Was ist Predictive Maintenance?
Bei der vorausschauenden Instandhaltung, auch prädiktive Instandhaltung oder Predictive Maintenance (PdM) genannt, geht es darum, eine bedarfsgerechte und zustandsorientierte Instandhaltung zu ermöglichen und nicht um eine Instandhaltung, die möglicherweise erforderlich wird. Das Schlüsselwort hierfür ist "Wartungsbedarf". Herkömmliche Instandhaltungsmaßnahmen umfassen feste Wartungspläne und reaktive Maßnahmen bei Anlagenausfällen. Dies führt oft zu unnötigen Ausfallzeiten und hohen Kosten. Predictive Maintenance und Facility Management sind Begriffe, die oft im Zusammenhang verwendet werden.
PdM nutzt historische und Echtzeitdaten, um mit Hilfe von KI, maschinellem Lernen, Datenanalyse und Überwachungstechnologien den optimalen Zeitpunkt für Wartungsarbeiten vorherzusagen und ungeplante Maschinenausfälle zu minimieren. Die Wartungsmaßnahmen werden an die Anforderungen der individuell überwachten Anlagen angepasst.
Der englische Begriff „Preventive Predictive Maintenance“ (PPM) ist eine Kombination aus zwei Instandhaltungsansätzen: Preventive Maintenance und Predictive Maintenance. PPM nutzt Echtzeitdaten und vorausschauende Analysen, um den Zeitplan für vorbeugende Instandhaltungsmaßnahmen zu informieren und zu optimieren. Das bedeutet, dass Wartungsaktivitäten nicht nur auf festen Zeitplänen basieren, sondern dynamisch an den tatsächlichen Zustand und die Leistung der Anlagen angepasst werden.
Wie funktioniert Predictive Maintenance?
IoT-Sensoren erfassen relevante Zustandsdaten wie Vibration, Temperatur oder Stromverbrauch. MQTT (Message Queuing Telemetry Transport) ist ein leichtgewichtiges, publish-subscribe-basiertes Messaging-Protokoll, das häufig im Kontext des Internet der Dinge (IoT) eingesetzt wird. IoT-Sensoren fungieren als MQTT-Clients und veröffentlichen ihre Messdaten regelmäßig an bestimmte Topics auf dem MQTT-Broker.
Alle von den IoT-Sensoren erfassten Daten werden an Cloud- oder Edge-Computing-Plattformen übertragen. Dort werden die Daten gespeichert und analysiert. Cloud-Computing-Plattformen bieten Skalierbarkeit und Zugänglichkeit. Edge-Computing-Plattformen ermöglichen die Datenverarbeitung näher an der Quelle und in Echtzeit.
Prädiktive Algorithmen und Datenanalysen werden dann eingesetzt, um Muster zu erkennen, die auf bevorstehende Ausfälle hinweisen.
5G Predictive Maintenance umfasst die Nutzung eines 5G-Netzes, um eine zuverlässige Hochvolumen-Datenübertragung zu ermöglichen.
Mithilfe von Algorithmen für maschinelles Lernen (ML) und Künstliche Intelligenz (KI) sowie statistischen Modellen wird daraufhin ein optimales Wartungsintervall geplant. Die Infrastruktur für Predictive-Maintenance-Lösungen umfasst: Datenerfassung und -speicherung, Datenverarbeitung, Condition Monitoring, Prognose und Asset Health Evaluation.
Auf der Grundlage der von IoT-Sensoren erfassten Daten können auch digitale Zwillinge der physischen Anlagen erstellt werden. So können Unternehmen reale Szenarien simulieren, um Prozesse durch bessere Entscheidungen zu optimieren.
Durch die Integration von vorausschauender Wartung in das Industry 4.0-Framework können Unternehmen eine hocheffiziente, flexible und zuverlässige Produktionsumgebung schaffen.
Wireless IoT Technologien und Predictive Maintenance
Produkte für Predictive Maintenance
Es gibt zwei Hauptkomponenten für ein IoT-Predictive-Maintenance System.
Die erste ist die Hardware. Dazu gehören IoT-Geräte wie Sensoren, intelligente Messgeräte, IoT-Gateways, Aktoren und speicherprogrammierbare Steuerungen (SPS), die Daten sammeln. Diese Geräte werden an Maschinen und in der gesamten Produktionslinie installiert. Sensoren sind die Kernkomponente der vorausschauenden Wartung.
