Asset Management
Equipment for the film industry
Every video production, be it a feature length film, a television program, an advertisement or an instructional video, requires an enormous range of equipment. Film companies usually rent the equipment from specialized providers. Dollies, cameras, camera stands, light stands, power supplies and a lot of cables will be ordered and leased for a specific amount of time.
Equipment rental companies assemble the requested material and send it to the film set. In order to track assets and take stock, bar code labels are often adhered to every item. Similar is true for large music, sports or conference events.
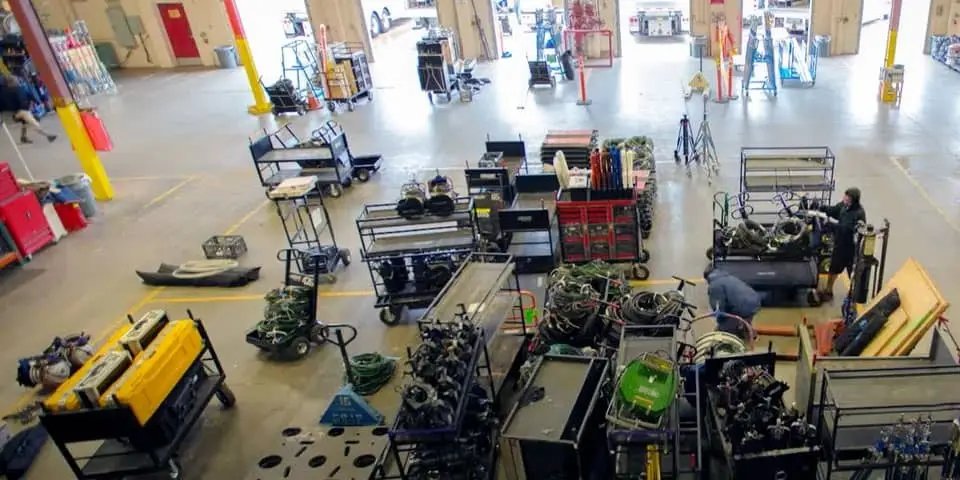
Compiling an order of rental equipment for the film or event industry can involve up to 1,000 different items – including picking the correct cables from an inventory of 25,000 unique cables.
Taking stock of varied equipment
AV equipment leasing companies have very large inventories of a very diverse set of components. Thousands of different kinds of cables are coiled up waiting to be used. The employees’ task is to go into their warehouse, identify exactly the right items using bar code scanners, pull those off the shelf and assemble them in what is called a ‘staging area’.
Employees then verify by manually scanning each item that the assembled kit matches the order completely. Only then can it be dispatched to the customer. This complex process has to be reversed when the customer returns the equipment. Employees then also need to find out which pieces are missing or have been damaged. Then they return the equipment to the shelves in the warehouse.
Time-intensive identification process
With bar code, assembling the kit is very time consuming. Some pieces of equipment are heavy and manipulating them for clear line of sight is cumbersome. Finding exactly the right kind of cable of the correct length also usually took a very long time. “Imagine going into a warehouse and into the cable section”, says Ken Horton of HID.
“There's 25,000 cables on the various shelves and you've got to locate and pull a unique cable that's there.” On top of this difficulty, scanning everything which had finally been assembled in the staging area alone used to take two people two and a half hours to complete for some orders. The same number of hours was necessary upon return of the equipment. Compiling the exception report which states missing or damaged items used to take days.
Human error and loss of business
Scanning bar-code labels manually increases the likelihood of human error and the chance that equipment might be overlooked is high. It also costs video equipment rental companies valuable time. For whilst equipment is waiting to undergo quality control or to be returned to the shelves, it cannot be rented out to a new customer.
Film equipment is identified using RFID
Solving the problem using RFID
With RFID tags attached to every piece of rental equipment, identifying where something is on a shelf is very easy. First the unique identification number of the item in question is pulled up in the software system. A handheld reader can be used in a Geiger counter functionality in which it pings faster as one gets closer to the looked-for object.
This helps greatly in identifying the right kind of cable in fully packed shelves even when there is no line of sight. In the staging area, several RFID tags can be read simultaneously even when the tagged items are already packed in a container. One customer has indicated that a two-person, 2.5 hour process has been reduced by 95 %, to a one person task taking only 15 minutes.
In another case, the check-in process was reduced from 22 minutes to only 10 seconds. Fixed readers or RFID gates shorten the identification time upon return of the equipment. The read result is much more accurate and exception reports can be compiled quickly. They now reach the customer within 90 minutes of returning the kit. Apart from damaged items, all of the returned equipment can be rented out again immediately.
