Wash Cycles
Reusable Packaging Regulated by Law
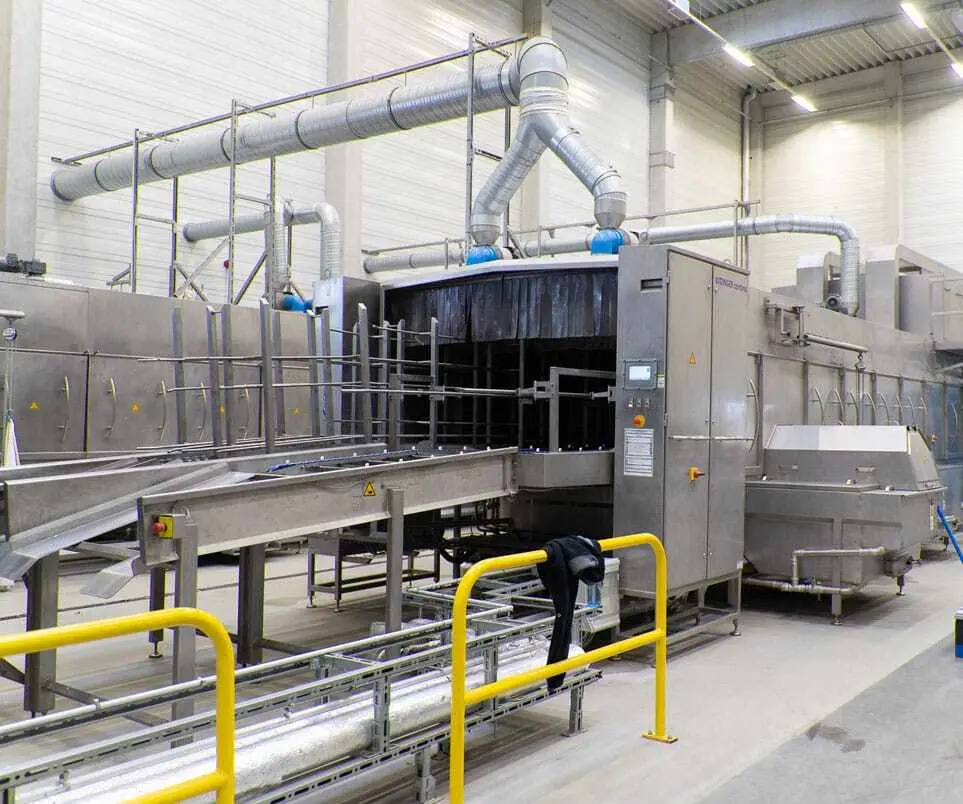
The returnable load carriers are cleaned automatically in the washing system.
German restaurants and catering businesses have been required by law since January 2023 to use reusable containers. Businesses that offer food and drinks to take away or as a delivery service must offer reusable packaging as an alternative to disposable plastic packaging. This regulation is not yet in force in industrial sectors. Disposable packaging and load carriers, whether made of wood, plastic, paper or metal, are often still the order of the day in this sector.
The problems associated with the ecological consequences of this practice are obvious. Plastic packaging and stretch film in particular, which is wrapped around the load like oversized cling film, can rarely be recycled. Disposable packaging also often does not meet the hygiene requirements of the food and consumer goods industry.
German restaurants and catering businesses have been required by law since January 2023 to use reusable containers. Businesses that offer food and drinks to take away or as a delivery service must offer reusable packaging as an alternative to disposable plastic packaging. This regulation is not yet in force in industrial sectors. Disposable packaging and load carriers, whether made of wood, plastic, paper or metal, are often still the order of the day in this sector.
The problems associated with the ecological consequences of this practice are obvious. Plastic packaging and stretch film in particular, which is wrapped around the load like oversized cling film, can rarely be recycled. Disposable packaging also often does not meet the hygiene requirements of the food and consumer goods industry.
