative center of the region, it is temperately cold all year round. The region covers a geographically extremely heterogeneous area characterized by rivers, fjords, coasts, mountains and marshlands. Fast transport connections are limited.
A famous characteristic of the region are the variations in sunlight. In summer, the sun stays above the horizon continuously for 1.5 months in this region. In winter, on the other hand, there is polar night between mid-November and mid-January.
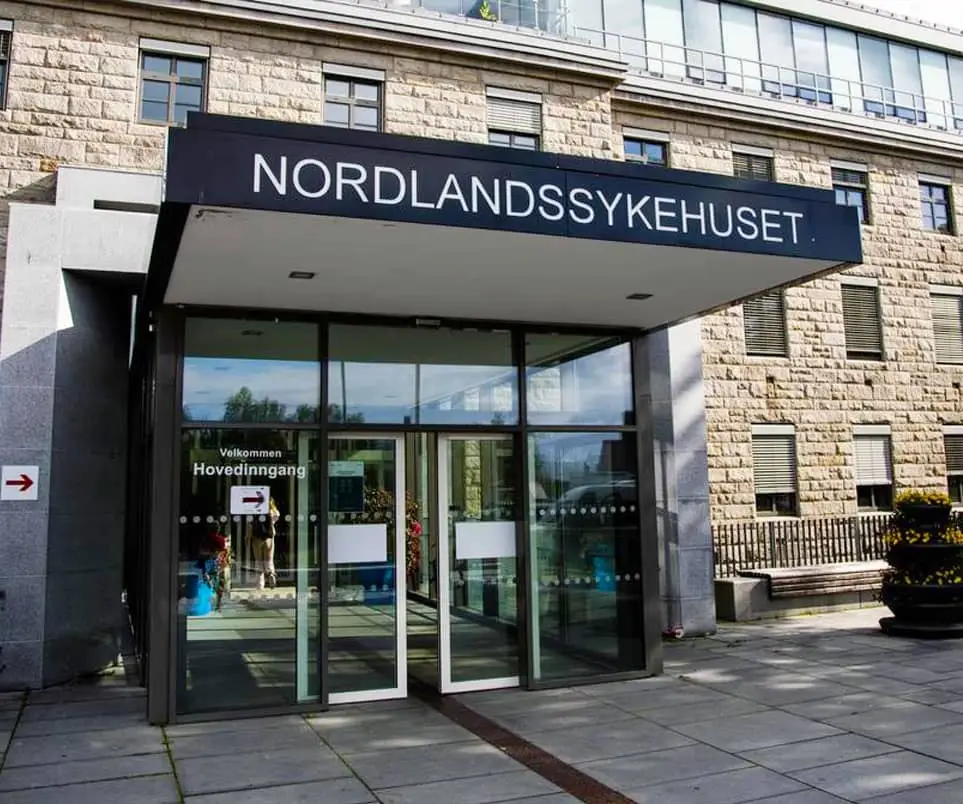
Over the past 15 years, Nordland Hospital has invested approximately 5.5 billion Norwegian kroner in new hospital buildings. A new local hospital in Stokmarknes opened in 2014, and the modernized and expanded somatic hospital in Bodø was completed in 2021.
"The medical facilities in the Nordland region are geographically far apart. The care of the patients therefore requires a functional emergency organization."
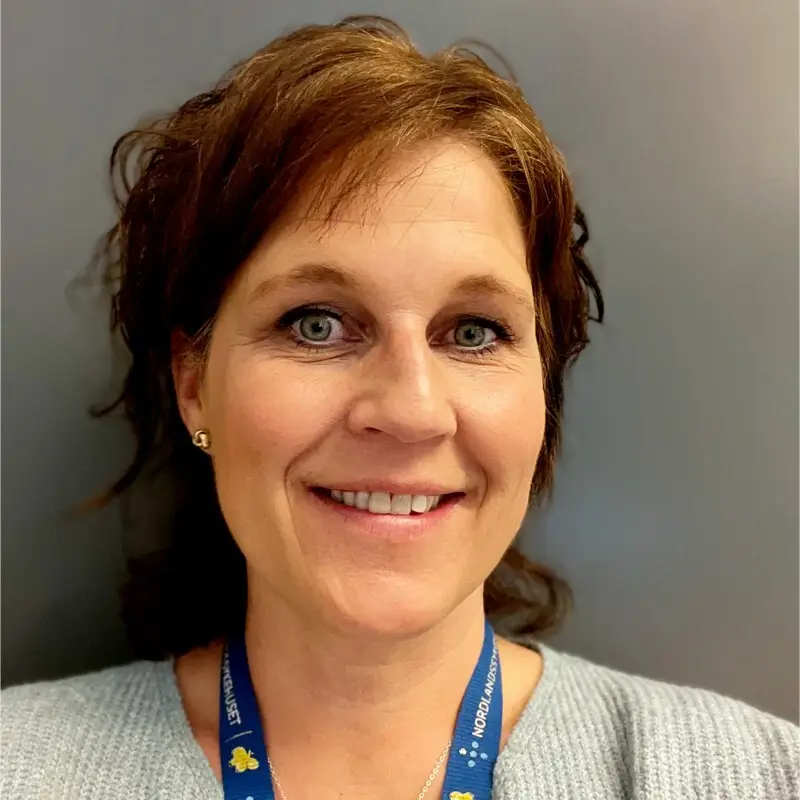
Helse Nord in Northern Norway
Helse Nord, based in Bodø, is the regional health authority of Northern Norway. It is responsible for public specialist healthcare in Northern Norway and Svalbard. The Nordland Hospital Trust is the second largest health trust in Nordland county, providing traditional general hospital services. The health trust employs more than 4,000 people and serves about 136,000 people in 20 municipalities in the regions of Salten, Lofoten and Vesterålen.
