Heat-Not-Burn Products
Delivering a Smoke-Free Future
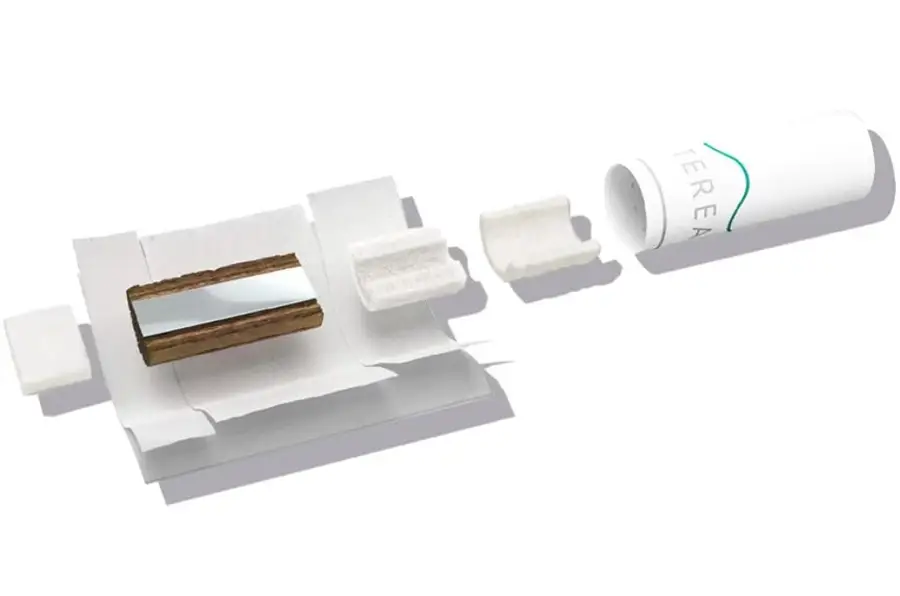
TEREA are heated tobacco sticks designed for use with IQOS ILUMA devices.
Since 2008, PMI has been working on developing and scientifically assessing less harmful smoke-free alternatives. The most successful smoke-free product, IQOS, was launched in 2014. Smoke-free products are manufactured in PMI's factories in Switzerland, Italy, Greece, Romania, Poland, Korea and Indonesia. Company´s vision – shared by all at PMI – is that smoke-free products will one day replace cigarettes.
Ten years ago, PMI made a huge step towards making this vision a reality by making IQOS available for adult smokers for the first time. In the past ten years, the company has continuously innovated and expanded our portfolio of smoke-free products driven by consumers’ needs and expectations and backed by science. Today, its smoke-free products are available in 80+ markets globally, offering millions of adult smokers a range of better alternatives to continued smoking.
Today, IQOS is the no. 1 tobacco heating system globally with more than 28 million users, of which approximately 20.8 million stopped smoking, with the balance in various stages of conversion. In Japan, where IQOS was first launched 10 years ago, nearly 1/3 of adult smokers are using IQOS.
Since 2008, PMI has been working on developing and scientifically assessing less harmful smoke-free alternatives. The most successful smoke-free product, IQOS, was launched in 2014. Smoke-free products are manufactured in PMI's factories in Switzerland, Italy, Greece, Romania, Poland, Korea and Indonesia. Company´s vision – shared by all at PMI – is that smoke-free products will one day replace cigarettes.
Ten years ago, PMI made a huge step towards making this vision a reality by making IQOS available for adult smokers for the first time. In the past ten years, the company has continuously innovated and expanded our portfolio of smoke-free products driven by consumers’ needs and expectations and backed by science. Today, its smoke-free products are available in 80+ markets globally, offering millions of adult smokers a range of better alternatives to continued smoking.
Today, IQOS is the no. 1 tobacco heating system globally with more than 28 million users, of which approximately 20.8 million stopped smoking, with the balance in various stages of conversion. In Japan, where IQOS was first launched 10 years ago, nearly 1/3 of adult smokers are using IQOS.