Es gibt verschiedene Arten von Sensoren, die unterschiedliche Parameter wie Vibration, Temperatur, Druck und Lärm erfassen. Datenerfassungssysteme sorgen dafür, dass alle erfassten Daten übertragen und für die Analyse aufbereitet werden. Von dort aus werden die von den Datenerfassungssystemen aufbereiteten Daten über Verbindungsgeräte an einen zentralen Cloud-Speicher oder eine Analysesoftware weitergeleitet. Die Übertragung kann über kabelgebundene Netzwerke, Mobilfunknetze wie 5G oder Wi-Fi erfolgen. OPC UA kann verwendet werden, um eine interoperable Kommunikation zwischen verschiedenen Sensoren und Geräten unterschiedlicher Hersteller zu gewährleisten.
Die zweite Komponente ist die Datenanalysesoftware zur Verarbeitung und Analyse der erfassten Daten. Dazu gehören beispielsweise KI und Algorithmen für maschinelles Lernen. KI in Unternehmen ermöglicht die Vorhersage von Anlagenausfallzeiten auf Basis der analysierten Daten. Sie verwandelt also Rohdaten in verwertbares Wissen. Enterprise Resource Planning (ERP)-Systeme und computergestützte Wartungsmanagementsysteme (CMMS) können ebenfalls mit Datenanalysesoftware integriert werden.
Neben der Software für das Instandhaltungsmanagement kommen dann auch Softwarekomponenten wie Predictive Modelling zum Einsatz. Diese Software fungiert als operative Drehscheibe für das Management der Instandhaltungsaktivitäten.
Zahlen & Fakten
Wartungsarbeiten sind teuer. Nach einer Studie der Universität Newcastle entfallen 15 bis 40 Prozent der Produktionskosten auf die Instandhaltung. Vorausschauende Wartung kann helfen, diese Kosten zu senken. Laut einem Bericht von "Deloitte Insights", einem Unternehmen, das eigene Untersuchungen und eingehende Analysen durchführt, können Unternehmen, die vorausschauende Wartungslösungen einsetzen, ihre gesamten Wartungskosten um 5 bis 10 Prozent senken. Auch der Zeitaufwand für die Planung von Wartungsarbeiten kann um 20–50 Prozent reduziert werden. Die Anlagenverfügbarkeit und die Betriebszeit können ebenfalls um 10–20 Prozent gesteigert werden.
Zusätzlich zu diesen Vorteilen kann Predictive Maintenance die Ausfallzeiten von Maschinen und Anlagen um 35 bis 50 Prozent reduzieren und die Lebensdauer von Maschinen und Anlagen um 20 bis 40 Prozent verlängern, so ein Bericht von Nucleus Research, einem Anbieter von ROI-orientierter Technologieforschung.
Erfolgreiche Beispiele für Predictive Maintenance
Vorausschauende Instandhaltungsstrategien werden in vielen Branchen eingesetzt. Dazu gehören: Fertigung und Produktion, Energiewirtschaft, Transport, Logistik, Öl- und Gasindustrie, Bergbau, Luft- und Raumfahrt, Bauindustrie sowie Chemie- und Pharmaindustrie. Unternehmen, die diese Strategien anwenden, sparen Kosten, reduzieren Stillstandszeiten von Maschinen und Anlagen und erhöhen die Sicherheit im Umgang mit Maschinen. Die betrieblichen Abläufe entlang der Supply Chain werden optimiert. Die folgenden Praxisbeispiele aus Industrie und Energiewirtschaft zeigen, wie drahtlose IoT-Technologien für die vorausschauende Wartung eingesetzt werden.
Predictive Maintenance bei Rosendahl Nextrom
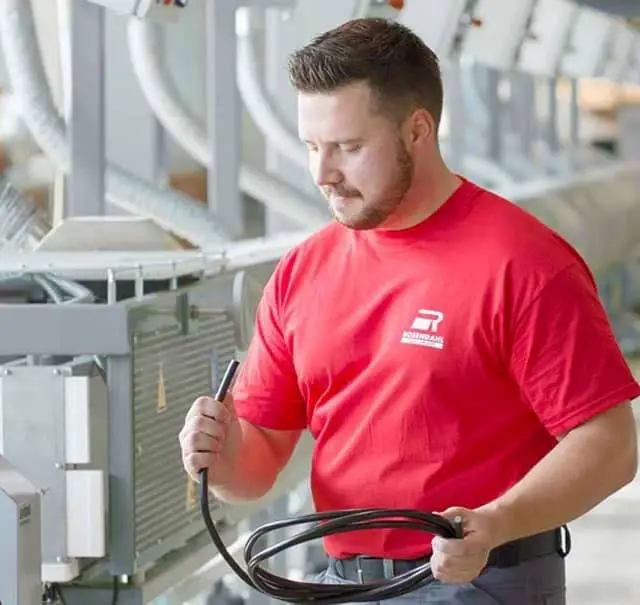
Rosendahl Nextrom, ein Hersteller von Kabeln, Lichtwellenleitern und Batterien, setzt den Kommunikationsstandard OPC UA der OPC Foundation für die vorausschauende Wartung seiner Anlagen ein. Im Anlagenteil Extruder werden beispielsweise Zug-, Temperatur- und Objektdaten, die bei der Zustandsüberwachung erfasst werden, über OPC UA übertragen. Durch die Analyse von Erfahrungswerten und historischen Daten wird eine vorausschauende Wartung möglich.