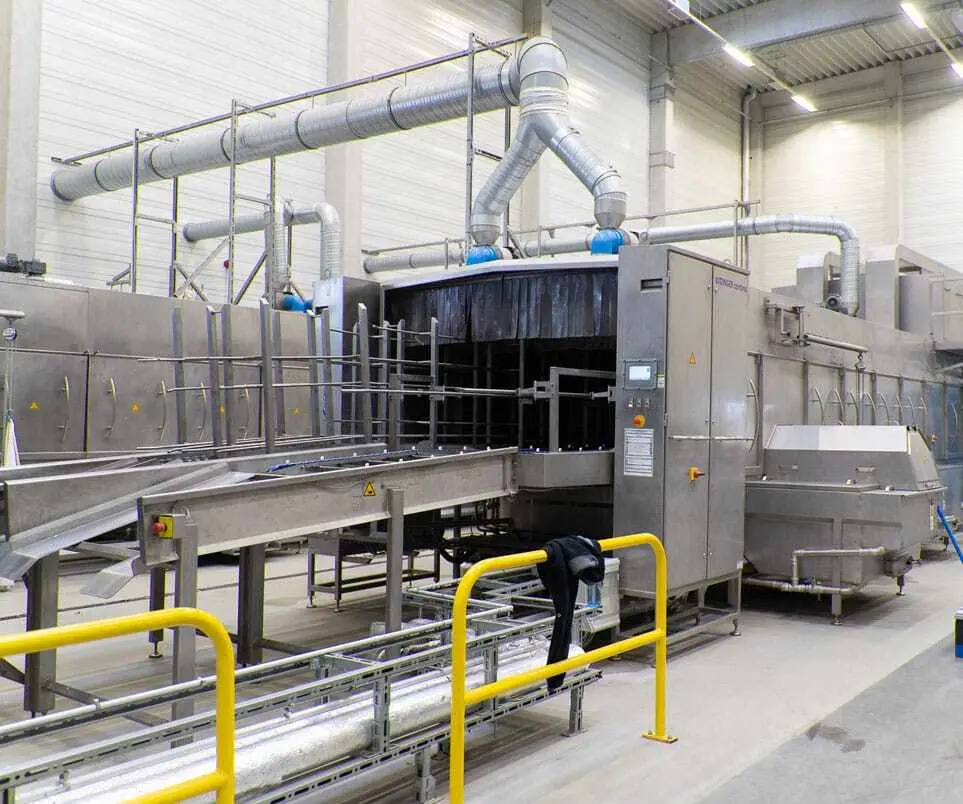
The returnable load carriers are cleaned automatically in the washing system.
“The core of our business is the pooling of returnable transport items. Sustainability is the focus of our business model. This means that we ensure optimum utilization of our truck transports by using returnable load carriers that are optimized for the load capacities of the trucks. The aim is to achieve maximum output with minimum handling and transportation, i.e. to offer our customers the best possible service using as few resources as possible.”
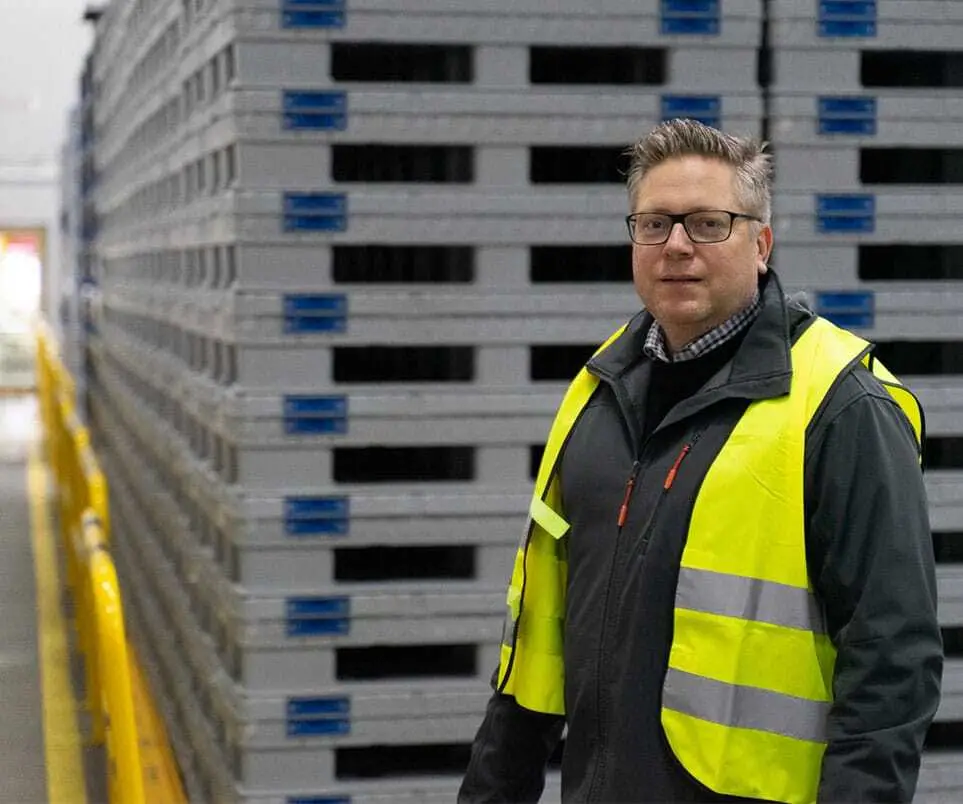
Efficiency Benefit in the Pooling System
In logistics, returnable load carriers are often referred to as returnable transport items or RTIs for short. Customers use the full service provided by Recalo. The pooling operator sends cleaned and reconditioned RTIs to its customers.
These customers use the RTIs to ship their own supplier products and components. Once the RTIs have been dispatched, Recalo organizes the return of the load carriers and takes care of all further processes.