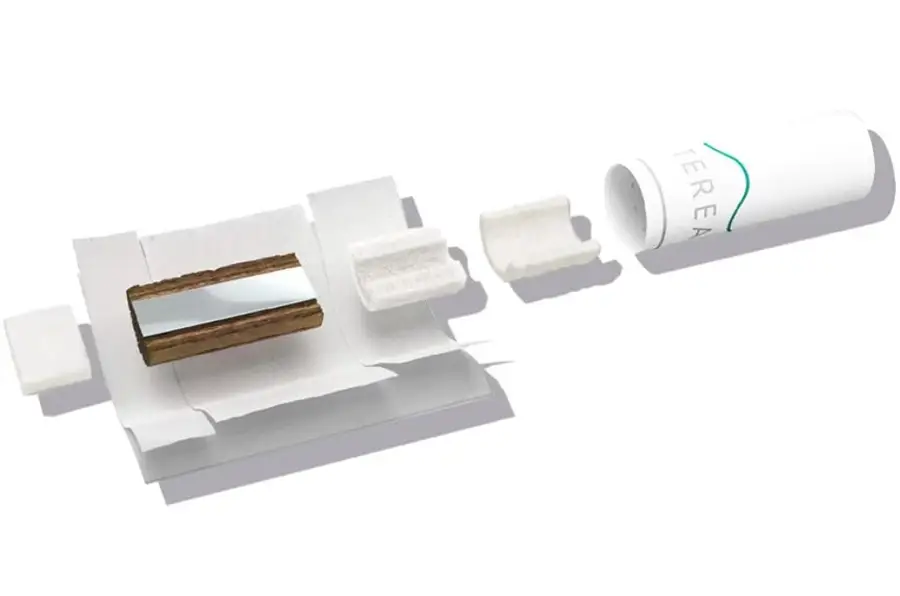
TEREA are heated tobacco sticks designed for use with IQOS ILUMA devices.
Making Heat-Not-Burn Products
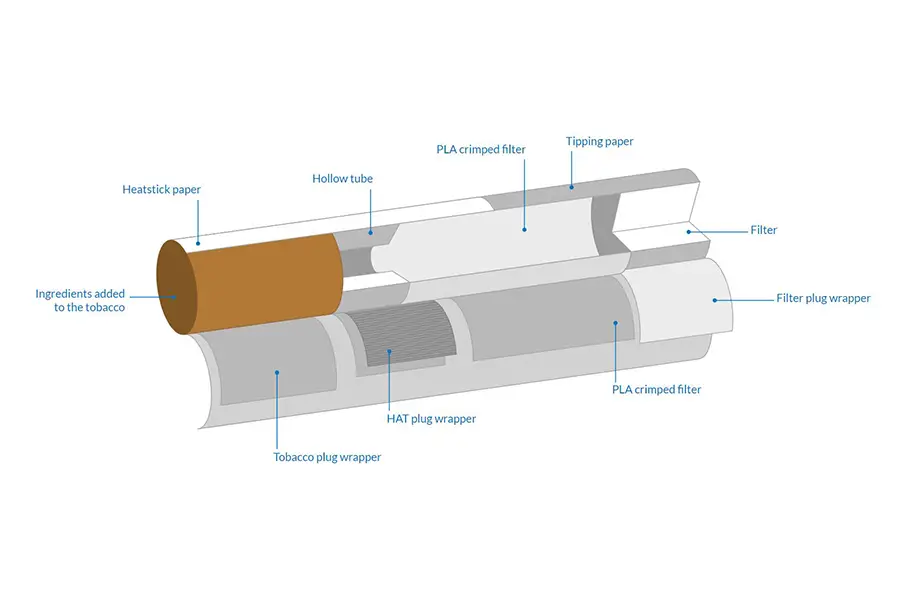
HEETS are specially designed tobacco products that contain tobacco material and several filter sections. These heated tobacco units are also intended for use with IQOS heating devices.
Heated tobacco products (HTPs), also known as heat-not-burn products, are electronic devices which heat tobacco without burning it to release a nicotine-containing aerosol, providing adults with a better alternative to continued smoking. They use consumable tobacco sticks, which are inserted into the device by consumers, and are disposed of after use.
Heated tobacco sticks (also known as heated tobacco units, or HTPs) are processed tobacco plugs designed for heating. The tobacco plug is made from tobacco leaves, which are ground and reconstituted into tobacco sheets, called cast-leaf. These sheets are then crimped and made into a tobacco plug. The latest generation of HTP also has a unique metal heating element coated with stainless steel for efficient tobacco heating.