Bodø is the largest city in Nordland, with a population of approximately 50,000. The hospital in Lofoten is located in Gravdal near the town of Leknes. The hospital in Vesterålen is located in the town of Stokmarknes. In total, Lofoten and Vesterålen have approximately 55,000 inhabitants.
Medical Care
Healthcare services take into account the topography of the region. The region's emergency ambulance service includes a total of 123 ambulances, 13 boats, 6 small aircraft and 4 helicopters. In emergencies in remote areas, citizens provide first aid until a doctor arrives by rescue boat or helicopter.
Inpatient care is provided at the central hospital in Bodø, which has 237 beds in the somatic department and 140 beds in the psychiatric department. Hospitals with 42 (Lofoten) and 66 beds (Vesterålen) are available for inpatient care in other parts of Nordland.
The Administrative Center Bodø
The city of Bodø is home to more than 30 government agencies and institutions. Economic pillars are therefore the service industry and public administration. As a starting point for travel to the Lofoten Islands and further north, tourism has increasingly gained significance in Bodø over the years. In 2024, Bodø will be one of three European Capitals of Culture.
Workwear With RFID Chips
Workwear at Nordland Hospital
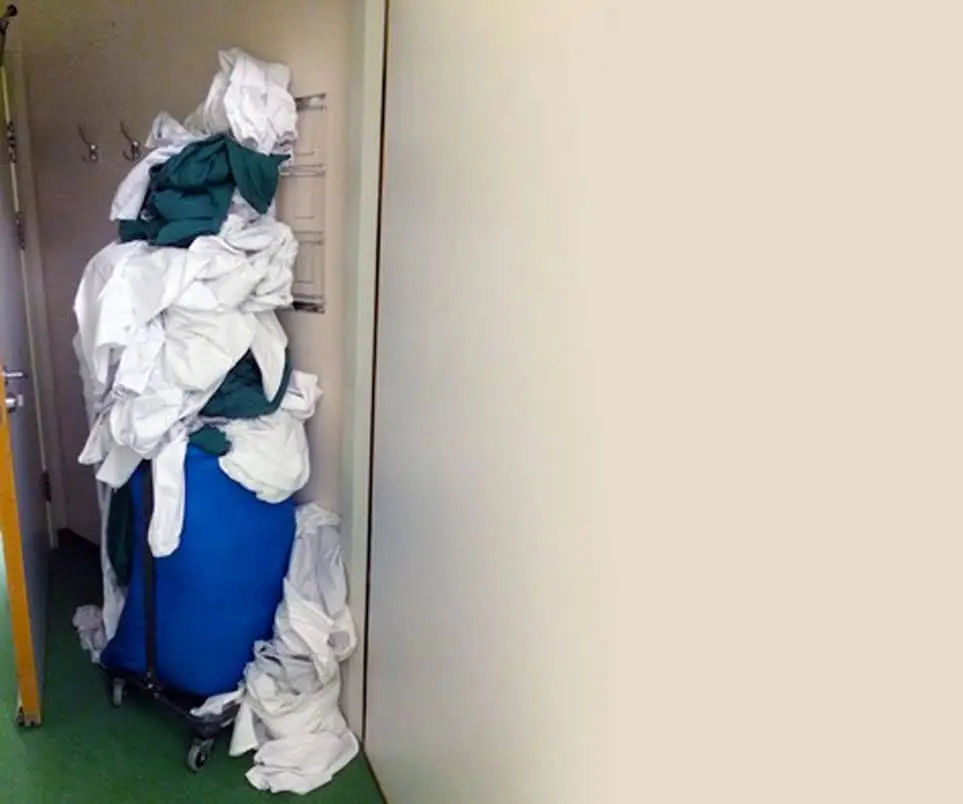
Past: This is not where used work clothes belong.
3,000 employees work in the somatic and mental health departments at the hospital in Bodø. Every day, approximately 700 employees, such as doctors, nurses, kitchen and operational staff, require washed work clothes.
30,000 garments are part of the inventory and the work clothes are not personalized. In previous years employees could only pick up work clothes from Monday to Friday before 3 p.m. The new textile management system allows them to do so 24/7. The only garments not offered in the new textile room are the green surgical clothes.
Before the textile management system was implemented, there were regular bottlenecks in the provision of clean work clothes. The return of used clothes was a problem.
Unreturned Work Clothes
When Vibeke Mikalsen took over as Head of Operations, she quickly realized that the laundry cycle was not working smoothly for the employees. Work clothes were worn but not returned. Used laundry was found in "temporary storage," such as in staff rooms. "Employees were not putting the clothes in the designated laundry bins," explains Vibeke Mikalsen.
"Used clothes were piled up on desks, stuffed behind office doors or placed on shelves." This was the main reason for the lack of the right size and number of the required work clothes.
3,000 employees work in the somatic and mental health departments at the hospital in Bodø. Every day, approximately 700 employees, such as doctors, nurses, kitchen and operational staff, require washed work clothes.
30,000 garments are part of the inventory and the work clothes are not personalized. In previous years employees could only pick up work clothes from Monday to Friday before 3 p.m. The new textile management system allows them to do so 24/7. The only garments not offered in the new textile room are the green surgical clothes.
Before the textile management system was implemented, there were regular bottlenecks in the provision of clean work clothes. The return of used clothes was a problem.
Unreturned Work Clothes
When Vibeke Mikalsen took over as Head of Operations, she quickly realized that the laundry cycle was not working smoothly for the employees. Work clothes were worn but not returned. Used laundry was found in "temporary storage," such as in staff rooms. "Employees were not putting the clothes in the designated laundry bins," explains Vibeke Mikalsen.