The customer therefore saves the investment in RTIs and has nothing to do with the management, cleaning and repair of returnable load carriers. Peaks in demand can also be bridged at short notice. The RTIs in the pooling system are always in circulation and never stand around unused for long. Thanks to its close network of logistics partners and customers, Recalo can organize the return of the pallets very efficiently and make optimum use of its trucks.
CO<sub>2</sub> Footprint
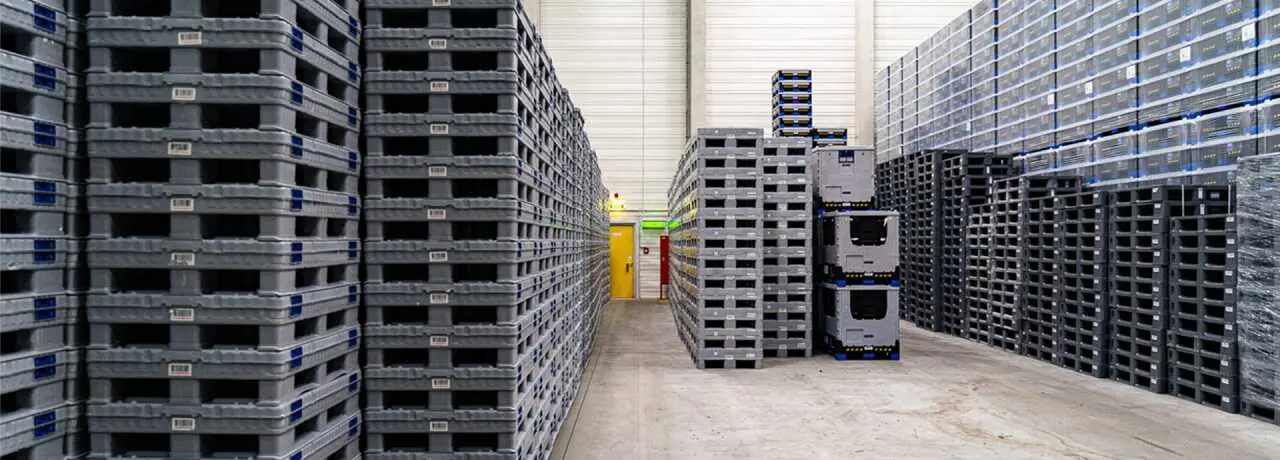
Recalo can respond to fluctuations in demand from its customers at any time and deliver in a short space of time.
Tailored Transport Solution
The company also develops specific load carriers for its customers, such as a collapsible plastic box with a divider shelf, which halves the pressure on the lower boxes and thus prevents unsightly deformation and problems with automatic removal. This box is based on the footprint of a Euro pallet and is almost one meter high when opened out.
After unloading, it can be collapsed and is then only 30 centimeters high with the same footprint, including the divider shelf. The boxes are designed so that the transport space of the truck can always be filled up to the edge of the load – both with the boxes opened out and collapsed.
Another reason for the good CO2 footprint is the long service life of the boxes, which remain in use much longer than wooden pallets. Wood has also poor hygiene properties.
This and the ambiguity about the previous use of a wooden pallet mean that they can only be used to a very limited extent in the hygiene and consumer goods sector. Recalo has once again increased the service life of its boxes with replaceable runners. These are the first elements to wear out and are then simply replaced instead of discarding the entire box.
This increases the service life of the RTI and keeps the CO2 footprint of the entire service at a minimum.
Transparency and Speed
RTI Pooling Reduces Tied-Up Capital
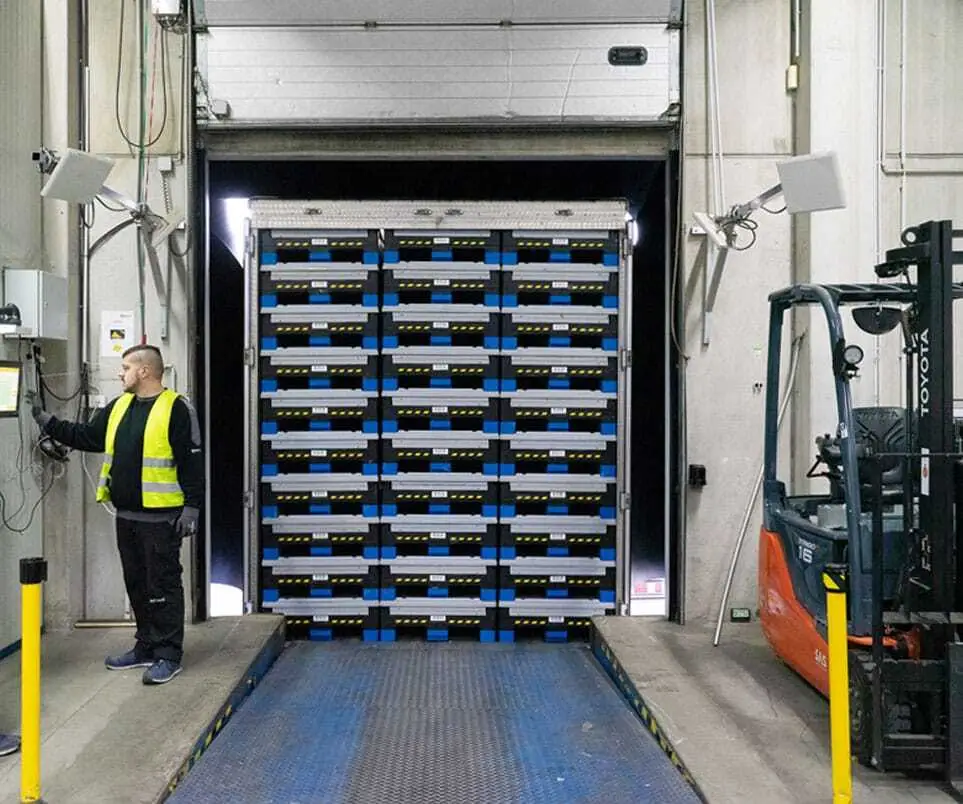
The boxes are designed in such a way that the loading volume of the trucks is always optimally utilized.