Das Ergebnis: eine optimierte Lebensdauer der installierten Schnecken.
Rosendahl Nextrom, ein Hersteller von Kabeln, Lichtwellenleitern und Batterien, setzt den Kommunikationsstandard OPC UA der OPC Foundation für die vorausschauende Wartung seiner Anlagen ein. Im Anlagenteil Extruder werden beispielsweise Zug-, Temperatur- und Objektdaten, die bei der Zustandsüberwachung erfasst werden, über OPC UA übertragen. Durch die Analyse von Erfahrungswerten und historischen Daten wird eine vorausschauende Wartung möglich.
Das Ergebnis: eine optimierte Lebensdauer der installierten Schnecken.
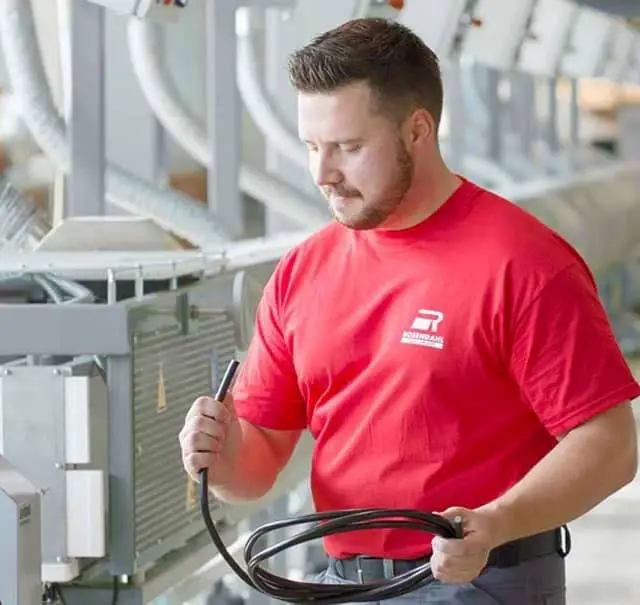
„Der größte Vorteil liegt natürlich in der leichteren Anbindung von Maschinen in bestehende Systeme. Durch den Wegfall von Hardware- Adaptern werden wir unabhängiger und flexibler. Umgekehrt ermöglicht der Standard auch die Verfügbarkeit von neuen Prozesswerten und den umfassenden Datenzugriff in real-time.“
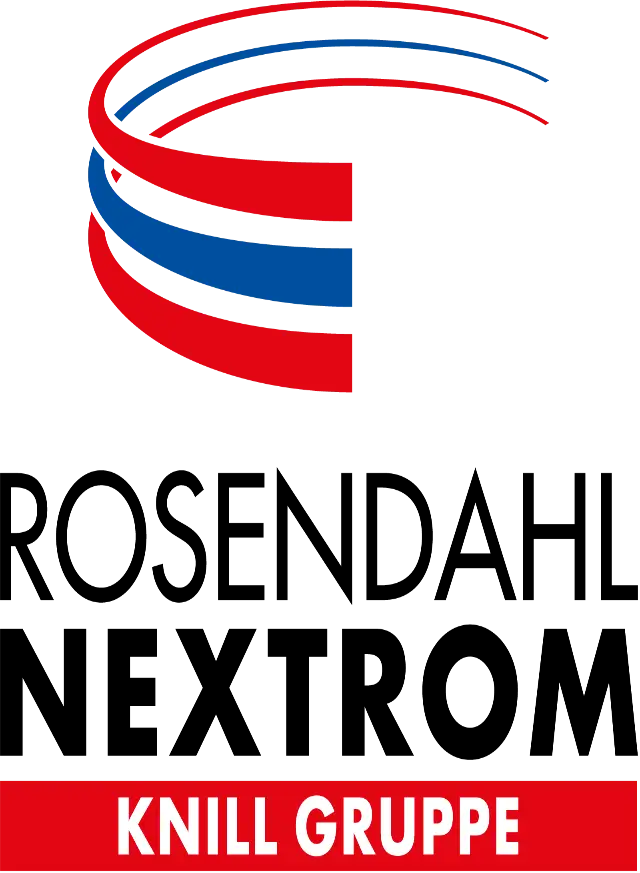
Benedikt Wagner
Head of Commissioning and Programming
Predictive Maintenance bei Scatec
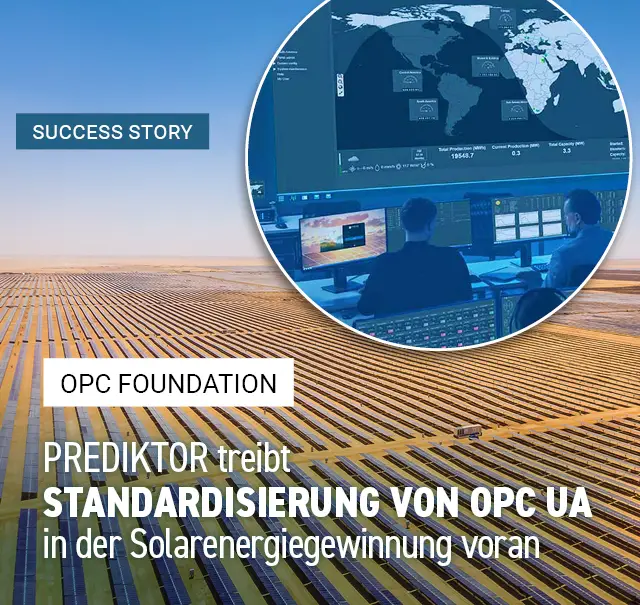