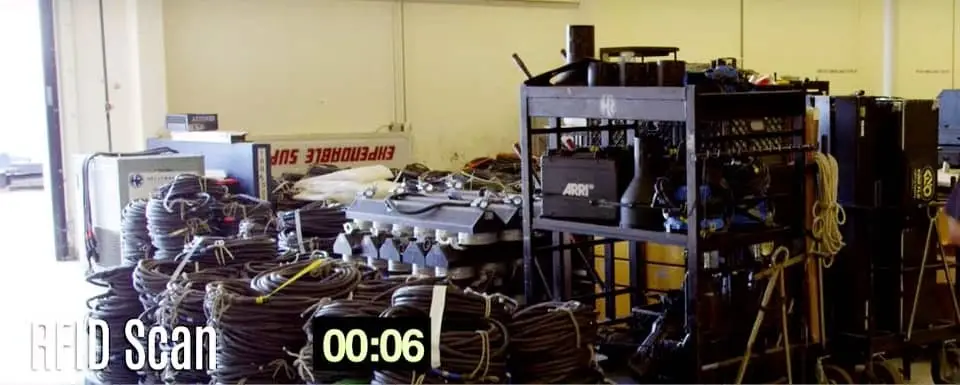
RFID tagged equipment can be read in bulk in a matter of seconds without line of sight – a significant advantage compared to barcodes.
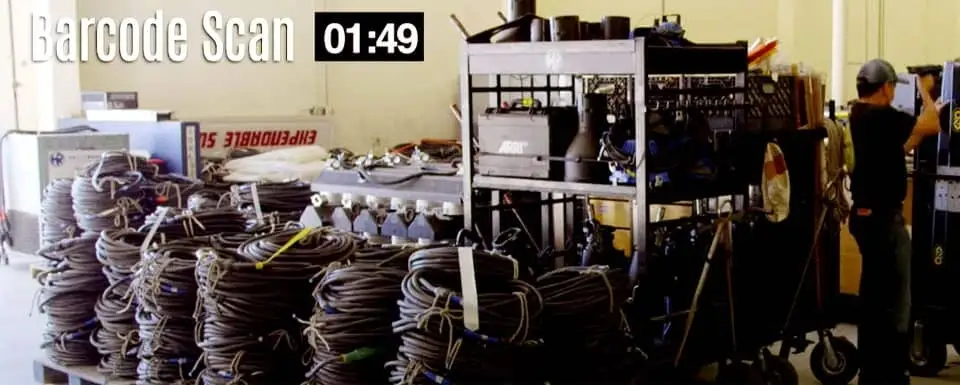
Solving the problem using barcode.
Auto-ID software
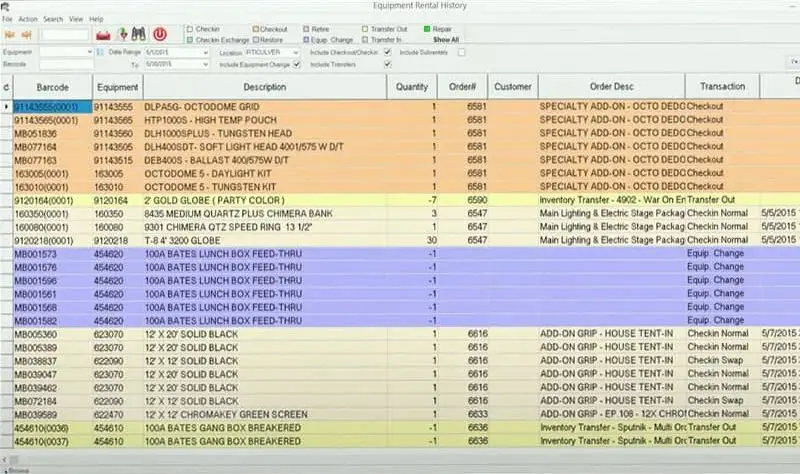
In order to process the unique identification numbers of the video equipment, a specialized software is used. It collects, stores and manipulates the information which is collected from the tags, guarantees fast and accurate information about rental availability and links equipment with necessary accessory items as needed.
So as to simplify an order list, parent and child relationships can be defined within the software. For example, a camera kit which has a set of 20 lenses enclosed may show as one item instead of 21 items. The data is increasingly stored in a cloud and can be accessed through smartphone apps.
In order to process the unique identification numbers of the video equipment, a specialized software is used. It collects, stores and manipulates the information which is collected from the tags, guarantees fast and accurate information about rental availability and links equipment with necessary accessory items as needed.
So as to simplify an order list, parent and child relationships can be defined within the software. For example, a camera kit which has a set of 20 lenses enclosed may show as one item instead of 21 items. The data is increasingly stored in a cloud and can be accessed through smartphone apps.