Since its founding in 2017, Recalo has been at the nexus of the two global mega trends of sustainability and digitalization. RTI pooling is particularly attractive for retail chains or manufacturers of food, consumer goods and pharmaceuticals.
In a typical application, a manufacturer of packaging trays for fresh meat places an order with Recalo. It receives the load carriers and uses them to supply its customer, the meat processor. The packaging manufacturer would now normally have to ensure that the load carriers are returned on time so that he can serve his next customer.
This is time-consuming and also inefficient due to the limited quantities of load carriers – and would also tie up capital in the load carriers, which would be in the warehouse for a large part of the time, as the demand for RTIs can fluctuate greatly. In the pooling system, customers only ever use as many load carriers as they currently need. When demand peaks, Recalo actively supports its customers with additional RTIs.
The packaging tray manufacturer orders the RTIs from Recalo, loads them and sends its goods to the meat producers, from whom Recalo collects the load carriers.
However, as Recalo not only has a single producer of supplier products, but several customers, the company can organize and plan the return transport much more efficiently than each individual participant in this cycle could on their own.
Recalo also cleans the load carriers, takes care of maintenance and ensures that only intact RTIs remain in the pool. Thanks to its broad customer base, the company can offer its RTI pool not only in Germany, but currently also in 13 other European countries.
Since its founding in 2017, Recalo has been at the nexus of the two global mega trends of sustainability and digitalization. RTI pooling is particularly attractive for retail chains or manufacturers of food, consumer goods and pharmaceuticals.
In a typical application, a manufacturer of packaging trays for fresh meat places an order with Recalo. It receives the load carriers and uses them to supply its customer, the meat processor. The packaging manufacturer would now normally have to ensure that the load carriers are returned on time so that he can serve his next customer.
This is time-consuming and also inefficient due to the limited quantities of load carriers – and would also tie up capital in the load carriers, which would be in the warehouse for a large part of the time, as the demand for RTIs can fluctuate greatly. In the pooling system, customers only ever use as many load carriers as they currently need. When demand peaks, Recalo actively supports its customers with additional RTIs.
The packaging tray manufacturer orders the RTIs from Recalo, loads them and sends its goods to the meat producers, from whom Recalo collects the load carriers.
However, as Recalo not only has a single producer of supplier products, but several customers, the company can organize and plan the return transport much more efficiently than each individual participant in this cycle could on their own.
Recalo also cleans the load carriers, takes care of maintenance and ensures that only intact RTIs remain in the pool. Thanks to its broad customer base, the company can offer its RTI pool not only in Germany, but currently also in 13 other European countries.