Der Solarstromanbieter Scatec nutzt "PowerView" für das Datenmanagement. PowerView ist eine datengesteuerte Lösung, die auf dem OPC UA Standard der OPC Foundation basiert. Die Wartung von mehr als 500.000 Solarmodulen erfolgt durch Reinigung, um Verluste und Leistungsprobleme durch Verschmutzung zu vermeiden. PowerView generiert Vorschläge für optimale Reinigungs- und Wartungszeiten auf Basis von Geräte- und Anlagendaten sowie Kontextdaten wie Wettervorhersagen.
Das Ergebnis: reduzierte Wartungskosten und verbesserte Ressourcenplanung.
Der Solarstromanbieter Scatec nutzt "PowerView" für das Datenmanagement. PowerView ist eine datengesteuerte Lösung, die auf dem OPC UA Standard der OPC Foundation basiert. Die Wartung von mehr als 500.000 Solarmodulen erfolgt durch Reinigung, um Verluste und Leistungsprobleme durch Verschmutzung zu vermeiden. PowerView generiert Vorschläge für optimale Reinigungs- und Wartungszeiten auf Basis von Geräte- und Anlagendaten sowie Kontextdaten wie Wettervorhersagen.
Das Ergebnis: reduzierte Wartungskosten und verbesserte Ressourcenplanung.
