Interview mit Ramin Hassan
1. Warum wurde die CNC-Fräsmaschine angeschafft, und für welche spezifischen Prozesse wird sie eingesetzt? Hatte die Corona-Pandemie oder Engpässe in der Leiterplattenproduktion einen Einfluss auf diese Entscheidung?
Ramin Hassan: Die Entscheidung zur Anschaffung der CNC-Fräsmaschine war primär durch die Notwendigkeit motiviert, unsere Elektronikfertigung weiter auszubauen und flexibler zu gestalten. Wir wollten die Produktion sowohl für Gehäuseteile, als auch für Elektronikkomponenten wie Leiterplatten und Antennen optimieren.
Insbesondere in der Corona-Pandemie, als die globalen Lieferketten stark gestört waren, stießen wir auf entsprechende Engpässe. Um unsere Reader und Antennen trotzdem weiterhin zeitnah liefern zu können, entschieden wir uns dazu, eine Anlage anzuschaffen, die beide Bereiche abdecken kann.
2. Welche Vorteile bietet diese Anlage?
Ramin Hassan: Die CNC-Fräsmaschine ermöglicht es uns, sowohl größere Bauteile wie Gehäuse als auch elektronische Bauteile wie zum Beispiel Antennen effizient zu produzieren. Ein weiterer wichtiger Aspekt war die Umweltfreundlichkeit der Technologie. Im Gegensatz zum Ätzen fallen beim Fräsen keine umweltschädlichen Chemikalien an, und der entstehende Abfall besteht aus recyclingfähigen Reinstoffen.
Egal, ob wir Leiterplatten oder Metallteile herstellen, im Großen und Ganzen entstehen immer Metallspäne, die abgesaugt werden und recyclingfähig sind.
3. Welche Funktionen bietet diese Maschine, und wie viel Produktionskapazität können Sie pro Woche mit ihr erreichen?
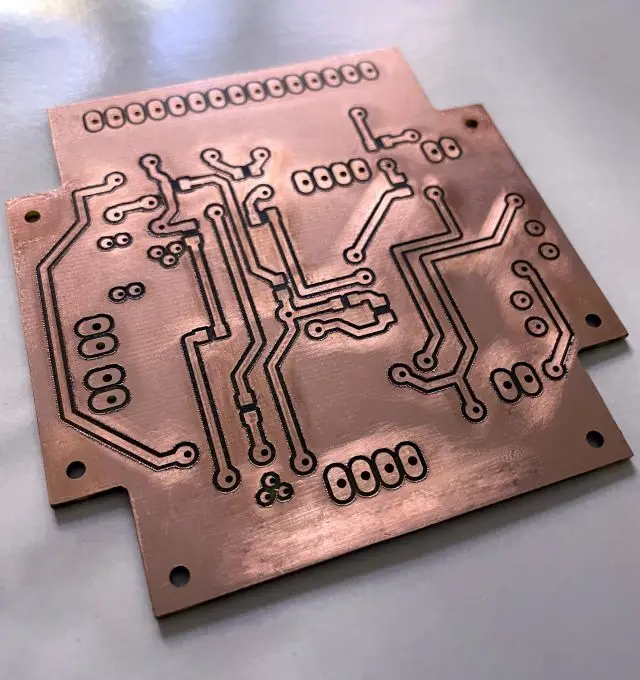
Leiterplatte für Prüfhardware (Bild: GERA-Ident)
Ramin Hassan: Die CNC-Fräsmaschine bietet eine Vielzahl von Funktionen. Durch die sehr große Anzahl verfügbarer Messer und Werkzeuge sind wir in der Lage verschiedenste Materialien damit zu schneiden oder zu fräsen, einschließlich Kunststoffe wie ABS oder PA, aber auch FR4, Holz, Aluminium und Stahl.
Durch das eingebaute Kamerasystem zur automatischen Passmarkererkennung, ist ein präzises Arbeiten auch ohne genaue Positionierung des Materials möglich.
Die Produktionskapazität variiert je nach Produkt und Komplexität des Herstellungsprozesses. Manche Teile erfordern mehr Zeit im Herstellungsverfahren als andere, weshalb die Stückzahl nicht immer der beste Gradmesser für die Kapazität ist.
Ursprünglich wurde die Maschine für Rapid Prototyping angeschafft, um im Bereich der Prototypenentwicklung schneller agieren zu können. Heute nutzen wir sie jedoch auch für kleinere und mittlere Produktionsvolumina.
Ramin Hassan: Die CNC-Fräsmaschine bietet eine Vielzahl von Funktionen. Durch die sehr große Anzahl verfügbarer Messer und Werkzeuge sind wir in der Lage verschiedenste Materialien damit zu schneiden oder zu fräsen, einschließlich Kunststoffe wie ABS oder PA, aber auch FR4, Holz, Aluminium und Stahl.
Durch das eingebaute Kamerasystem zur automatischen Passmarkererkennung, ist ein präzises Arbeiten auch ohne genaue Positionierung des Materials möglich.