Manufacturing heated tobacco products is an entirely different process than conventional cigarette making.
Heated tobacco products (HTPs), also known as heat-not-burn products, are electronic devices which heat tobacco without burning it to release a nicotine-containing aerosol, providing adults with a better alternative to continued smoking. They use consumable tobacco sticks, which are inserted into the device by consumers, and are disposed of after use.
Heated tobacco sticks (also known as heated tobacco units, or HTPs) are processed tobacco plugs designed for heating. The tobacco plug is made from tobacco leaves, which are ground and reconstituted into tobacco sheets, called cast-leaf. These sheets are then crimped and made into a tobacco plug. The latest generation of HTP also has a unique metal heating element coated with stainless steel for efficient tobacco heating.
Manufacturing heated tobacco products is an entirely different process than conventional cigarette making.
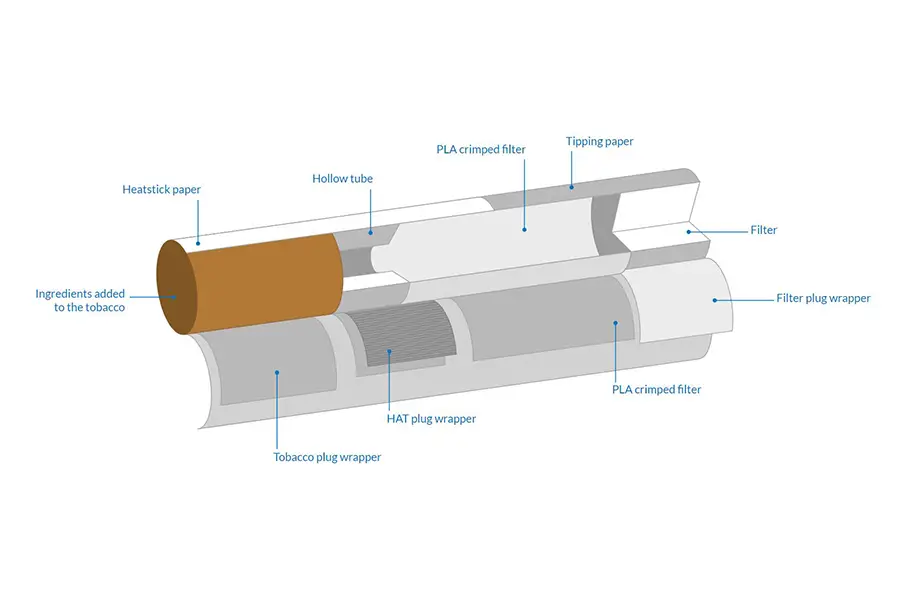
HEETS are specially designed tobacco products that contain tobacco material and several filter sections. These heated tobacco units are also intended for use with IQOS heating devices.
OPC UA Journey
Heterogenous Technologies
Some of PMI's older production equipment is not Industry 4.0-ready. Josselin Vallee, Manager for Machine Integration & Supervision at PMI, describes this as a "jungle of very different technologies". In this heterogeneous machine park, only five data points could typically be collected using various communication standards. These were mainly used for performance monitoring. Using advanced Industry 4.0 tech was difficult.
In order to facilitate the seamless production across various machines from different manufacturers, an interoperable communication standard was required. As a result, in 2017, PMI joined the OPC Foundation and started using OPC UA.
"We needed a way to communicate with our machines," explains Josselin Vallee. OPC UA stood out as a communication platform because it seamlessly connects information technology (IT) and operational technology (OT).
To speed up data exchange across the industry, leading international tobacco products manufacturers, including PMI, and the OPC Foundation formed a working group. Together, they created the companion specification "Tobacco Machine Communication" (TMC), version 1.0 in 2017.
The latest version of TMC (version 2.0) has been available since June 2022 after incorporating the learnings of applying the specification in a manufacturing environment. It aims to make data exchange and interoperability requirements work smoothly for both tobacco product manufacturers and OEMs.
In its smoke-free production facilities, PMI is leveraging OPC UA for smarter manufacturing.