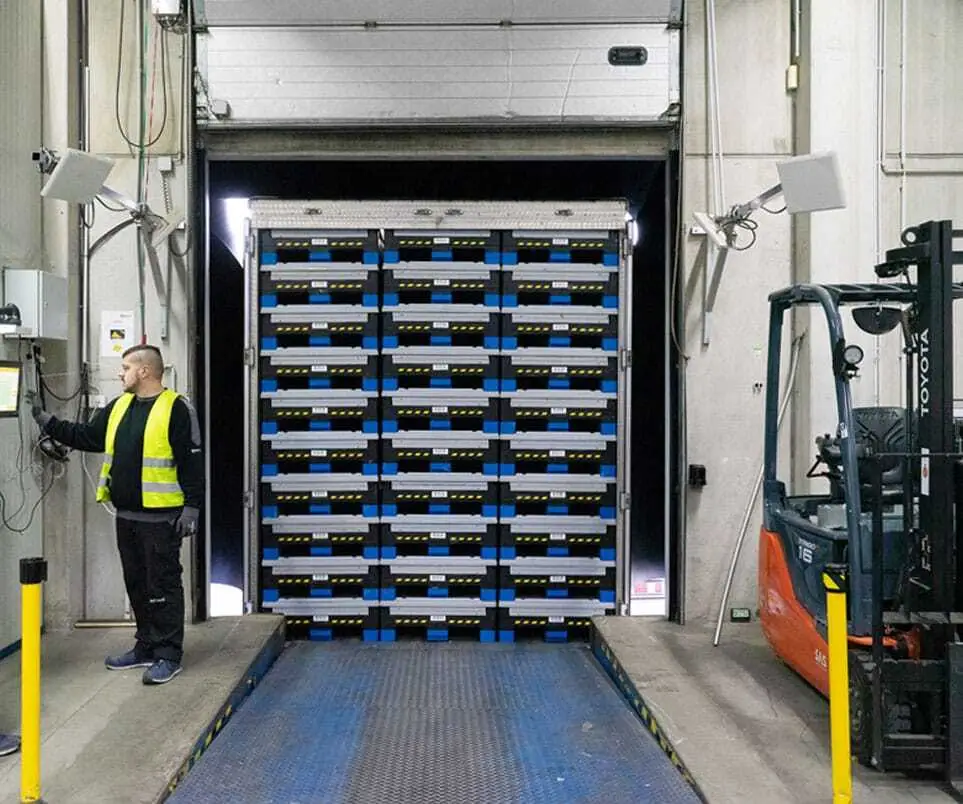
The boxes are designed in such a way that the loading volume of the trucks is always optimally utilized.
The Challenge of Asset Management
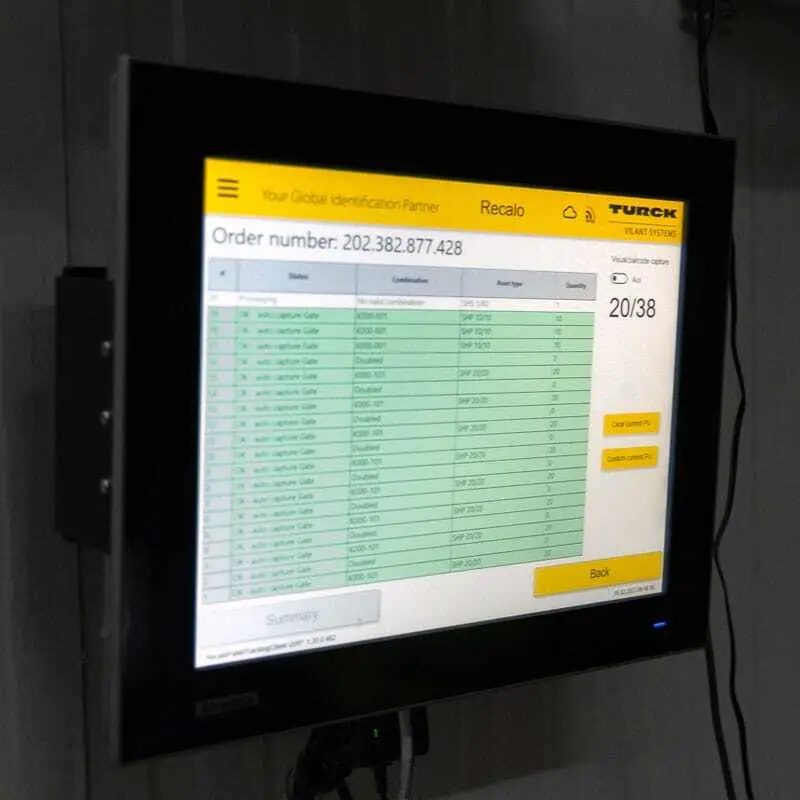
The Turck Vilant Client shows directly whether the truck is filled with the correct boxes at the correct stacking height.
Recalo must constantly keep track of where its customers' RTIs are currently located. The company must ensure that every customer has enough containers to ship their goods. It is obvious that the RTI pool with more than 90,000 units can only be run economically if their logging is fully automated.
Managing director Daniel van der Vorst was quick to rule out the sole use of barcode identification: “The most important decision criteria for an RFID system for us were high data quality, fast bulk recording and the ability to automate our processes.”
When hundreds of boxes are sent to customers, the items have to be recorded in bulk, which is virtually impossible with barcodes. On the other hand, barcodes have the advantage that targeted scanning of individual codes with barcode scanners is often easier than with RFID readers.
Recalo must constantly keep track of where its customers' RTIs are currently located. The company must ensure that every customer has enough containers to ship their goods. It is obvious that the RTI pool with more than 90,000 units can only be run economically if their logging is fully automated.
Managing director Daniel van der Vorst was quick to rule out the sole use of barcode identification: “The most important decision criteria for an RFID system for us were high data quality, fast bulk recording and the ability to automate our processes.”
When hundreds of boxes are sent to customers, the items have to be recorded in bulk, which is virtually impossible with barcodes. On the other hand, barcodes have the advantage that targeted scanning of individual codes with barcode scanners is often easier than with RFID readers.