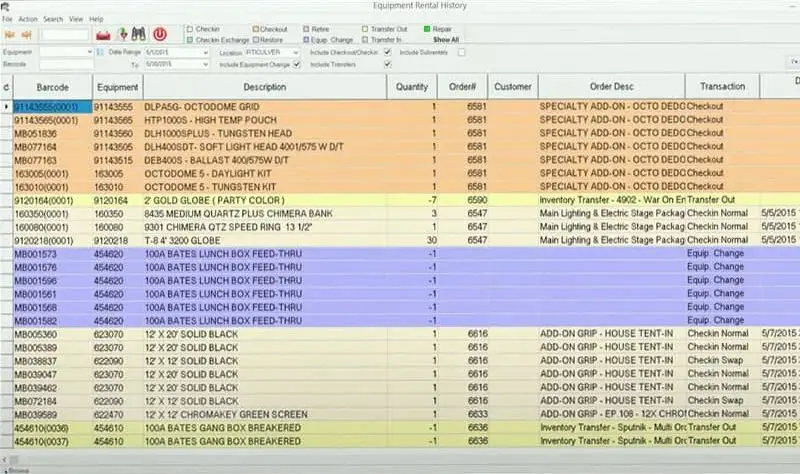
The hardware
The passive RFID tags transmit in the UHF range and can be read within 10 m distance. Tags can be cold- or heat-resistant and withstand UV light and water, depending on what customers need. They are adhered to the equipment surface and can be made to work with different kinds of materials. Cables are identified using the Sentry cable tag. There are no special requirements of readers for this application.
Tags remain attached and last the life of the asset in spite of the rough handling and harsh environmental conditions in which many of the rental assets are deployed.
Rentex entertainment equipment rental
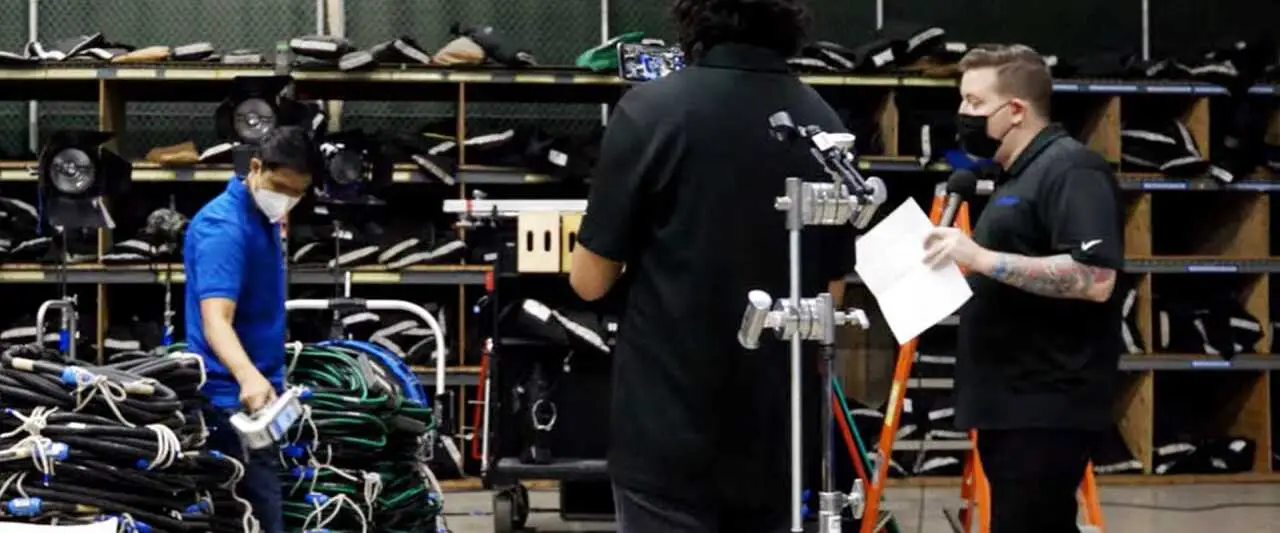
Using an RFID reader, the time required to identify rental equipment is reduced to a few seconds, equating to a time save of 99.24 percent.
Asset Tracking
Rentex is a company which rents out professional entertainment equipment. Established in 1980, they are a long-standing expert in video equipment rental. Until 2020, Rentex relied on barcode for identifying hundreds of thousands of owned items. This was quite time-consuming. Reviewing the processes in place in early 2020, it was found that efficiency and accuracy needed to improve. Since each item could take minutes to process, the hours added up fast. This drove up operating costs and slowed delivery of equipment to customers.