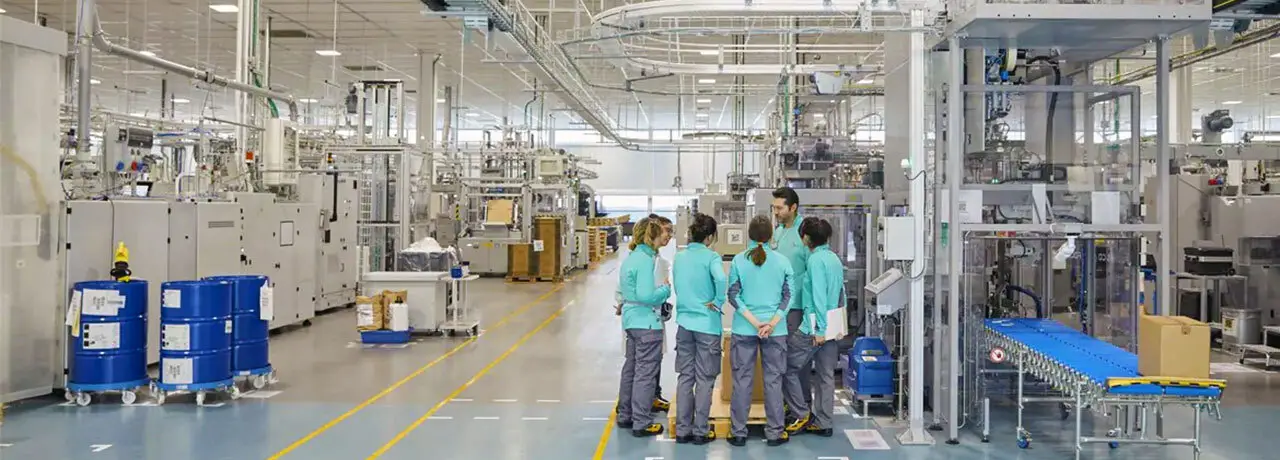
Now, with OPC UA and the TMC Server, employees can access rich and structured information from production equipment for an increasingly data-driven manufacturing environment.
"Due to the emergence and rapid expansion of new smoke-free products, there was a need to employ various new production machines and processes. Consequently, a universal communication standard for these machines became essential requirement."
Pilot Phase and Simulation
The Pilot Use Case
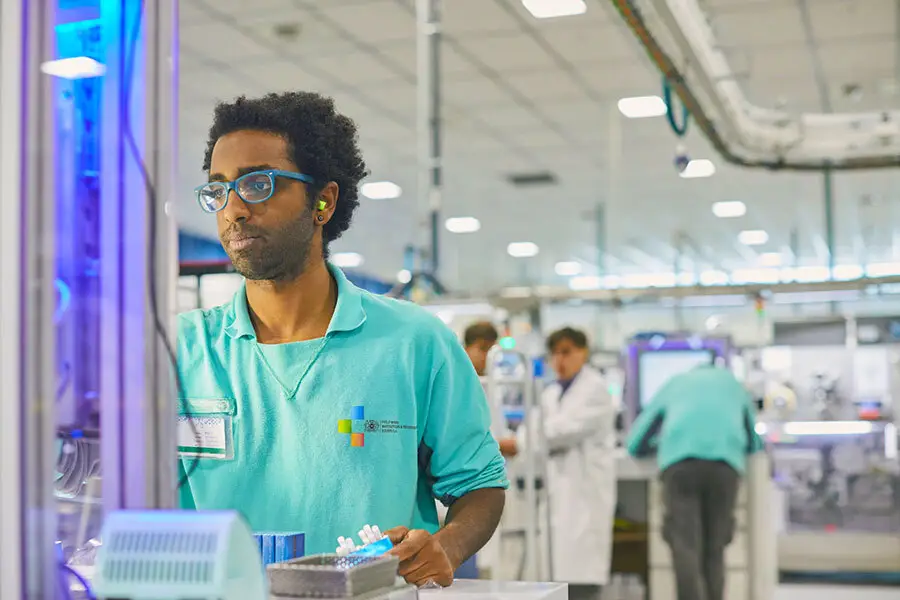
During the pilot project, PMI ascertained that OPC UA met its business objectives.
