Take IoT in Manufacturing to the Next Level at WIoT tomorrow!
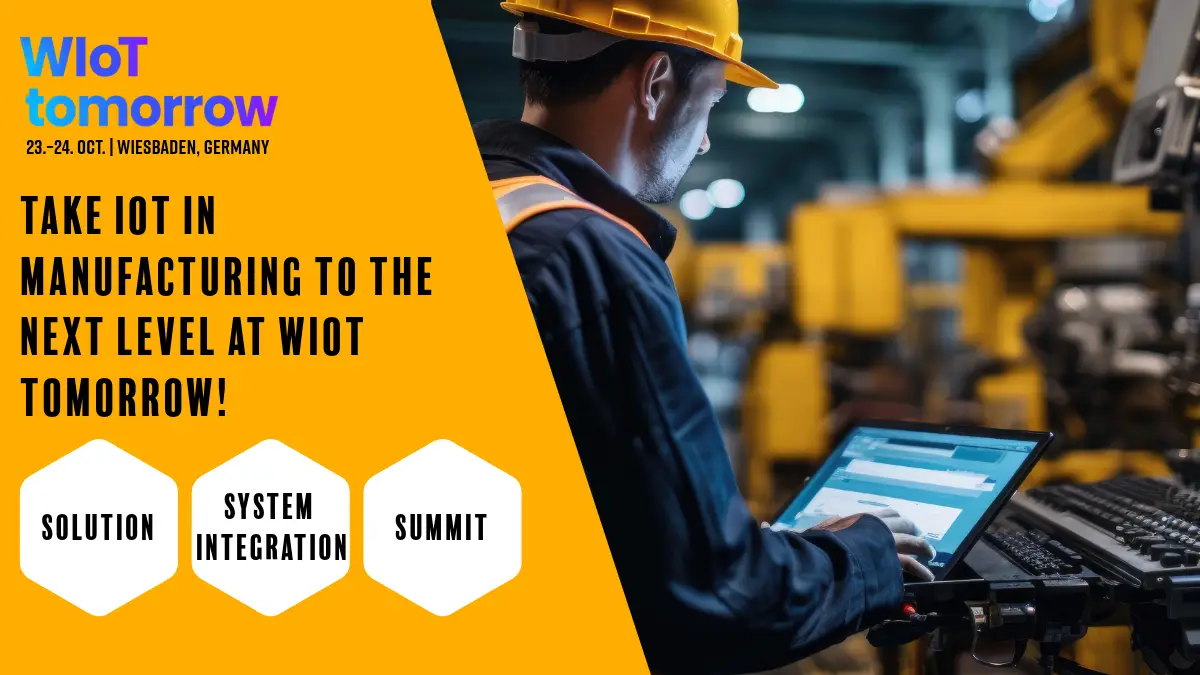
Why WIoT Tomorrow is a Must for the IoT in Manufacturing Industry
If you’re working in the manufacturing industry, WIoT Tomorrow 2024 is an event you need to attend. The Internet of Things (IoT) is revolutionizing how factories and production lines operate, making them smarter, more efficient, and better at reducing costs. From improving quality control to reducing unplanned downtime, IoT in the manufacturing industry is leading the way in the next wave of digital transformation.
WIoT Tomorrow is where you can see how IoT can benefit your manufacturing processes and help your business stay ahead in a competitive landscape.
Why IoT in Manufacturing is Changing the Game
IoT in the manufacturing industry is all about using IoT devices and sensors to connect devices across the factory floor. These devices monitor physical objects such as machines, equipment, and even materials. The collected data from these devices helps manufacturers gain insights into how their production systems are working. This data collected can then be used to make improvements in production processes, optimize resource use, and prevent costly problems before they happen.
One of the key advantages of IoT in industrial manufacturing is how it improves quality control. By using IoT technology to monitor products during production, factories can ensure that every item meets strict quality standards. This is especially important in industries where precision is critical, such as automotive, aerospace, or electronics. IoT also enables manufacturers to spot issues early, preventing defective products from making it to the customer and improving overall product quality.
Optimizing Production Processes with IoT
In a smart factory, IoT plays a crucial role in optimizing production processes. By using sensors to track everything from machine performance to the flow of materials on the assembly line, IoT helps factories run more smoothly. With IoT, manufacturers can analyze the data collected from their machines to detect patterns or trends that may indicate potential problems.
For example, IoT sensors can alert operators if a machine is showing signs of wear, allowing for maintenance before the machine breaks down. This type of predictive maintenance reduces unplanned downtime, keeping production lines running without interruptions. In industries where downtime can be costly, such as automotive or consumer goods manufacturing, this can result in significant savings.
IoT also helps factories become more flexible. In traditional manufacturing, changing a production line to make a new product can be time-consuming and costly. With IoT, machines and devices can communicate with each other, enabling quicker adjustments to production processes. This flexibility allows manufacturers to respond faster to changes in customer demand, creating a more agile production system.