Asset Tracking
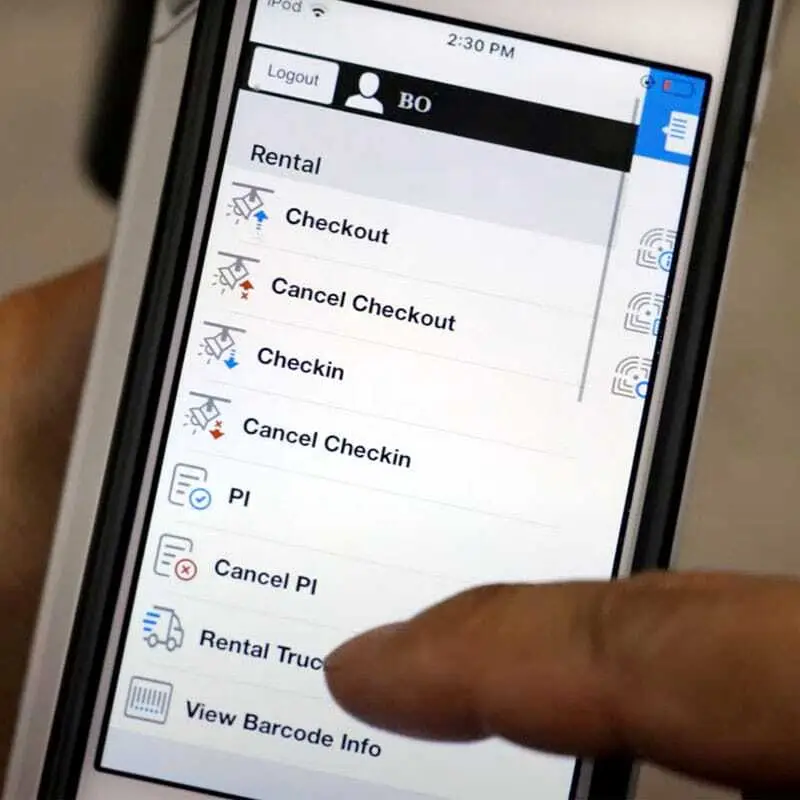
The US-American audio and video rental company Rentex tracks over 200,000 items.
Rentex is a company which rents out professional entertainment equipment. Established in 1980, they are a long-standing expert in video equipment rental. Until 2020, Rentex relied on barcode for identifying hundreds of thousands of owned items. This was quite time-consuming. Reviewing the processes in place in early 2020, it was found that efficiency and accuracy needed to improve. Since each item could take minutes to process, the hours added up fast. This drove up operating costs and slowed delivery of equipment to customers.
Rentex is a company which rents out professional entertainment equipment. Established in 1980, they are a long-standing expert in video equipment rental. Until 2020, Rentex relied on barcode for identifying hundreds of thousands of owned items. This was quite time-consuming. Reviewing the processes in place in early 2020, it was found that efficiency and accuracy needed to improve. Since each item could take minutes to process, the hours added up fast. This drove up operating costs and slowed delivery of equipment to customers.
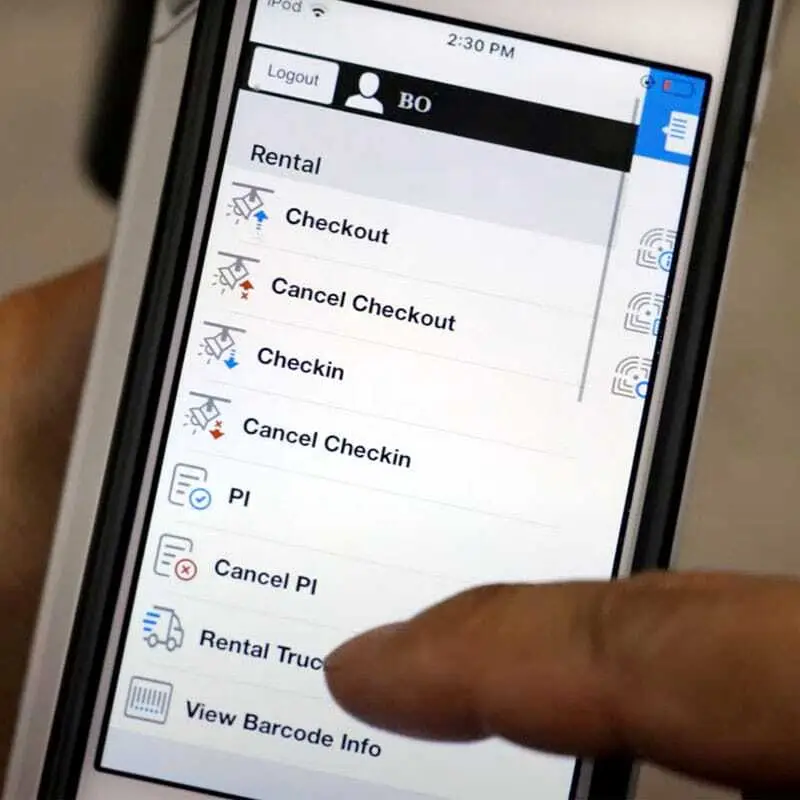
The US-American audio and video rental company Rentex tracks over 200,000 items.