In the first use case, an automated material identification, traceability, and integration solution was created. PMI integrated OPC UA and the TMC Server to a specific machine.
PMI produces intermediate materials with different recipes and characteristics. When a downstream machine gets these materials, it checks if they match its process order. These materials have different attributes which can influence how they are processed or cause unplanned downtime.
Previously, every incoming material and its label had to be visually checked every four minutes. With limited information on the label, PMI could not get insights on material attributes. It was also difficult to improve their characteristics in upstream production processes.
In the first use case, an automated material identification, traceability, and integration solution was created. PMI integrated OPC UA and the TMC Server to a specific machine.
PMI produces intermediate materials with different recipes and characteristics. When a downstream machine gets these materials, it checks if they match its process order. These materials have different attributes which can influence how they are processed or cause unplanned downtime.
Previously, every incoming material and its label had to be visually checked every four minutes. With limited information on the label, PMI could not get insights on material attributes. It was also difficult to improve their characteristics in upstream production processes.
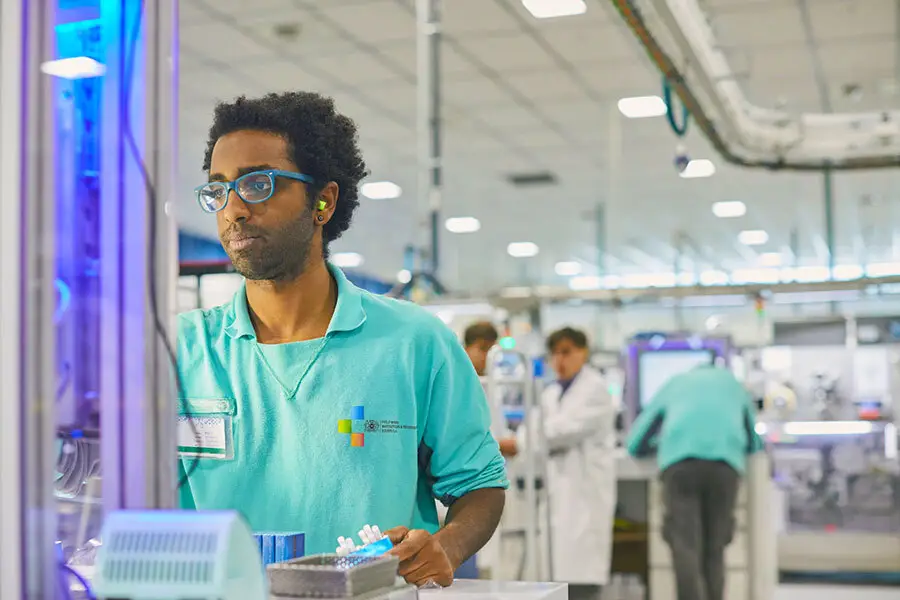
During the pilot project, PMI ascertained that OPC UA met its business objectives.
Validating Solution Based on OPC UA
To fix these issues, PMI created a solution using OPC UA and the TMC companion specification. "The TMC companion specification gathers material, machine, performance, and process order information, all in one place. This makes it easy to receive, check, and send information back and forth.
Now, we can verify material quality with our MES system and collect material and machine information when there are processing issues." explains Josselin Vallee. To speed up the transformation to OPC UA, PMI has collaborated with Aleph Digital Industry, which supported the integration of additional manufacturing micro-services.
Global Roll-out
Encouraged by project early success, PMI is now rolling-out OPC UA for new (native) and legacy (retrofit) equipment. The aim is to enable various Industry 4.0 use cases.
Retrofitting With OPC UA
The Three Main IoT Challenges of Moving to OPC UA
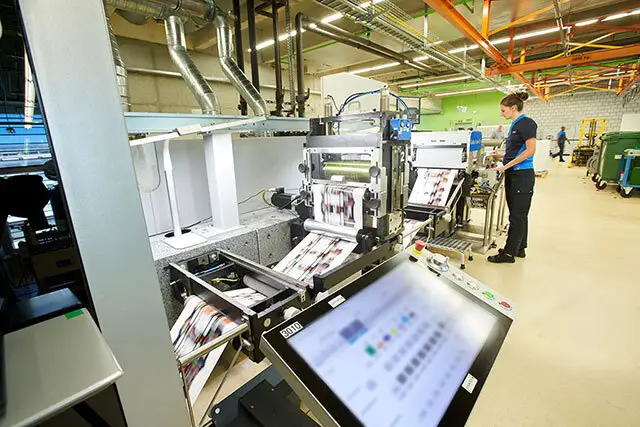
Three issues make integrating OPC UA at PMI challenging.