"Used clothes were piled up on desks, stuffed behind office doors or placed on shelves." This was the main reason for the lack of the right size and number of the required work clothes.
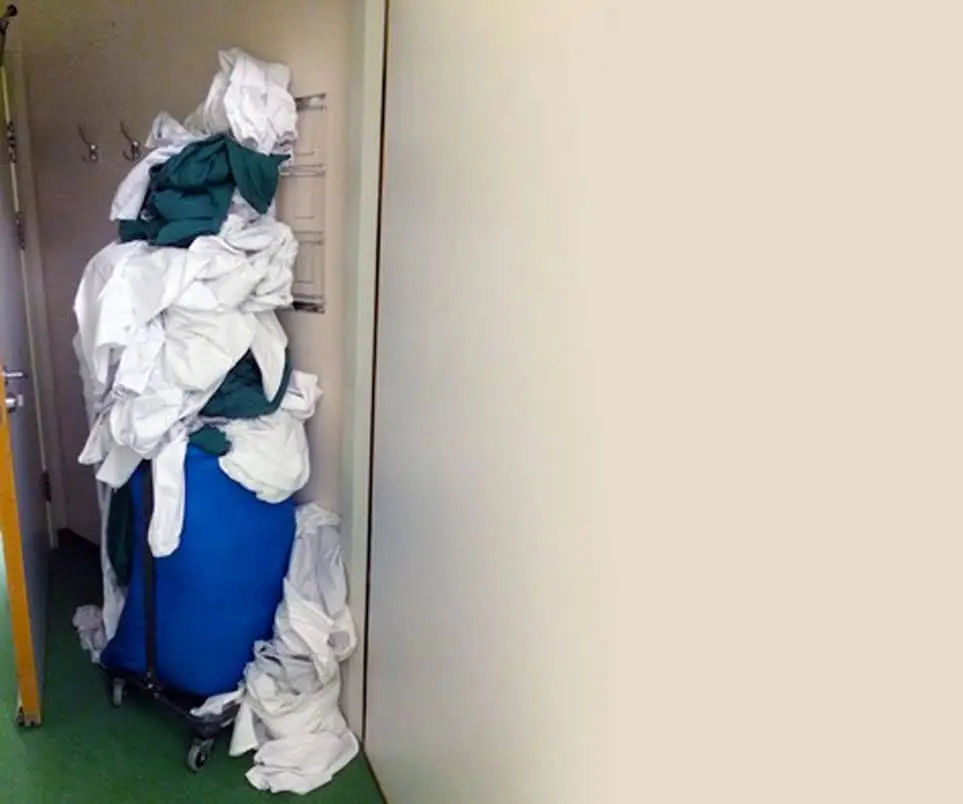
Past: This is not where used work clothes belong.
Deficits at the Laundry Service Provider
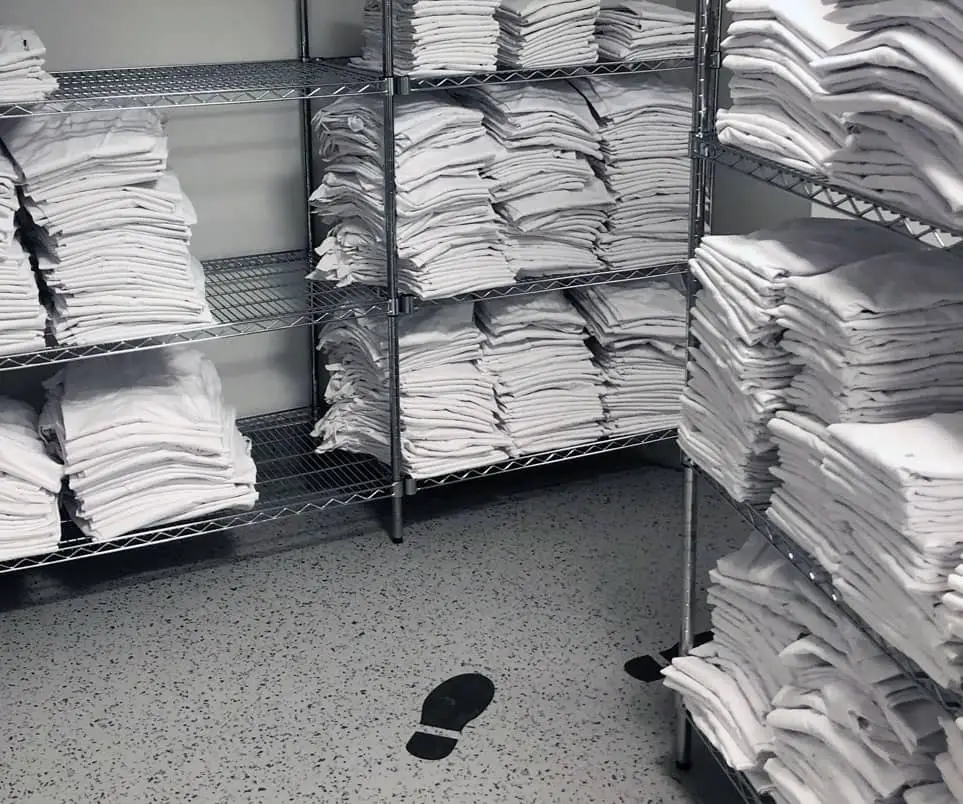
Today: Available workwear pleases all.
The cooperation with the laundry service provider for the workwear was a challenge. "The service provider was constantly delivering large quantities of linen, and more than we actually needed," recalls Vibeke Mikalsen. However, much of the linen was not in the circulation. "We could never match the delivery quantities with the delivery bills, unless we counted by hand."
This resulted in too much workwear being in circulation and high monthly costs for rental linen.