Die Produktionskapazität variiert je nach Produkt und Komplexität des Herstellungsprozesses. Manche Teile erfordern mehr Zeit im Herstellungsverfahren als andere, weshalb die Stückzahl nicht immer der beste Gradmesser für die Kapazität ist.
Ursprünglich wurde die Maschine für Rapid Prototyping angeschafft, um im Bereich der Prototypenentwicklung schneller agieren zu können. Heute nutzen wir sie jedoch auch für kleinere und mittlere Produktionsvolumina.
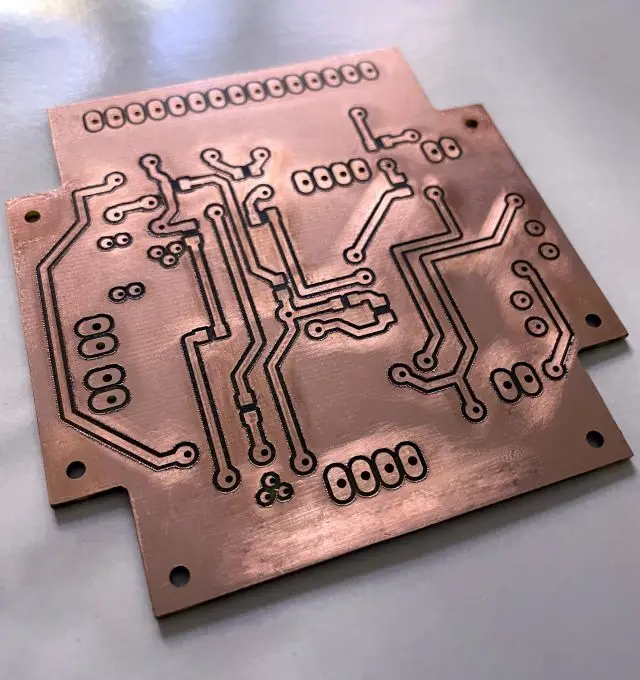
Leiterplatte für Prüfhardware (Bild: GERA-Ident)
4. Für welche spezifischen Anwendungen setzen Sie die Maschine ein?
Ramin Hassan: Die Maschine wird sowohl im Hardware- als auch im Transponderbereich eingesetzt. Beispiele hierfür sind Leiterplattenproduktion sowie Individualisierung von Standardgehäusen und Geräteelementen.
Üblicherweise konzentrieren wir uns auf RFID-Labels, jedoch ermöglicht uns die Maschine auch die Herstellung von Hardtags, die Durchführung von Prototypenversuchen und die Produktion bis hin zu mittleren Stückzahlen – also mehreren Tausend Einheiten.
Im Bereich der Prototypenherstellung bauen wir beispielsweise Adapterplatinen für große Transponderchips auf. Diese kleinen Leiterplatten werden mit den Chips bestückt und lassen sich so im Prototypenprozess besser in die endgültigen Leiterplatten integrieren – einschließlich Messpunkten und anderen Funktionen.
5. Welche konkreten Vorteile hat Gera-Ident durch die seit 2022 angeschaffte Maschine erzielt?
Ramin Hassan: Leiterplatten haben in der Regel eine Größe von bis zu 300 x 200 Millimetern. Zum einen können wir nun deutlich größere Leiterplatten herstellen – bis zu einer Größe von 750 x 900 Millimetern, was eine erhebliche Erweiterung der Produktionsmöglichkeiten darstellt. Auch in der Antennenproduktion sind wir nun maßunabhängiger als früher.
Die Präzision ist mit einer Toleranz von rund 0,01 Millimetern sehr hoch und entspricht der klassischen Ätztechnik. Dabei bleiben wir aber ressourcenschonend und chemikalienfrei. Ein weiterer Vorteil besteht darin, dass wir viele Aufgaben, die früher extern beauftragt werden mussten, nun intern erledigen können. Dies ist insbesondere bei Testläufen oder Mindermengen von Vorteil, bei denen der Entwicklungsprozess noch unklar ist.
Gerade 2022, als sich die Lieferketten schwieriger gestalteten, stiegen bei vielen Lieferanten die Mindestmengen. In diesem Bereich sind wir nun deutlich unabhängiger geworden, besonders bei kundenspezifischen Aufträgen.
Wir sind nun in der Lage, auf kundenspezifische Aufträge schneller zu reagieren und die Lieferzeiten signifikant zu verkürzen. Durch die interne Durchführung von Nachbearbeitungsschritten und Individualisierungen können wir nicht nur die Kundenbedürfnisse effizienter bedienen, sondern auch Abfall und Energie sparen.