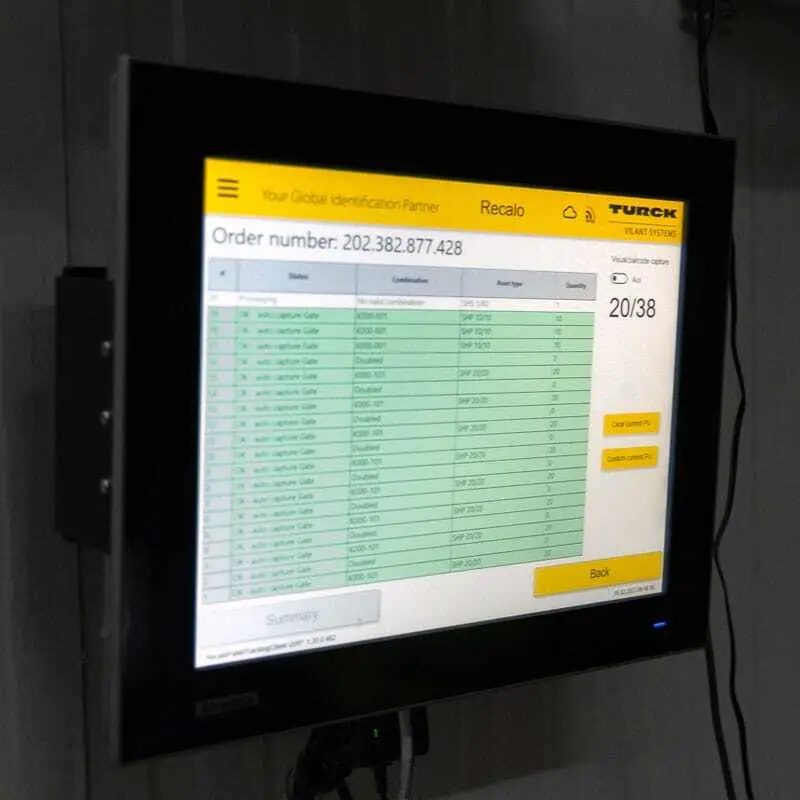
The Turck Vilant Client shows directly whether the truck is filled with the correct boxes at the correct stacking height.
Barcode and RFID
RFID System for Complete Process Transparency
Recalo therefore uses a hybrid solution and equips its pallets with labels that combine barcodes and RFID UHF tags. The hybrid tag enables every Recalo load carrier to be clearly and efficiently identified by the system, regardless of which technology is used at the respective location.
Van der Vorst spoke to the track and trace specialists from Turck Vilant Systems for the first time at a trade fair. “I noticed straight away that Turck Vilant really understood the processes and the problems we face. It was important for us to have an internationally based company as a partner, so that support for our overseas locations is also guaranteed,” says the managing director, describing his reasons.
Turck Vilant Systems developed a complete system for Recalo consisting of RFID read/ write points that are operated via the Turck Vilant Client middleware. They are used to carry out central tasks such as the checking in or out of an RTI in the pool.
This data is then processed by the Turck Vilant Visibility Manager. This server application provides fully automated loading control in close communication with Recalo's ERP system. This full integration of shipment verification with the ERP system was crucial to the success of the solution.
Seamless Tracking Throughout the Entire Logistics Cycle
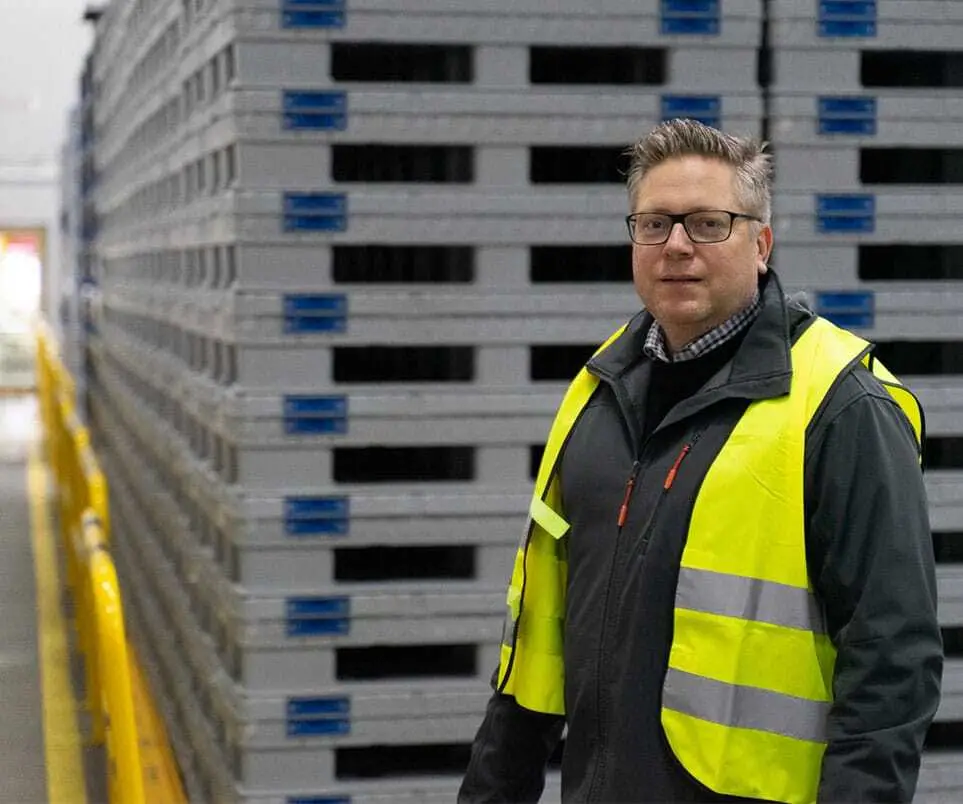
Daniel Van der Vorst, Recalo
Recalo's processes, from shipping to the customer to tracking the boxes in the cycle to their return, are completely paperless.