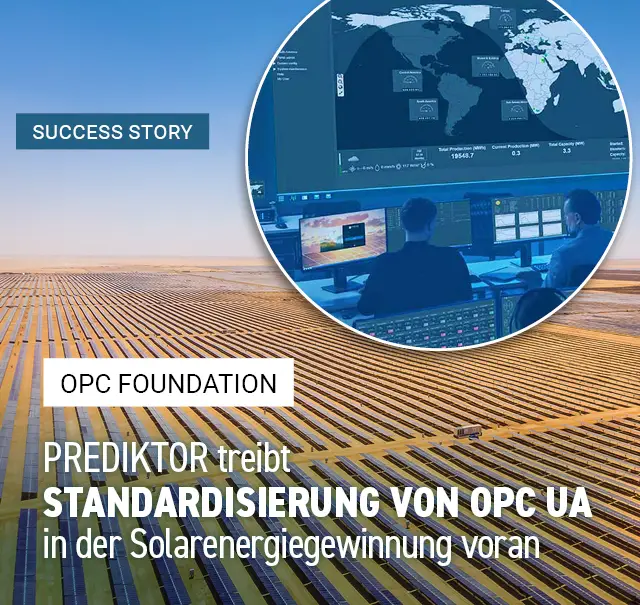
„Ohne ein solches System entsteht die Problematik, dass die Sammlung von immer mehr Daten nicht unbedingt einen Mehrwert erzielt. Der Betreiber wird mit Daten überflutet. Es können beispielsweise hunderte Alarme angezeigt werden, ohne dass eine angemessene Reaktion möglich ist. Es braucht ein System, welches in die Datenströme eintauchen kann und herausfindet, was die Alarme verursacht und hochwertige Empfehlungen ausspricht, wie die Probleme zu beheben sind.“
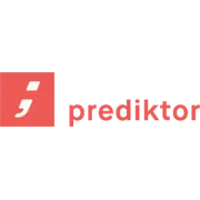
Thomas Pettersen
Vice President Operations Management
Vorausschauende Wartung bei Groupe Renault
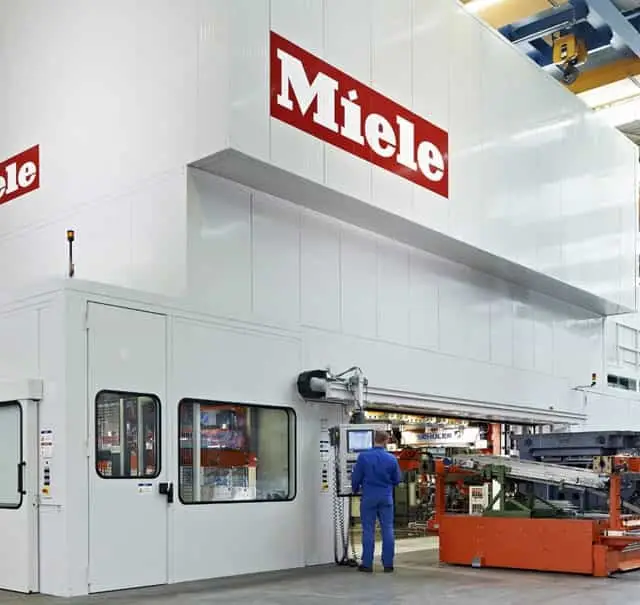
Groupe Renault nutzt den Kommunikationsstandard OPC UA der OPC Foundation für das automatisierte Schweißen von Bauteilen. Durch den Einsatz von Adaptern werden Komponenten wie Schweißprozesse, Roboter, CNC und PLC OPC-UA-fähig. Die 2.200 angeschlossenen Roboter im Karosseriebau überwachen die Schweißprozesse, erkennen Anomalien in Echtzeit und führen auf Basis der gesammelten Daten eine vorausschauende Wartung der Komponenten durch.
Das Ergebnis: Die Fehlerquote im Schweißprozess sank um 20 Prozent.
Groupe Renault nutzt den Kommunikationsstandard OPC UA der OPC Foundation für das automatisierte Schweißen von Bauteilen. Durch den Einsatz von Adaptern werden Komponenten wie Schweißprozesse, Roboter, CNC und PLC OPC-UA-fähig. Die 2.200 angeschlossenen Roboter im Karosseriebau überwachen die Schweißprozesse, erkennen Anomalien in Echtzeit und führen auf Basis der gesammelten Daten eine vorausschauende Wartung der Komponenten durch.
Das Ergebnis: Die Fehlerquote im Schweißprozess sank um 20 Prozent.
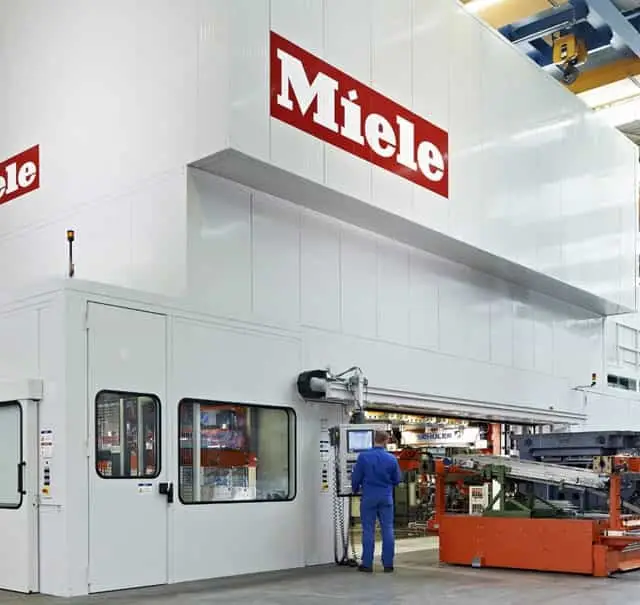
Weitere Stories zum Thema Predictive Maintenance
Die Zukunft der vorausschauenden Wartung
Die Zukunft der Predictive Maintenance wird von einer Kombination aus technologischem Fortschritt und strategischen Ansätzen geprägt sein. Ziel ist es, die Effizienz, Zuverlässigkeit und Nachhaltigkeit von Instandhaltungsprozessen weiter zu verbessern. Die vorausschauende Instandhaltung wird ein integraler Bestandteil der Initiativen Industrie 4.0 und Manufacturing X sein. Sie wird sich nahtlos in intelligente Fabriken einfügen, in denen vernetzte Systeme und fortgeschrittene Automatisierung für optimale Leistung und minimale Ausfallzeiten sorgen.
