On-Metal RFID Transponder for Bottle Labeling
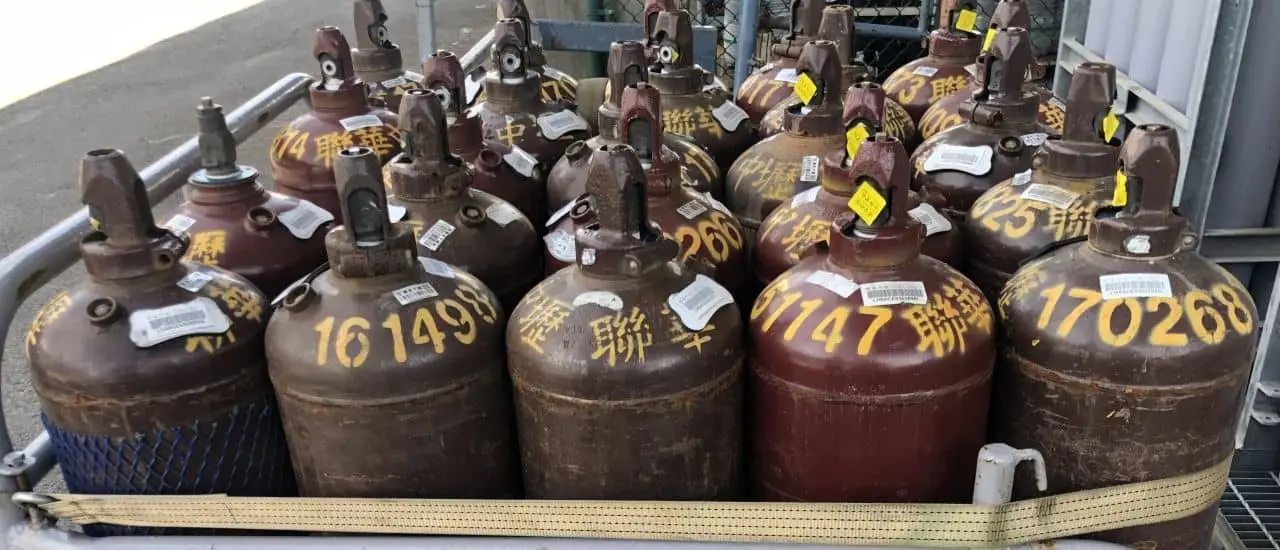
Seamless Tracking of Metal Gas Cylinders and Kegs
B-Id has developed a unique RFID transponder that is suitable for use on metal cylinders and containers. The transponder was originally developed to function at 100 percent on metal gas cylinders, but can also be applied to any metallic object with curved surfaces. A special development is the antenna, which is designed in such a way that the metal cylinder serves as a reinforcement for the antenna.
The Challenges of On-Metal Tagging
Metal has always been a problem for RFID labeling. For LF and HF technologies and products, B-Id relies on absorbent materials to ensure shielding from metal. For UHF RFID antennas, however, the use of absorbent material is not possible. UHF antennas must be specially developed and adapted to the respective application.
All UHF RFID products from B-Id are equipped with customized antennas. One outstanding example is B-Id's innovative On-Metal Soft Tag, which was developed for labeling metal gas cylinders and kegs. The antenna is designed so that the metal surface of the cylinder acts as part of the antenna.
Tag with a Soft Shell
The On-Metal Soft Tag from B-Id is characterized by an innovative 4 millimeter thick flexible shell that enables effortless application to round surfaces. This feature makes it particularly suitable for labeling bottles, especially in demanding industrial environments. Thanks to its adaptability, this label is also ideal for labeling metal kegs. Unlike hard-shell labels, which are easily breakable in the event of collisions, the soft shell of the On-Metal Soft Tag eliminates this risk. This shell is designed to prevent potential breakage, providing a robust and resilient labeling solution for diverse applications. This flexibility not only ensures the integrity of the label, but also optimizes overall durability, especially in environments where impact hazards cannot be ruled out.
Developed for Use in Industrial Environments
The On-Metal Soft Tag from B-Id is characterized by its excellent resistance to extreme pressure. Even under the harshest conditions, the functionality of these transponders remains intact, even if they have to be sandblasted every three to four years.
"A few years ago, one of our industrial customers in Munich was faced with the challenge of finding a solution for the sandblasting process. Based on this request, we developed the on-metal transponder, which is specially designed to withstand the demanding requirements of the sandblasting process."
- Yiwen Jin, Managing Director