First: The technical skill and effort needed to implement the companion specification varies from equipment-to-equipment across OEMs. This leads to differences in how well the companion specification is adhered to. Some machines in a production line adhere better than others.
The second challenge is the alignment of the companion specification with the data already available or generated by the equipment in OPC UA and TMC retrofit use cases.
The third challenge revolves around effectively managing the substantial volume of data produced when equipment is OPC UA and TMC-enabled.
Three issues make integrating OPC UA at PMI challenging.
First: The technical skill and effort needed to implement the companion specification varies from equipment-to-equipment across OEMs. This leads to differences in how well the companion specification is adhered to. Some machines in a production line adhere better than others.
The second challenge is the alignment of the companion specification with the data already available or generated by the equipment in OPC UA and TMC retrofit use cases.
The third challenge revolves around effectively managing the substantial volume of data produced when equipment is OPC UA and TMC-enabled.
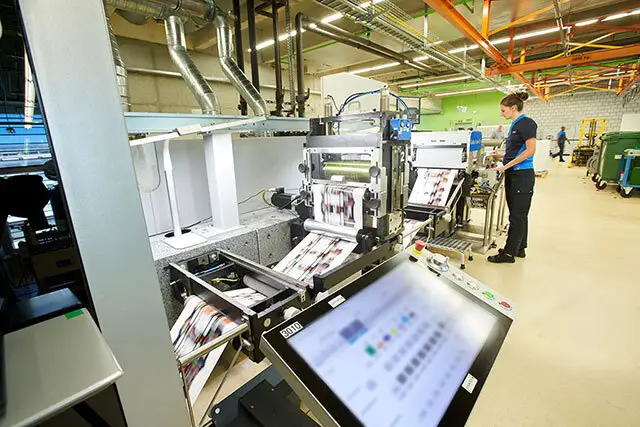
Matching an Existing Machine Capability
"There is often a gap between the capabilities of a machine one wishes to retrofit and what the accompanying specification dictates. However, some parts of our information model are empty because additional logic has to be implemented in the system of machines to fulfill our specification conformance units", explains Josselin Vallee. "Our transformation with OPC UA and TMC is not 'just' about standardizing data exchange, but also standardizing, to some extent, machine functionality."
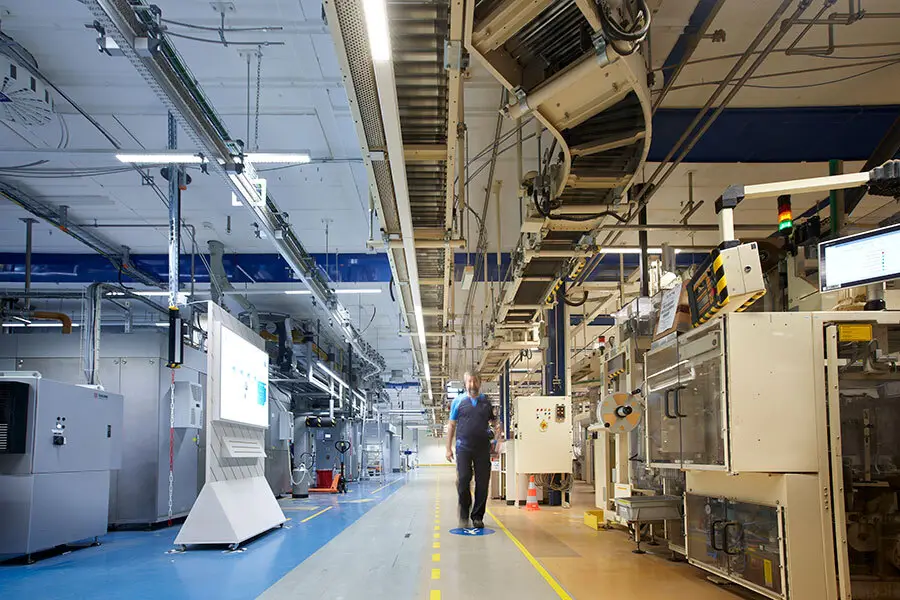
In a retrofit, additional sensors and IoT gateways are integrated, if possible, in order to communicate with PMI’s industrial cloud.