The RTIs are cleaned, temporarily stored and, if necessary, repaired at the Conditioning Center in Riedstatt near Frankfurt. When a truck is unloaded, the employees transport the stacks of boxes with forklift trucks through an RFID gate that captures their identification numbers. Employees can confirm directly at the gate whether all boxes have been recorded correctly. The employees in Riedstatt are able to load a complete truck in less than half an hour. Up to 20 compactly stacked boxes are simultaneously recorded with a forklift truck through the RFID gate and loaded into the trucks.
The entire process was designed as a digital system. For example, the system knows how high the trailer of the loaded truck is and shows the employees how high the stacks of boxes should be in order to make optimum use of the loading capacity. When the requested boxes pass through the RFID gate, not only are all tags recorded, but the system also checks whether the required stack height has been reached.
Using the direction gate algorithm, the system also determines the direction in which the boxes pass the gate. Anyone who has ever seen how full a truck can be filled with Recalo's standardized system boxes immediately realizes that this level of efficiency would be difficult to achieve manually.
Recalo's processes, from shipping to the customer to tracking the boxes in the cycle to their return, are completely paperless.
The RTIs are cleaned, temporarily stored and, if necessary, repaired at the Conditioning Center in Riedstatt near Frankfurt. When a truck is unloaded, the employees transport the stacks of boxes with forklift trucks through an RFID gate that captures their identification numbers. Employees can confirm directly at the gate whether all boxes have been recorded correctly. The employees in Riedstatt are able to load a complete truck in less than half an hour. Up to 20 compactly stacked boxes are simultaneously recorded with a forklift truck through the RFID gate and loaded into the trucks.
The entire process was designed as a digital system. For example, the system knows how high the trailer of the loaded truck is and shows the employees how high the stacks of boxes should be in order to make optimum use of the loading capacity. When the requested boxes pass through the RFID gate, not only are all tags recorded, but the system also checks whether the required stack height has been reached.
Using the direction gate algorithm, the system also determines the direction in which the boxes pass the gate. Anyone who has ever seen how full a truck can be filled with Recalo's standardized system boxes immediately realizes that this level of efficiency would be difficult to achieve manually.
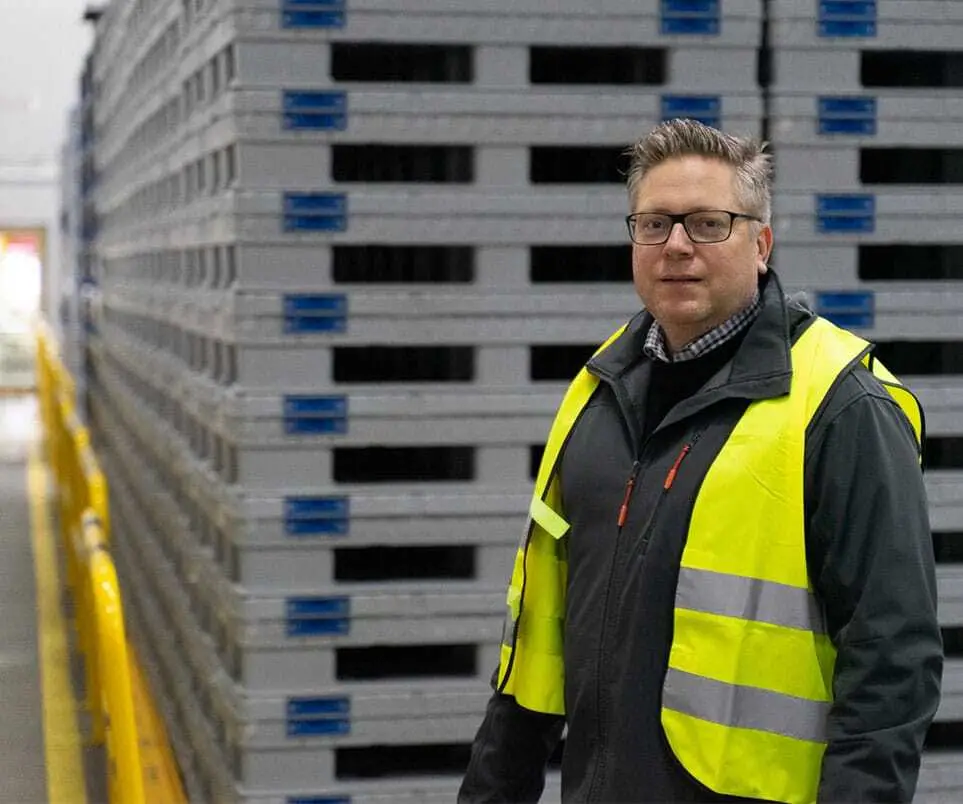
Daniel Van der Vorst, Recalo
"I immediately noticed that Turck Vilant Systems understood our processes and problems. It was important for us to have an international company as a partner, so that support for our overseas locations is also guaranteed."