Die Entwicklung von Algorithmen der künstlichen Intelligenz und des maschinellen Lernens wird genauere Vorhersagen von Maschinenausfällen ermöglichen. Predictive Analytics nutzt diese Algorithmen zur Analyse großer Datenmengen, um Muster und Trends im Maschinenzustand zu erkennen.
Cloud Computing wird eine zentrale Datenablage ermöglichen, in der große Mengen an Wartungsdaten gespeichert und weltweit abgerufen werden können. Dies wird die Zusammenarbeit und den Datenaustausch zwischen verschiedenen Standorten und Abteilungen erleichtern und die Instandhaltungsstrategien insgesamt verbessern. Mit der Zunahme des gesammelten Datenvolumens werden Big-Data-Analysen erforderlich, um die von IoT-Geräten gesammelten großen Datenmengen zu verarbeiten und zu analysieren.
Auch die vorausschauende Wartung wird zunehmend virtuell. Proaktive Wartungsstrategien werden zunehmend durch den Einsatz digitaler Zwillinge ermöglicht. Der Zustand physischer Anlagen kann virtuell und in Echtzeit überwacht werden. AR-basierte Lösungen für die vorausschauende Wartung werden immer häufiger eingesetzt. Ziel ist es, Szenarien in der Praxis zu simulieren, in denen das Wartungspersonal seine Fähigkeiten gefahrlos trainieren kann.
Virtual-Reality-Technologien werden in der vorausschauenden Wartung eingesetzt, um entweder die Anlage selbst oder bestimmte Teile, Komponenten oder Produkte virtuell darzustellen. Dabei kann es sich um bereits vorhandene Objekte handeln oder um Objekte, die noch nicht existieren, aber geplant sind.
Ein aufkommender Trend in der Anlageninspektion ist Extended Reality (XR). Dabei geht es um die Integration von Augmented und Virtual Reality Tools in Instandhaltungsprozesse. Fernwartung, immersives Training und virtuelle Simulationen im Bereich Predictive Maintenance werden durch XR-Technologien wie AR und VR ermöglicht.
Ein weiteres Schlagwort für die Zukunft der vorausschauenden Wartung ist "Echtzeit". Um Predictive Maintenance in Echtzeit zu ermöglichen, wird eine Kombination aus Edge Computing und Predictive Analytics eingesetzt. Dabei werden künstliche Intelligenz und Business Intelligence (BI) zur Analyse des Anlagenzustands kombiniert. Immer mehr Unternehmen erkennen das Potenzial von Edge-Computing-Lösungen für die vorausschauende Wartung: Sensordaten können in Echtzeit analysiert werden, um die Entscheidungsfindung für Wartungsmaßnahmen zu erleichtern und zu beschleunigen.
Zur Zukunft der vorausschauenden Wartung gehört auch die Zusammenarbeit von Mensch und Maschine (Mensch-Roboter-Kollaboration / MRK). Moderne Schnittstellen und KI-gestütztes Wissen werden Technikern helfen, fundierte Entscheidungen zu treffen, während Maschinen Routinediagnosen und Wartungsaufgaben übernehmen. Kollaborative Roboter oder Cobots werden mit menschlichen Technikern zusammenarbeiten, um komplexe Wartungsaufgaben zu unterstützen und Präzision zu gewährleisten. Diese Roboter werden mit KI- und IoT-Funktionen ausgestattet sein, um Diagnosen und Reparaturen in Echtzeit durchführen zu können.