Data Management
OPC UA, paired with TMC, provides PMI with more detailed, clear, and frequent information.
Ingesting, storing, and computing large amounts of information from manufacturing processes, at higher frequencies, was a complex challenge. Nevertheless, the entire new dimension of information exchange, powered by OPC UA, opens big opportunities for scalable Industry 4.0 solutions at PMI.
“From just five standard data points we had in the past, we now have access to hundreds, if not thousands. We have also drastically increased the frequency of data exchange from two-digit seconds to one-digit. This means large amounts of data exchanged, and results in an intense strain on the machine hardware and on our IT infrastructure.“
Speed Management
Machine Orchestration Powered by OPC UA
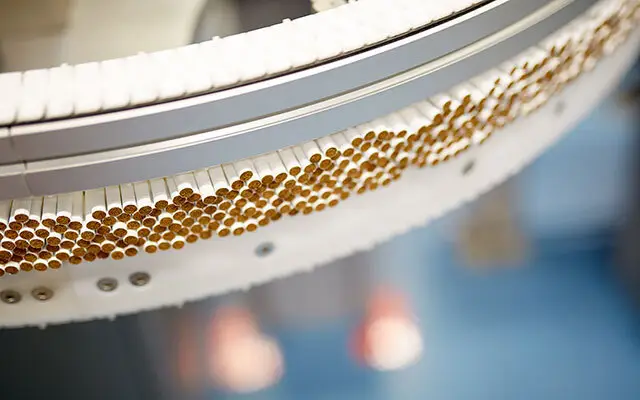
Some material is stored in-between machines in material buffers to prevent machine downtime.
In high-speed production, syncing machine speeds within a production line is crucial. To decrease the impact of a machine failing, some material is stored in-between machines, in material buffers. When a machine fails, the material buffers hold materials from the upstream machine and feed the downstream machine. This prevents the whole line from stopping.
"Buffers, however, store limited amounts of materials. The speed of machines using these buffers impacts how long before we run out and the whole line stops," explains Josselin Vallee.
Reducing the Amount of Buffer Material
Traditionally, PMI controlled machine speeds using machines’ status based on buffer filling levels, and visual observation.
In recent years, PMI has reduced the size of buffers in its production lines. “With smaller buffers, we had to improve equipment speed-control during failures to keep high uptime. Simply acting, based on buffer levels and relying on immediate reaction from our operators, wouldn't be enough. We needed smarter controls."
In high-speed production, syncing machine speeds within a production line is crucial. To decrease the impact of a machine failing, some material is stored in-between machines, in material buffers. When a machine fails, the material buffers hold materials from the upstream machine and feed the downstream machine. This prevents the whole line from stopping.
"Buffers, however, store limited amounts of materials. The speed of machines using these buffers impacts how long before we run out and the whole line stops," explains Josselin Vallee.
Reducing the Amount of Buffer Material
Traditionally, PMI controlled machine speeds using machines’ status based on buffer filling levels, and visual observation.
In recent years, PMI has reduced the size of buffers in its production lines. “With smaller buffers, we had to improve equipment speed-control during failures to keep high uptime. Simply acting, based on buffer levels and relying on immediate reaction from our operators, wouldn't be enough. We needed smarter controls."
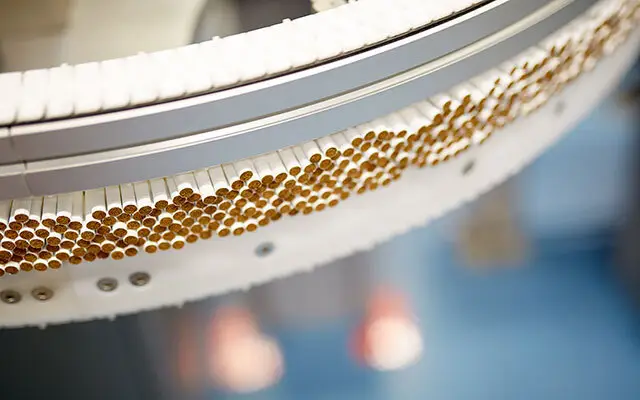
Some material is stored in-between machines in material buffers to prevent machine downtime.