Rental Tracker provides the software
Rental Tracker is a supplier of software to companies which rent equipment to the entertainment industry. They understand the needs of the industry very well, in particular the need to make every piece of equipment and every minute count. Since Rental Tracker knew the process of equipment rental so intimately, they were able to see that there were bottlenecks involving costly labor and slowing the transactions tremendously.
“They worked with us to say: OK, RFID could solve this problem. How do we develop tags that meet the needs of this industry? And so we did that.”
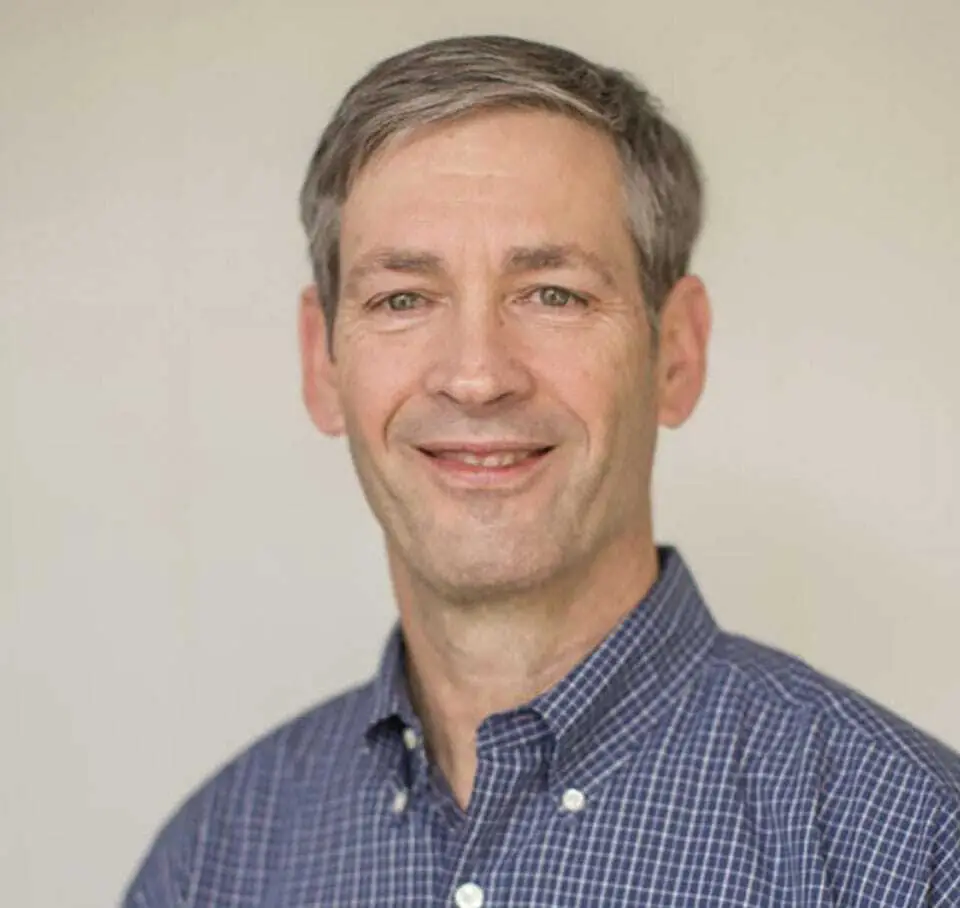
Implementing the solution
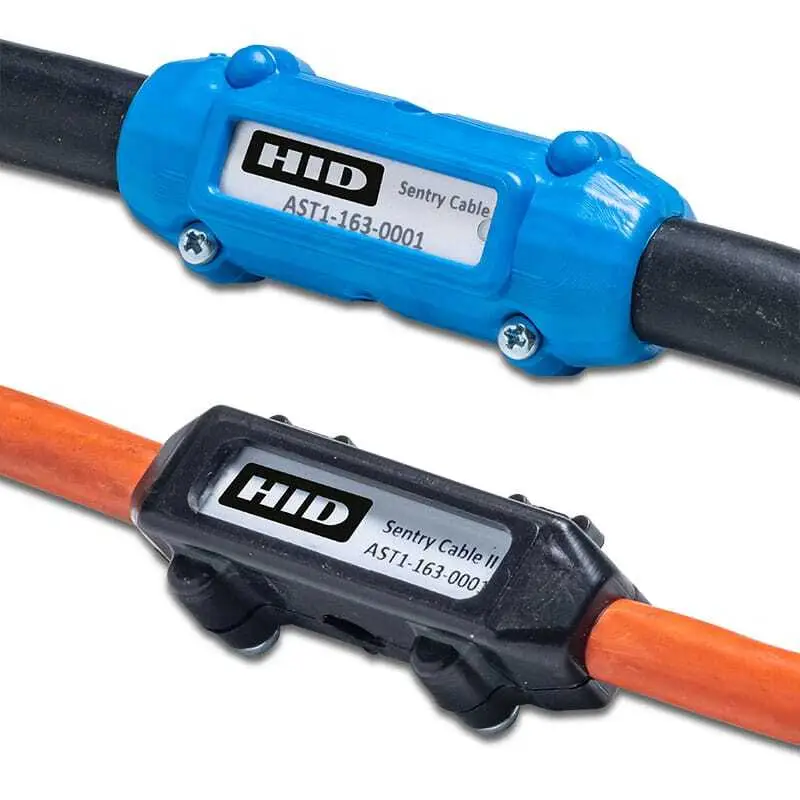
Efficiencies at Rentex improved almost immediately upon deploying RFID.