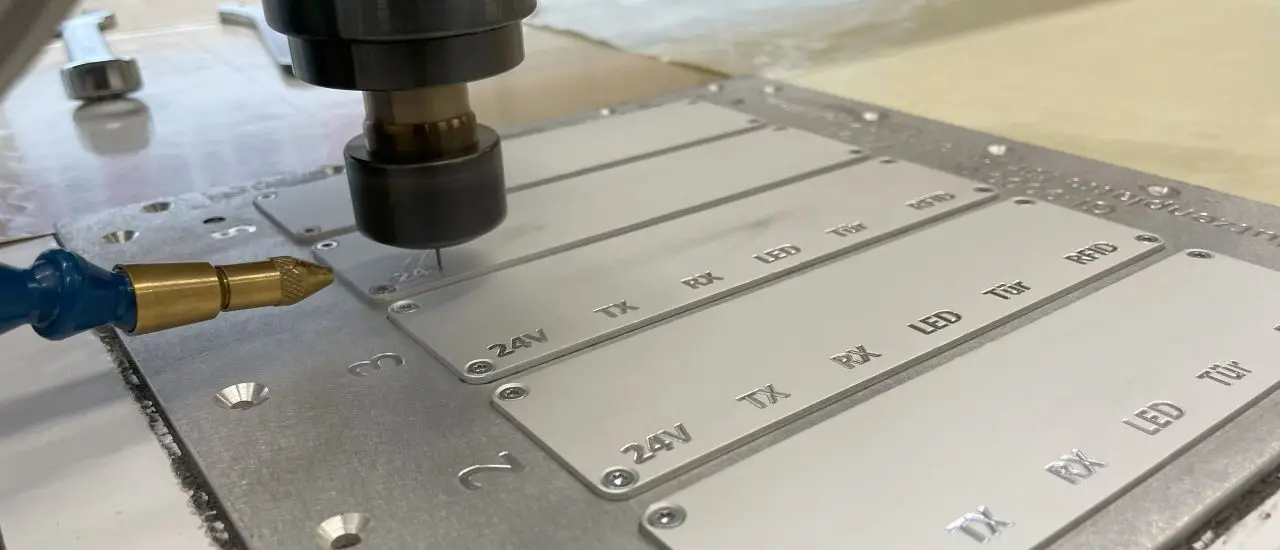
CNC-Fräse im Einsatz: Fertigung der Seitenteile für ein Readergehäuse. (BIld: GERA-Ident)
6. Welche spezifischen Vorteile bietet die Kombination der Fräsmaschine mit einem 3D-Drucker für Ihre Produktionsprozesse?
Ramin Hassan: Generell erfolgt die Produktion in Kombination. Bei der Konzeption elektronischer Geräte gibt es immer ein Elektronikteil und ein Gehäuseteil – die sogenannte Einhausung. Den Elektronikteil fräsen wir mit der CNC-Maschine, während der Gehäuseteil im 3D-Druckverfahren hergestellt wird.
Dafür arbeiten wir mit mehreren Partnern zusammen, um diese Prozesse effizient zu realisieren. In manchen Fällen übernehmen auch die Kunden direkt die Gehäuse, sodass wir nur noch die Elektronik in die vorbereiteten Gehäuseteile integrieren müssen.
Ein konkretes Beispiel dafür ist die Entwicklung von Sensor-Transpondern für den medizinischen Bereich, speziell im Hygienebereich. Hier kombinieren wir gefräste Leiterplatten mit 3D-gedruckten Gehäusen, um komplette Transponderlösungen anzubieten. Der 3D-Druck ermöglicht uns, individuell angepasste Gehäuse schnell und kostengünstig in kleinen Stückzahlen zu produzieren, was mit traditionellen Fertigungsmethoden nicht möglich wäre.
Die Kombination aus CNC-Fräsmaschine, 3D-Druck und unserem RFID-Know-how gibt uns die Flexibilität, auf kundenspezifische Anforderungen passgenau einzugehen. Sprechen Sie uns an – wir realisieren auch Ihre individuelle RFID-Lösung.
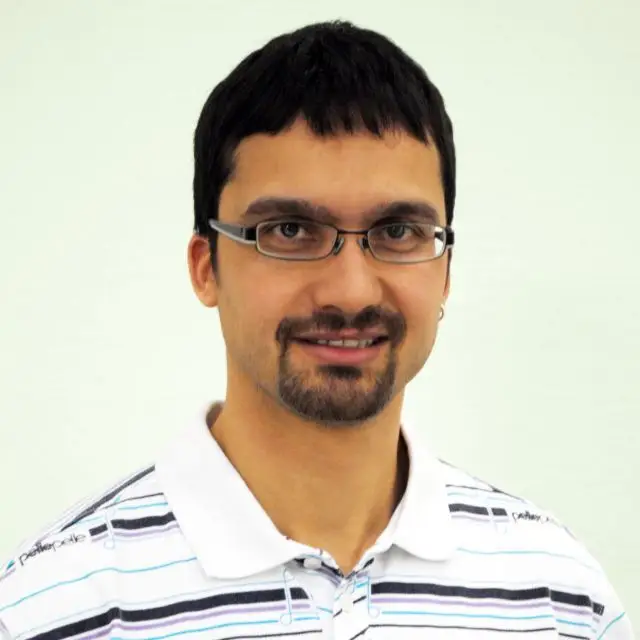