A Visit to a Hospital in Lüneburg
Focus Security in Norway has, in the last five years, invested in resources for tracking technology in healthcare systems. They led the delegation from the hospital to Lüneburg in 2019. This resulted in a successful corporation project between Nordland Hospital, Focus Security and Deister Electronic.
The RFID solution installed there served as a blueprint for implementation in Bodø.
The cooperation with the laundry service provider for the workwear was a challenge. "The service provider was constantly delivering large quantities of linen, and more than we actually needed," recalls Vibeke Mikalsen. However, much of the linen was not in the circulation. "We could never match the delivery quantities with the delivery bills, unless we counted by hand."
This resulted in too much workwear being in circulation and high monthly costs for rental linen.
A Visit to a Hospital in Lüneburg
Focus Security in Norway has, in the last five years, invested in resources for tracking technology in healthcare systems. They led the delegation from the hospital to Lüneburg in 2019. This resulted in a successful corporation project between Nordland Hospital, Focus Security and Deister Electronic.
The RFID solution installed there served as a blueprint for implementation in Bodø.
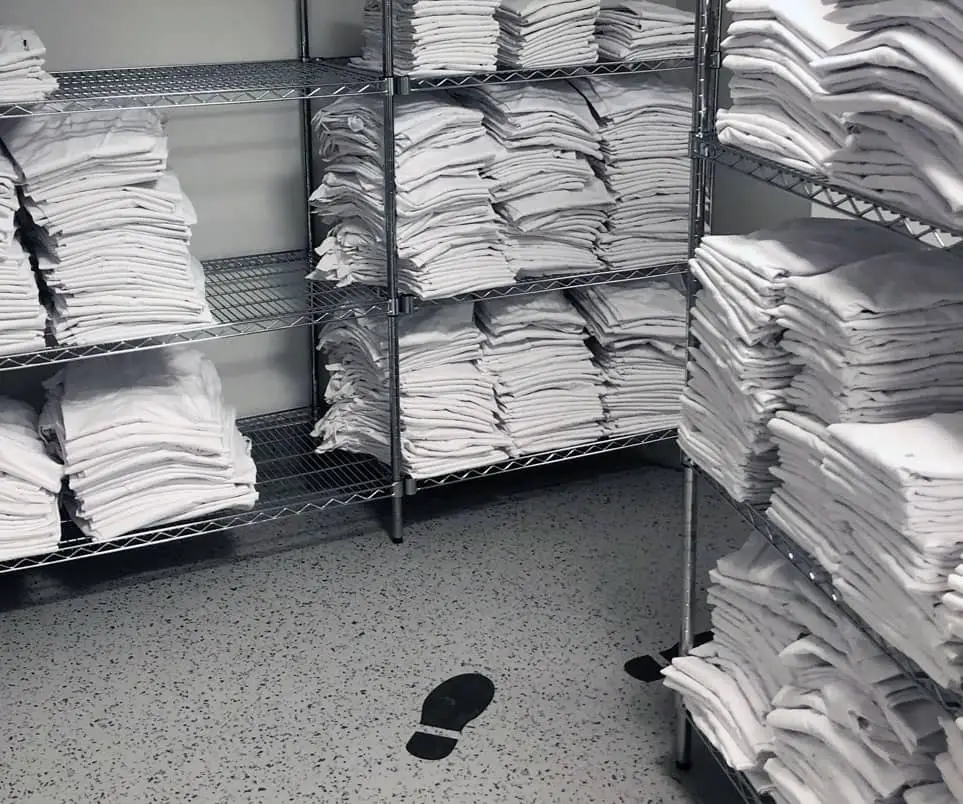
Today: Available workwear pleases all.
Textile Room Solution
The RFID-based Textile Room
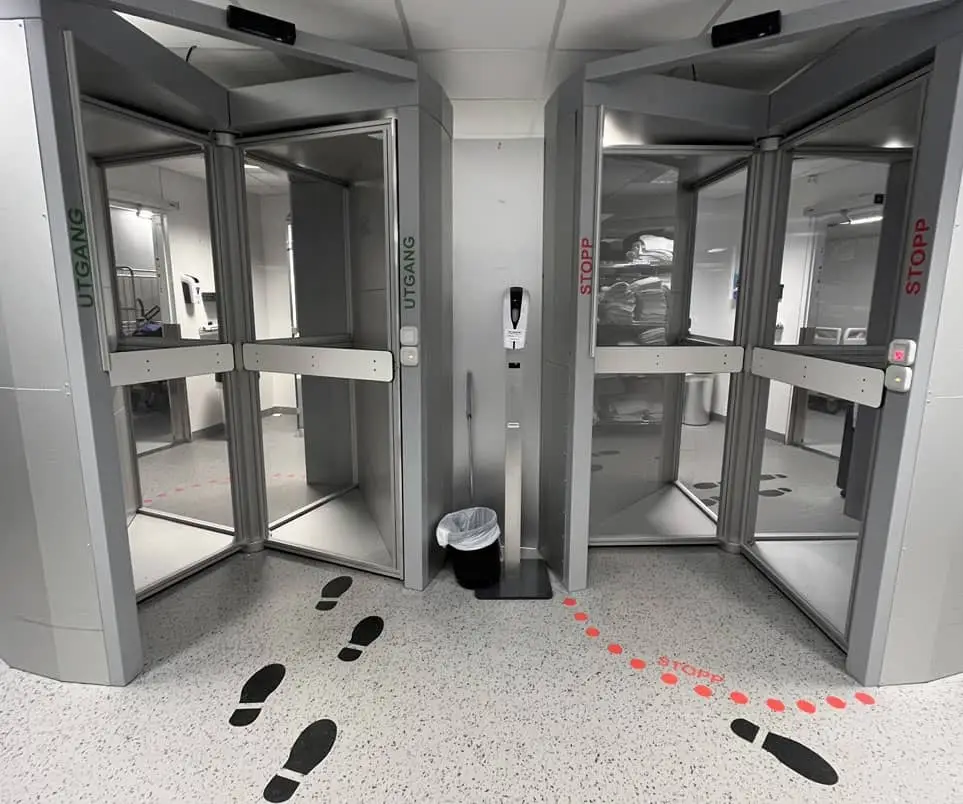
The way into and through the laundry room is marked. The RFID card must be presented here.