Vorteile der IoT-basierten vorausschauenden Wartung
Vorteile von Wireless IoT
- Echtzeitüberwachung
- Kostenreduktion
- Vermeidung von Produktionsausfällen
- Längere Lebensdauer der Maschinen
- Datenbasierte Entscheidungen
Wissenschaftliche Untersuchungen haben gezeigt, dass es für Unternehmen von entscheidender Bedeutung ist, der Zuverlässigkeit von Maschinen Priorität einzuräumen. Vorausschauende Wartungslösungen spielen hier eine entscheidende Rolle, insbesondere in Verbindung mit IoT-Technologien. Es gibt fünf Hauptvorteile der Implementierung von IoT Predictive Maintenance:
- Durch das frühzeitige Erkennen möglicher Probleme können Produktionsausfälle und damit verbundene Verluste vermieden werden. Da Wartungsarbeiten nur dann durchgeführt werden, wenn sie tatsächlich erforderlich sind, wird die Maschinenverfügbarkeit maximiert.
- Durch die Vermeidung ungeplanter Ausfälle und die Minimierung unnötiger Wartungsarbeiten werden die Wartungskosten deutlich reduziert.
- IoT-basierte vorausschauende Wartung ermöglicht eine bessere Planung und Koordination von Wartungsarbeiten, was zu einem effizienteren Einsatz von Ressourcen und Personal führt.
- Durch die kontinuierliche Überwachung des Maschinenzustands können potenzielle Sicherheitsrisiken frühzeitig erkannt und behoben werden, was die Sicherheit am Arbeitsplatz erhöht. Dies bedeutet, dass das Risiko von Ausfällen, die zu Unfällen führen, reduziert wird, was wiederum die Arbeitssicherheit für das Instandhaltungspersonal erhöht.
- Optimal gewartete Maschinen arbeiten präziser und zuverlässiger, was die Qualität der produzierten Waren verbessert. Richtige Wartungspläne verlängern die Lebensdauer von Maschinen und Anlagen.
Wissenschaftliche Untersuchungen haben gezeigt, dass es für Unternehmen von entscheidender Bedeutung ist, der Zuverlässigkeit von Maschinen Priorität einzuräumen. Vorausschauende Wartungslösungen spielen hier eine entscheidende Rolle, insbesondere in Verbindung mit IoT-Technologien. Es gibt fünf Hauptvorteile der Implementierung von IoT Predictive Maintenance:
- Durch das frühzeitige Erkennen möglicher Probleme können Produktionsausfälle und damit verbundene Verluste vermieden werden. Da Wartungsarbeiten nur dann durchgeführt werden, wenn sie tatsächlich erforderlich sind, wird die Maschinenverfügbarkeit maximiert.
- Durch die Vermeidung ungeplanter Ausfälle und die Minimierung unnötiger Wartungsarbeiten werden die Wartungskosten deutlich reduziert.
- IoT-basierte vorausschauende Wartung ermöglicht eine bessere Planung und Koordination von Wartungsarbeiten, was zu einem effizienteren Einsatz von Ressourcen und Personal führt.
- Durch die kontinuierliche Überwachung des Maschinenzustands können potenzielle Sicherheitsrisiken frühzeitig erkannt und behoben werden, was die Sicherheit am Arbeitsplatz erhöht. Dies bedeutet, dass das Risiko von Ausfällen, die zu Unfällen führen, reduziert wird, was wiederum die Arbeitssicherheit für das Instandhaltungspersonal erhöht.
- Optimal gewartete Maschinen arbeiten präziser und zuverlässiger, was die Qualität der produzierten Waren verbessert. Richtige Wartungspläne verlängern die Lebensdauer von Maschinen und Anlagen.
Vorteile von Wireless IoT
- Echtzeitüberwachung
- Kostenreduktion
- Vermeidung von Produktionsausfällen
- Längere Lebensdauer der Maschinen
- Datenbasierte Entscheidungen
Herausforderungen bei IoT-basierter Predictive Maintenance
Die Implementierung von IoT-basierten Predictive Maintenance-Systemen kann erhebliche Vorteile bieten, ist aber auch mit zahlreichen Herausforderungen verbunden. Sorgfältige Planung, geeignete Sicherheitsmaßnahmen, kontinuierliche Überwachung und Anpassung sowie die Schulung von Fachkräften sind für den Erfolg solcher Projekte entscheidend.
Es gibt drei Hauptherausforderungen bei der Implementierung eines IoT-basierten Predictive Maintenance Systems.