Multiple tag designs were used to deliver the best performance with the different equipment surfaces. Rentex tested the rugged tag which had been designed for the rental industry by placing it on a metal plate and hitting it with a ball peen hammer.
It withstood three crushing blows of significant force before the tag stopped transmitting. These forces were significantly higher than anything the tags would encounter during normal use which was sufficient proof of their durability. Two Sentry tags models, one for cables and a generic one, were also used. The RFID system was deployed to all 10 Rentex locations in December 2020. A total of 200,000 items were tagged.
Multiple tag designs were used to deliver the best performance with the different equipment surfaces. Rentex tested the rugged tag which had been designed for the rental industry by placing it on a metal plate and hitting it with a ball peen hammer.
It withstood three crushing blows of significant force before the tag stopped transmitting. These forces were significantly higher than anything the tags would encounter during normal use which was sufficient proof of their durability. Two Sentry tags models, one for cables and a generic one, were also used. The RFID system was deployed to all 10 Rentex locations in December 2020. A total of 200,000 items were tagged.
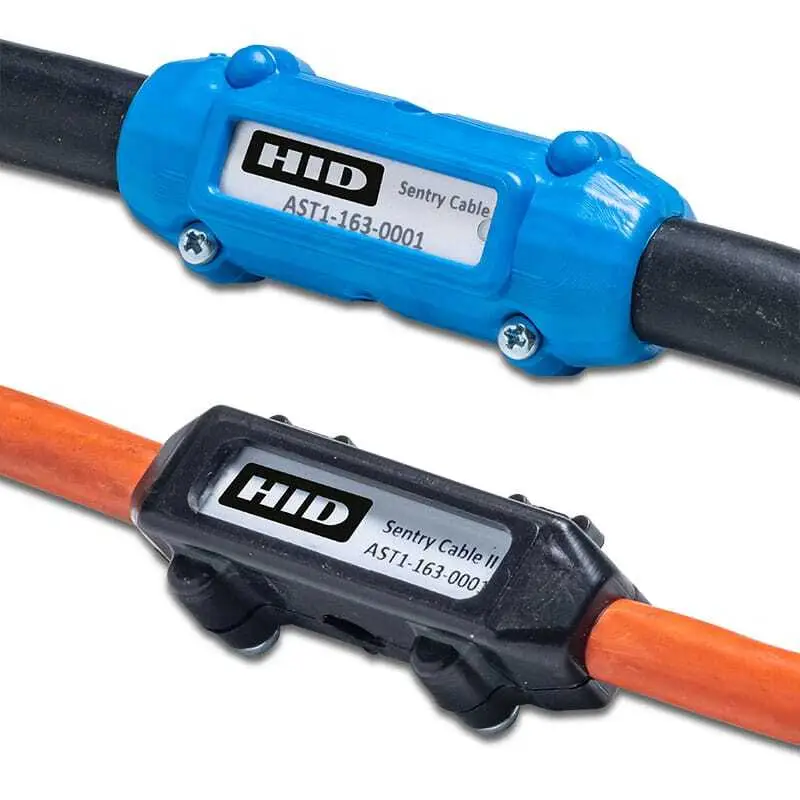
Efficiencies at Rentex improved almost immediately upon deploying RFID.
Results
Efficiencies at Rentex improved almost immediately upon deploying RFID. In one case, Rentex was able to reduce a 2.5 hour, two-person process to a 15-minute, one-person process. This equals a 95 % reduction in time and labor costs. In another case, Rentex replaced a 22-minute check-in process with one that took 10 seconds, which represents a staggering 99.24 % reduction. Fewer manual and more automated tasks characterize work at Rentex now.
Interview with Ken Horton
AV Equiment Rental is More Accurate with RFID
Ken Horton explains in an interview with RFID & Wireless IoT Global how AV equipment rental companies can improve shipment and inventory accuracy with RFID and simplify their work processes.