The room solution from Deister Electronic functions like a walk-in closet. The intelligent, transparent revolving doors at the entrance and exit of the room solution can only be passed through by users after successful identification.
Before entering the laundry room, employees can check how many garments they are allowed to borrow via a display on the wall. The total number is limited to six garments. If the quota is used up, the employee must first return the worn laundry before being allowed to check out fresh clothing.
The room solution from Deister Electronic functions like a walk-in closet. The intelligent, transparent revolving doors at the entrance and exit of the room solution can only be passed through by users after successful identification.
Before entering the laundry room, employees can check how many garments they are allowed to borrow via a display on the wall. The total number is limited to six garments. If the quota is used up, the employee must first return the worn laundry before being allowed to check out fresh clothing.
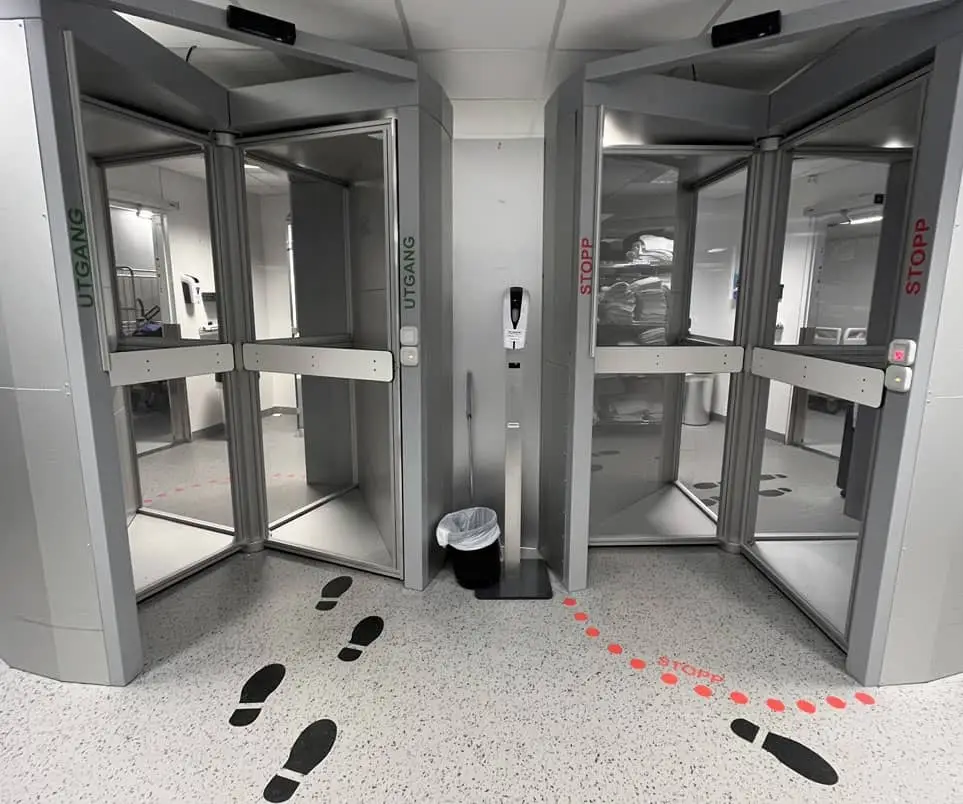
The way into and through the laundry room is marked. The RFID card must be presented here.
The Check-Out Process
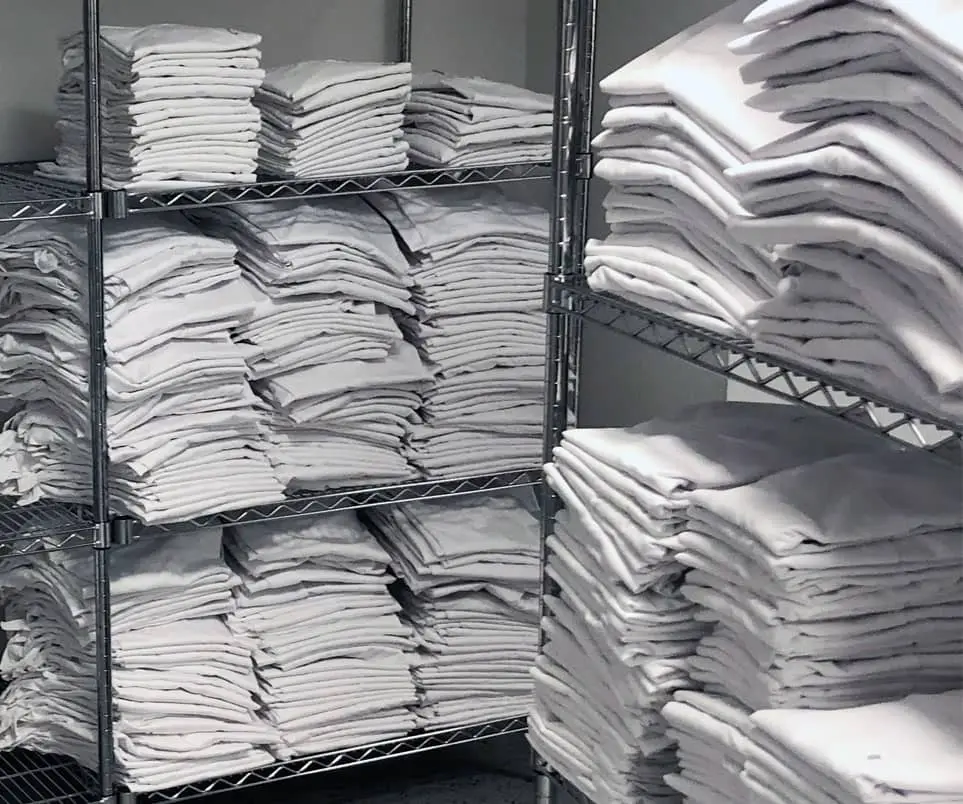
Each employee may remove up to six items of laundry. Additional linen can only be borrowed if worn items are returned. The system precisely controls the removal and distribution for each employee.