The Speed Management Controller
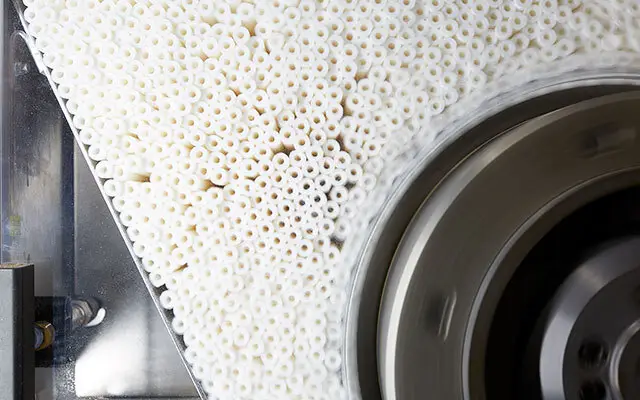
Despite buffers, PMI needed better speed control to keep equipment uptime and yield high.
To tackle this, PMI engaged up with Aleph Digital Industry to create a robust, scalable, and adaptable edge solution to control machines exclusively through OPC UA.
"Aleph has developed the Speed Management Controller (SMC) for PMI, which operates on an edge controller, beside the machines”, explains Diego Paccagnan, CEO of Aleph Digital Industry. SMC continuously learns from each machine's uptime and downtime, monitoring buffer levels, and predicting upcoming stops or restarts. “Based on this information, SMC adjusts the optimal speed for each machine, minimizing blockages or starvations”, says Diego Paccagnan.
With OPC UA and TMC in newly enabled equipment, coordinating machine speed on production and packaging lines becomes more precise. Decisions can be taken based on a large set of data points. This results in a longer mean time between failures and increased uptime, even for highly automated machines.
PMI is now globally implementing SMC, using the OPC UA communication standard’s interoperability and the TMC companion specification for scalability.
To tackle this, PMI engaged up with Aleph Digital Industry to create a robust, scalable, and adaptable edge solution to control machines exclusively through OPC UA.
"Aleph has developed the Speed Management Controller (SMC) for PMI, which operates on an edge controller, beside the machines”, explains Diego Paccagnan, CEO of Aleph Digital Industry. SMC continuously learns from each machine's uptime and downtime, monitoring buffer levels, and predicting upcoming stops or restarts. “Based on this information, SMC adjusts the optimal speed for each machine, minimizing blockages or starvations”, says Diego Paccagnan.
With OPC UA and TMC in newly enabled equipment, coordinating machine speed on production and packaging lines becomes more precise. Decisions can be taken based on a large set of data points. This results in a longer mean time between failures and increased uptime, even for highly automated machines.
PMI is now globally implementing SMC, using the OPC UA communication standard’s interoperability and the TMC companion specification for scalability.
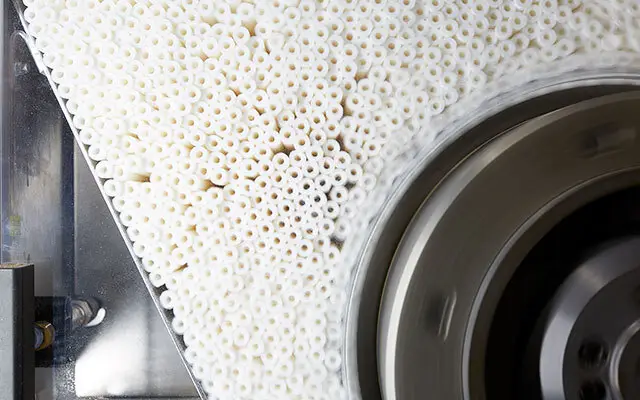
Despite buffers, PMI needed better speed control to keep equipment uptime and yield high.