Interview
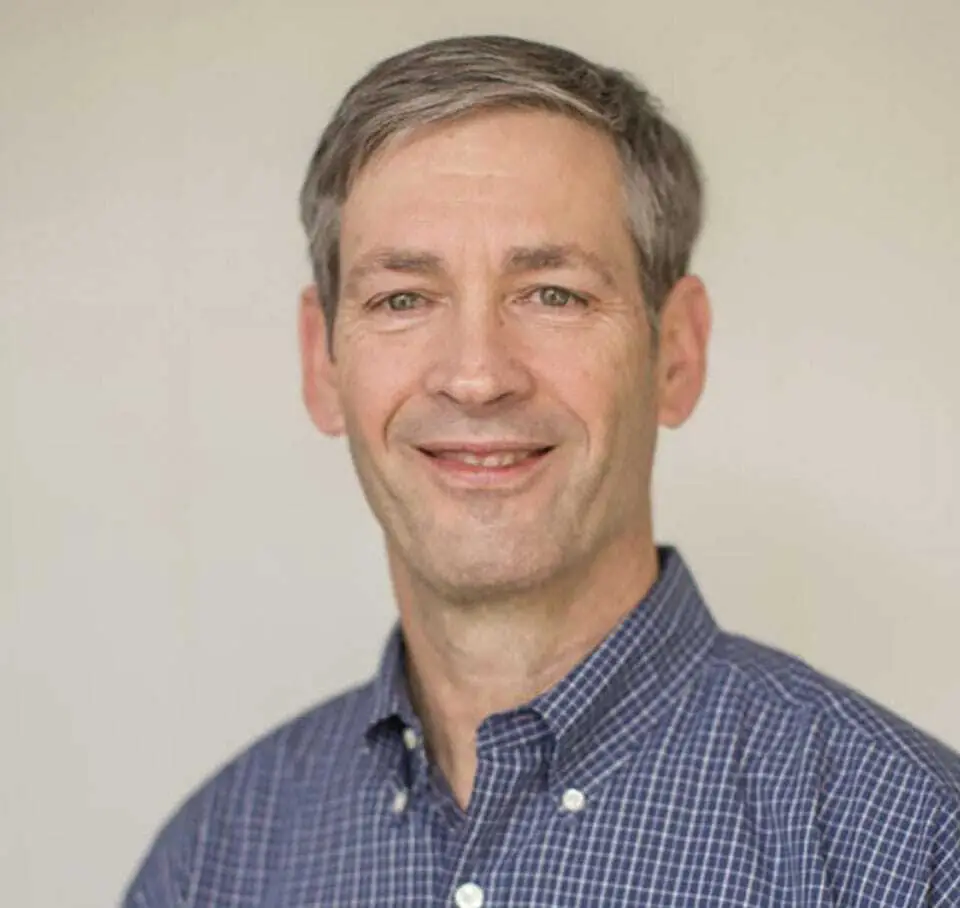
Ken Horton is the former CEO of Vizinex RFID (part of HID).
1. Mr Horton, what is the target market for the solution you provide?
The target market we're talking about right now is companies which lease equipment that is used in the creation of video content like feature length films or advertisements. The producers of these sorts of content are concerned mostly about financing, the quality of the scripts and the talent which they have hired. They don't want to own the equipment that's necessary to make a particular production because it probably won't be the same set of equipment that will be needed for their next production, or the one after that. So they count very much on video equipment leasing companies and their large inventories.
2. How does the process of ordering equipment usually transpire?
A movie company will come to one of these leasing companies and ask for a thousand items. You know, they need cables and lighting, they need all of this stuff for a particular production. And this equipment has to go on to location.
And sometimes that's just a set in a local facility, but sometimes it's the middle of the Arizona Desert because they're making a cowboy movie. What's important is that the that the leasing company has to go into their warehouse to identify exactly the right items, pull those off the shelf, they bring them to a staging area, they then verify that the order has been assembled correctly and then they get it out to the customer. It’s important to get it right the first time around.
3. Why is it so important that the order be 100 % accurate?
It’s because making a mistake can be really costly for everyone involved. If you're in the Arizona Desert filming and you find out that the cable that you've received is the right cable, but instead of being 50 feet long it’s 25 feet long, it can potentially shut down production. Then there are dozens of people standing around waiting for the right cable.
And someone is, literally, flying a helicopter from the warehouse to the set to get the crew the right cable. That’s why accuracy is key.
4. How did this very particular solution come into being?
We worked closely with Rental Tracker who supplies software to equipment rental companies. Rental Tracker understood that RFID could streamline processes and improve data timeliness and accuracy, but needed a partner with RFID experience and expertise. So, Rental Tracker approached Vizinex, now part of HID.
Rental Tracker and Vizinex worked together to develop a solution for these firms. It's all about having the right equipment on hand, utilizing it well, moving equipment as quickly as possible. Every minute that it's being used by a customer is revenue. The speed and accuracy with which these processes of getting it out of the warehouse to the customer, back in, and then back out again, are really critical.