The wearer identifies him/herself at the texCarousel with an ID card and then enters the storage room. The wearer then removes the desired garments and leaves the room via the texCarousel at the exit. In the process, the removed clothing is automatically identified and captured, as an RFID chip the size of a small button is sewn into each garment.
The main focus of the room solution is the fast and automated registration of employees and clothing, as for many users, a fast and efficient distribution is particularly important in order to avoid waiting times. Fresh clothing is delivered in standard wire container models via the texGate.
The wearer identifies him/herself at the texCarousel with an ID card and then enters the storage room. The wearer then removes the desired garments and leaves the room via the texCarousel at the exit. In the process, the removed clothing is automatically identified and captured, as an RFID chip the size of a small button is sewn into each garment.
The main focus of the room solution is the fast and automated registration of employees and clothing, as for many users, a fast and efficient distribution is particularly important in order to avoid waiting times. Fresh clothing is delivered in standard wire container models via the texGate.
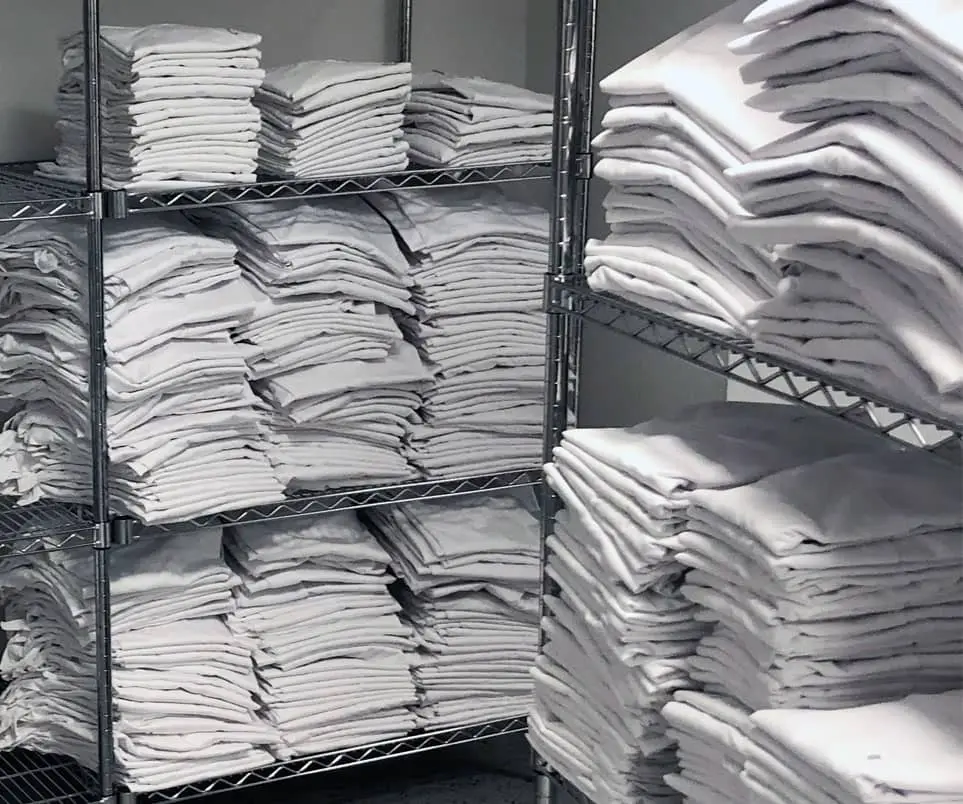
Each employee may remove up to six items of laundry. Additional linen can only be borrowed if worn items are returned. The system precisely controls the removal and distribution for each employee.
Commissioning and Costs
The remodeling and installation of the laundry room began in January 2021 and was completed in May 2021. The tags are attached to the workwear by the laundry service provider. The cost of the entire installation was 300,000 euros, including the structural changes and costs for IT, without additional monthly costs.
In theory, the hospital management expects the expenditure to be amortized after ten years. However, employee satisfaction is not something that can be calculated in figures. According to Vibeke Mikalsen, this advantage outweighs the economic benefit.