1. Technische Herausforderungen
Unterschiedliche Maschinen und Geräte verwenden oft verschiedene Protokolle und Standards, was die Integration und Interoperabilität der Systeme erschwert. Um dieses Problem zu lösen, müssen Unternehmen interoperable Kommunikationsstandards wie OPC UA verwenden.
IoT-Sensoren erzeugen enorme Datenmengen, die verarbeitet und analysiert werden müssen. Eine hohe Datenqualität und eine genaue Datenerfassung sind entscheidend, um zuverlässige Vorhersagen treffen zu können. Auch die Verwaltung und Verarbeitung dieser großen Datenmengen stellt eine Herausforderung dar. Dafür sind ausreichend Bandbreite, Speicher- und Rechenressourcen erforderlich. Unternehmen müssen daher in eine Infrastruktur für das Datenmanagement investieren. Die Systeme müssen zudem skalierbar sein, um mit den wachsenden Datenmengen und der Anzahl vernetzter Geräte Schritt halten zu können.
2. Organisatorische Herausforderungen
Die Implementierung von IoT-basierten PdM-Systemen kann erhebliche Anfangsinvestitionen in Hardware, Software und Infrastruktur erfordern. Es besteht auch ein Bedarf an qualifizierten Fachkräften, die sowohl über technisches Wissen im Bereich IoT und Datenanalyse als auch über Fachwissen im Bereich Instandhaltung verfügen. PdM-Systeme müssen nahtlos in bestehende IT- und Instandhaltungssysteme integriert werden, was komplex und zeitaufwändig sein kann.
Die Einführung neuer Technologien in der Instandhaltung kann auch für das Personal eine Herausforderung darstellen. Gründe dafür sind vor allem mangelndes Vertrauen und Verständnis für die neuen Technologien. Aus diesem Grund ist eine angemessene Schulung und Unterstützung entscheidend für die erfolgreiche Einführung von IoT-basierten vorausschauenden Wartungslösungen.
3. Herausforderungen für Sicherheit und Datenschutz
IoT-Geräte und -Netzwerke sind anfällig für Cyber-Angriffe. Es ist wichtig, robuste Sicherheitsmaßnahmen zu implementieren, um Daten und Systeme zu schützen. Cybersicherheitslösungen umfassen regelmäßige Sicherheitsprüfungen, Intrusion-Detection-Systeme und Netzwerksegmentierung. Die Erfassung und Verarbeitung großer Mengen von Betriebsdaten wirft auch Datenschutzfragen auf. Es muss sichergestellt werden, dass alle gesetzlichen Anforderungen und Datenschutzrichtlinien eingehalten werden.
Partner im Bereich Predictive Maintenance
Ausblick – Next-Level Predictive Maintenance
Zu den sich abzeichnenden Trends im Bereich der vorausschauenden Instandhaltung gehören die schnellere und kostengünstigere Einführung durch Predictive Maintenance-as-a-Service (PdMaaS), die Verbesserung der Arbeitssicherheit durch robotergestützte Inspektionen und der Einsatz immersiver Technologien wie Extended Reality.
Predictive Maintenance-as-a-Service
Predictive Maintenance-as-a-Service (PdMaaS) ist eine Kombination aus Software und einem Serviceteam, um die vorausschauende Wartung für Fertigungsunternehmen und -anlagen verfügbarer, zugänglicher und erschwinglicher zu machen. Der Implementierungsprozess wird nur geringfügig gestört, da von den Mitarbeitern in der Fabrik oder Anlage nur wenige Eingaben erforderlich sind. Eine Schulung ist nicht notwendig. PdM as a Service kann auch an die spezifischen Anforderungen von Anlagen und Werken angepasst werden.
Inspektion mit autonomen Robotern
In gefährlichen Umgebungen, wie z. B. in der Öl- und Gasindustrie, setzen Unternehmen zunehmend automatisierte Roboterinspektionen zur Überwachung von Anlagen ein. Autonome Roboter und Drohnen werden als mobile Sensorplattformen eingesetzt. Diese werden zur Überwachung von Anlagen eingesetzt. Die Daten werden anschließend in computergestützte Wartungsmanagementsysteme (CMMS) übertragen.
Immersive Technologien
Vorausschauende Wartungslösungen, die Augmented, Virtual und Extended Reality (AR, VR und XR) nutzen, werden weiterentwickelt, um die Fernüberwachung zu ermöglichen, die Wartungsvisualisierung zu verbessern und die Fernunterstützung und -schulung des Wartungspersonals zu verbessern.