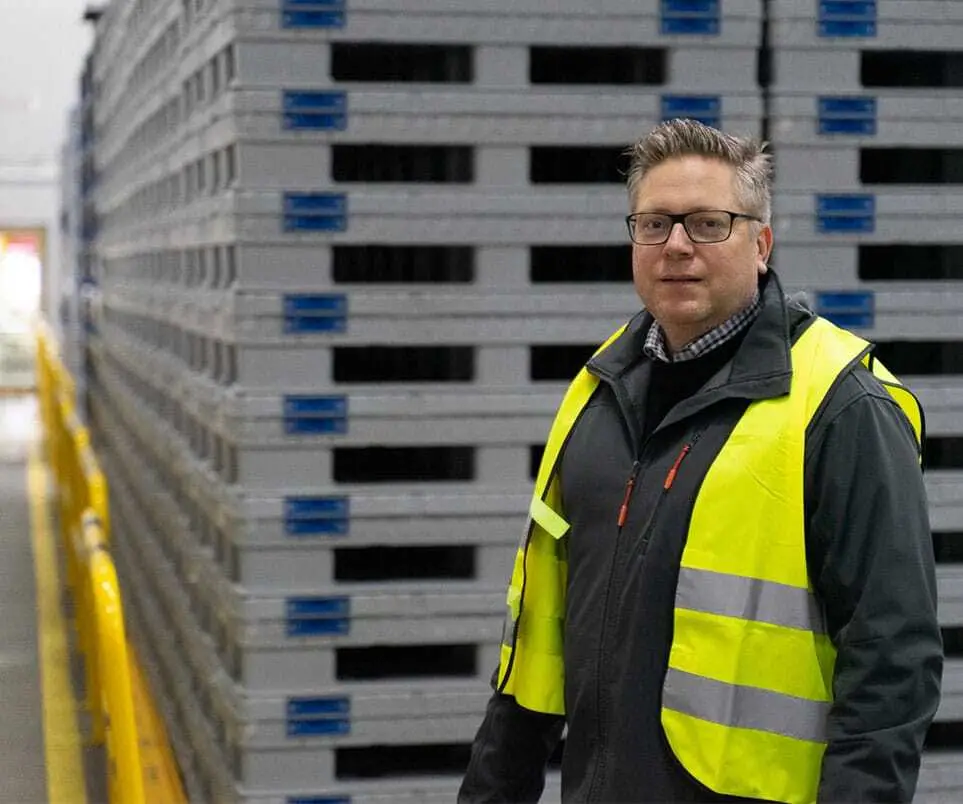
RTI Pool Always in the “Sweet Spot”
To ensure that the entire process chain is recorded seamlessly, the receipt of RTIs by Recalo's customers must also be recorded. This data is transferred to Recalo's ERP system via interfaces so that the company always knows which box is currently in which customer's cycle. This information enables the RTI pool operator to keep their customers' stocks always at the ideal level and indicate impending bottlenecks early on or conversely, request the return of RTIs.
The journey towards the final tracking system, which today very reliably records the boxes in the entire cycle, was not easy, as Daniel van der Vorst emphasizes. “We also found that the implementation process was more complex than expected. Turck Vilant was the right partner for the job. The fact that we have different industrial trucks in operation and numerous combinations of products which we had to accommodate added to the complexity.”
Outlook
Not every site in Europe has yet been fully equipped with the RFID track and trace solution from Turck Vilant Systems. This is set to change in the coming months and years in order to close the gaps in other European countries.
“We will definitely continue to expand the system. It is essential for us to know where our returnable load carriers are at any given time. This means that we will also successively equip our overseas locations with RFID technology so that we have the greatest possible transparency in the flow of goods,” concludes Daniel van der Vorst.