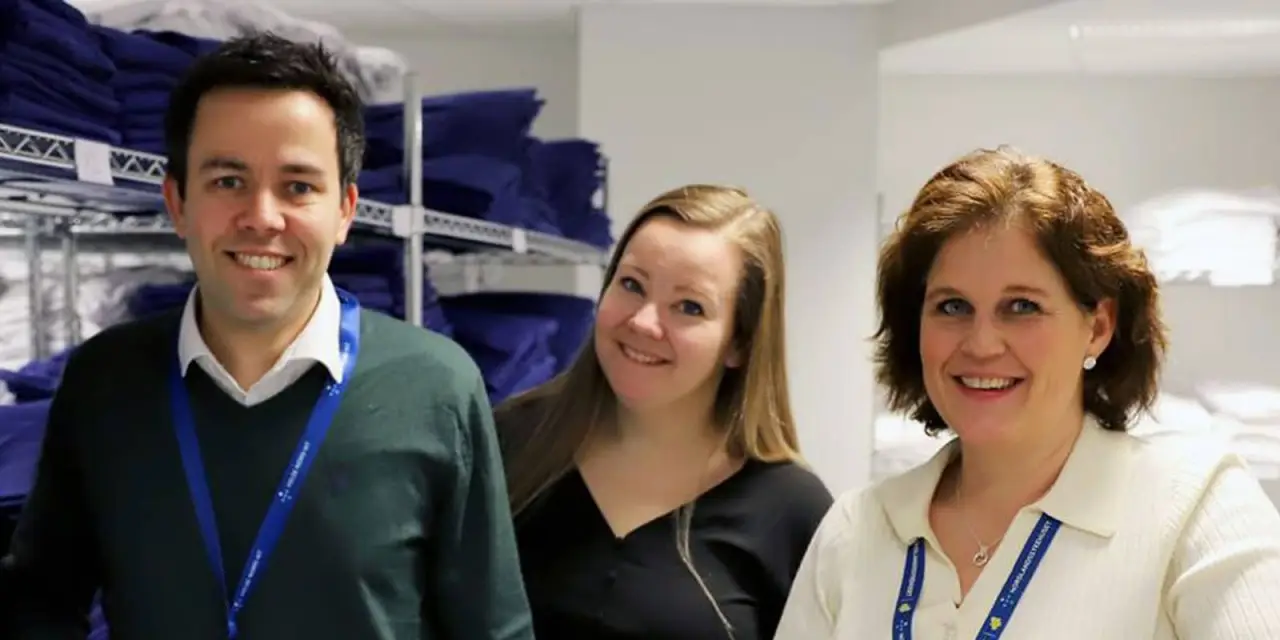
Jan-Inge Johannessen, Susanne Simonsen and Vibeke Mikalsen managed the entire project and are pleased with the success.
Laundry Quota Halved
Advantages
Textile Management Since 2021 With RFID
- Sufficient supply of clean laundry at all times 24/7
- Access to laundry available at all times
- Less rented linen in circulation
- Laundry items are identifiable
- Access to laundry is controlled
- Reduction of the risk of infection
- Improved fire safety
- More manageable and fool-proof return of used clothes
- Valid figures and statistics on consumption and better planning
Back when the distribution of clothing was still done manually. The laundry company Nor Tekstil had about 50,000 garments in circulation. Now there are only about 30,000, which means a saving of 175,000 euros in a leasing period for 5–10 years. In addition, there is a positive impact on the environment, as the laundry quota is reduced.
"The new solution benefits everyone: the patients, the employees, hygiene, the environment and – through the cost reduction – also the clinic's management," explains Vibeke Mikalsen.
Satisfied Employees
After the employees' familiarization period with the system, the processes improved quickly. The fact that laundry is available at all times and that work clothes are guaranteed to be in the right size was very positively received.
For some employees, however, the new textile management solution meant a major change. Laundry now has to be returned before new items can be borrowed. If the quota is used up, access to the textile room is denied.
Back when the distribution of clothing was still done manually. The laundry company Nor Tekstil had about 50,000 garments in circulation. Now there are only about 30,000, which means a saving of 175,000 euros in a leasing period for 5–10 years. In addition, there is a positive impact on the environment, as the laundry quota is reduced.
"The new solution benefits everyone: the patients, the employees, hygiene, the environment and – through the cost reduction – also the clinic's management," explains Vibeke Mikalsen.
Satisfied Employees
After the employees' familiarization period with the system, the processes improved quickly. The fact that laundry is available at all times and that work clothes are guaranteed to be in the right size was very positively received.
For some employees, however, the new textile management solution meant a major change. Laundry now has to be returned before new items can be borrowed. If the quota is used up, access to the textile room is denied.
Textile Management Since 2021 With RFID
- Sufficient supply of clean laundry at all times 24/7
- Access to laundry available at all times
- Less rented linen in circulation
- Laundry items are identifiable
- Access to laundry is controlled
- Reduction of the risk of infection
- Improved fire safety
- More manageable and fool-proof return of used clothes
- Valid figures and statistics on consumption and better planning
"The laundry company Nor Tekstil has sewn the RFID chips into the work clothes. The delivery and collection of the clothes takes place five times a week."
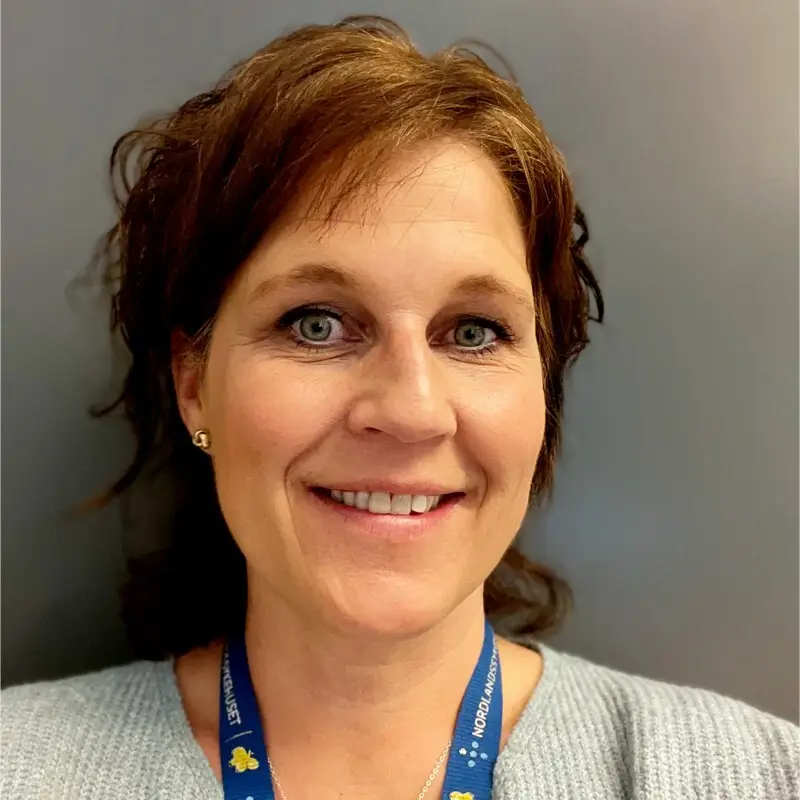
textag Textile Management
Solution Provider Deister Electronic
Deister Electronic was founded in 1978 and is now one of the world's leading medium-sized companies for electronic safety systems and identification systems for industrial automation with over 200 employees and subsidiaries in five countries.