Reducing Costs with IoT in Manufacturing
One of the biggest benefits of IoT in manufacturing is its ability to help businesses save money. By using IoT devices to monitor equipment, materials, and energy use, manufacturers can find ways to reduce waste and cut costs. For example, IoT sensors can track how much energy each machine uses, helping factories identify opportunities to save energy and lower utility bills.
In addition to energy savings, IoT helps manufacturers optimize the use of raw materials. By tracking how materials move through the production processes, IoT solutions can ensure that materials are used efficiently, minimizing waste. This also leads to better inventory management, as manufacturers can monitor stock levels in real time and reorder supplies as needed. This real-time visibility into inventory can prevent overstocking or running out of key materials, both of which can negatively impact the bottom line.
Another key cost-saving benefit is the reduction of unplanned downtime. IoT technology enables factories to predict when machines are likely to fail, allowing them to schedule maintenance during planned breaks instead of dealing with unexpected breakdowns. This keeps the production lines running smoothly and prevents costly delays in manufacturing.
Improving Safety in Manufacturing with IoT
Safety is a top priority in any manufacturing environment, and IoT is helping to make factories safer for workers. IoT devices can monitor equipment and environmental conditions in real time, alerting workers and managers to potential hazards. For example, sensors can detect dangerous temperature or pressure levels in a machine, allowing workers to address the issue before it leads to an accident. This improves the overall safety of the factory and helps prevent injuries.
IoT also helps with compliance by ensuring that machines and processes meet safety regulations. By collecting and analyzing safety-related data, IoT solutions can provide insights into how well a factory is following safety protocols. This makes it easier for manufacturers to maintain a safe working environment while also reducing the risk of costly fines or legal issues.
At WIoT Tomorrow, you’ll have the chance to see how IoT solutions are improving safety in the manufacturing industry and learn how these technologies can help protect your workers and your business.
Enabling Digital Twins in Manufacturing
One of the most exciting developments in IoT for manufacturing is the rise of digital twins. A digital twin is a virtual copy of a physical system, such as a machine or even an entire factory. By using IoT devices to collect data in real time, manufacturers can create digital twins that mirror the real-world performance of their machinery. This allows them to run simulations, test new ideas, and predict potential problems before they happen.
For example, a digital twin of a production line can show how changes in one part of the system will affect the rest of the operation. This can help manufacturers optimize their production processes without disrupting actual production. Digital twins also enable manufacturers to test new designs or production methods in a virtual environment, reducing the risks associated with changes to the factory floor.
At WIoT Tomorrow, you’ll have the chance to see how digital twins are being used in manufacturing and how this cutting-edge technology can help your business improve efficiency, reduce costs, and stay competitive in the global market.
The Role of Industry 4.0 and the Industrial Internet
IoT is at the heart of Industry 4.0, the next phase of the industrial revolution. Industry 4.0 focuses on the use of smart technologies, such as IoT devices, to create more automated and interconnected production systems. In a smart factory, IoT allows machines and systems to communicate with each other, sharing data and working together to optimize production.
The Industrial Internet refers to the use of IoT technology to connect devices and machines across industries, enabling them to work together in more efficient ways. In the manufacturing industry, this means using IoT to collect and share data across different parts of the production system, from raw materials to finished products. This level of connectivity allows manufacturers to make more informed decisions, improve efficiency, and produce higher-quality products.
IoT in the manufacturing industry is a key driver of Industry 4.0 and the Industrial Internet, helping businesses of all sizes take advantage of the latest technologies to improve their operations. At WIoT Tomorrow, you’ll see how these technologies are being applied in the real world and learn how your business can benefit from this digital transformation.
Why WIoT Tomorrow is a Must-Attend Event for Manufacturers
WIoT Tomorrow is the premier event for anyone involved in the manufacturing industry. With IoT transforming how factories operate, this event offers a unique opportunity to explore the latest IoT devices and solutions that are shaping the future of manufacturing. Whether you're looking to improve production processes, enhance quality control, or reduce costs, WIoT Tomorrow provides the tools and insights you need to succeed.
By attending WIoT Tomorrow, you’ll have the chance to learn from industry leaders, discover cutting-edge technologies, and network with other professionals in the manufacturing sector. You’ll see how IoT is being used to improve product quality, enhance safety, and optimize manufacturing processes across a range of industries.
Conclusion: Don’t Miss Out on the Future of IoT in Manufacturing
The future of the manufacturing industry is being shaped by IoT, and if you’re responsible for production or factory operations, attending WIoT Tomorrow is a must. From digital twins and predictive maintenance to real-time monitoring and automated systems, the innovations on display will show you how IoT can transform your factory into a smart factory.
By embracing IoT in manufacturing, you’ll be able to make better decisions, improve product quality, and reduce costs. Don’t miss the opportunity to be part of the next wave of digital transformation in manufacturing. Join us at WIoT Tomorrow 2024 and discover the future of IoT technology in the manufacturing industry.
The Digitalization of Industry on Think WIoT
If you're eager to learn more about the incredible potential of IoT in industrial manufacturing, we highly recommend checking out the "The Digitalization of Industry" section on Think WioT. It's a fantastic resource!