1. Mr Horton, what is the target market for the solution you provide?
The target market we're talking about right now is companies which lease equipment that is used in the creation of video content like feature length films or advertisements. The producers of these sorts of content are concerned mostly about financing, the quality of the scripts and the talent which they have hired. They don't want to own the equipment that's necessary to make a particular production because it probably won't be the same set of equipment that will be needed for their next production, or the one after that. So they count very much on video equipment leasing companies and their large inventories.
2. How does the process of ordering equipment usually transpire?
A movie company will come to one of these leasing companies and ask for a thousand items. You know, they need cables and lighting, they need all of this stuff for a particular production. And this equipment has to go on to location.
And sometimes that's just a set in a local facility, but sometimes it's the middle of the Arizona Desert because they're making a cowboy movie. What's important is that the that the leasing company has to go into their warehouse to identify exactly the right items, pull those off the shelf, they bring them to a staging area, they then verify that the order has been assembled correctly and then they get it out to the customer. It’s important to get it right the first time around.
3. Why is it so important that the order be 100 % accurate?
It’s because making a mistake can be really costly for everyone involved. If you're in the Arizona Desert filming and you find out that the cable that you've received is the right cable, but instead of being 50 feet long it’s 25 feet long, it can potentially shut down production. Then there are dozens of people standing around waiting for the right cable.
And someone is, literally, flying a helicopter from the warehouse to the set to get the crew the right cable. That’s why accuracy is key.
4. How did this very particular solution come into being?
We worked closely with Rental Tracker who supplies software to equipment rental companies. Rental Tracker understood that RFID could streamline processes and improve data timeliness and accuracy, but needed a partner with RFID experience and expertise. So, Rental Tracker approached Vizinex, now part of HID.
Rental Tracker and Vizinex worked together to develop a solution for these firms. It's all about having the right equipment on hand, utilizing it well, moving equipment as quickly as possible. Every minute that it's being used by a customer is revenue. The speed and accuracy with which these processes of getting it out of the warehouse to the customer, back in, and then back out again, are really critical.
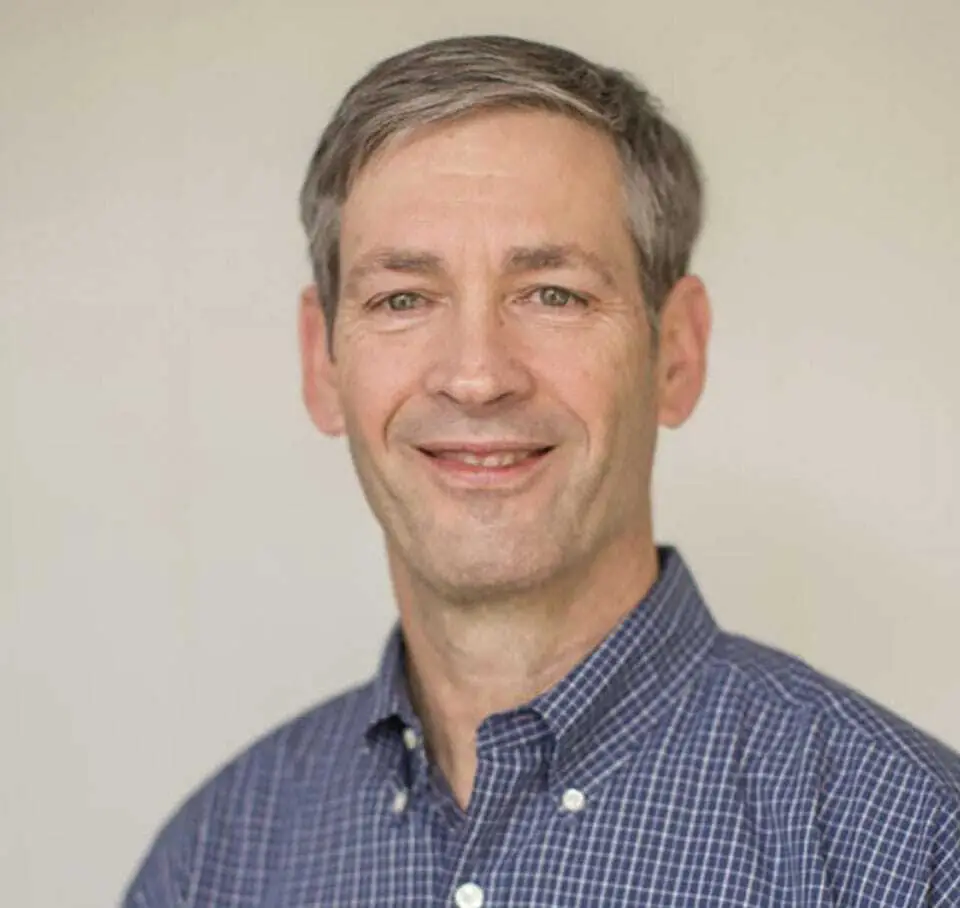
Ken Horton is the former CEO of Vizinex RFID (part of HID).