To this day, Deister Electronic is a family-run company rooted in the Hannover region of Germany.
Textile Management with texRoom
The textile room solution that Deister Electronic implemented at Nordland Hospital is called texRoom.
The core idea of texRoom is a central room solution with a textile distribution system, which is individually projected and implemented according to customer requirements. texRoom is freely scalable and can be expanded with the cabinet solution texCabinet.
Both solutions use so-called texReturn cabinets for the return of clothing. Items removed from a texRoom or returned in a texReturn are booked in the respective personnel account in the Commander Connect software. This achieves greater hygiene, efficiency and digitalization in workwear management and the entire laundry cycle.
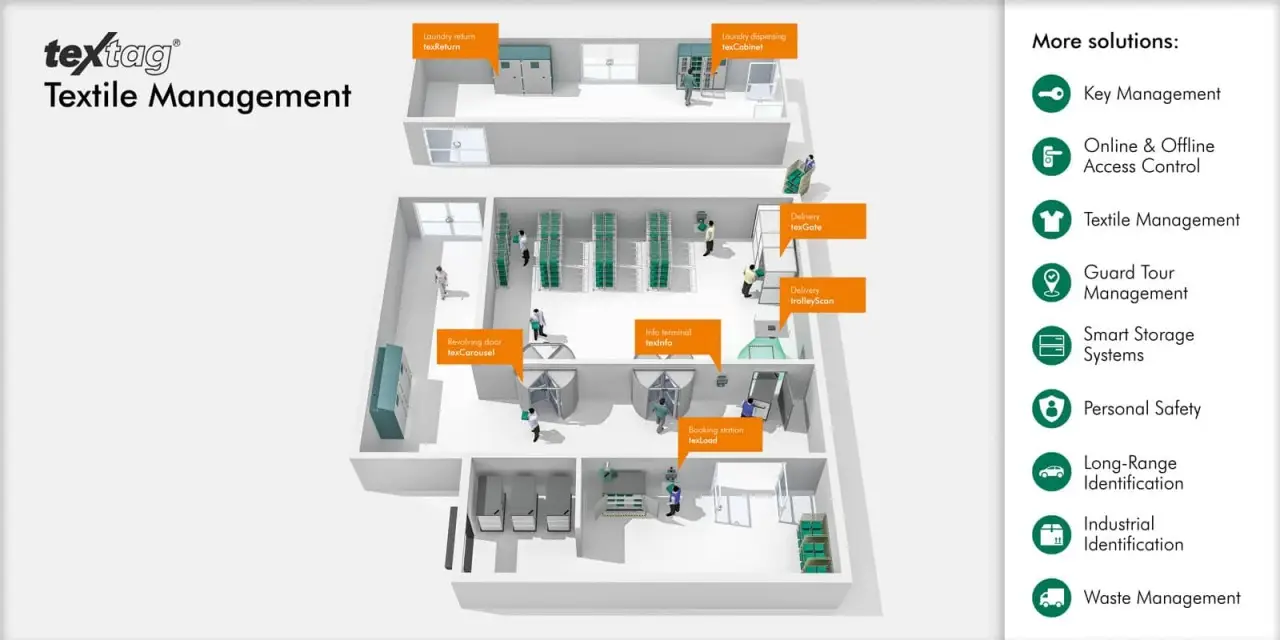
Textile Management with texRoom
"For more than 40 years, Deister Electronic has been providing RFID solutions for securing people, objects and buildings, including numerous solutions for the healthcare sector."
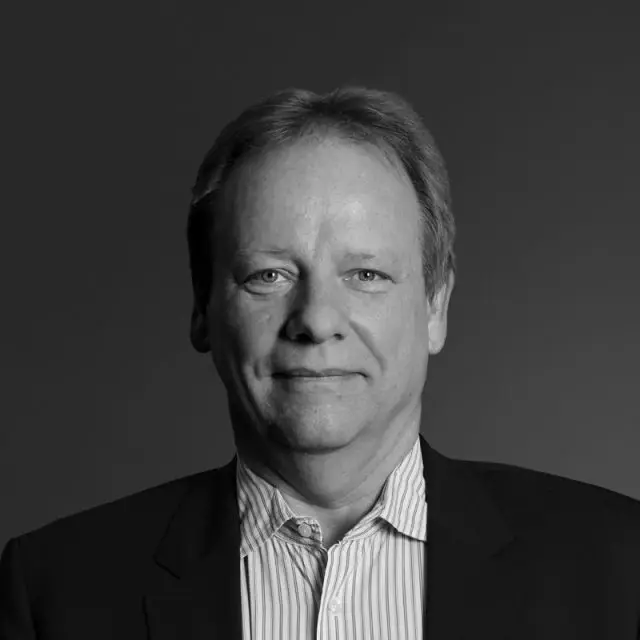